Makers of Spray-Foam Insulation Named in Lawsuits
Federal lawsuits claiming that spray-polyurethane foam insulation is toxic and can sicken those who live in houses where it has been installed are pending in more than a half-dozen states as lawyers deal with an “avalanche” of complaints, a Florida attorney says.
Vince Pravato, an attorney at Wolf & Pravato in Fort Lauderdale, says that to date, complaints have been filed in federal district courts in Florida, New York, Michigan, New Jersey, Connecticut, Wisconsin, and Pennsylvania, with filings also expected in North Carolina and Arkansas.
Pravato has been retained by clients to pursue claims against a number of manufacturers and installers, including Demilec, Lapolla, Masco, and NCFI Polyurethanes.
The filings mark the start of what is likely to be a protracted legal effort on the part of a number of attorneys representing many homeowners. These attorneys are hoping that the cases will be bundled into something called “multidistrict litigation,” which would speed pretrial proceedings. A hearing is scheduled for the end of May in Kentucky.
Jury trials that could help shape an eventual outcome are still months away.
Some clients suffer ‘severe health issues’
Pravato was one of the attorneys working on litigation that targeted defective drywall manufactured in China and installed in thousands of homes in the United States. Class-action settlements approved in that case could cost the manufacturer more than $1 billion.
“I was not eager to jump into another situation like the Chinese drywall case,” Pravato says, “but more and more people began contacting me. I said I would look into it, and it became an avalanche.”
The chief complaint is chemical sensitivity that some people develop after their houses have been insulated. While a number of manufacturers have been cited, Demilec comes up most frequently, Pravato says. Most often, the affected homeowners were in their homes at the time the foam was sprayed, or returned home immediately afterward.
Clients who developed health problems typically didn’t know what was causing them. That included a family doctor from Virginia who was forced out of his home.
“He had significant neurological problems,” Pravato says. “He had MRI testing because he was losing sensation in his legs. He had breathing problems. He was seeing an allergist. He couldn’t figure out what the problem was, and he was a medical doctor. He said, ‘Vince, if somebody came to me with these problems and said it was spray foam, I wouldn’t believe him.’ And he finally figured out what it was. They moved out, and he’s doing much better. But his house sits empty. When you hear these stories, it’s just a tragedy after a tragedy. These people are losing their homes. It’s terrible story after terrible story.”
Pravato believes that many others are in a similar situation. “I think there are a lot of people out there who are having problems and don’t know why they are having problems,” he says. “This hasn’t become a giant public concern so far. You don’t have a lot of news coverage on it. I don’t think people really have the tools to know what is the cause of a lot of the problems they may be having.”
Two-part foam that must be applied carefully
Spray polyurethane foam has become a popular insulation option, especially in high-performance houses. Although relatively expensive, it effectively seals cracks and seams in wall and ceiling cavities much better than batt insulation.
Foam comes in two varieties, open-cell and closed-cell, each with slightly different properties and different R-values. Of the two, closed-cell foam is a better insulator, with R-values of about 6.5 per in. Once cured, it also becomes a vapor retarder. Open-cell foam has a lower R-value, roughly 3.5 per in. Although it acts as an air barrier, it’s not an effective vapor barrier. According to Pravato, open-cell foam is the target of more of the complaints than closed-cell foams.
Both open-cell and closed-cell foams are applied in fundamentally the same way. They consist of two chemicals that are mixed in the head of the installer’s spray gun and expand on contact. Once the foam cures, it’s designed to become an inert material that’s benign to homeowners. The problem, the complaints allege, is that the foam remains toxic.
“When applied, the resulting polyurethane foam is supposed to become inert and non-toxic,” reads a Florida complaint naming Demilec’s Sealection insulation, “but SPF remains toxic after installation because either, as designed, it is impossible to become inert and non-toxic even under optimal conditions; or proper installation (and thus non-toxicity) is nearly impossible given the exacting set of installation requirements and inadequate training and installer certification methods.
“Due to the defective nature of Demilec’s design and manufacture of SPF, the defective nature of Demilec’s training of distributors/installers, and the defective nature of Demilec’s warnings, labeling and training materials, the application and installation of SPF is anything but controlled, resulting in the installation of an SPF that causes property damage and health hazards to occupants of installed homes such that the only remedy is the complete removal of the SPF.”
The complaint cites Demilec’s own instruction manual for installers, notably the company’s warning that applying the foam requires “strict adherence” to approved techniques and that a “regular maintenance program must be followed and temperatures must be scrupulously respected.”
The complaint alleges that Demilec knew its certified installers were “not fit” to do their jobs and that training and supervision were inadequate.
No known method of remediation
Once installed, spray polyurethane foam is very difficult to remove, complicating the situation for homeowners who develop chemical sensitivities as well as clouding the eventual outcome of the court cases.
“Our goal is to find ultimately a remediation process for these homes,” Pravato says. “EPA right now acknowledges that there isn’t any safe way to remediate the homes. I have several clients who have tried to remediate and have been unsuccessful.”
Efforts have included something called “ice blasting,” in which shards of ice are shot at installed foam at high speed, essentially abrading it away from any surface where it’s been applied. According to Pravato, the foam breaks into very small particles and spreads easily, making the situation potentially worse than it was.
One client in Florida whose home was sprayed with foam only in the roof is proposing to remove the entire roof intact, without disturbing the foam, and replacing it with a new one. Another client scraped away most of the foam in his roof but still experiences problems when the summer heat warms the remaining foam.
Spray foam the focus of previous complaints
There’s nothing new about homeowner complaints that a fishlike chemical odor lingers for months after spray foam has been applied.
Green Building Advisor senior editor Martin Holladay in 2011 interviewed eight homeowners who’d experienced problems with spray-foam applications and reported on his findings at GBA. In a few cases, unpleasant odors persisted despite attempts to remove foam that appeared faulty or spray over it to seal it in. In some cases, manufacturers tried to blame the smell on other substances that might have been in the house, and their efforts to get to the root cause of the problem and correct it were spotty at best.
In Holladay’s interviews, Demilec was cited frequently as the foam manufacturer. “We’ve had a lengthy ordeal with representatives from Demilec,” Florida homeowner Mike Roth told Holladay. “Their agenda was to prove there was something else in the house causing the smell and it wasn’t their problem.” Roth is one of the homeowners represented by Pravato’s office.
Reports of poor air quality and impacts on health have cropped up a number of times in other GBA posts and Q&A threads. Homeowners shared remarkably similar stories.
Response from manufacturers
Green Building Advisor made attempts to contact representatives of Demilec, Masco, Lapolla, and NCFI Polyurethanes. Voice messages, or in some cases email requests for comment, were not returned.
GBA also asked the Spray Foam Coalition, an association of companies that make and sell spray polyurethane foam, for comment on reported problems with the insulation and the pending court cases. The response reads in part:
“The Center for the Polyurethanes Industry (CPI) and the Spray Foam Coalition (SFC) are aware of recent cases involving spray polyurethane foam. Our members are committed to the health and safety of polyurethane products, which includes spray polyurethane foam (SPF), and those who use them.
“According to the U.S. Environmental Protection Agency, after SPF is correctly applied and cured, it is considered to be relatively inert, which means the chemicals are finished reacting. When having SPF installed, homeowners should talk to their professional contractor about the product’s curing time and appropriate safety precautions.
“The SPF industry has for many years and will continue to support the safe and appropriate use of SPF; moreover, the industry works with regulators, researchers, producers and applicators to ensure that those using SPF have access to information they need about how to use the product safely. Along with government agencies, researchers and other relevant experts, the SPF industry works to provide the best information available about the health and safety aspects of SPF and identify where additional research could be conducted. Industry leaders and organizations work together to provide free health and safety training to professional contractors, and anyone interested in learning more about the product, as well as a library of other free resources, [may go to] spraypolyurethane.org.”
The statement also says that the Spray Polyurethane Foam Alliance recently launched a professional certification program, which “will continually raise the bar on safety, performance, quality and professionalism.”
Efforts to streamline the court cases
Plaintiff attorneys, including Pravato, will seek multidistrict-litigation status in a hearing in May. If granted, a single federal judge would be able to rule on pretrial questions common to all similar complaints no matter where they were filed. Unlike a class-action lawsuit, these multidistrict cases would be heard by juries in the courts where they were originally filed. In a class action, a single case that goes all the way through trial settles all similar cases for plaintiffs in the same class.
Pravato says that the multidistrict designation is a way of getting consistent rulings on common legal questions while making the legal process more economical. “If you have 20 different judges hearing these matters, you may have all types of different rulings on different issues,” he says. “Having everything consolidated in front of one judge will streamline the entire process, and it will give the cases consistency.”
He continues: “It’s very difficult to file individually against these giant chemical companies. They have the deep pockets, and the recovery for an individual home makes it very difficult for a law firm to get involved and hire the type of experts you need.
“Let’s say the damages are only $200,000 to a home. If you have to spend $100,000 in expertise to hire chemists and various experts you need to prove your case, it almost becomes prohibitive to bring your case against these manufacturers and installation companies.”
If the cases do win multidistrict-litigation status, Pravato says that a few bellwether trials could be fast-tracked all the way through jury trials within a year, with findings used to shape a potential settlement.
Attorneys are seeking to have the multidistrict cases heard in a southern Florida federal court by Judge Kenneth A. Marra.
Fine Homebuilding Recommended Products
Fine Homebuilding receives a commission for items purchased through links on this site, including Amazon Associates and other affiliate advertising programs.
Handy Heat Gun
Reliable Crimp Connectors
8067 All-Weather Flashing Tape
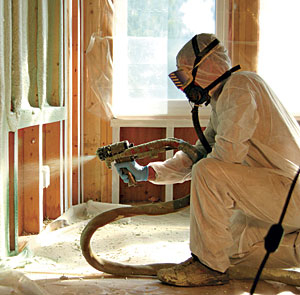
View Comments
so, is it a a real complaint or one made up in the crazy world we live in?
How many applications in Canada, other countries with out greed driven litigation?
What a nightmare! I hope y'all are going to do a feature on whether spray-foam is safe or not and under what conditions.
There is an overwhelming amount of technical info that is missing here. Different chemicals are used in open cell and
closed cell foams and even among each type there are several
different formulations and there are additive chemicals sometimes such as fire retardant and chemicals which adjust
the optimum curing temperatures etc. I wonder also if what
they are actually referring to is the more accurately used
term of poly-isocyanurate which is a two part closed cell
foam where before curing one of the components contains
cyanide and after curing it is supposedly transformed into
a safer chemical. I do know that when this foam is burned
a cyanide gas is given off and when only one whiff is taken
you are dead. So it is rarely mentioned or talked about
as far as how dangerous the closed cell foams are in the
event of a fire. There is no such thing as someone stumbling out of a house coughing and choking from breathing smoke.
There really needs to be some very specific laboratory
analysis for each specific foam mixture and measurements of
off-gassing after installation much like they did years
ago when there was a lot of formadelhyde used in the glue
of primarily plywoods and particle boards used in cabinets
and paneling and kitchen countertops and other furniture components etc. A point I wish to make is that I
suspect of all the 2 part foam formulas used, we need
to identify which are the best and which are the worst
and then prohibit the use of the worst.
I am an ex custom home builder and have used the closed cell
foam many times. I know that basically the same stuff
( polyisocyanurate) is also used on commercial roofs and commercial refrigeration such as warehouses, box-cars,
refrigerated trucks, and convenience store and grocery
store cold storage rooms etc.
Specilized, I had to breath deeply before replying to your comment. To be fair, if I wasn't living through this nightmare right now, I might be skeptical too. There's a lot of greed in this world. It would take pages to describe what we've gone through in the past six months - which began by naively hiring a seemingly good company to sprayfoam our entire roof interior in an old house so we could be up to code in our fixer upper.
Two days before Christmas we packed a bag and left our homeand have lived in six hotels, friends, family and now an apartment. We are living check to check after putting thousands of dollars into our little home that we planned to retire in. We were in the home while they sprayed for two days and slept there 4 nights. You cannot imagine what it's like to lose the place you go home to each night, lose all of you hard earned money/savings, and realize that people knowingly did this without any caution at all. And you can't go in to get your belongings, due to all kinds of symptoms that you eventually learn are VERY serious. Now, we spend every spare moment when off work, researching, reading and calling anyone who could possibly help us. IT MUST STOP. We are good people and have never been interestered in anything litigious but unless someone wants to have us move in with them, we have no choice.
I think greed might play into why people are still spraying this stuff without caution. And often lying about it afterwards as in our case. We still don't have a lawyer. If anyone in Chicago suburbs can help, please comment. Thank you.