What's the Difference: Metal-twist drill bits
High-speed steel, black oxide, titanium, or cobalt
Although twist-type drill bits easily bore holes through wood, plastic, and composite materials, they’re really designed to drill through metal. Back in the day, each type of bit had a particular point configuration that was easily distinguished by its color and material. For example, when you picked up a high-speed steel bit, also known as a “bright” bit, you knew it had a 118° chisel point on it. When you picked up a cobalt bit, you knew it had a 135° split point. Now the market is saturated with each kind of bit in a variety of different point styles. Understanding how each type of material affects a bit’s performance is still important.
High-speed steel
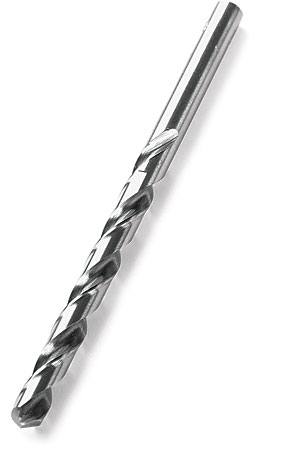
High-speed steel differs from ordinary steel in that it is alloyed. During the heat-treatment process, it becomes extremely hard and wear resistant. The harder a drill bit, the less friction is created when drilling, and the longer the bit will last.
Cost: Low, around $2 per 1⁄4-in.-dia. bit
Best uses: These bits are great for general use in soft to medium-hard materials.
Drawbacks: This bit isn’t strong enough to perform well in hard metal like alloys and is still often found with a 118° chisel point, which leads to the performance issues described in the sidebar at right
Black oxide
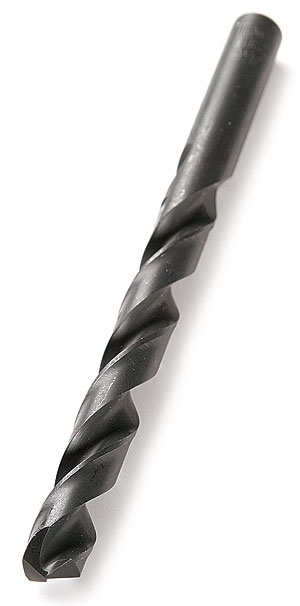
The base material in a black-oxide bit is high-speed steel, so the performance characteristics are very much the same as an uncoated version. The black coating is added for looks and offers a small amount of corrosion protection.
Cost: Low, around $2 per 1⁄4-in.-dia. bit
Best uses: These bits are great for general use in medium-hard materials.
Drawbacks: The blackening process of these bits creates a slightly porous surface that tends to pick up pieces of softer material. This additional material increases friction and wear, so these bits shouldn’t be used in soft metals like copper or aluminum.
Titanium
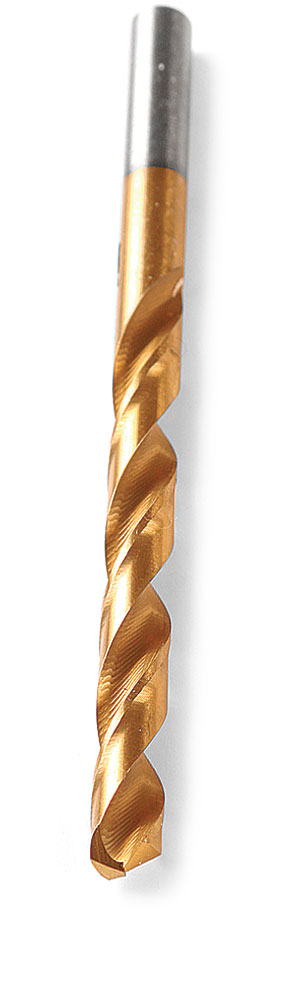
Like black-oxide bits, the base material of a titanium bit is high-speed steel. A 1-micron- to 3-micron-thick coating of titanium nitride is added to the bit to increase its hardness, lubricity—which reduces friction and wear—and overall durability.
Cost: Medium, around $4 per 1⁄4-in.-dia. bit
Best uses: These bits are good in repetitive drilling applications through hard metal like plain steel.
Drawbacks: Besides their higher cost, these bits have one other major drawback: When sharpened, the titanium coating is removed from one of the three primary cutting surfaces, resulting in a bit that never performs as well as a new one.
Cobalt-steel
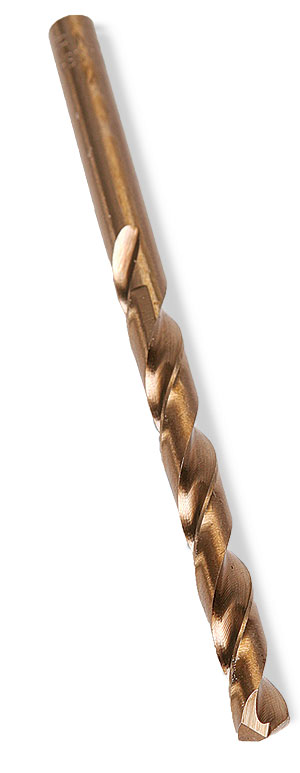
There are two types of cobalt-steel bits: those rated as M-42, which contain 8% cobalt, and those rated as M-35, which contain 5% cobalt. Both types perform adequately for the most-demanding metal-drilling tasks.
Cost: High, around $5 per 1⁄4-in.-dia. bit
Best uses: These bits go through extremely hard or abrasive metals like stainless steel, cast iron, or titanium alloys.
Drawbacks: Unfortunately, as the hardness of a bit increases, so does its brittleness. As the hardest solid-material bit available, a cobalt-steel drill bit is the most wear resistant, but also the most susceptible to breaking.
Point styles
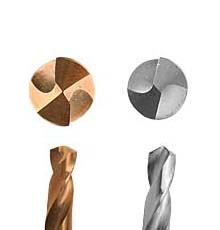
A 135° split-point drill bit (left) performs better than a 118° chisel-point bit (right) for a couple of reasons. A split-point bit has an offset tip that cuts into material on contact, but a chiselpoint bit displaces material until the bit’s cutting edge engages the material. Because of this quality, a chisel-point bit demands greater initial pressure and has a greater tendency to “walk,” which can lead to damaged surfaces or asymmetrical holes. A 118° chisel point is less expensive, though, because it doesn’t require as many grinds during the manufacturing process.
Photos by: Krysta S. Doerfler