Roman builders may have a thing or two to teach us about concrete.
Underwater samples taken from a breakwater 2000 years old show a more durable concrete and suggest lower carbon emissions in its manufacture.
The Lawrence Berkeley National Laboratory announced that researchers working in part of the Bay of Naples in Italy sampled concrete that is chemically different and more durable than its contemporary equivalent. In addition, the limestone used to make it was fired at much lower temperatures than what’s standard in today’s lime kilns.
Concrete is widely used but carries a steep carbon penalty
Concrete is the most widely used construction material in the world. The glue that holds it together is portland cement, a mixture of limestone and clay that’s baked at high temperatures in giant kilns fired by powdered coal, oil, or gas.
Modern kilns operate at temperatures of more than 2600 degrees F, but Berkeley researchers discovered that the Roman process required less lime and that it could be processed at a much lower temperature: 1652 degrees F.
“It’s not that modern concrete isn’t good–it’s so good we use 19 billion tons of it a year,” says Berkeley Lab project leader Paulo Monteiro. “The problem is that manufacturing portland cement accounts for 7% of the carbon dioxide that industry puts into the air.”
For every ton of concrete that’s produced, a ton of carbon dioxide also is produced, researcher Marios Soutsos told Chemistry World in a 2008 interview. Modern kilns are more efficient, producing about 800 kilograms of carbon dioxide per ton, but that’s still a significant amount.
Carbon emissions are not only the result of burning the fuel needed to attain high kiln temperatures, but also the breakdown of the calcium carbonate itself.
The Roman recipe
Romans mixed lime and volcanic rock to make concrete. “For underwater structures, lime and volcanic ash were mixed to form mortar, and this mortar and volcanic tuff were packed into wooden forms,” reported Berkeley Lab. “The seawater instantly triggered a hot chemical reaction. The lime was hydrated–incorporating water molecules into its structure–and reacted with the ash to cement the whole mixture together.”
The best ash for maritime concrete came from the town of Pozzuoli. Ash with similar characteristics, which is called pozzolan, is found all over the world.
In modern concrete, the cement binder is a compound of calcium, silicates, and hydrates, or C-S-H, while Roman concrete had more aluminum and less silicon, according to Berkeley Lab. The calcium-aluminum-silicate-hydrate (C-A-S-H) “is an exceptionally stable binder.”
“For us, pozzolan is important for its practical applications,” says Monteiro. “It could replace 40% of the world’s demand for portland cement. And there are sources of pozzolan all over the world. Saudi Arabia doesn’t have any fly ash, but it has mountains of pozzolan.”
Not unlike modern fly-ash concrete
The Romans’ concrete recipe seems to show some similarities to modern blends that replace some of the portland cement with fly ash, a waste product from coal-fired power plants, or blast-furnace slag. According to the U.S. Environmental Protection Agency, cement may contain up to 40% coal fly ash by weight.
Paul Preuss, who wrote the report on the team’s findings for Berkeley Lab, said in an email, “While fly ash and pozzolan have similar chemistry, many places have access to pozzolan that may not have ready access to fly ash (e.g., Saudi Arabia).” He added that because portland cement sets and cures quickly when compared to Roman seawater concrete, Roman concrete “isn’t a panacea.”
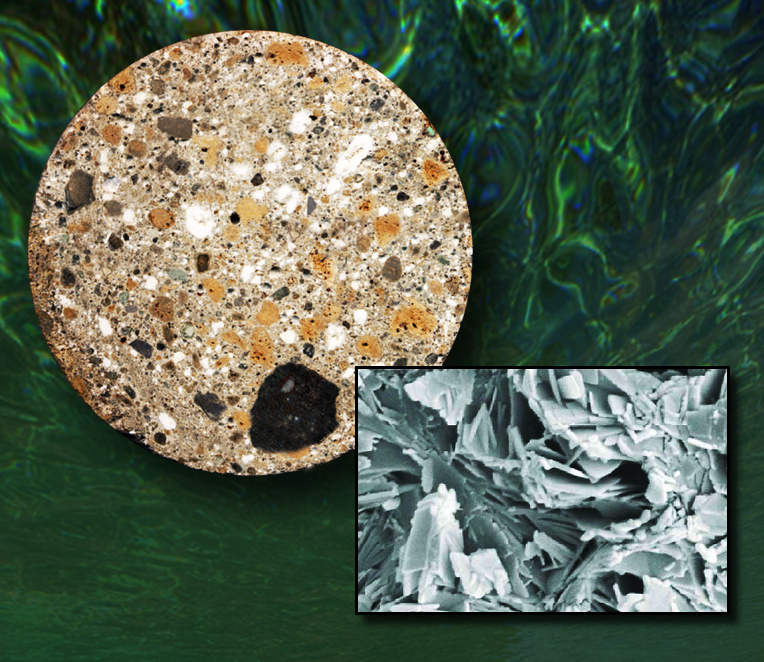
Core samples of Roman concrete 2000 years old contain pumice, lava and other volcanic material, and lime. The inset photo shows Al-tobermorite crystals, a key to the high quality of Roman concrete.