Carving a stair railing transition
The following text were sent to us by Seth Kiser, a trim carpenter in Anacortes, Washington. Look for more of Seth’s take on stairbuilding in the future, both here and in the magazine.
I have been a carpenter for over 16 years and have specialized in stairs and railings for the past 9. Over the years, I have witnessed many carpenters and homeowners scratch their heads in frustration from stairs and railings. To many, railings seem to hold a mystery. My hope with this article is to simplify one aspect of railing installation.
One of the most common problematic issues for wall mounted railings is what to do with the railing when the stairs make a turn. If the stairs make a turn and have a landing, the code stipulates the landing is a separation between the flights and allows the railings to be separate and terminate into the wall. However, many times limited space doesn’t allow for landings and require pie-shaped treads, making it a winding stair. Along with other requirements pertaining to rise and tread size, the code mandates a continuous handrail. As most people who have installed handrails have learned, when a stair turns, the handrail must twist to follow the stair. To my knowledge, there are but 2 options for a wood handrail to turn:
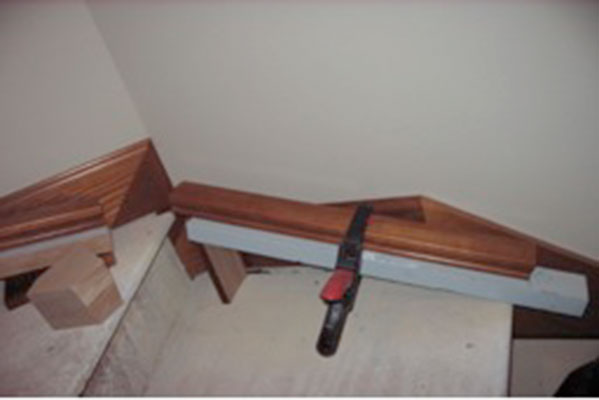
First is for the rail to go from pitched, level out, turn the corner, drop down (usually with a goose necked part), then resume the angle of the stair.
Second is a part that both turns and twists, which is a hand-carved part.
My goal here is to give step by step instruction on how to produce a hand carved part, from layout to final installation. It is my opinion that in many cases this produces the most aesthetically pleasing option.
1. I start by laying lengths of scrap material across the noses of the treads. (photos 1 and 2) This establishes the angle or pitch of the stair. I nail the scraps directly to the treads. This gives me something to clamp the rail to while I fit the block to be carved. Once I have the angles, I shim the scraps then cut them back so they don’t interfere with the fitting of the block.
2. Next, I cut clean, square ends on two lengths of rail and space the rail pieces the exact distance from the wall that the rail will eventually be mounted and slide them up or down to roughly the same distance from the corner (this will ensure a uniform part), and clamp them down. The space between the two rails is arbitrary, just keep in mind the bigger it is the more to carve but will produce a more gradual turn. I usually try and gage the part to be carved by the size of the rail, the smaller the rail, the shorter the part.
Once the rail pieces are clamped down, I go to work fitting the block to the two rails. The block is of the same material as the handrail, hemlock in this case. You could glue something up. I buy a square 4×4 post from my stair parts distributor (Johnson Postman) and am able to use the post for several jobs. Because this stair turns 45 degrees, I start by cutting the block 22½ degrees on both sides, bigger than is necessary, and then adjust the cuts until the block fits tight to both rails (photo 3).
3. After I have established a perfect fit, I scribe the outline of the rails onto the block (photo 4). Then mark for the rail bolts, 7/8” up from the bottom and centered side to side for the bolt. Depending on the size of the block, the bolts may need to be cut down so they don’t meet in the middle of the block.
I usually like to carve against scrap pieces of rail so if I slip, it doesn’t ruin the rail. When this is the case, I put a small dot of glue between the parts when I bolt them together, this makes sure the parts don’t move during carving, yet is easy to break loose once I’m done. (photo 5).
4. After the parts are carefully aligned with the marks and bolted together, I mark out the general shape of the part. I have found it is handy to have a clamping work bench to clamp the work piece down. Then I go to work with my angle grinder. I try to match the grit of the paper to the density of the wood, 36 grit for maple, oak, and jatoba. In this case, 60 grit for hemlock. I start cutting down the bulk of the material, no details, just the general shape.
I work the piece from all sides, gradually bringing it down to size. I stop here and there to reestablish the shape.
Once the general shape has been ground down, I’m finished with the grinder.
5. Next, it’s just a matter of drawing lines between the two rails for the details. The dremel is the tool for this job. Again, I take my time to whittle the piece down to the details. I work the part down with my dremel as far as possible, then grab my chisels. I use a skew chisel and a flat chisel to even out the profile. Once I’m as far as the hand tools can go, I hit the areas I can reach with my random orbital and hand sand the tight spots.
Once I get down to this stage, I let my hands tell me how far to go. I run my hand over the piece until I am satisfied with how it feels. Here is a picture of the piece with all the tools I use to produce the finished product (photo 6). From layout to here takes me about 2 hours.
6. After the part is finished, the hard part is over. So I start putting the rest of the handrail together. I like the top of the rail 36” off the nose of the treads. After I subtract the depth of the rail, I set the brackets at about 34”. On a wall mounted handrail, I always build the rail in place. This way, I can be assured that everything will fit and won’t be tweaked when the handrail gets fastened to the brackets. I fit the wall returns last, so I can scribe them to the wall if necessary.
Photos and text by Seth Kiser, Anacortes, Wa
Fine Homebuilding Recommended Products
Fine Homebuilding receives a commission for items purchased through links on this site, including Amazon Associates and other affiliate advertising programs.
Handy Heat Gun
Affordable IR Camera
Reliable Crimp Connectors
View Comments
This website format makes it very hard to follow along with the photos and the format of this site make no sense.
I agree that the article layout is a bit odd... but looking past that and on to the important aspects… I’m very appreciative of the information.
I’ve faced this dilemma with fence caps meeting at odd angles couple of times and wondered how best to solve it. In the case of fences, hand carving is a bit over the top, but this answers my question and provides me with a method that could very well come in handy in the future.
Thank you for settling this for me.
Makes for a beautiful smooth transition and well executed. From layout to finished part, 2 hours is fast. How did you handle the dust? Maybe we can see a final installed on the wall photo next time.