Getting the Right Concrete
Whether by bag or truckload, the correct concrete mix can make a project, and the wrong concrete can ruin it.
Synopsis: According to contributing editor Rick Arnold, concrete is the most versatile construction material you can work with. In this article, Arnold outlines the process for getting things right when you’re working with concrete, whether it’s by the bag or by the truckload. Concrete is made up of three main ingredients: cement, water, and aggregate (gravel and sand). Water activates the cement to form a paste that coats the aggregate. The strength of the mix is in its water-to-cement ratio; the lower the ratio, generally, the stronger the concrete. Concrete also can be tweaked with admixtures, which customize a mix. Admixtures include water reducers, air entrainers, retarders, fibers, fly ash, accelerators, and integral colorings. Code specifies concrete strengths for specific uses. Arnold includes information on determining the appropriate slump and the way to deal with concrete in very hot or very cold temperatures. This article includes sidebars on mixing your own concrete and on estimating the amount of concrete you’ll need for a specific job.
Concrete is the most versatile construction material you can work with. It can be formed to any shape and can be used for just about any purpose: footings, walls, roofs, floors, walkways. It can be poured from a wheelbarrow, a truck, or a pump. It can be placed during freezing or hot temperatures, dry conditions, pouring rain, and blinding snow. The beauty of concrete, though, is that you can manipulate and control its physical properties to create the perfect combination of strength, durability, workability, and cost for each particular use and condition.
The basics
Having a basic knowledge of the ways that the concrete mix can be altered to suit certain use requirements and to compensate for the various weather and pouring conditions you may encounter is crucial to making sure you have a successful project. If you’ve ever watched an experienced crew pour and work concrete, they make it look easy. That’s partly because they understand concrete; they know that they can adjust the mix to suit the job and the conditions. For example, a patio that’s poured in a cold climate on a damp 35°F day should have a different mix than a patio that’s poured in a hot climate on a dry 85°F day. The problem is that the consequences of an improper mix are not evident until it’s too late.
Even inexperienced builders, though, can have success with concrete if they know the available options and can communicate their needs to the batch operator at their local ready-mix concrete plant. Don’t worry; knowing the actual ingredients and ratios is not necessary. That’s the batch operator’s job. In fact, the batch operator is the best source of guidance in creating the ideal mix for the job because it’s in his best interest to ensure that your project goes well.
When I order concrete, I specify the strength, aggregate size, and slump, and then I discuss any physical limitations of the job, the weather conditions, and my desired level of quality. This allows the batch operator to give me a mix that suits all my needs.
Cement is the glue of concrete
When mixed with water, cement forms a paste that coats the aggregate in the mix. The cement cures and binds the ingredients together. Cement is available in five different types, but most are intended for large-scale or specialized projects. Type I cement is the most widely used, especially for residential projects.
The strength of concrete depends on its water-to-cement ratio: the lower the ratio, to a point, the stronger the concrete. The primary characteristic that you need to consider is the required strength for the use, which is measured in pounds per square inch (psi). Concrete with a psi of 3000, for instance, will withstand 3000 lb. of compression per square inch before breaking.
In many cases, building codes dictate the required strength of concrete. The IRC (International Residential Code) calls for concrete used in footings, foundations, and interior slabs (basements and garages, for example) to have a strength of 2500 psi. The concrete for exterior slabs (patios, for example) must be at least 3000 psi.
You may hear a seasoned concrete worker call in an order and identify the strength that he wants by stating a mix ratio (“1:2:2,” for example) or a number of cement bags per yard (“five-bag mix,” for instance). A good batch operator knows that the worker wants concrete with a certain psi strength, which he will provide, but not necessarily with those exact ingredient measurements. A more accurate approach is to identify the desired strength of the concrete in terms of its psi, which reduces the chance of misinterpretation.
Increasing the strength of the concrete above its specifications is perfectly acceptable, but if you are considering it because of job-specific structural concerns, then consult an engineer. About the only time that I increase the strength beyond what is required is when I plan to add water at the job site (which decreases the strength) to improve the concrete’s ability to flow for a hard-to-reach pour. Admixtures, however, are better than water in many cases, especially when it comes to flatwork like slabs or patios.
Tweak the load with admixtures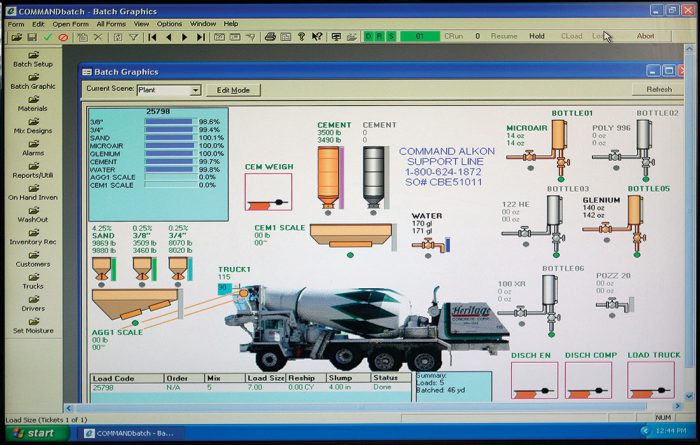
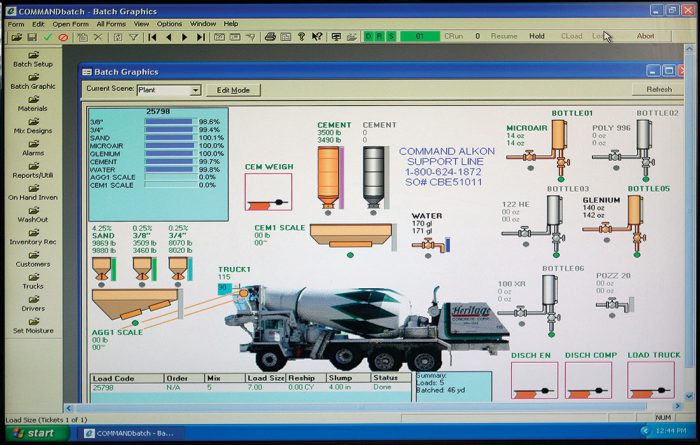
In addition to manipulating the concrete’s three main ingredients, ready-mix plants rely on an array of chemical and mineral additives, called admixtures, to customize a load of concrete. Admixtures typically are added to concrete to compensate for difficult jobs and uncooperative weather, and their beauty is that they don’t adversely affect the strength of the concrete.
1. Water reducers
The name says it all: Water reducers reduce the need for water. Generally speaking, you can add a water reducer to a mix without reducing the water, and you can create concrete that has a higher slump while still retaining its strength. If you add a water reducer and reduce the amount of water in the mix, the slump can stay the same while the strength of the mix increases.
Midrange water reducers are generally used for slumps of about 4 to 7, such as in flatwork, and they help to provide better workability.
High-range water reducers, also known as superplasticizers, help on jobs where a high slump—say, around 8 or higher—is required. For instance, a foundation wall that contains a lot of steel rebar, especially around the openings, can easily get clogged by a stiff mix; this creates problematic voids in the concrete. These water reducers are especially handy for stay-in-place forms such as ICFs, which are more prone to voids because of their internal structural webbing and because there is no way to inspect the concrete wall within visually.
2. Air entrainers
Air entrainers add air to the mix, forming microscopic voids throughout the cured concrete that allow for the expansion of water as it freezes. They’re a critical ingredient for the durability of exposed flatwork in regions that experience freeze-thaw cycles and deicing salt applications, and it’s required by code in many areas. If air entrainment is not added to exposed flatwork, the consequence is often a weak surface susceptible to spalling or scaling, where the top 1⁄8 in. or so of cured concrete pops off in chunks.
Air entrainers aren’t necessary for interior slabs and should be avoided on jobs that will receive a smooth trowel finish. This admixture also can lead to finishing difficulties if you plan to use a power trowel.
3. Retarders
Retarders are used to delay the setting time of concrete. The warmer the ambient temperature, the more quickly the concrete will set up, and the smaller the window of opportunity you have to work it properly. It’s a sure bet that on a hot day when you’re pouring a large slab in direct sunlight, one of your workers won’t show up. This situation is when a retarder is a lifesaver.
Quick set times can be anticipated on very hot days, and the retarder can be mixed in at the plant. Alternatively, it can be added to the truck before the pour as conditions require. A retarder also can be used as a water reducer.
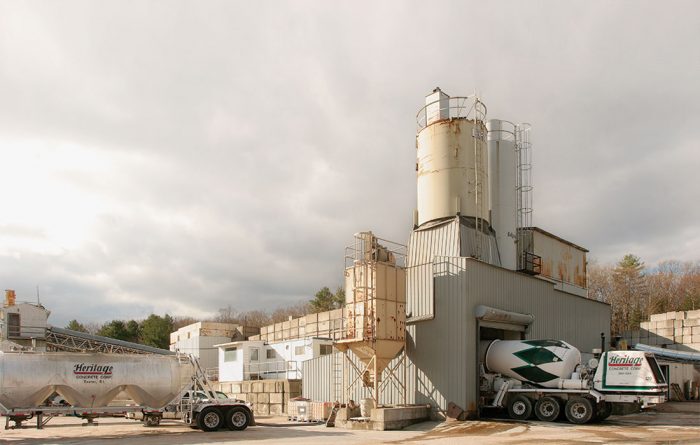
4. Fibers
Small synthetic fibers are mixed into the concrete to help prevent microscopic cracks from developing during the concrete’s plastic state, when cracking is a risk. These fibers can provide a more durable finished product that is less prone to problems. Some workers use fibers as a substitute for 6×6 welded-wire mesh in exterior flatwork, but I still include wire mesh because it helps to keep any cracks that do form from opening up.
5. Fly ash
Fly ash is the residue produced from coal combustion, and in concrete, it’s kind of like high-performance filler. Fly ash can replace a portion of the cement and/or sand in a mix with no detrimental effect on strength. In fact, fly ash can improve the performance of concrete. This is a great way to use industrial waste that would otherwise be headed for a landfill. Keep in mind, however, that fly ash usually acts as a retarder.
6. Accelerators
Accelerators are used to reduce the setting time of the mix without lowering the concrete’s intended strength.
For those cool-weather pours (temperatures in the 40s and 50s) where you don’t want to hang around for hours waiting to work the concrete after it has been poured, an accelerator cuts the wait time considerably. For pours where the temperature doesn’t get above freezing, it’s a good idea to add an accelerator to prevent the water in the mix from freezing. An accelerator shouldn’t be used in place of thermal blankets or other freeze-protection methods that typically are used to aid in the curing process of concrete poured in cold weather. I have also used an accelerator to give the mix early strength when I have needed to remove forms prematurely.
A warning: If the job contains steel rebar or wire mesh, you should avoid chloride-based accelerators because they can corrode the steel.
7. Integral coloring
Integral coloring, which changes the color of the entire batch of concrete mix, is an alternative to broadcasting a color across the surface after the concrete has been placed, or using stains or dyes after the concrete has cured. The advantage to integral coloring is that because the color runs throughout, surface wear won’t be as evident. Also, most integral coloring pigments are resistant to damage from exposure to weather and UV light.
Some ready-mix plants have dispensing systems for integral coloring; others often add a customer-supplied colorant to the batch as it is being mixed at the plant. Avoid adding color to the mix when the truck arrives. There’s a good chance of uneven distribution, and this will be evident only after the concrete is placed. Also, the extra on-site mixing needed to distribute the color may accelerate the setting of the concrete, which will reduce your work time once the concrete is poured. Finally, avoid adding water to a colored batch of concrete partway through the pour, because this can alter the shade of the remaining mix.
Aggregate is the filler
Aggregate, which makes up 60% to 80% of concrete, adds strength while reducing cost. Most ready-mix plants offer stone from around 3 ⁄ 8 in. to 1-1 ⁄ 2 in. in diameter. The smaller the aggregate, the more cement is needed to coat the total surface area (smaller stones add up to more surface area), and the greater the chance that the cured concrete will crack. That’s because it’s the cement in the concrete that cracks, not the stones.
The stone size is sometimes driven by the type of project. In general, the size of the aggregate shouldn’t exceed one-fourth the thickness of flatwork or one-fifth the thickness of walls. For example, 1-1 ⁄ 2-in. stone is too big to use in a 4-in.-thick slab such as a garage floor. For this application, 3 ⁄ 4-in. stone is fine, but I usually call for 3 ⁄ 8-in. stone for slabs because the smaller stones are easier to move and require less work to float. The workability of the concrete is the other driving factor in aggregate size. Smaller stone makes the concrete easier to work with and finish, which is especially important to consider for areas like basements or garage floors, which have a large surface area.
When specifying larger sizes of aggregate, request that a gradient mix of smaller stones be added to the batch. This helps to fill in the gaps between larger stones rather than relying on sand, which is typically added to every mix regardless of stone size. Remember, the more sand and cement used in a mix, the higher the risk of cracking.
Estimate accurately so that you don’t get caught short
Concrete volume is measured and ordered in cubic yards. A simple example is a 10-ft. by 10-ft. patio formed for a 4-in.-thick slab:
10 ft. x 10 ft. = 100 sq. ft.
100 sq. ft. x 4 in. (or 0.333 ft.) = 33.33 cu. ft.
33.33 cu. ft. ÷ 27 cu. ft. (1 cu. yd.) = 1.23 yards
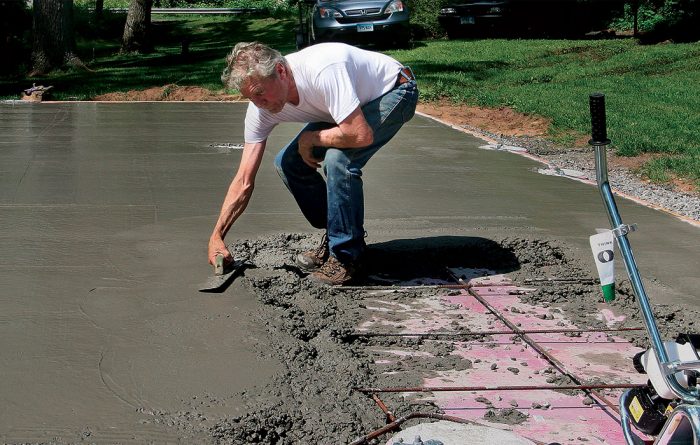
One sure way to create havoc and possibly ruin a job is to come up short on concrete. There are lots of ways to lose concrete: Forms can spread, holes can be overexcavated, chutes can overflow, concrete can be spilled, or there can be a change in volume from loss of air entrainment or settling in a wet mixture. Unless your job site is next to the ready-mix plant, chances are that the short load of concrete you just poured will have set up by the time the makeup load arrives. It’s nearly impossible to meld the new concrete into the old without a structural or visual flaw.
I usually order at least a half-yard more than I need, but if I’m using an overhead boom pump, I order a full yard extra.
When scheduling, try to give the plant as much warning as possible, particularly if you want to pour first thing in the morning. Four or five days’ notice is usually sufficient, and a follow-up call the day before is always a good idea. For a large pour involving more than one truck, make sure to discuss the timing of the deliveries. For easy-access foundations and slabs, close intervals are preferred, but for difficult jobs or when using a pump, plan on spacing out the deliveries. Otherwise, unless you’ve included a retarder in the mix, the concrete in the waiting trucks will set quickly after placement. Read more about getting caught short in the “Patrick’s Barn” blog posts at FineHomebuilding.com.
Water activates the curing process
The amount of water used in a batch of concrete depends on several things: the required strength of the concrete, the ratio of aggregate to cement, and the desired slump of the batch. The slump is a measure of the consistency of concrete; the lower the number, the stiffer the mix. In addition to specifying the strength of the concrete, you also must specify the slump at which you want that strength.
For pouring footings or foundation walls, a slump of 5 or 6 is typical. If access on the site is limited and I know that I’ll be manually pushing the concrete through the forms rather than being able to drive the discharge chutes where needed, I figure on a looser slump of about 6 or 7. If I want a slump higher than 7, I don’t want to get it by increasing the amount of water in the mix because that also means reducing the amount of aggregate and increasing the amount of cement to maintain the desired strength. For footings or foundations that require a slump higher than 7, I ask for a water-reducing admixture, which lets me get a higher slump without adding more water. For slab work, I order up to about a 5 slump with water; for anything beyond that, I ask for an admixture. If a job has strict specifications about required strength and slump, be careful about using water to adjust slump.
The concrete truck carries water on board; that water can be added to the mix at the job site to increase the slump and to make the concrete easier to pour. Be careful about adding too much water at the job site, though, because that will change the design of the mix. In general, adding 1 gallon of water to 1 yard of mixed concrete can reduce the strength by about 200 psi. It also will increase shrinking potential—and therefore cracking potential—and decrease freeze-thaw resistance. At a certain point, the mix can become so loose that the large aggregate will separate from the rest of the mix, producing an inferior final product.
During cold-weather conditions (40°F and below), the plant uses hot water to warm up the ingredients so that hydration (curing) will occur in a timely manner. Be aware that hot water accelerates the setting of concrete. Once winter weather starts in cold climates, most ready-mix plants continue to use hot water even though there may be unseasonably warm days at the beginning and at the end of the season. Accelerated curing times can be countered if you use the proper admixture in your concrete.
Conversely, if the temperature is unseasonably cold and the ready-mix plant hasn’t switched over to mixing loads with hot water, the curing time of the concrete may be painfully slow. While it’s nice to have a little extra time, waiting around with a crew for an extra three or four hours can get expensive. In both cases, an admixture can be used either to accelerate or to slow down the curing time.
When is it worth mixing your own?All the concrete plants that I’ve dealt with have a minimum order, which ranges from 1 yard to 5 yards depending on the plant. ![]() For jobs requiring less than a yard, I often buy ready-mix bags (80 bags per yard) and mix my own batches in a portable job-site mixer or a wheelbarrow. If I need 1 to 3 yards, I rely on companies that specialize in the delivery of small loads; they mix the on-board ingredients on site. Because their trucks are smaller, they are handy at getting into areas too small for regular concrete trucks. For any job requiring more than 3 yards, I call the ready-mix plant. Most concrete trucks can hold 10 to 12 yards. ![]() Some ready-mix plants have additional costs that should be considered before setting the budget for a job. Extra fees are often charged for exceeding the time allotted for emptying a truck (be ready when the truck pulls up) and for using concrete from the same truck for multiple small jobs on different sites. Always check with the individual ready-mix plant to find out its specific charge schedule. Use the concrete calculator at FineHomebuilding.com to help you decide whether to mix it yourself. |
—Rick Arnold is a builder from North Kingstown, R.I., and the author of Working With Concrete (The Taunton Press, 2003).
Photos by Rodney Diaz, except where noted.
From Fine Homebuilding #228