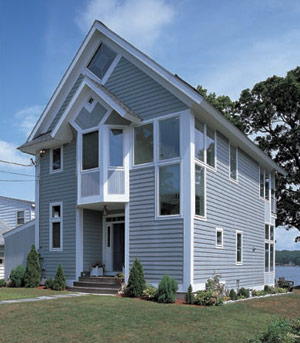
They had inherited a house with mixed blessings. The positives were plain to see: The house faced a community green (the site was originally a spiritualist compound formed almost 100 years ago in Niantic, Connecticut), and the back side offered a wonderful panoramic view of the Niantic River framed by mature maple trees.
The one clear downside was the site’s microscopic size (approximately 1/8 acre). It’s a fact of life that most waterfront homes built before the 1960s are considered “preexisting” or “nonconforming” by current local zoning laws. In other words, what is now in place could not have been built today, so there are special limitations to any new construction that may be built on these sites. In planning a new house, the Johnstons had to build on the existing footprint and carefully rebuild the shed shape on one side to match the original house, which left them virtually no wiggle room.
A Slow Process
As with many two-income families seeking to create a home, the thought of building a new house was fraught with financial concerns for the Johnstons. They had a budget of $160,000 in 1995.
Given the limitation of the existing footprint, the house could only grow by building a second story, which would increase the size to between 1,500 sq. ft. and 2,000 sq. ft. The project progressed through sporadic bursts of design activity, regulatory approvals, bidding, and so on during a three-and-a-half-year process of design and permitting and, of course, the unavoidable increase in construction costs over time. Throughout all the ups and downs of the approval process, the owners remained steadfast in their resolve to build the house, and they ended up with a $200,000 price tag for an 1,800-sq.-ft. house that had two-and-a-half bedrooms and one-and-three-quarter baths.
What made containing the budgetary creep even more challenging was the homeowners’ desire for high-quality, durable, and aesthetically expressive materials and features. They chose wood siding (not vinyl), wood flooring (not carpet), a wood-burning fireplace (not gas), high ceilings, and some crafty windowscaping using high-quality windows. The final product is a combination of open space and careful detailing built within extraordinary limits, a beacon of hope for average housing consumers who think that they can’t afford a custom home.
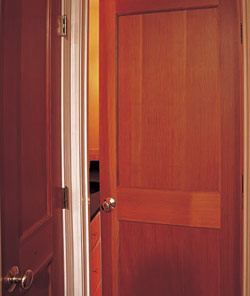
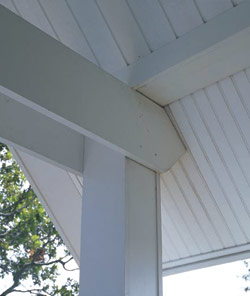
Big Moves in a Small House
To make the wish list real, a variety of approaches were employed to “ease the squeeze” of a relatively small house set within a fixed footprint. First, visual connections were made through the interior to take advantage of the rewarding waterfront vista. The visual connection starts at the front door, where the view opens up from the raised foyer through the living room and out double doors that are set into a grid of windows facing the river.
Second, the open space of the first floor was used to help overcome the feeling that this is only an 1,800-sq.-ft. house. The refrigerator turns its back to the entry and is fully clad with walls and a “roof,” allowing anyone entering the house to see over the refrigerator out to the water view.
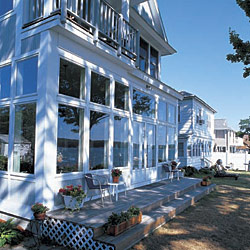
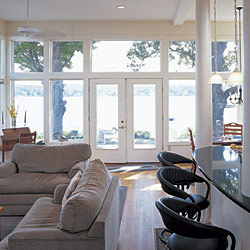
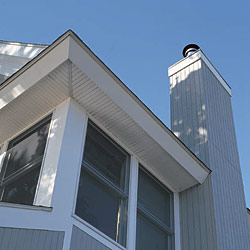
Simple stock materials can be used in custom construction to save money-as long as they are removed from direct examination. The chimney shroud in this house for example, is covered with one of the least expensive materials available (T1-11 plywood), and the soffit is a prefabricated perforated alumninum material that simulates a tongue-in-groove wood product. Neither chimney nor eave is within close viewing or touching distance, and both standard materials are subtly introduced to save throusands of dollars.
Splurge Here, Save There
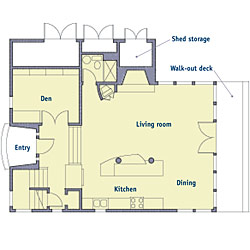
A number of custom touches enliven the house: a covered walk-out porch for the master bedroom, a bay window for the son’s bedroom, a built-in shroud for the television, and the expressive exterior trim—all wrought of standard parts brought to life by simple coordination of line, color, shape, and material. With the deep blue front door and cool gray clapboards, the white trim becomes a coordinating element that wraps around corners, defines grids, and highlights features. There is one truly luxurious custom piece in the house: the granite countertop set to the raised lip of the island, making the stock cabinets fade in comparison to its sinuous line and lustrous presence.
Structure was simplified to reduce costs. Two framing bays, one on the kitchen side of the house, the other on the living-room side, are supported by a central beam, which in turn is supported by two columns. The roof is a symmetrical gable tied together by the ceiling of the second floor, which forms the floor of the attic. The roof peak soars to create a large attic, with windows that allow natural light. When combined with a full basement, this small house functions much larger than you might expect.
People Power
It’s not just design that keeps cost down, it’s also the can-do spirit of the owners. The Johnstons themselves subcontracted out the electrical work and purchased cabinets and bathroom fixtures directly (all stock elements).
Knowing the limits that were present, the architect worked on an hourly basis using some of his lowest-billing dollar-per-hour employees and a sympathetic engineer to keep total design fees down to about 5 percent of the construction cost. Many questions were answered by phone, and e-mailed digital photographs often took the place of the architect’s on-site presence and detail drawings. The project was blessed with builders Sutherland and Krause, who had a wealth of common sense and hard-edged integrity and commitment in a situation with little or no budgetary leeway. They were local builders, interested in the community, who went the extra mile to make a tight budget into a beautiful house.
One of the main things that keeps home design fresh and challenging for residential architects is that no two scenarios are ever alike. In this case, an abundance of limits was overcome by the dedication of all parties concerned. “We are very happy with both the design and construction,” Nancy says, “and overjoyed that we are able to stay on the water and stay connected with our family heritage.”
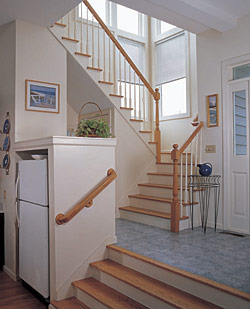
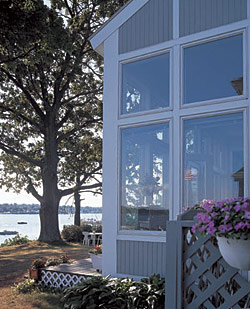
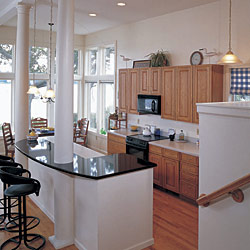
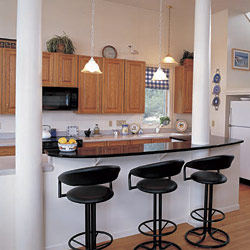
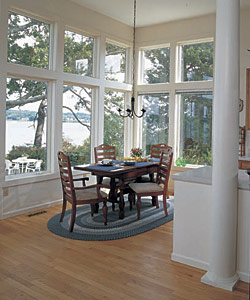
Duo Dickinson is an architect in Madison, Connecticut. Photos by: Ken Gutmaker