Efflorescence and Spalling in Concrete
Understand the causes and methods for prevention of this destructive force commonly seen in concrete and masonry structures.
Concrete work and masonry work can be stressful. From forming small decorative concrete projects to pouring tall concrete walls, when things go wrong, at best it’s a scramble to keep the project moving forward. Concrete can be repaired, but we all would prefer to get it right the first time.
Even when you get the forms set up well, it can be tricky to make sure that you are using the right concrete for the job. And there is even a problem that can occur long after the concrete has cured. Efflorescence and spalling may not trump immediate concerns over the weather, of having the right mix, or of running out of material before the job is done, but they can turn a promising project into a headache.
Efflorescence, the white, chalky residue that sometimes appears on the surface of a concrete or masonry project, can simply be a frustrating cosmetic issue, or it can be an indication of moisture problems that might eventually lead to serious structural issues as a result of spalling. Before you can adequately address either, you first need to understand how they work.
The Process
Concrete, brick, stone, and mortar all contain mineral salts, as do the soils they routinely come in contact with. All of these porous building materials also absorb water. The ability for concrete to absorb water through capillary action is remarkable. According to Building Science Corporation, the theoretical limit of capillary rise in wood is roughly 400 ft. In concrete, however, the capillary rise can approach 6 miles.
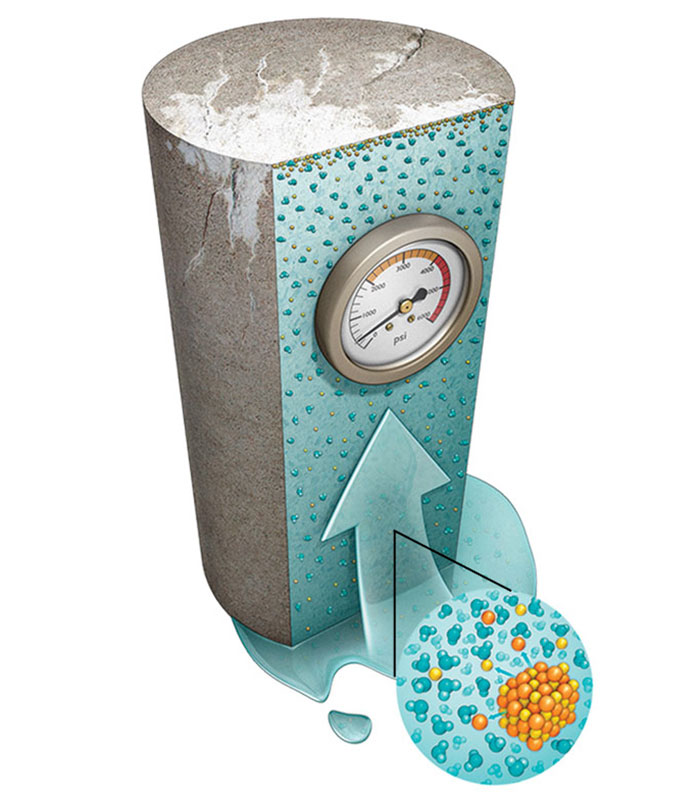
As water moves through the porous structure of these materials due to capillary action, it draws salt with it. This capillary pressure is relatively low—between 300 psi and 500 psi. The water makes its way to the surface of the material, evaporates, and leaves the white, powdery salt behind. The moisture that fuels this process most often comes from groundwater, but in some cases, it is caused by snow and rain. Efflorescence alone does not pose a problem, other than an unpleasant appearance in areas of high visibility.
The Concern
As more salt accumulates on or just beneath the surface, more water migrates through the material to dilute the salt in a process known as osmosis. This process can create incredibly strong hydrostatic pressure within the building material—anywhere from 3000 psi to 5000 psi. Concrete typically has a structural strength of 2000 psi to 3000 psi. Hydrostatic pressure that exceeds the strength of the building material can blow the surface off the material. This flaking is known as spalling, and if it is not addressed, it can eventually compromise the structural integrity of the project. While spalling can occur on concrete, it’s especially a concern on stone, brick, or block, where portions of the assembly can degrade to a point where they crumble. Hydrostatic pressure is not the only cause of spalling. Spalling also can be caused by freeze-thaw cycles in concrete and masonry products that have a high moisture content.
How to Prevent It
Efflorescence and spalling can be prevented in concrete by stopping moisture migration. This can be accomplished with a capillary break, such as subslab polyethylene sheeting or liquidapplied elastomeric waterproofing. Although the same is true for masonry work, efflorescence is sometimes tolerated, and spalling is often anticipated by using sacrificial mortar. The mortar used in these assemblies is intentionally softer than the masonry, and it degrades first. The mortar joints, or in some cases the mortar parge coating, are simply repointed or reapplied every 20 years or so.
—Rob Yagid, design editor.
Drawings: Christopher Mills.
From Fine Homebuilding #234
View Comments
I HAD A SEVERE SPALLING PROBLEM ON A JOB I SUBCONTRACTED TO A LOCAL CONCRETE FIRM. IT OCCURRED WITHIN A YEARS TIME. I HAD TO DEAL WITH THE REPERCUSSIONS OF THE CUSTOMERS DISSATISFACTION. SINCE THAT TIME, I INSIST THAT A 6 MIL. POLY MEMBRANE BE LAID BENEATH THE WIRE MESH OF EVERY SLAB POURED. I HAVE HAD ZERO PROBLEMS SINCE THAT TIME. HOWEVER, MY NEW SUBCONTRACTOR THINKS I'M A BIT NUTS AND I ALWAYS HAVE TO INSPECT THE SITE PRIOR TO AUTHORIZING THE CONCRETE POUR. OLD HABITS DIE HARD.