What's the Difference: Circular sawblades
Today's circular sawblades feature a variety of tooth grinds specifically designed to handle a multitude of cuts and materials
If you’ve recently looked into replacing the blade on your circular saw, miter saw, or tablesaw, you might be puzzled by the range of tooth grinds available. Early versions of these sawblades had only teeth with tops that were ground flat. Now, manufacturers produce an array of tooth grinds. Some are designed to cut faster, some to cut smoother, some to cut cooler, and some to handle the growing number of composite materials encountered on the job site. Here’s a look at the five most common styles on the market.
Flat-top grind (FTG)
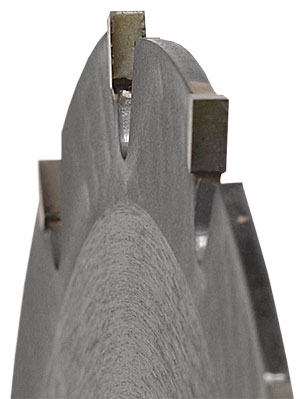
An FTG tooth configuration is designed to cut and rake material out of the sawkerf efficiently. Because of their high rake angle, these teeth aren’t as sharp as other designs and need to be pushed through a cut with more force. Some FTG blades are made with thick plates and large carbide. It’s a rough-cutting design, but it provides a lot of impact resistance. FTG blades are easy to manufacture, so they often cost the least.
Best uses: FTG blades can be used to cut anything from softwood to nonferrous metals, and they excel in circular saws used for demolition work, where the quality of the cut is less important than the life of the blade.
Alternate top bevels (ATB)
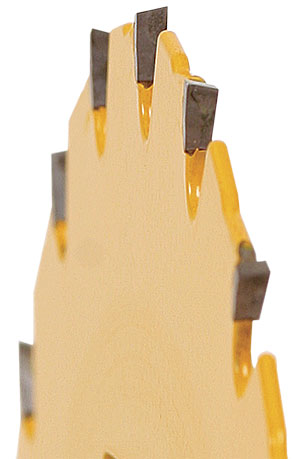
Designed both to rip and to crosscut efficiently, ATB-shaped teeth are common in all-purpose blades. In the past, this design did not do as well when ripping, but this quality is less of an issue with newer thin-kerf ATB blades. ATB blades are sharp but are typically less durable than other tooth grinds, which results in a shorter life. Many manufacturers are now integrating specialized carbide into their blades to overcome this shortcoming.
Best uses: ATB blades perform well in circular saws and miter saws whether cutting LVLs, I-joists, flooring, oriented-strand-board (OSB) sheathing, or pine studs. Some versions can even be used to cut aluminum and steel.
Combination tooth (Comb.)
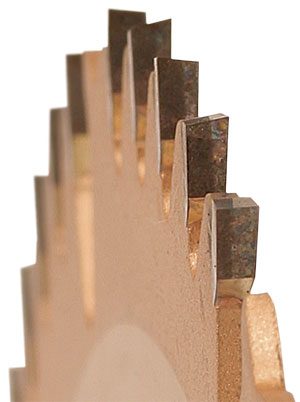
This design typically groups teeth in sets of five—four ATB teeth followed by a single FTG tooth—with a large gullet between each set. Designed for both ripping and crosscutting, the gullet allows for better chip ejection. This blade can be called a jack-of-all-trades but a master of none; it provides acceptable results when cutting through a number of different materials.
Best uses: This blade can be used in any saw, but it performs best when used in a tablesaw. Its tooth grind and configuration allow it both to rip and to crosscut all wood species and composite materials well.
Triple-chip grind(TCG)
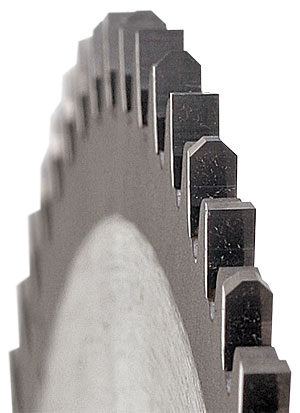
Most TCG blades are manufactured with a flat-ground tooth placed between two teeth with beveled edges. These teeth are slightly taller than the flat teeth and hog off the bulk of the material. The flat tooth chips away the corners left in the bottom of the kerf. This tooth configuration results in a slower cut, but it helps to keep the blade cooler so that it lasts longer and gives better results on heat-sensitive materials.
Best uses: TCG blades are best used for cutting hard materials like MDF, OSB, melamine, laminate countertops, solid-surface materials, and some plastics. Although they won’t scream through material like some other blades, they are handy to have for all saws.
High alternate top bevel (HiATB)
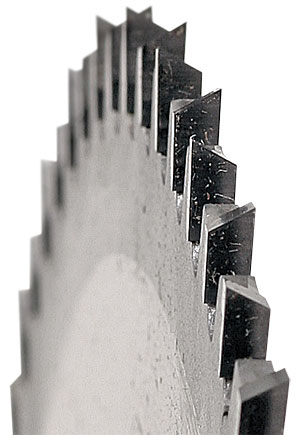
These teeth are ground just like regular ATB teeth, only the bevel angle is much more severe—between 30° and 38°. The higher bevel angle creates a V-groove down the center of the blade and increases the sharpness of the blade and the crispness of its cuts.
Best uses: HiATB teeth are designed for extrafine cutting tasks in sheet goods like melamine and cabinet-grade plywood, which are prone to chipping. These blades are most useful in a tablesaw.
Photos by: Krysta S. Doerfler