Make Your Own Lightweight Concrete Vanity Top
A glass-fiber-reinforced concrete mix creates an elegant, lightweight counter and sink.
In recent years, concrete has become a popular material for countertops and sinks. Despite its popularity, the fact remains that concrete is heavy. Taking a cue from the world of commercial concrete, craftsman Buddy Rhodes started making a lighter concrete countertop by reinforcing the concrete with glass fibers. In this “Master Carpenter” article, he explains how he does it. First, he molds the sink. The mold, made of plywood tightly wrapped with polyester cloth and coated with fiberglass and polyester resins, represents the inside, rather than the outside, of the sink. After he makes the sink mold, Rhodes makes the counter form, making sure to leave spaces for the faucet and drain, and attaches the sink mold. He uses lots of wax to ensure that the mold releases from the finished sink. Rhodes sprays on the counter’s finished surface with a large spray gun, also known as a popcorn gun. Then, he mixes concrete, fiber, and mesh, and loads it onto the sink mold. After curing overnight, the sink and counter are ready to be popped out of the mold. This article includes sidebars on forming an overflow drain, coaxing a stubborn sink out of a mold, and making a special beading tool.
Concrete countertops have become popular over the past 20 years, and with good reason. Of course, they look great. Because they’re cast, they can be made in almost any shape or style, and unlike other counter materials, they’re practically bombproof. Best of all, almost anyone can make one with a few basic tools, which brings the price below that of most other materials.
I began working with concrete about 30 years ago. I made countertops, benches, big planters, and decorative tiles. Most of these were made either with a traditional aggregate mix or a dry-pack technique I devised that yields a variegated look (see “Casting a Concrete Fireplace Surround,” FHB #174). Made in molds, the objects were finished by hand-troweling or by rubbing with successively finer abrasive pads.
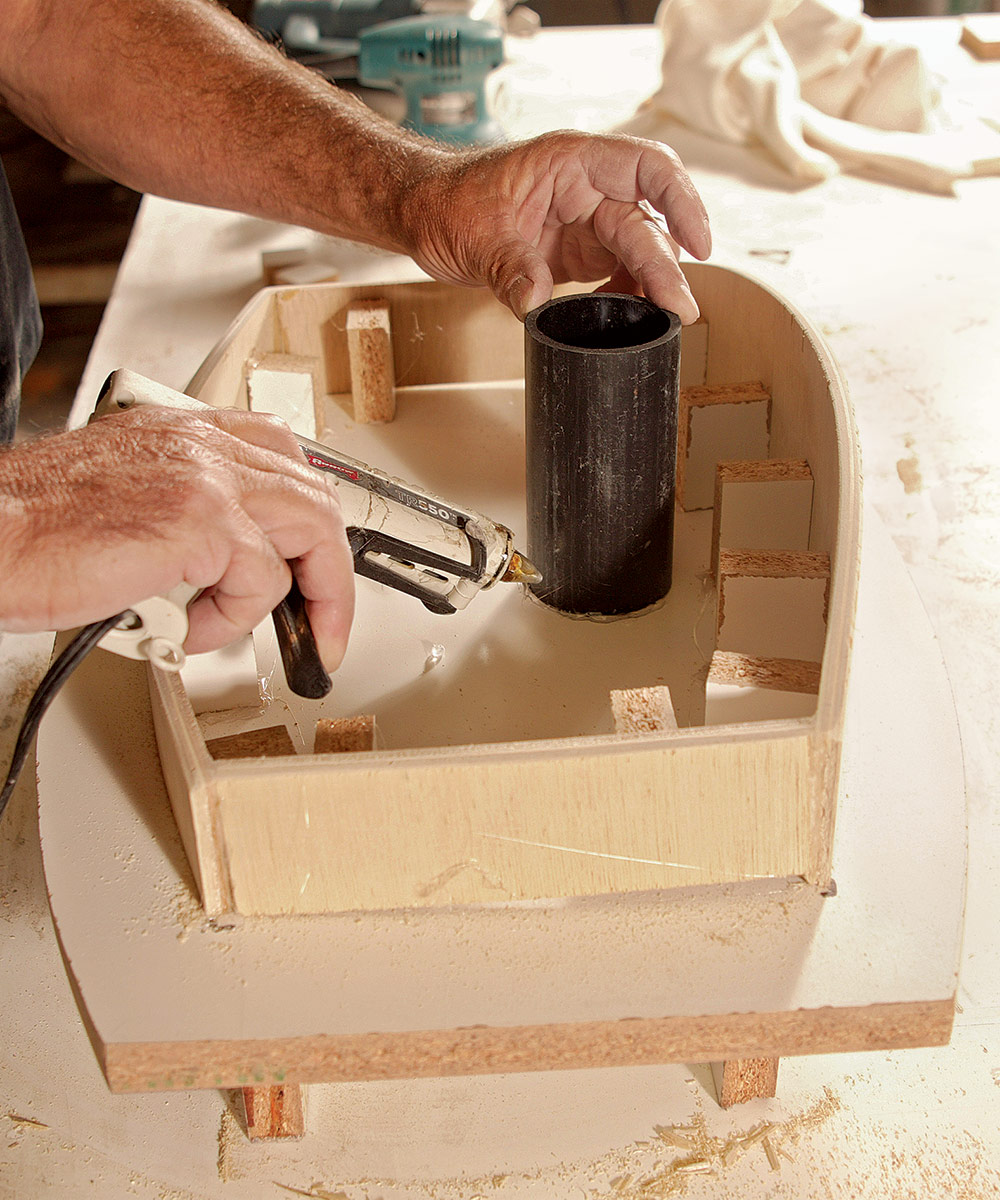
A few years ago, I started fooling with a technique borrowed from the world of commercial concrete. For some time now, fabricators have made exterior panels for high-rise buildings with a mix that yields a strong, lightweight concrete. Their secret is to substitute fiberglass fibers and mesh for the traditional steel reinforcement. Because there’s no need to bed the steel reinforcement in inches of concrete, the concrete can be made as thin as 1 1/4 in. Perhaps best of all, the finished surface is sprayed into the form before the rest of the concrete is added, which cancels the need for almost all the surface polishing and work at the end of the project. Here, I’ll show how I made a vanity counter and integral sink bound for Fine Homebuilding’s Project House. The first step in the process is to make the mold for the sink from fiberglass-resin-impregnated cloth and plywood, then attach it to the countertop form. Once it’s complete, I use a drywall-texture spray gun to coat the form with a thin layer of tinted concrete, then mix a thicker batch with fiberglass fibers and hand-pack it to the final thickness. When the concrete has cured, the counter is nearly complete and needs only a light buffing and a couple of coats of sealer before being installed.
Start with the sink mold
The first step in making the mold is to determine the shape of the sink. You can make a sink in almost any shape or depth, as long as it directs water to the drain. The depth of the bowl is established by plywood ribs glued to a base that represents the sink rim. This frame then is covered with resin-impregnated cloth that hardens into a negative of the sink bowl. The trick here is to use different forms of polyester—polyester fleece cloth, two-part fiberglass resin, and auto-body filler—that bond together perfectly.
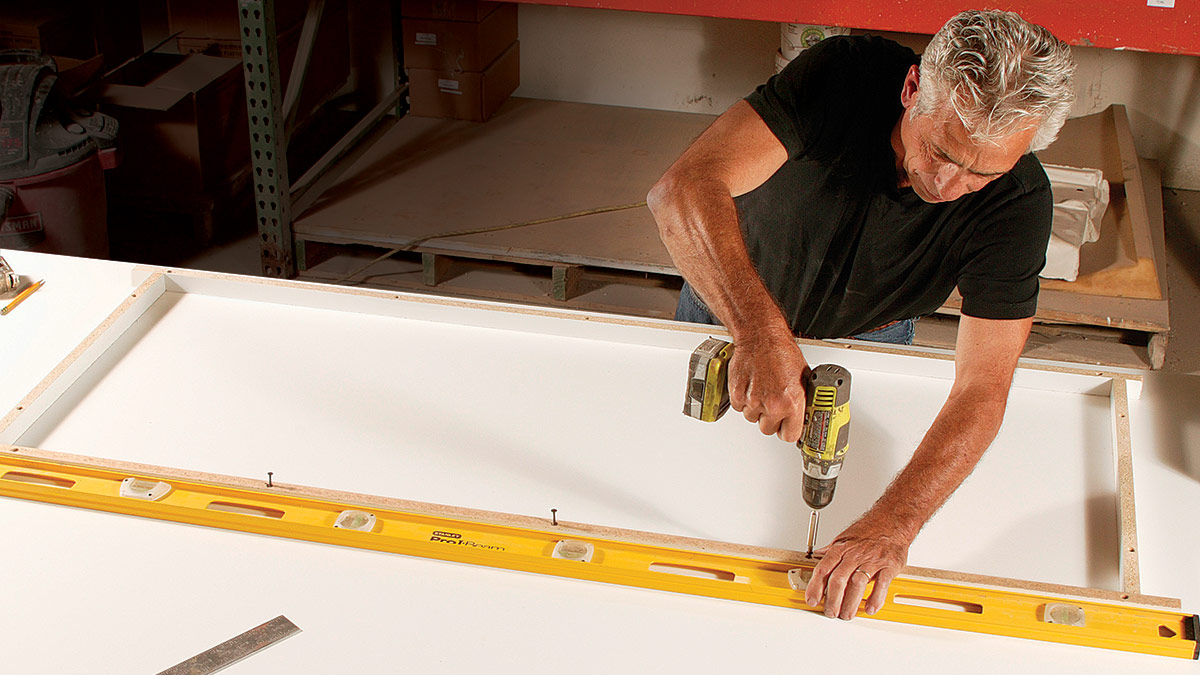
Also watch the companion video series:
View Comments
What are some advantages to using concrete over more conventional materials?