Keep a Dormer Addition Clean and Dry
A well-planned construction sequence contains the debris and keeps the rain out of the house.
Synopsis: A veteran remodeling contractor walks readers through a recent dormer addition, explaining how he choreographed the process to minimized mess, rain damage and other inconveniences for the owners. He outlines his construction sequence and offers tips for any remodel.
Retrofitting a shed dormer in an occupied house can be a disruptive project. But with careful planning, intrusions such as a constant parade of workers and demolition debris can be kept out of the house. And although there’s always some time when the roof is open or a wall is missing, avoiding weather damage is straightforward: Just expect pouring rain every night, and plan accordingly.
First, build the new roof
The work on this house involved replacing two small existing dormers with a large shed dormer, and the job affected almost every upstairs room. To ensure that the project was weathertight, we’d build the new dormer’s roof first, but we needed room for demolition and reconstruction under it.
We began by framing the dormer’s outside wall with four posts and a long header. This approach meant we could frame the dormer roof while cutting only four small holes in the original roof. Then, after we built the new roof and removed the old dormers, we could fill in the studs and the window framing.
We marked the locations of the wall posts to correspond with where we wanted the interior partitions to fall. Then we cut out small sections of roof with a reciprocating saw to give us access to the top plate of the existing wall and installed the first corner post. When this post was carefully braced and plumbed, we used a water level to calculate the height of the other corner post to ensure that the roof was level. Once this second post was positioned and plumbed, we strung a line between the two end posts and set the remaining posts to that height, making sure the load was transferred directly to a stud below.
With the posts braced and in place, we installed the headers. At the end of the day, we covered the holes in the roof made by the new posts with aluminum flashing and plastic sheeting.
Tear out only what can be rebuilt that day
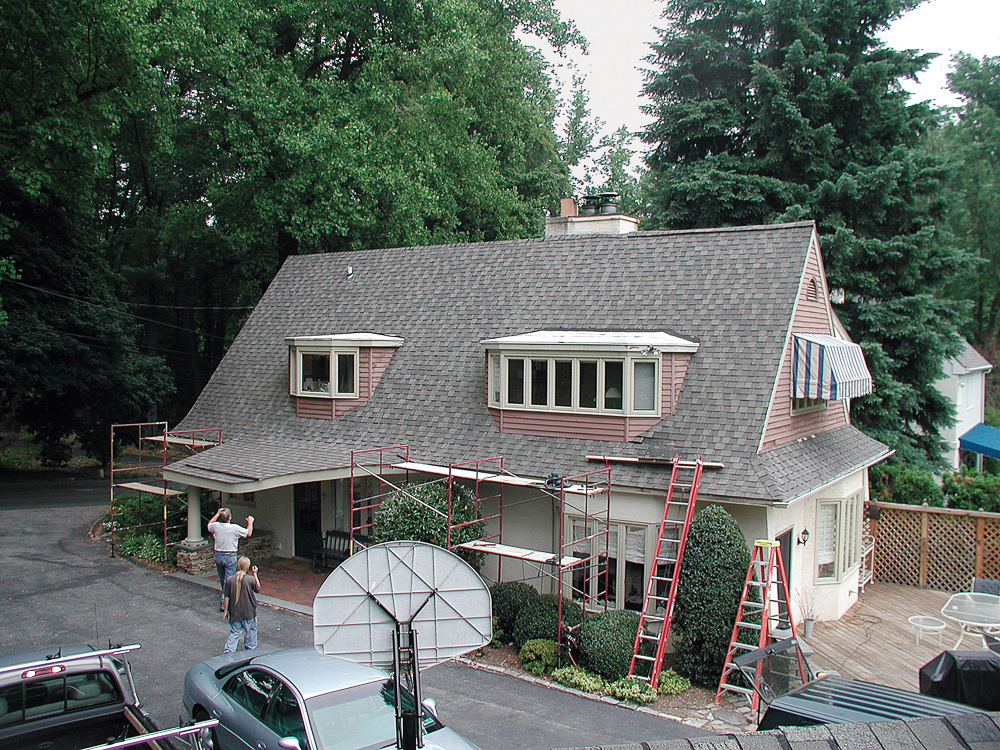
We framed the new dormer’s roof in two sections over two days. We calculated where the new dormer rafters would intersect with the oldest section of roof, cut a 2-ft.-wide section, and removed it. This approach gave us access to the attic without having to go through the house, and also provided light and ventilation to the attic where we would be working.
After the new rafters were securely in place, the sheathing and the #30 felt were installed. The next day, we repeated the performance for the rest of the dormer roof. We now had a reasonably weathertight lid on the work area and could begin the demolition process. To keep out rain, we protected the work site with tarps, which were layered like roofing shingles and held fast with furring strips.
Keep the work site separate from the house
The interior of the dormer was divided into four areas: master bedroom, closet, the daughter’s bathroom, and her closet. It was important to complete the master bedroom quickly, so we built the front wall, sheathed it, installed the window, and had it drywalled and trimmed before some of the other sections were even started. By finishing this room first, the owners got their bedroom back quickly.
We were careful to isolate the workspace from the rest of the house. Two small existing closets were turned into walk-in closets. Before we commenced with serious demolition of either closet, we reframed the door openings, drywalled over them, and taped the seams, planning to cut out the doorways after the dirty work was done. Having the living side of the wall closed acts as a barrier against construction while allowing the electricians and plumbers to do their work on the other side.
Even the small amount of drywall we did on the living side of the wall meant dust. We took the usual precautions. A plastic runner protected the upstairs carpet. To contain airborne dust, I tacked tarps across doorways, placed a box fan in a window as an exhaust, and vacuumed at the end of each workday. On the other side, we completed almost all the work before we cut through to install the new doors and trim.
Because the bathroom door wasn’t being moved, we taped it shut and put a sheet of foam insulation over it for protection. The bathroom then was gutted and rebuilt.
No muss, no fuss
Much of this job revolved around not making a mess. We planned the placement of the Dumpster so that we could build a plywood chute to it for debris removal, but kept it out of the way of deliveries. We were working directly over the driveway, and we made sure we swept up carefully every night.
The bathroom’s outside wall was left unframed as an access to the second floor, and consequently, little traffic went through the house. The dormer was finished toward that opening, and the day before the tile was installed in the bathroom, we finished framing the rough opening and hanging the drywall, then installed the window and trim. The tilesetter’s wet saw was set up on the scaffold outside, and his helper spent the day getting a tan and passing cut tiles through the window.
Every remodeling project is an intrusive ordeal for the homeowner. The single most important aspect of our remodeling strategy was that my clients appreciated the efforts we took to protect their home and privacy.
Staying ahead of the weather
To keep out rain, build the new roof before removing the old one.
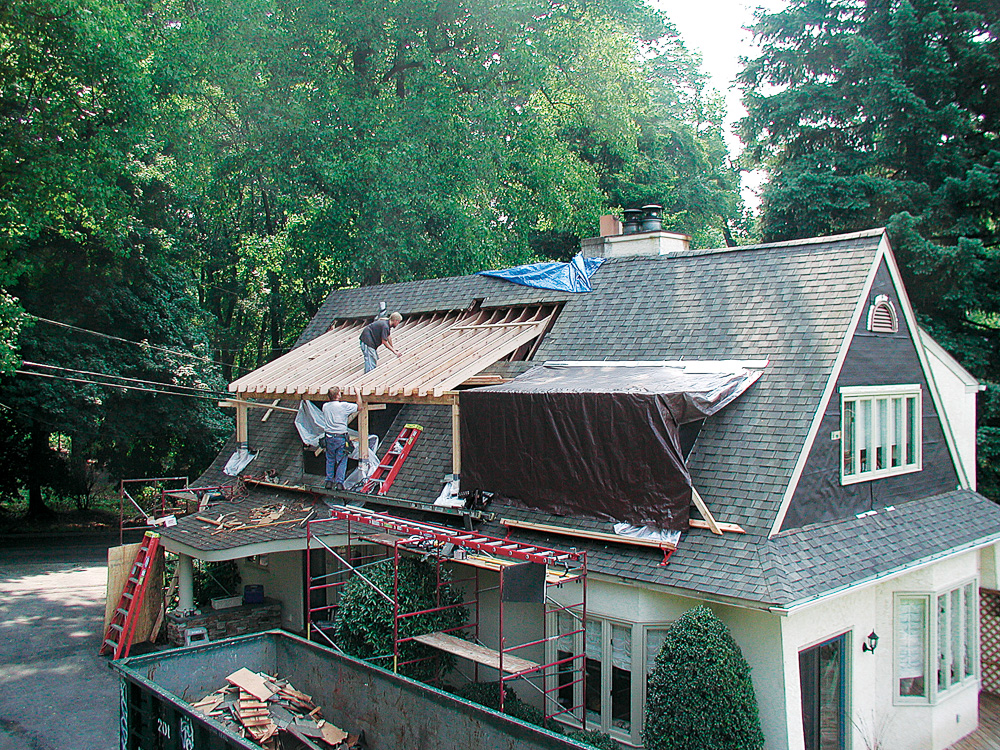
Supporting the new dormer roof with one long header and four posts meant cutting only four small holes in the old roof. Setting and temporarily flashing the posts was the first day’s work. Half of the dormer’s new roof was framed and then sheathed the next day, and all the openings were flashed and tarped against the wind and rain. The dormer’s roof was completed and sheathed, and #30 felt paper kept out the rain.
Keeping a project neat
To protect the house from dust and debris, the occupied space was sealed with drywall and plastic. Also, the debris was removed (and new materials brought in) through the new dormer windows.
Construction sequence minimizes disruption (reference drawing above):
- (Master bedroom) Evicting the owners from their bedroom was the most intrusive part of the renovation, so this room was finished first. The outside walls here were completed and the trim in place before demolition started elsewhere.
- (Closet-orange) The new closet wall was framed and drywalled (including the doorway) on the occupied side, creating a solid barrier to construction fallout. Plastic sheeting would not have sealed the walls nearly as well.
- (Closet-green) This closet was finished quickly. The bathroom would take the most time and require the most schedule-juggling, which is why it was planned to be done last.
- (New bathroom) Toward the end of the project, the window opening in the bathroom’s outside wall was the only access to the work area. The job was finished working toward this opening, with the window installed and the bathroom paint and trim finished just before the new work was opened to the rest of the house.
Tips for any remodel
- Minimize traffic through the house.
- Scrupulously seal off the living space from the work zone.
- Use a window fan in the work zone to exhaust dust and fumes.
- Take extra precautions to protect the stuff that stays. If the floor stays, for instance, cover it with plywood (and tape the seams) rather than rely on a tarp.
- Clean up the work zone at the end of every day.
- To keep peace in the house, consider hiring a cleaning service halfway through.
Photos by Nicholas Pitz. Drawing by Don Mannes
Related stories:
From Fine Homebuilding #158
For more photos, illustrations, and details, click the View PDF button below:
Fine Homebuilding Recommended Products
Fine Homebuilding receives a commission for items purchased through links on this site, including Amazon Associates and other affiliate advertising programs.
Stabila Classic Level Set
Portable Wall Jack
Protective Eyewear