Warm Floors on a Tight Budget
Using factory-assembled pieces and swapping a boiler for a water heater can lower the cost of radiant-floor heating systems.
Synopsis: For many years, radiant-floor heating systems have been too pricey to entice many homeowners. According to contributing editor Scott Gibson, however, with simpler, less expensive heating systems and factory-assembled components now on the market, some companies are trying to make radiant-floor heat a bigger player. To generate cost savings, newer radiant-floor heating systems are replacing expensive boilers with more affordable water heaters. Also, some suppliers sell systems online. Radiant-floor heating systems are available as either closed or open systems. Closed systems circulate the same water or glycol in an isolated loop. Open systems access the water used in household plumbing. Open systems can be indirect or direct. In indirect systems, water used for heating is separated from water for household use; in direct systems, however, the same water is used for heating and for household use. This article includes sidebars on water-heater vs. boiler usage; the way a condensing water heater works; the controversy over the health safety of direct systems; and a first-person commentary about installing a radiant-floor heating system ordered online.
Our radiant-floor heating system is everything the heating contractor said it would be: quiet, efficient, and unobtrusive. The heat is even. There’s no blower noise and no radiators to arrange furniture around. I like everything about it—except what it cost.
The three-zone system, designed around a German-built Viessmann boiler, cost $29,000 when our 2100-sq.-ft. house was built three years ago, or roughly $14 per sq. ft. That’s apparently not out of line with national averages for a system with similar components, but it’s more than forced-air or conventional hydronic heat would have been.
After getting an estimate like that, some homeowners take a deep breath and go ahead anyway, but many run the other way. Despite a number of attractive features, radiant-floor heat accounts for as little as 5% or 6% of the U.S. market, according to the Radiant Panel Association, and high cost is certainly one of the big reasons why.
That’s exactly what a variety of parts suppliers and system designers would like to change. By using simpler, less expensive heating equipment and factory-assembled components, companies such as Warm Floors, Radiantec, and Hannel Radiant Direct are making radiant-floor heat more competitive with conventional hydronic systems. In the process, they’ve touched off a war of words with more traditionally minded plumbers and mechanical contractors.
Conventional systems usually include a boiler
The basic idea behind a radiant-floor heating system is pretty simple: To keep the house comfortable, all you have to do is pump heated water through loops of plastic tubing placed in or under the floor. Tubing can be stapled to the bottom of subflooring, encased in a concrete slab, or inserted in grooves formed in special types of subflooring.
No matter how tubing is deployed, the system needs a way to heat water. The Radiant Panel Association estimates that in 90% of all radiant installations, water is heated in a boiler, the centerpiece of conventional radiator and baseboard fin-tube hydronic systems.
Boilers are ideally suited to produce water in the 160°F to 180°F range, just what most hydronic systems require. Boilers can be equipped with sophisticated controls, such as outdoor resets that regulate water temperature according to demand, and mixing valves to regulate water flow and temperature. They also can provide domestic hot water via an indirect water heater or a heat exchanger inside the boiler itself. All this probably explains why most heating contractors continue to specify boilers in radiant-floor designs.
Boilers and related controls, however, can be expensive. Our Viessmann (www.viessmann.com) is the Mercedes-Benz of boilers, as the installer put it, but it cost $2100, not including the $1170 indirect water heater or the $965 mixing block. Other controls were extra. That is one of several reasons why radiant-floor systems are expensive, but by no means the only one. Labor is another. If a heating contractor or plumber does the work, high labor rates add up quickly. Radiant systems also tend to be designed and built one component at a time by an on-site contractor, so each system is essentially a custom installation. Add it all up, and what you get is expensive.
Water heaters replace boilers
One of the selling points for radiant-floor systems is that water temperatures can be relatively low, meaning less energy consumption. Unlike radiators or baseboard systems that require 160°F water, a radiant-floor system typically needs water lower than 120°F. That’s why using a conventional boiler in a radiant-floor system doesn’t make any sense to Robert Starr, the owner of Radiantec (www.radiantec.com), a Vermont-based company that sells components for radiant-floor heating systems.
“Boilers are old school,” he says. “It’s technology that’s been around for 150 years. The idea is and was to make very-high-temperature water in a pressure vessel, to boil it. That’s what boilers do. But in fact, a boiler is not a very good way to make radiant heat. Radiant heat runs on warm water. It doesn’t run on steam.”
Instead of a boiler, Radiantec recommends the installation of a high-efficiency gas water heater. Polaris (www.polariswaterheaters.com), the brand that Radiantec sells, has a stainless-steel tank to resist corrosion and has a fuel efficiency of 95% or more, according to its manufacturer (sidebar left). Starr says that although high-efficiency water heaters are expensive, they’re still cheaper than a comparable boiler and are less complicated. As important, they’re designed for water temperatures compatible with radiant-floor systems and can be teamed with solar hot-water systems. In all, Starr says, it’s a perfect fit.
Replacing a boiler with a domestic water heater isn’t a new idea. Mike Luttrell, owner of Warm Floors (www.warm floors.com) in Napa, Calif., described that scenario in an article on radiant heat published more than 20 years ago (FHB #27). Given the right conditions of house size and insulation, a standard water heater can even be used in place of a more expensive condensing water heater, Luttrell says.
Open-direct systems are simple and affordable
Where Starr parts company with convention is in advocating open-direct systems in which the same water used for radiant heating is also used for bathing, cooking, and drinking. His critics gnash their teeth, but Starr says the approach is straightforward, inexpensive, and safe. “Our idea of a control costs about $70 and consists of an on-off relay,” Starr says. “A thermostat turns a pump on, and that’s all there is to it.”
Radiantec says the cost of materials for a two-zone, open-direct system in a 2500-sq.-ft. house is roughly $7500, or $3 per sq. ft. That price includes a Polaris water heater, but not installation.
Owner-builders or contractors who install the tubing themselves might need a plumber for making final connections.
Starr is not the only one with a simpler-is-better approach, or the only one selling open-direct systems. In addition to Warm Floors, Hannel Radiant Direct (www.radiantdirect.com) also designs and factory-assembles radiant packages, including open-direct layouts, at prices below industry averages for custom systems.
But there’s a catch. Although the International Code Council (ICC) accepts open-direct radiant-floor heat and in February 2008 voted against outlawing open-direct systems, some local jurisdictions still do not allow them. Anyone planning to install such a system should check with local code officials first.
Indirect systems separate heating, potable water
Both camps in the debate over open-direct systems see merit in designs that incorporate a water heater instead of a boiler, and that maintain separate heating and domestic hot-water loops.
There are two ways to do this. One is by running water for radiant heat through a dedicated water heater separate from the potable-water system. Although that eliminates the potential for bacterial cross-contamination and keeps down costs, it also means the homeowner has to buy a second appliance for heating domestic water.
Another option is to heat both domestic water and radiant water with a single water heater, but to separate the two halves of the system with a heat exchanger. In these indirect systems, the heat exchanger can be an external flat-plate heat exchanger or part of a specialized water heater, such as the Combi Core made by Laars (www.laars.com). Stainless-steel heat exchangers add several hundred dollars to the cost of a system and are marginally less efficient because the heat exchange between the potable and heating sides isn’t perfect.
Indirect systems have many of the same cost and simplicity benefits as open direct, as well as the same limitations. Water heaters, for instance, are “dumb,” meaning they don’t have the more sophisticated temperature controls found on boilers. Once the thermostat is set, that’s it; water in the heating loops can’t be adjusted for outside conditions. Water heaters also have shorter warranty periods than some boilers. Our Viessmann came with a 20-year guarantee, but the Polaris tank is guaranteed for 10 years and the Phoenix for seven.
Yet indirect systems eliminate concerns that Legionella bacteria might infect potable-water supplies. Even York, Pa., plumber Dave Yates likes them in certain situations.
“Obviously, the simpler you keep a heating system, the less expensive it’s going to be, both upfront-cost-wise and in long-term maintenance cost, but it might not be the least expensive to operate,” Yates says. “That’s the rub.”
Time for lower costs
Larry Drake, executive director of the Radiant Panel Association (www.radiantpanelassociation.org), sees an industry that has chosen not to make radiant heat as simple or as financially accessible as it could be.
“As I tell people in our industry, if we want to stay a small niche market serving high-end custom homes, keep doing what we’re doing,” he says. “But if you want a lot of people to enjoy radiant heating, there’s got to be some significant changes made in our industry in the way we do things. We have to simplify.”
Comparing a water heater with a boiler for radiant-floor heat
After comparing the Viessmann boiler system installed at my house in Maine to an owner-installed open-direct water-heater system designed for the same space, I came up with almost identical results until I reached the installation costs. Due to the complexity of the job, the amount of supplemental equipment required, and a plumber’s labor, the boiler’s installation costs were at least three times more than the water-heater-based system. However, different types of equipment, designs, and regional markets affect a boiler system’s cost, so it’s always a good idea to research options before spending any money.
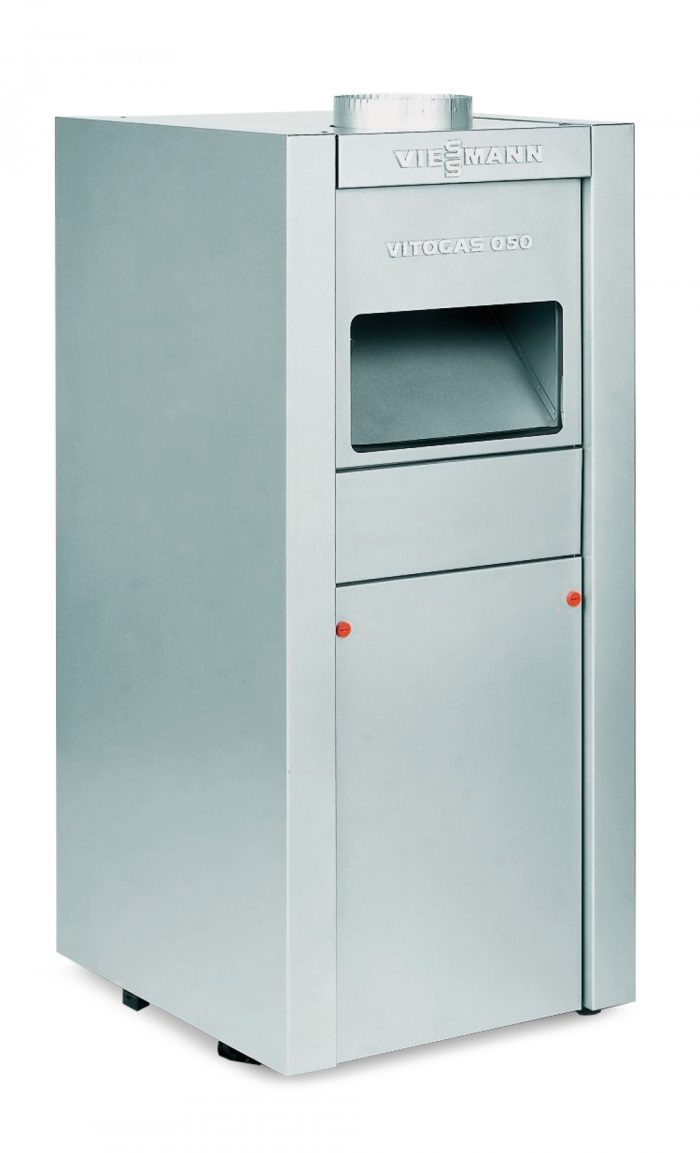
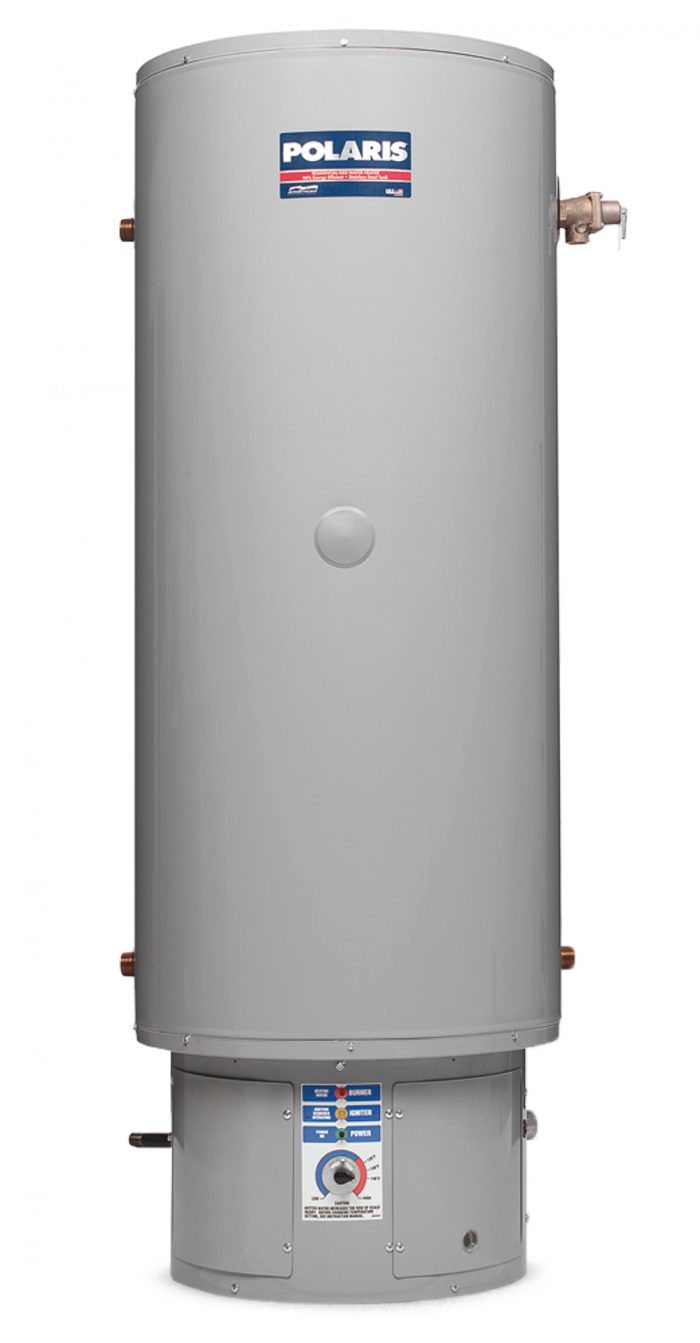
- Unit cost
- Water heater – $4000
- Boiler and controls – $4200
- Efficiency rating
- Water heater – 95%
- Boiler – 95%
- Installation cost
- Water heater – $3 to $4 per sq. ft.
- Boiler – About $14 per sq. ft.
Inside a condensing water heater
Standard water heaters that burn natural gas or liquid propane (LP) lose a lot of heat through the flue. In contrast, high-performance condensing water heaters extract heat from flue gases before they exit the tank. Among the brands now on the market are Polaris (drawing below), made by American Water Heaters (www.americanwaterheater.com), and Phoenix, manufactured by Heat Transfer Products (www.htproducts.com).
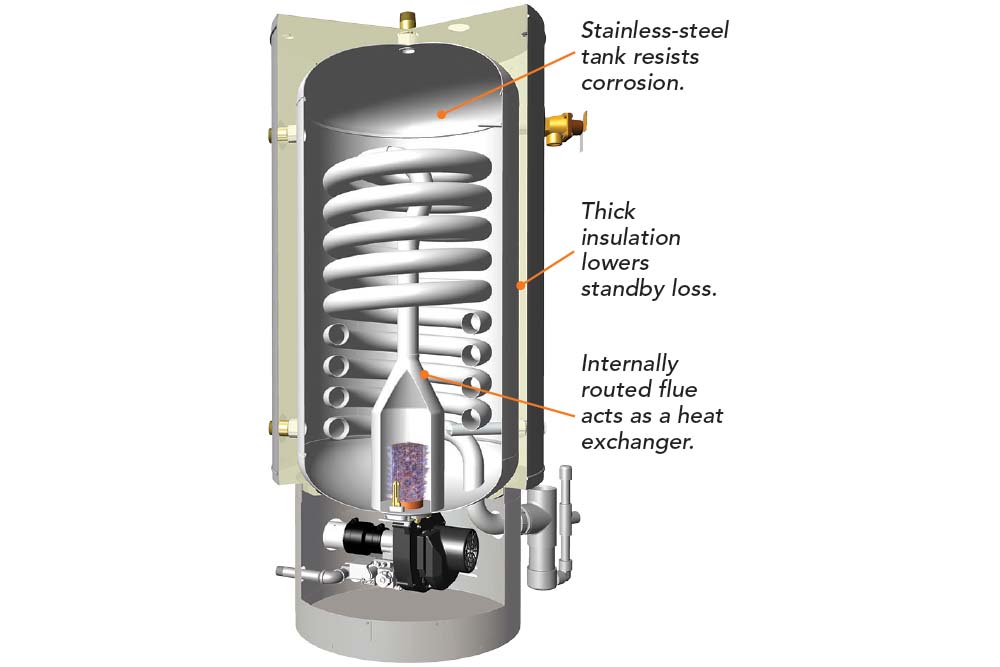
According to the U.S. Department of Energy, most gas water heaters are about 65% efficient and have standby heat loss of about 6.5% per hour. According to their manufacturers, both the Polaris and the Phoenix are more than 95% efficient and have enough insulation to minimize standby heat loss to 1% or less.
These condensing water heaters produce enough hot water to provide potable water and radiant heat simultaneously. Fifty-gal. Polaris water heaters, for example, are rated for an input of 130,000 Btu to 199,000 Btu, compared with the 42,000-Btu input of the average 50-gal. water heater available at The Home Depot.
One source for both water and heat
In a traditional boiler-based radiant system (not shown), the heating medium (water or glycol) remains in a closed loop. Domestic hot water can be heated by a dedicated water heater, or it can be heated in the boiler and stored in a separate tank. In systems based on a high-efficiency water heater, the configurations can be closed or open. In the latter type, potable water is the same water circulated in the radiant tubing. Although open systems have generated some controversy, their simplicity and lower cost make them an attractive option for radiant heat.
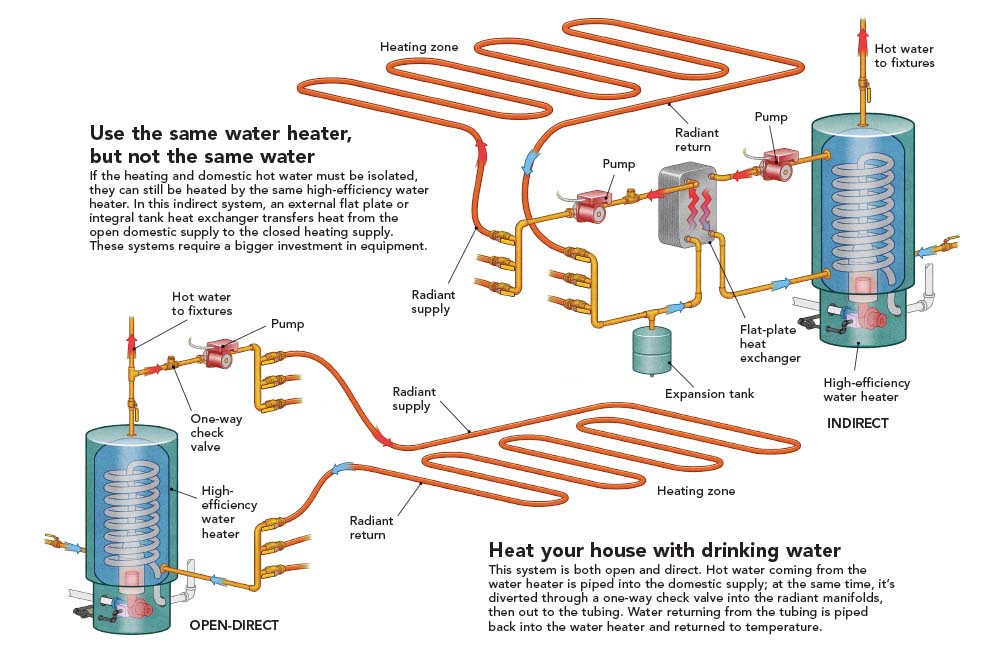
A sharp divide of opinion over potential health risks. Dave Yates, a Pennsylvania plumber and heating contractor, is adamantly opposed to open-direct radiant-heating systems. Yates and a group of colleagues filed a petition with the ICC to ban open-direct systems because they believe the systems pose a health risk that far outweighs any potential savings. The cause of his concern is Legionella, the bacteria identified in 1976 when 34 people at an American Legion convention died from a previously unidentified pneumonia now known as Legionnaire’s disease.
Legionella is an aquatic bacteria that multiplies when conditions are right: stagnant water between 68°F and 122°F and the presence of sediment or “biofilms” in water lines that can be a food source. People become infected by inhaling a water aerosol that contains the bacteria. Yates and others contend radiant-floor heating systems present perfect conditions for “bacterial amplification” and that the contamination will automatically spread to the domestic-water supply in an open-direct radiant system.
To Robert Starr of Radiantec and others, the claims are overblown. Warm Floors’s Mike Luttrell, a heating contractor for 30 years, says the real reason for controversy has to do with protecting profit margins, not health.
The Centers for Disease Control and Prevention says Legionella colonization is already “extremely common” in residential plumbing systems. Although the agency says an open-direct system “certainly sounds like it may create conditions that would be favorable for Legionella growth,” no reports linking the bacteria to open-direct radiant-heat systems have been recorded.
Building new or remodeling, you have choices for warm-floor installations
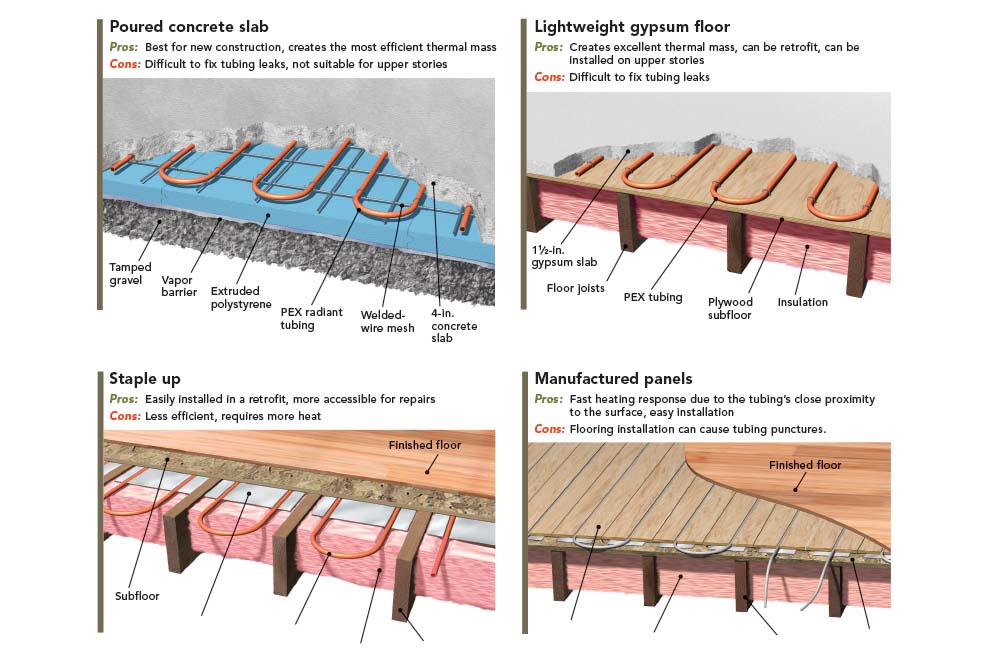
Buying radiant online
Although most heating systems are put together by local heating and plumbing contractors, you can buy a radiant-floor heating system over the Internet, believe it or not. A number of companies offer components online, including Hannel Radiant Direct in Spokane, Wash. We asked Hannel’s owner, Gunnar Evenson, how that process works and roughly how much it would cost if we ordered a staple-up radiant system for a 2100-sq.-ft. house. Our open-direct system would supply both domestic hot water and two heating zones with a high-performance gas water heater.
How it works. Hannel starts by assigning a salesperson to the job and directing the prospective customer to an
online questionnaire that collects information including house size, location, and system preferences. Hannel also requests project plans, typically in the form of a CAD file. With this information, the company produces a quote within two weeks. Once plans and price are finalized, it takes two weeks or less for the system to ship. With components on hand, the customer starts installation. A detailed Hannel manual and company technicians available by phone provide support. Hannel also suggests lining up a local professional who can provide help if you hit a snag.
What you get. Evenson says Hannel sends a “completely assembled” panel that includes a brass manifold, a bypass valve, controls, and quick-mount pump flanges, all of it pressure and electrically tested. This system includes a 100,000-Btu, 34-gal. Polaris water heater with a trim kit already mounted. Controls would be relatively simple connections between zone valves on the manifold and a thermostat for each zone. Valves built into the manifold open and close with thermal actuators. For an open system, Hannel supplies a brass pump with a replaceable cartridge to simplify repairs. The order also includes 3500 ft. of 1⁄2-in. oxygen-barrier PEX tubing. All fittings are compression or threaded, so no special crimping tools are required. Plumbing for the domestic side is the responsibility of the homeowner. Hannel recommends that a licensed gas technician install the water heater.
How much it costs. For our hypothetical project, Hannel estimates the cost at no more than $8400, or about $4 per sq. ft. of heated space. Installation and assembly of the parts is up to the buyer. Of the total, Hannel says the water heater and related plumbing account for between 40% and 50% of the cost. While relatively expensive, the Polaris can provide heat and domestic hot water that conventional water heaters can’t. Manifold, pumps, and controls make up 25% to 35% of the total. Tubing and related materials make up the rest. Shipping is included in the price. Each component in the system is guaranteed by the manufacturer. Warranty claims and replacement parts are
A first-time customer reports
I first learned about open-direct radiant systems a few years ago when I worked on a Fine Homebuilding article, “Energy Efficient From the Ground Up”. At the time, I was impressed with the simplicity of the system. I didn’t have a lot of money to spend when it came time to start my own renovation, so I contacted Radiantec to order a system. After calculating the theoretical heat loss for my house, we settled on an open-direct system consisting of a 34-gal., 100,000-Btu water heater and enough plumbing for three separate zones. Radiant heat can be expensive, but because I could install it myself, it cost only about $11,000, which included hiring a plumber for the initial water-heater hookup. The materials alone cost $8500.
At first, I had some trepidation about installing the system myself (I’m a carpenter, not a plumber), but overall, it went extremely well. Customer service was very good. When I had a problem, I called the help line and could tell that the techs had lots of field experience. I was also reassured when one of my plumbers, initially leery of the quality, gave the components his blessing. Although the installation took a few days of hard work, the heat is on, and the system really delivers. I like the fact that I have the ability to fine-tune the zones, too. If the kitchen is too warm, I can adjust the temperature by just opening and closing a valve. Finally, any questions that I might have about the long-term reliability of the system (and the water heater in particular) come down to this: It’s relatively inexpensive to replace the water heater, unlike a big and complicated boiler.
-Former FHB editor Chris Green is a builder renovating his own home in New Milford, Conn.
Photos: Roe A. Osborn; Charles Bickford; courtesy of Viessmann Werke GmbH & Co.; courtesy of American Water Heaters. Drawings: John Hartman; Toby Welles/WowHouse; courtesy of American Water Heaters.
Related stories:
- How to Choose the Right-Size Heating and Cooling System
- Radiant-Ready Subfloor
- Choosing Boilers and Controls for Warm Floors
From Fine Homebuilding #201
For more photos, drawings, and details, click the View PDF button below: