A Higher Standard for Energy Efficiency
A practical design delivers a remarkably airtight, super-insulated home on a modest budget.
Synopsis: This contemporary home by Jesse Thompson and Richard Lo of Kaplan Thompson Architects achieves extraordinary energy performance through a design based on proven assembly methods and carefully executed, straightforward construction techniques. Purposefully modest, this home proves that better-performing homes are attainable through smart design and proud craftsmanship. For that, this project embodies what we consider to be the definition of quality in residential design and construction.
For a number of years, Rob and Fiona were content to live in a simple Maine cottage a stone’s throw from the water’s edge. In recent years, however, they had tried having a new house designed to accommodate their changing needs, but quickly got mired in results that were much larger and more expensive than what they wanted. After tiring of these unsuccessful ventures, they came to my firm seeking a compact, modern, extremely energy-efficient home that would blend into the tightly woven neighborhood where they planned to root themselves for the years to come.
We set to work applying our studio’s motto—beautiful, sustainable, attainable—to the project. Our early meetings quickly centered on the meaning of cottage in the 21st century. We wondered if the term still defined the classic British buildings of Rob and Fiona’s youth, which so successfully fit between clusters of lavender and privet hedges, or if cottage had come to mean something bolder and simpler with less of the romantic touchstones of 19th-century construction. We concluded that we needed to draw on each of these ideas, and that the house would need to be simple, tough, and practical, in keeping with the Maine life that Rob and Fiona love.
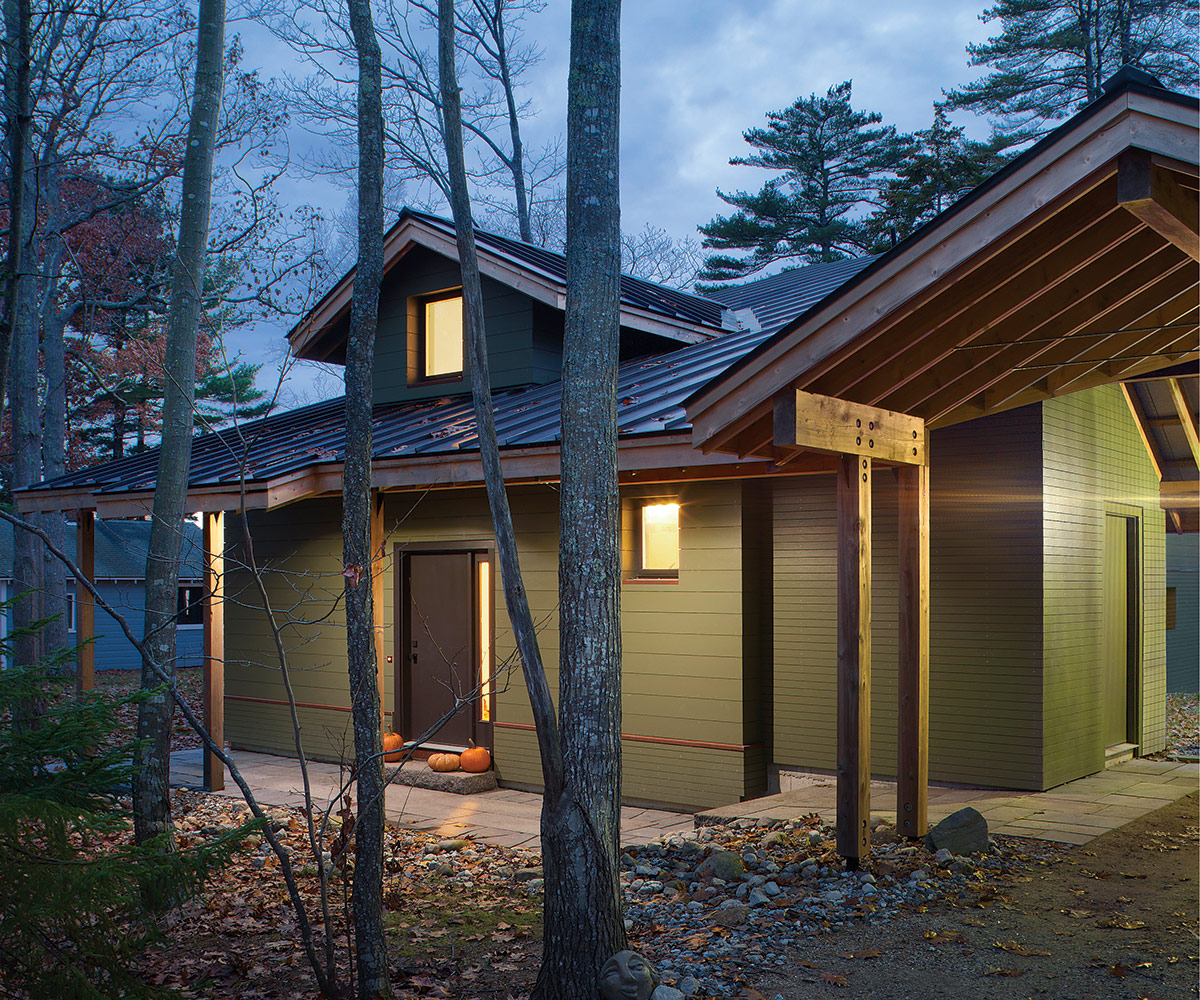
We thought that a house approximately 1800 sq. ft. in size would be able to meet their budget and allow for the quality of design and construction they desired. Early on, it became evident that their goals included very low energy use, nontoxic materials, a quiet and simple aesthetic, bedrooms that faced the water, a flexible office space, and LEED certification.
Ultimately, we designed a house that met all those wishes. The house feels spacious and comfortable, it’s certified LEED Platinum, it beats the Passive House air-tightness standard by 30%, and it meets the Architecture 2030 Challenge of reducing fossil-fuel use by 70% when measured against average homes in the region. While we were able to accomplish all of this for only $175 per sq. ft., we had to navigate plenty of challenges along the way to make the project a reality.
The site dictates form and layout
Rob and Fiona’s site was challenging. The outstanding views on the property are to the west. However, the axis of the Flying Point Peninsula on which the house sits stretches from northeast to southwest, and solar south didn’t align with either direction.
We generated a variety of sketches to test the best house position. The most comfortable scheme locked the main axis of the house perpendicular to the road, which is typical of homes in the neighborhood, but we twisted the interior views along the diagonal and placed large corner windows in all important rooms. We also pushed the prime rooms toward the back of the house as close to the water as we could, letting the house rise up in a simple wedge shape to cover the spaces inside. This provided interior rooms with stunning ocean views and allowed us to chase as much southern exposure for the triple-glazed windows as we could, exposing the slab to as much free heat as possible.
The resulting house shape feels quiet and centered, and the approach to the structure provides a gradual introduction to the home. A modest gabled porch connects to a timberframe carport and presents a welcoming entry, not unlike the many cottages on this part of the coast.
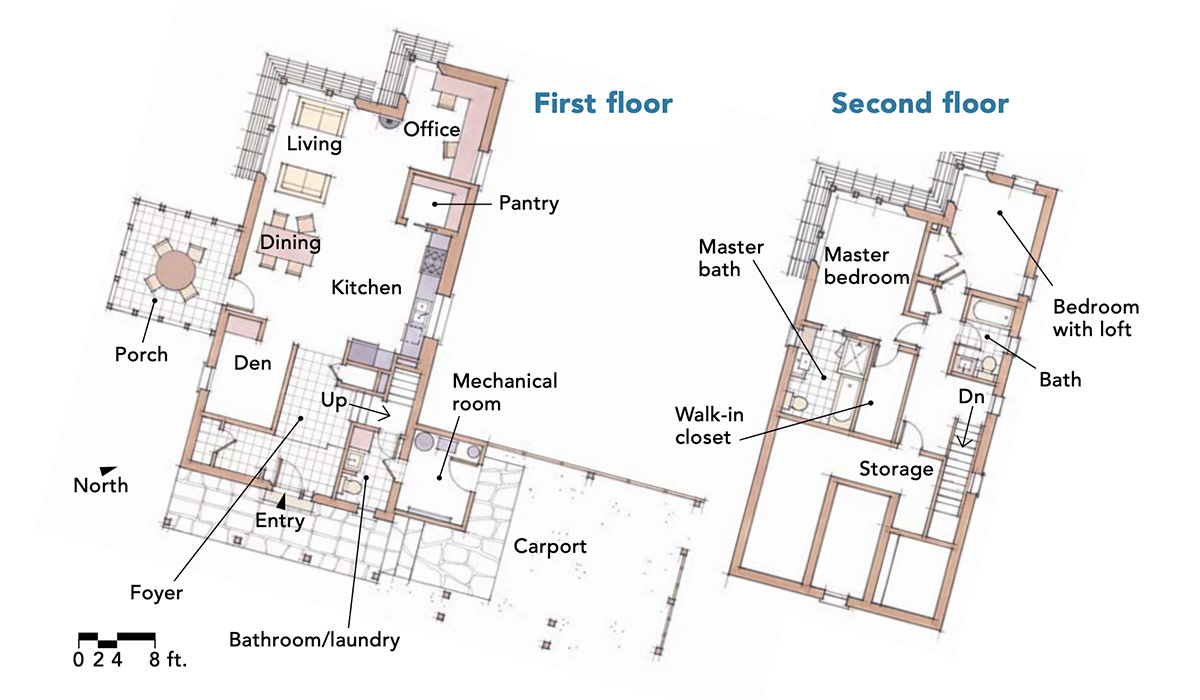
SPECS
Bedrooms: 2
Bathrooms: 2 1/2 Size: 1800 sq. ft. Cost: $175 per sq. ft. Completed: 2010 |
Location: Freeport, Maine
Architects: Jesse Thompson and Richard Lo; kaplanthompson.com Builder: Monaghan Woodworks; mwoodworks.com |
High-stakes, straightforward construction
Our design methodology revolves around marrying a smart building shell to as small and affordable a mechanical system as we can specify. This building site had several fuel options available: electricity, propane, oil, and wood. We haven’t installed an oil boiler in a house in many years because we think that it’s far too toxic and inefficient to store 275 gal. of hydrocarbons inside a modern building. Also, a masonry chimney had no place in the project for other reasons. Rob and Fiona didn’t want air-conditioning, so a major advantage of heat pumps would have been wasted on the project. Therefore, we designed the house around a simple, single-zone propane-fired in-slab radiant-heating system, with the help of a flat-plate solar system designed to produce 60% of the likely hot-water needs of the family. By keeping complicated mixing valves, pumps, and controls out of the project, we were able to free a substantial amount of money to improve the quality of the building shell without raising construction costs. This was significant because such a simple mechanical system wouldn’t work without a tough, warm building surrounding it.
We worked closely with the builder to evaluate various costs and construction methods for the walls and roof. The most economical method proved to be double 2×4 walls with an exterior air barrier, dense-packed with cellulose insulation. The roof was framed with 14-in. I-joists also dense-packed with cellulose. Our insulating target was based on a 5-20-40-60 building enclosure as laid out by Building Science Corp. for our climate zone: R-5 windows, R-20 under-slab insulation, R-40 walls, and R-60 roof.
Our approach to the house’s assembly, though not revolutionary, was proven extraordinary when the mechanical-sub bids came back. We went out for three bids. One price was more than $30,000 and added staple-up radiant tubing under the entire second floor in addition to our specified equipment. Another came back with a handwritten note declining to bid because the contractor had never seen such low heat loads and didn’t believe they were possible to achieve. The final bid came in from a contractor who trusted our heat-loss calculations and bid $15,000. The $15,000 we saved paid for all the upgrades of insulation and for the triple-glazing in the windows.
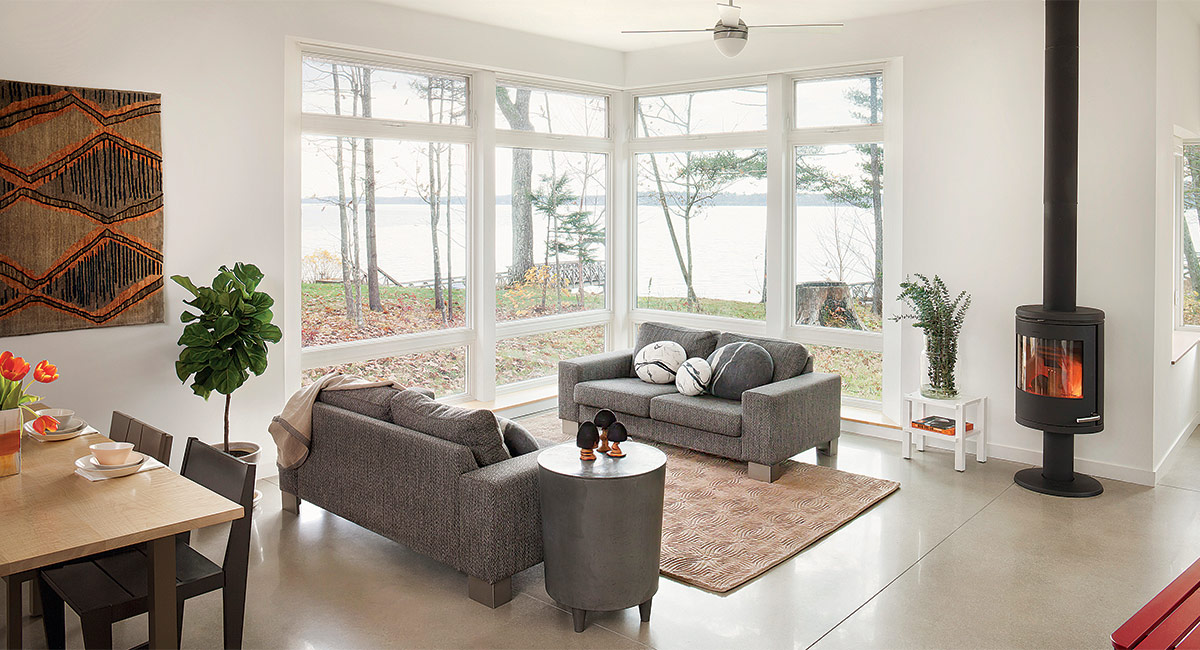
Triple-glazed windows typically eat up a significant portion of a construction budget, so we carefully consider the units we use. For this house, we chose InLine Fiberglass windows out of Toronto. These windows were well priced compared to similar products, the fiberglass exterior was ideal for a tough waterfront location, they were available with high solar-heat gain Cardinal 179 glazing, and they had great design-pressure values to prevent water infiltration and air leakage. The windows are a combination of fixed, casement, and awning units. Using large fixed lites in combination with smaller operable units is the most economical way to get large windows into a low-budget project.
None of these design efforts would have been worthwhile, however, if the house wasn’t built to be airtight. The contracting firm on the project had built many nice homes and had years of experience with coastal construction. This was their first LEED project, however, as well as their first project targeting an ambitious air-sealing specification. They teamed up with a high-quality local cellulose contractor who brought his blower door on site as soon as the ZIP System sheathing shell was in place and the windows were installed. They carefully swept over the entire building skin before any insulation showed up on the project, and took our 1.0 ACH50 specification as a challenge to be crushed. After we told them that the hardest metric to hit was the Passive House standard of 0.6 ACH50, they raised their game even further. The final blower-door number, taken when the house was complete, came back at 0.4 ACH50, with less than 150 cfm50 moving through the fan under pressure.
Giving the house lungs
The goal of the mechanical system was to keep it simple and low cost. To ensure that this was possible, we carefully integrated the HRV system into the construction system. We laid out all the interior ductwork in consultation with the ventilation contractor, checking for clashes throughout the 3D CAD model with framing members or vertical elements. We specified open-web floor joists to allow easy mechanical, plumbing, and electrical coordination in a house with no attic or basement. Adding a few dropped ceilings gave us extra room for mechanical runs in certain areas.
Efficiency complemented by coast-appropriate finishes
The Maine coast can be a brutal environment to live and work in. Just like the people who live in them, the homes here experience some of the most severe weather conditions in the country. Wind and water come from all directions, and leaky windows and walls provide regular tales of woe from local contractors and homeowners up and down the coast. Houses here need to be built with resilient materials. Rob and Fiona also wanted to use as many local, renewable, and nontoxic materials in their home’s construction as possible. Our contractor kept a close watch to ensure that highly off-gassing sealants didn’t creep onto the job site, and we worked hard to make sure that no sheet goods containing urea formaldehyde or other noxious products ended up in the building. The flooring was a simple palette of polished concrete and carbonized bamboo with water-based polyurethane, both of which are incredibly durable. We used local lumber for all the framing and the exposed exterior woodwork, primarily hemlock and white cedar.
The siding is factory-finished fiber cement, which we applied on the flat over furring strips. We used standard smooth fibercement clapboards for the upper siding section on 1×3 furring strips, and fiber-cement battens on 2×4 furring strips on the lower section for added visual depth at the base of the house. In addition, the contractor upgraded the window sill pans and horizontal flashings to copper for true 100-year durability and a more elegant look.
This house is a proud moment in the history of our firm. We worked to bring a fine grain of detailing to the durable, low-energy construction techniques we have deployed on previous projects at the same time that we managed to evoke the serene modernism that our clients love. That feels like success to us.
9 Details of a High-Performance Design

1. A heavily insulated concrete slab-on-grade foundation eliminates the need for deep excavation below the high-water line, sump pumps that can fail, expensive basement insulation, and the accompanying drywall.
2. An initial design with 12-in.-thick walls yields a well-insulated assembly. It’s always easier to thin up walls if necessary to gain space later in the planning stage than to have to go in the other direction.
3. A high-quality, well-sealed, and verified building shell is a must. Careful flashing details and rigorous air-sealing measures are verified with multiple blower-door tests throughout construction.
4. A house should breathe through a set of lungs, not by hoping that fresh air will somehow find its way inside. A high-quality ventilation system with heat recovery ensures health and efficiency.
5. An exterior air barrier comprised of ZIP System wall sheathing with taped seams is the easiest to build. A simple house form with overhangs and other details added after taping the basic box made hitting 0.4 ACH50 possible.
6. Self-adhesive flashing membranes stick poorly to ZIP sheathing. Flashing membranes should be stuck onto the ZIP tape that has been applied to the sheathing.
7. Spray foam around windows leaks. Water moves through pinhole “folds” in the foam at the rough openings. Caulking the spray foam to stop leakage around the windows is necessary.
8. Concrete slabs leak air far more than expected. Air moves through the crushed-stone layer, right through the insulation gap at the slab edge and into the conditioned space. It takes a considerable amount of tape and caulk to seal this transition.
9. You don’t need spray-foam insulation and/or airtight drywall for rigorous air-sealing. A sheathing air barrier, tape, and caulk do this well.
Jesse Thompson (kaplanthompson.com) is an architect in Portland, Maine. Photos by Trent Bell.
See more award-winning homes from HOUSES Awards.