There’s a raised ranch house going up next door to my house in Plainville, CT. The 7-man framing crew finished their work today, so I snuck over after work to peek at the quality of their work. I watched these guys as they worked, and they were efficient and hard-working. The quality of work and final look of the frame was pretty solid, telling me that they’re not a fly-by-night crew of Bubbas. But it bummed me out to see that they weren’t thinking very progressively or operating with a full knowledge of their profession.
Bump outs need weatherization, too
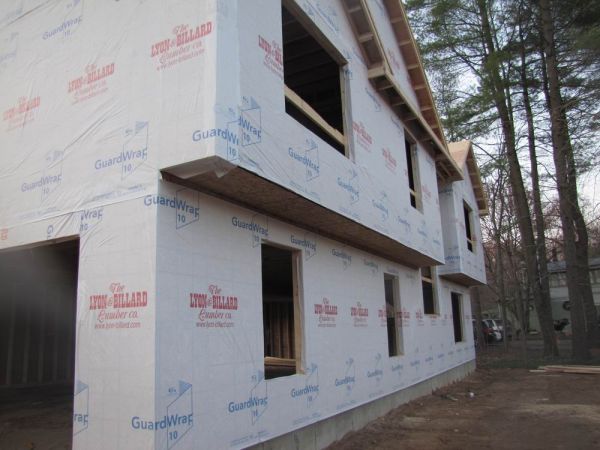
The housewrap was rolled out smooth, fastened well enough (staples were used instead of cap fasteners, but I’ll cut em some slack on that…), and the joints were lapped appropriately. BUT, they forgot the bottom of the bump outs and didn’t run the wrap all the way up to the top plate of the second floor.
These two areas make it pretty obvious that the framers don’t really understand what a weather-resistive barrier (WRB) is designed to do. It’s not just for keeping out water, but air, too. How does heat move? On air. Wrap it up fully, please. Also, don’t forget to add blocking and adequate insulation to the underside of those bumpouts. Those spots are going to be mighty cold otherwise.

For more information on this, read “Making Sense of Housewraps“
2x6s are great, but take advantage of their extra strength
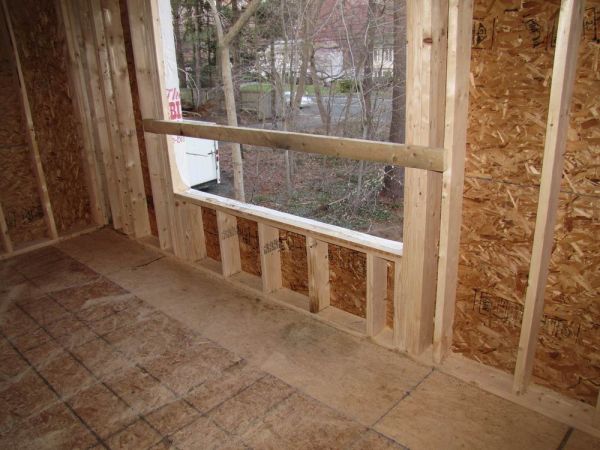
I think framing walls with 2x6s instead of 2x4s is a great idea. It leaves far more room for valuable wall insulation, something that will become more crucial when the 2009 version of the International Residential Code is adopted.
But if you’re going to frame with 2x6s, why not take advantage of their extra strength and space your studs 24 inches on center instead of 16 inches on center? While you’re at it, replace the OSB sheathing with an inch of rigid foam.
Don’t think it’s worth the trouble? Well case studies have proven that those two improvements will reduce your lumber bill by around $2,000 for a 2,000 square foot house and drop heating/cooling costs by around 30%.
That’s more money in your pocket and more insulation in your customer’s wall. Just make sure that if you start with 2x6s, you do the whole job with 2x6s…don’t cheat to save space like they did on the side of the bumpouts shown in the photo at right.
For more information on this, read “The Future of Framing is Here“
The sun offers free heat in cold climates. Use it.
Other than being architecturally horrific, this wall is missing out on some free energy. Flip your floorplan so that the bedrooms and living room are on this side and the unconditioned garage is on the North side, where heat isn’t beneficial.
Design it right, and the same south-facing wall will keep the hot summer sun out, too.
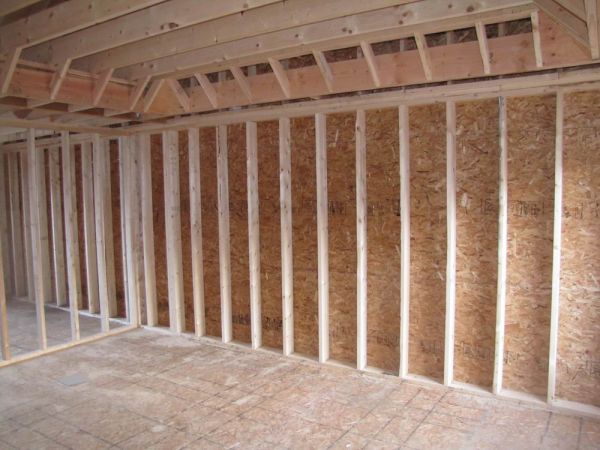
For more information on this, read “Drawing Board: Designing Sunscreens“
Fine Homebuilding Recommended Products
Fine Homebuilding receives a commission for items purchased through links on this site, including Amazon Associates and other affiliate advertising programs.
Handy Heat Gun
Affordable IR Camera
8067 All-Weather Flashing Tape
View Comments
dont disagree with the article at all, just putting in a word for the poor framers...
those guys did miss the wrap concept but all else is not up to them. they look at a drawing, read off dimensions, and use the material provided. the builder and architect should know better!
Mark,
That's a good clarification to make, because I didn't intend to "blame" this all on the framers. It's the whole thought process that needs to be addressed. Thanks for your comment.
Bump outs are just extra surface area that will conduct heat. There essentially unnecessary. Certainly the designer/architect could have found ways to end up with the same square footage without a bump-out. But then if the customer wanted a bump-out!
Supplying energy to make up a house's heat loss is a deign failure. Design failures are the designer's fault, particularly now when a house's building energy demand can be easily modelled at the design stage.
The pictures look like a tidy framing job. As builders, we have structure down, insulation and weather proofing is another story.
Adding an inch of insulation to the exterior works in most climates but in colder climates exterior foam board can create a double vapor barrier. The REMOTE wall system advocated by the Cold Climate Housing Research Center puts all the insulation on the outside wall eliminating the double vapor barrier concern. Insulation is one of the few things that a homeowner will buy once and have the return on investment over the life of the home.
I understand the energy and cost advantage of replacing the OSB with rigid foam, and I can be convinced that with appropriate strengthening at the corners the structure would be strong enough, but emotionally I can't accept that it would be a real house. Especially with vinyl siding used so ubiquitously, it just doesn't seem secure; one could break into a house like that just by picking an out of sight wall and cutting through with a pocket knife! It seems more like a fancy tent to me, but I'll admit I'm the type to prefer a concrete bunker (aesthetically designed, of course). I think its important that houses be designed with more than just energy efficiency in mind, as extremely important as that is. Homes need to be a refuge from more than just water and temperature extremes.
Let's not attribute too much air sealing benefit from the housewrap. I'm old enough to remember when Tyvek, Typar and other wraps marketed themselves primarily for air control. Then when energy efficiency concerns diminished they marketed themselves as weather resistive barriers; and now they're singing the efficiency song again. In practice, it's very very very difficult to apply housewrap in a fashion that will halt air leakage. It's much easier to seal up rigid materials like drywall, wall sheathing and rigid foam panels than it is to detail housewrap.
On the framing side - in addition to the stud spacing, it appears from the photos that they did not use OVE framing techniques. I see double top plates, extra cripple studs under window openings, structural jack studs, boxed in corner framing.... Version 3 of the Energy Star Home program requires some advanced framing techniques. I think it's only a matter of time before the IRC moves towards requiring minimal framing as part of improving energy efficiency.
I'm going to guess that the framers were in their 20's and 30's - the amazing thing is that they were born in an era after OVE framing and housewrap installation best-practices were developed. Why is it they fall back on 60 year old practices? I'll bet they all have G-3 or G-4 devices.
Excellent advise! Although I might still be partial to an O.S.B sheathing under the rigid foam insulation boards.
Another cost to consider when using 2x6 wall framing is the need for extension jambs on the doors and potentially the windows as well.
Another area that troubles me is inadequate ventilation at the eaves. Common construction practices currently do not provide enough. This lends itself to ice dams and leaks season after season. (Up north, that is) I'm exploring alternative techniques to eleviate this problem in my designs.
http://www.caddcreations.net
[email protected]
Good article. Here is a thought though. why would the framer care... I have been in framing crews before where we have to fight tooth and nail to get the bid, so that means cutting costs. All of those things cost money. It seemed like every job we went to it was a struggle for the framers to make a decent pay cheque ( that is spelled right, I live in Canada) so we cannot spend the time to do things right. And yes I do believe we built them wrong. Come on, we built 2x6 with OSB, with "R20" insulation in Calgary. This is a city that sees at least 1 to 2 weeks of minus 40 in the winter. (-40 is the same in Celsius and Fahrenheit) And studies have shown that even a properly installed bat of R20 is more likely R14. But at least people can drive their diesel pickups to pick up groceries and then pull into their vinyl sided beige colored monstrosity, which looks the same as the neighbor, and then the other one.... and that one... and the one across the street.....
Brownmaker, funny, but all to true. As a builder/framer/renovator or counselor or what ever is paying in this market. It is always a sticking issue between the framer and the designer. I think the responsibility for energy and design falls with the designer/architect. Sure there are simple changes that the framer can make. But, once I receive a set of plans it already has been though the approval process with the owner and more importantly with the Building Dept.. I am not going to create more issues and possible delays in the project arguing that the 2x6 spacing can be wider. or lets use foam board instead of plywood. No, to late, those decisions should of been made way before build day starts.
I agree, I have been on siding crews and hired many siding co. I as a builder feel more confident with a plywood or osb sheathing then foam board. At least I know with 100% confidence that the siding (whatever type) is securely nailed into a solid sheathing . Unfortunately I can not rely on the siders to find each and every stud with every nail they bang in into foam board.