My college degree is in Industrial Management, and a good portion of my studies were about Japanese Management Techniques. In the 1960’s Toyota had a very astute Industrial Engineer named Shigeo Shingo (he was a W Edwards Deming student) who is credited with the technique of Poka-Yoke. Poka-yokes ensure that proper conditions exist before actually executing a process step, preventing defects from occurring in the first place.
Here’s how Poka-Yoke works on my job sites:
- Don’t bid your key trades. The carpenter should know when there is a defect in the plumbing, the plumber should know when he’s interferring with HVAC, and the Electrician should know where/when he can drill through some studs, etc. You need the same trades on all your job sites to look out for one another, and for your clients! The low bidder just isn’t interested in finding a problem. He needs to get done and get to the next job. Your workforce needs to watch for problems and if you don’t know who is on your job then you are in for problems.
- Train, Train, Train. My Project Managers are constantly training our sub-contractors on how we want things done. The Risinger Way. We use my YouTube videos, Manufacturer’s manuals, and we review at the end of each job how we could have built it better.
- Don’t be afraid to stop work! Here’s where Poka-Yoke really comes into play….
I was walking a house in the framing stage Friday. The trades had started work, HVAC was 3/4 finished with duct work, plumbers just started, so had electricians. Our framing crew also does the exterior woodwork, siding, window install, and rigid foam. The framer stopped me and said: “I can’t install siding here.” Here is what he was pointing towards on this gable where siding was being installed. There is a 6″ bath exhaust fan penetration. You’re seeing the Hardie installed over Rain Screen, which is on top of 3/4″ R-Max foam, over Tyvek Drainwrap.
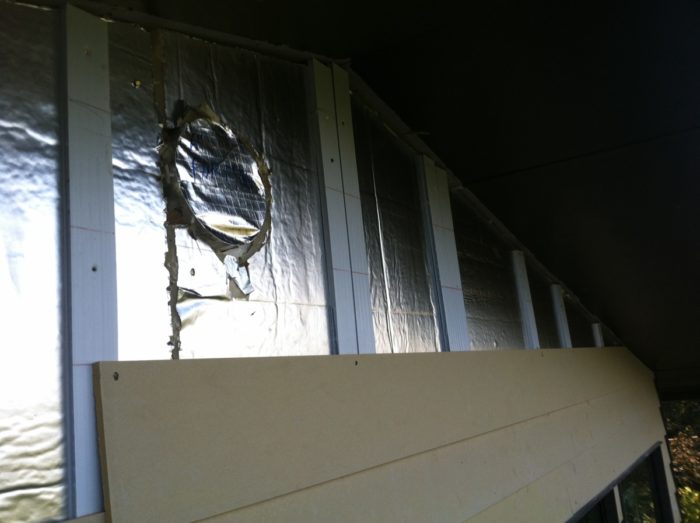
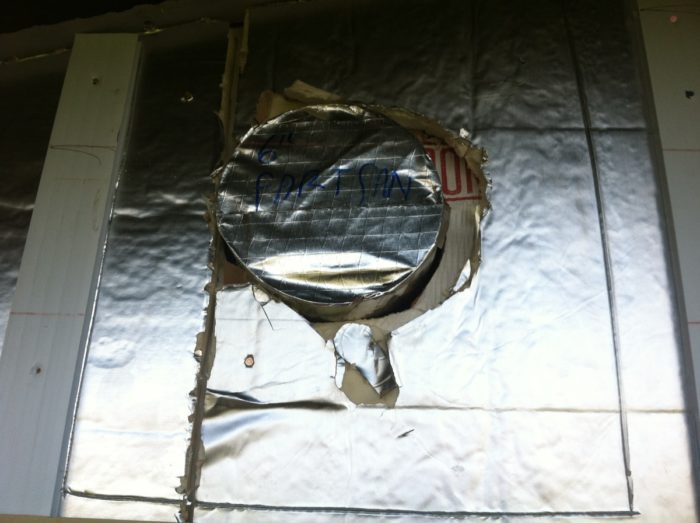
That’s not good! Unflashed penetration. It could be caulked on the inside to prevent air flow, but that wouldn’t stop water from working in to the wall cavity and rotting the house out. This type of error happens daily on job sites around Austin but clients won’t know there is a problem till 5-10-15 years later when it’s a major issue to fix. My guy was correct in saying STOP.
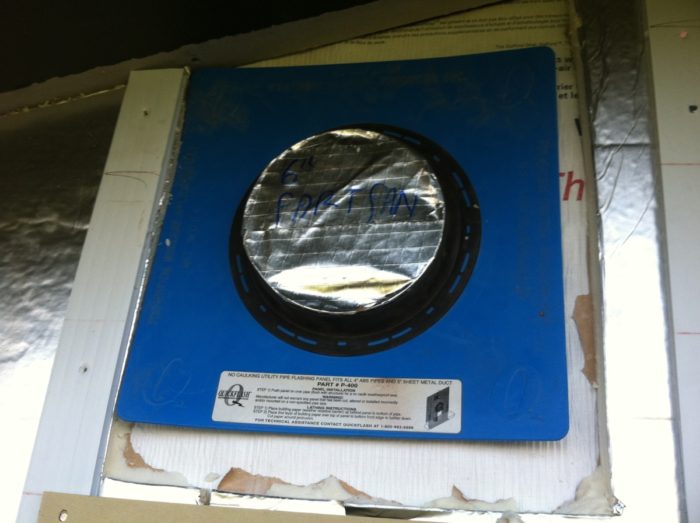
These penetrations need a gasket boot from QuickFlash that seals the duct much like a roof penetration.
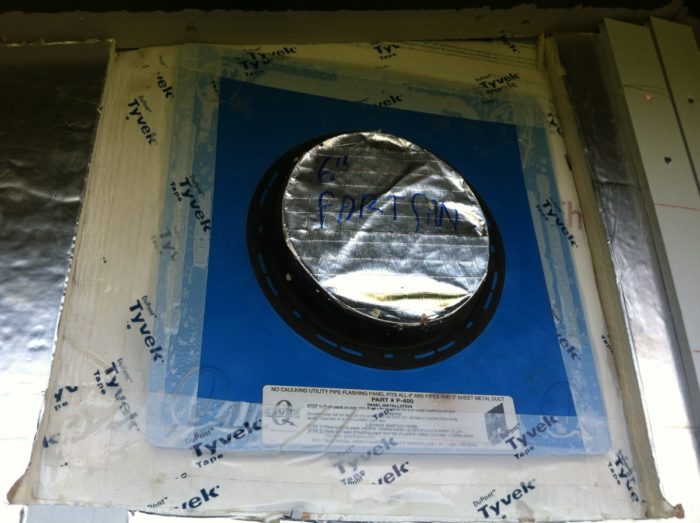
That boot is then properly taped to the Tyvek layer with Tyvek tape for a water & air tight seal. This method isn’t dependent on caulking the siding to prevent water infiltration.

All done. Much better!
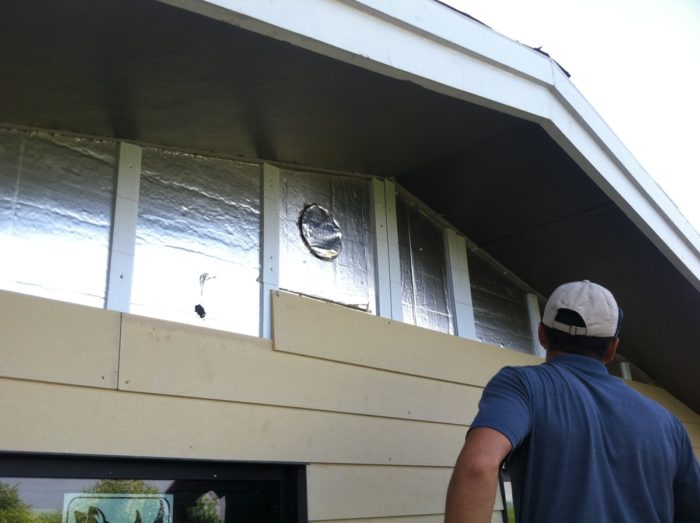
This penetration is under the roof overhang, but a windy rainstorm could have easy wet the wall in this location and caused moisture intrusion.
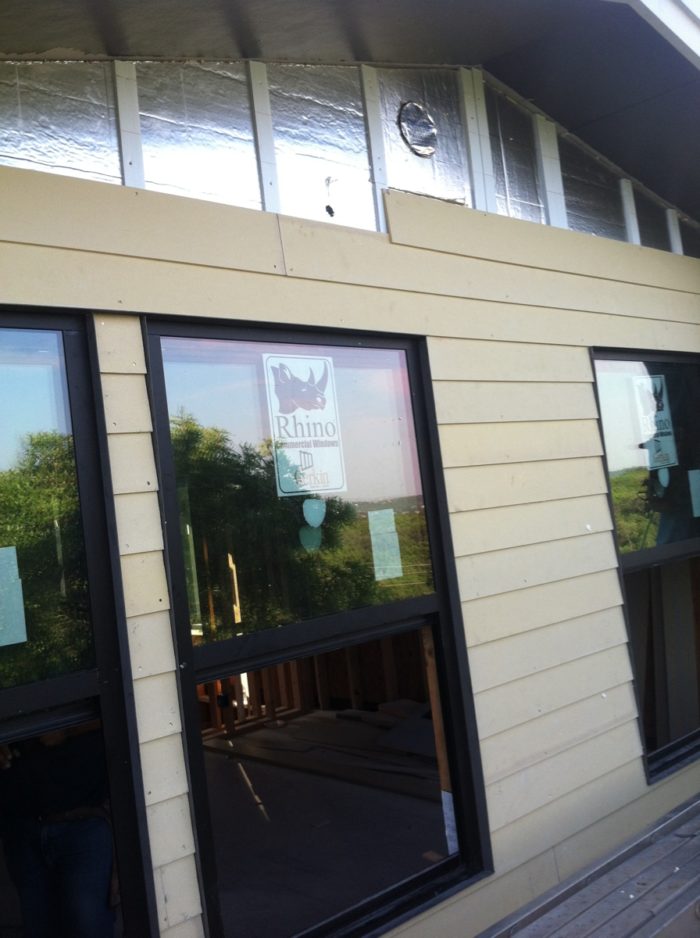
Hard to see in this photo, but the windows are “trim less”. We used a metal flashing all around the windows to give the window flange the depth we needed for the foam and the rainscreen battens then Hardie Plank siding.
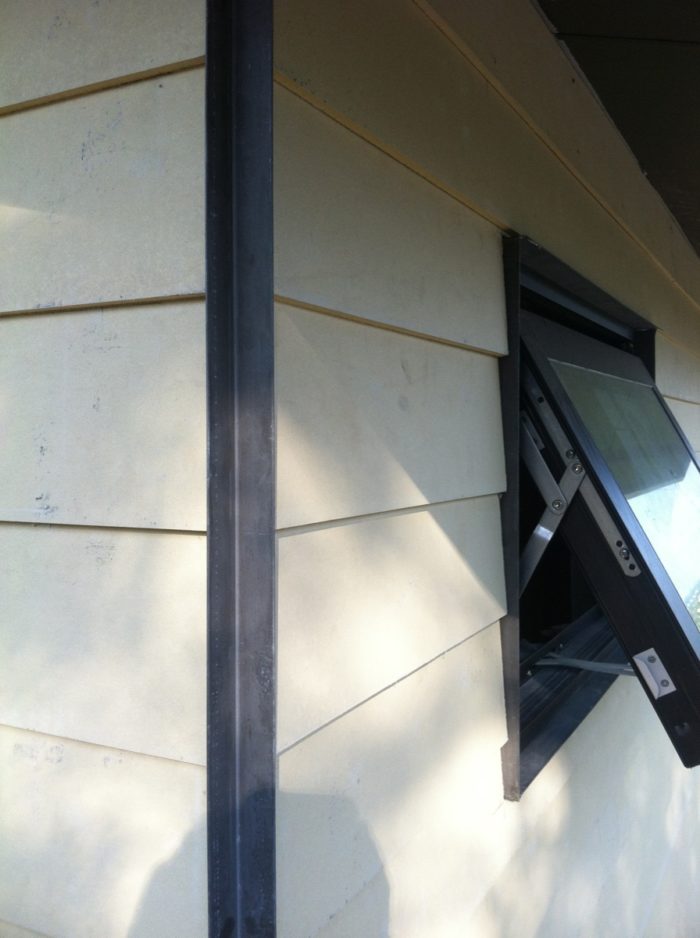
Side note here, but I really like the outside corner detail specified by Scott Ginder the Architect with Dick Clark Architects.
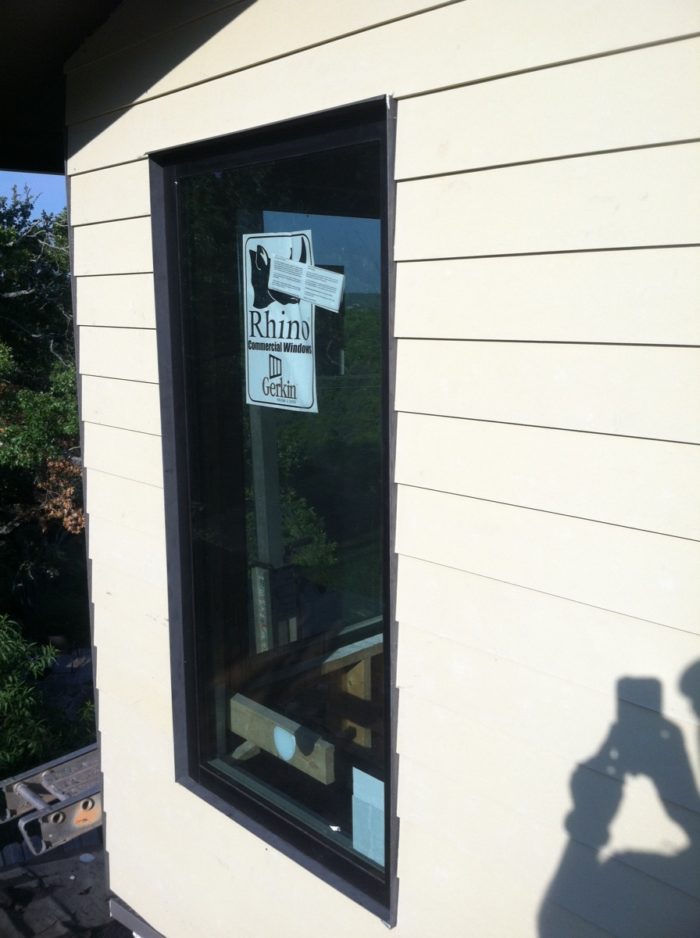
I’ve always been a fan of Toyota vehicles, they learned all these management techniques post WWII from the Americans. It’s fun to apply these principles to my houses in the pursuit of excellence.
– Matt Risinger Principle at Risinger Homes in Austin, TX
A general contractor specializing in High Performance Custom Homes & Remodels with Architects.
Fine Homebuilding Recommended Products
Fine Homebuilding receives a commission for items purchased through links on this site, including Amazon Associates and other affiliate advertising programs.
Graphic Guide to Frame Construction
Homebody: A Guide to Creating Spaces You Never Want to Leave
Code Check 10th Edition: An Illustrated Guide to Building a Safe House
View Comments
Nice approach and a welcome change from what a cabinetmaker friend of mine calls, "screw your buddy". When even subs that have worked together for years look out only for their own interests.
This would have been a lifesaver on our current project. We've been called in to paint/stain the exterior of a major remodel, long after all of the other trades are gone. Lots of details like the one in the article were overlooked. We're looking at the spaces between sidewall shingles and seeing Tyvek, bare nailing flanges on window, and the upper edges of drip edges, all exposed to the weather. Like the vent penetration in the article, these may take a few years to cause problems, but when they do, the problems will be major.
Would agree with Gough completely. Its a shame more jobs are not 'correctly done' the first time around. Shoddy workmanship creates problems not just for the sub who may come after you, but for the homeowner as well. Thanks for the interesting post!
@Gough & 7thLakeCarpentry: I think a lot of these issues start with the Builders that are bidding multiple subs looking for the lowest price. You get what you pay for, and finding the cheapest trade to work on your job will result in some sacrifice somewhere. Hunger wins over Integrity every time. If there is little or no profit on the job then you have little incentive to waive the "stop" flag. -Matt Risinger
What is that product you are using for furring ??
@rw7810: Those are corrugated plastic furring strips, similar to the ones made by CorAVent. There's a plastic supplier in Austin that sells 4x8 sheets of the material and we rip it to the sizes we need. It ends up being a nice savings over a commercial product. On the starter course we wrap an aluminum bug screen over the bottom. Works great, no rot, great ventilation, and we can custom size based on the material getting attached. Matt Risinger