How to Fix a Sagging Beam
Pboneox1 has been assured by an engineer that a built-up beam made from 2x12s is strong enough for the job, but he’s noticed the beam has deflected over its 16-ft. span by 3/4 in. The beam is over what will become a kitchen, and it will support the joists of the floor above.
“I am trying to figure out what I should do,” pboneox1 writes in Fine Homebuiding’s Breaktime forum. “I guess it is possible that it was just crowned improperly and it will not have any problems going forward, but I am not sure I am OK with just leaving it since I am installing a kitchen underneath it.”
The beam, made by nailing four 2x12s together, runs from an exterior wall to a block wall inside the house, pboneox1 says. Any ideas on how to straighten it out?
Is the beam really beefy enough?
The engineer’s cacluations notwithstanding, BossHog doubts the beam is deep enough for a 16-ft. span.
“The general rule of thumb for a beam is one inch of depth for each foot of span,” he writes. “So your 2×12 beam is pretty thin to start with.”
BossHog also wonders about some of the assumptions that went into the calculations.
“You say he [calculated] the beam and it had 3/4-in. deflection in it,” he writes. “Is that live load deflection, or total load deflection? Big difference. Also, what loading did he use? Some only use a 30-lb. live load for 2nd floor sleeping rooms in order to skimp by.”
DoRight points out that beam depth is more important than beam width.
“The resistance to bending goes up by the SQUARE of the depth,” he says. “A 2×12 has about twice the bending resistance as a 2×10. So going from three 2x12s to four does not do as much for you as one might think…
“That said, I am amazed how strong wood is. I know of a 16-ft. garage door header made of two 2x12s and 1/2 [-in.] plywood, which supports the ends of 26-ft. spanning trusses. This is in heavy snow load country as well. It does have a sag in it (not measured it) probably 1/2 to 1 in. Pretty amazing. Four 2x12s would be nearly 72% stronger in resistance to bending. I suppose one difference is the floor beam is largely dead load and the garage header has to handle a fair dead load and a significant (temporary) live load.”
A jack might remove the sag, but be careful
One possible solution, Pboneox1 writes, would be jack up the beam to eliminate the deflection, reinforce it with a 1/4-in. by 11-in. steel plate on each side, and bolt the assembly together. “It would be like a giant double flitch plate beam,” he says. “Any thoughts on this plan?”
“On a side note I was thinking of framing the beam in old barn wood so it looked like a actual exposed beam once I figured this out and that would be easier to do if it were straight,” he adds.
Run your plan by the engineer, Florida suggests, adding, “If not and it were my home I’d pull it out and install a steel beam.”
And, says Calvin, jacking the beam straight may not be as simple as it sounds.
“First, you need a secure, firm, well supported place to put the jack,” Calvin writes. “It is always possible to jack down the area below what you want to jack up. And, slow and easy with monitoring all the points of connection up, down and around is something you should be aware of.
“I’ve seen cases where the deflection was a poorly crowned joist or beam and jacking the middle to remove the dip, ended up lifting both ends. Work your way up from below what you intend to lift and take all precautions necessary to do as little damage correcting the problem.”
Oldhand, who thinks the best plan may be to leave the beam as is, wonders whether a well-seasoned beam of that size would be flexible enough to be straightened out by jacking.
“My guess would be that would actually weaken the beam itself,” he says.
Add shims to take out the sag
If the beam is indeed strong enough, some sagging should be expected over a span of 16 ft., DanH writes.
“When I replaced the sagging double 2×14 beam over my garage door with doubled 13-in. microlams I first let the load down on the beam, measured deflection, then raised the load again and inserted shims to compensate,” DanH writes. “I believe it was about 1/2 in. in 16 feet, with just a roof load overhead.
“(As a result, I have the only garage in the neighborhood where the garage door opening isn’t visibly sagging.)”
Then again, just about everything sags a little over time, including us.
“I’ve been trying to stop the sag for about 20 years now,” DanH adds. “It ain’t working.”
Fine Homebuilding Recommended Products
Fine Homebuilding receives a commission for items purchased through links on this site, including Amazon Associates and other affiliate advertising programs.
Handy Heat Gun
8067 All-Weather Flashing Tape
Reliable Crimp Connectors
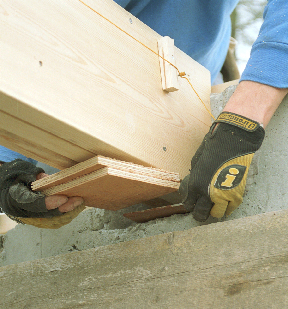
View Comments
A better way is to take it down, take it to pieces and glue and bolt the pieces together.
In most situations a 16' beam supporting a floor would be calculated to have deflections of no more than 0.5" due to live load, and 0.8" due to live + dead load. Therefore, under dead load only, about 0.3" of deflection could be expected.
If the engineer fully understands the situation and you are still not comfortable ask him to provide a detail using structural steel. Depending on your situation he may find that replacing the outer 2x12s with structural steel channels is a good solution. I see a couple of advantages to using a channel vs the flitch plates suggested. 1) Channels are much more efficient and therefore lighter/stronger than flitch plates. 2) The channels can be thru bolted without bolts protruding past the edge of the flange. The space between the web and flange can be packed out with wood to allow for attachment of finishes, etc.
Aslem provides the best advice. I'm stunned that any structural engineer would spec out a quad of 2x12s! Design is based on a number of factors, not just load. Deflection is always a part of the solution, especially in a deflection sensitive application.
Rule #1, design it right in the first place by a qualified engineer. If you can't afford one, use the tech service from a manufactured beam supplier. I see this short sighted practice all the time of going in cheap and then applying an expensive retrofit.
Sliderule
There really isn't enough information to offer specific advice...
1...The area of the floor above and any partition loads and any loads bearing on those partitions such as attic loads. ?
2-...Rules of thumb about depth to span are not very helpful..
3... what specie and grade of wood are the 2x12's ?
4...note...a 2x12 does not have about twice the resistance to bending as a 2x10.
In fact just about 50% more... S for 2x10 = 21.39 ; for 2x12 = 31.64
5...It sounds as though the floor above has not yet been framed...Do the calculations again...
6... Engineered lumber with greater capacities for bending and deflection would seem appropriate in this condition..
7... Is the span really 16' or is that a nominal dimension.?..Deflection is a function of the cube of the length..
Is there a reason the framer decided to nail 2x's together rather than just install an appropriate sized beam out of solid stock? It wasn't mentioned as I could see, if the boards were also glued when nailed together, shear factor goes straight to the nailing pattern. Poor idea at best.
I ran into a similar problem where I had 3 2x12s spanning 19'6". It was designed to carry the load from the roof ridge and the previous owner added storage using the built up beam to tie one end of the storage joists to.
The beam had deflected about 1.125". I solved the issue by having a 1/4" x 10" x "the free span length" plate with a full seam welded 1/4" x 3" bearing plate to create an "L" beam.
I jacked up the beam so it had about a 1/2" crown and bolted the plate to the built up beam. I have not noticed any deflection in over 13 years since I made the modification.
Unless I'm missing something here, what Pboneox1 is saying is that the beam has deflected 3/4" BEFORE he's even loaded it. Assuming "standard" lumber properties, deflection for total load is usually taken as L/240, for live load only L/360. The deflection being reported is for NO LOAD. If that's the case, he's got a useless, misshaped beam in place.
If the beam in question is going to be supporting a kitchen floor, it's always prudent to use heavier floor loading assumptions to account for the cabinetry, appliances and countertops. And here's where the engineer really needs to be well informed of the details of construction. I can guarantee that concrete countertops and a Viking range and a commercial refrigeration unit would add enough dead load beyond the standard to cause even more deflection than expected.
When Pboneox1 adds the floor joists, deck, flooring, cabinets, appliances, and countertops, that floor beam is going is to deflect even more than the 3/4" he's already got -- and "level" will be a long lost concept in the new house.
I have almost the same problem. The contractor put in a glue lam and the thing is cracking and bending all over the beam. I am thinking of strengthening the beam by putting some 1/2 inch bolts through it. I guess it could be pulled out and a steel beam put in but I think that it would be terribly expensive. I know I had a lousy contractor. I fired him, but too late.
Regarding deflections....Combined dead and live loads for floors should not exceed L/360 where L is in inches.. L/240 is suitable for rafters. The L/360 derives from a time when ceilings were plastered...That limit on deflection was deemed to be small and stiff enough for plaster to not crack... L/240 for combined dead and live loads is apt to result in a springy floor.
In a kitchen it is wise to design for a floor stiffer that L/360... and take into account concentrated loads from equipment and islands.
I agree with Perry525!
http://www.remodelinghellthebook.com/