3 Best-Practice Deck Building Tips
Matt Risinger takes us on a tour of several of his deck construction projects and points out details that can help a deck last.
Since most decks are made of wood, we can of course expect them to rot … eventually. The average deck, composed of treated lumber joists, beams and posts, will last somewhere between 15-25 years depending on the climate zone it is in and how much water it is tormented by, not to mention how it is built. In many cases it is not the deck boards that rot, but rather the treated lumber framing which is susceptible. There are however some fairly simple ways to extend your deck structure’s life-span to potentially 30-50 years. Doing so allows you to extend or match the endurance of your deck’s structure to those of the deck boards if you are installing exotic woods such as Ipe or Massaranduba, which many of our local architects like to use and which can last into that 40-50yr range. Whether you are using composite deck boards or going all out for Teak, here are three relatively economical and efficient tips to prolong your deck.
TIP #1: SEAL THE JOIST TOPS
One of the main causes of decay in a deck structure comes from the penetration of water into the deck joists via the screw holes. Water works its way through or underneath deck boards into the screw holes, eventually forcing rot to occur (treated lumber or not). Treated lumber is certainly not foolproof and the chemicals in treated lumber do not penetrate 100% of the material, which leaves much of the core of any piece vulnerable. We’ve found that the best product to minimize and deflect water infiltration these points is a product called Grace Vycor Plus Flexible Flashing. This is a self-healing peel and stick product that comes in rolls 75′ long and various widths (4″ 6″ 9″ & 12″), and is an easy, efficient install. A 4″ roll is mostly what you’ll need.
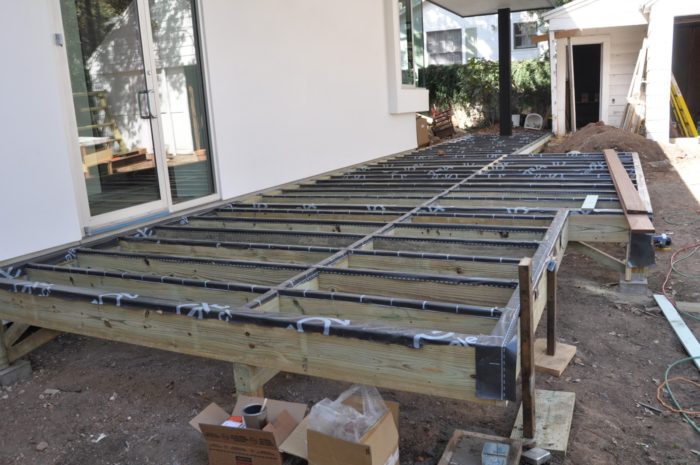
TIP #2: PROTECT YOUR POST BASES
Just as you do not want any of your deck joists in contact with the grade below it, neither do you want you post bases positioned similarly. This means not encasing it in the concrete, nor allowing it to sit directly in contact with the concrete where it can wick moisture or find itself encased in silt and topsoil after a few good downpours. The goal is to raise the bottom of the post just a couple of inches from the concrete and the soil to reduce it’s contact with organic material and moisture. Fortunately, there are plenty of good products for this important precautionary measure, which is easily and often neglected. On our last project, we used Simpson Strong Tie Z-Max 4×4 Adjustable post base and you can fasten these to your concrete footing with an anchor bolt, Tapcon fastener or a combination of a bolt with an appropriately chosen construction epoxy. This is again, a fairly economical and efficient implementation that can have a far reaching impact on your deck. As you are probably aware of, the endgrain of any wood species is like a bundle of straws and that bundle of cells will literally suck moisture right up and in, which leads us to Tip #3.
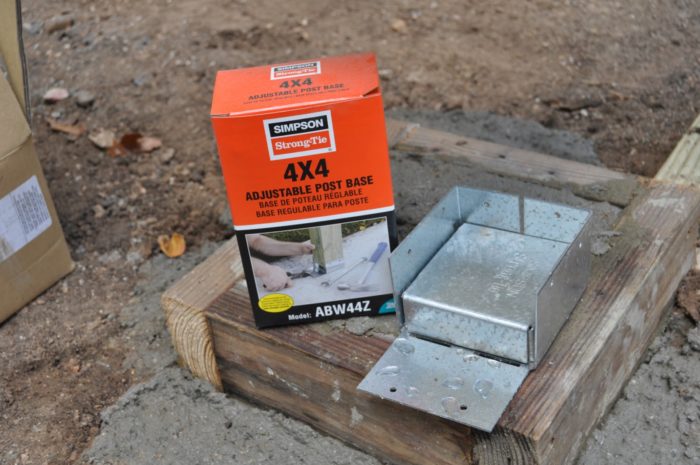
TIP#3: SEAL YOUR POST ENDS
Some might think this is over-the-top, but again, it’s a relatively simple and affordable addition to the installation of your treated lumber posts with long-term payoff. This process is a simple brush on application of a product called Seal Krete Multi Surface Acrylic Water Repellent, which should be available from your local building supply store (Home Depot in Austin carries it). When dried this product acts like a cap to your post ends and helps ensure a resistance to water wicking and infiltration. You can think of this as the equivalent of Scotch Guard for you posts. When you follow this tip in conjunction with Tip#2, your posts will be solid and reliable for a very long time.
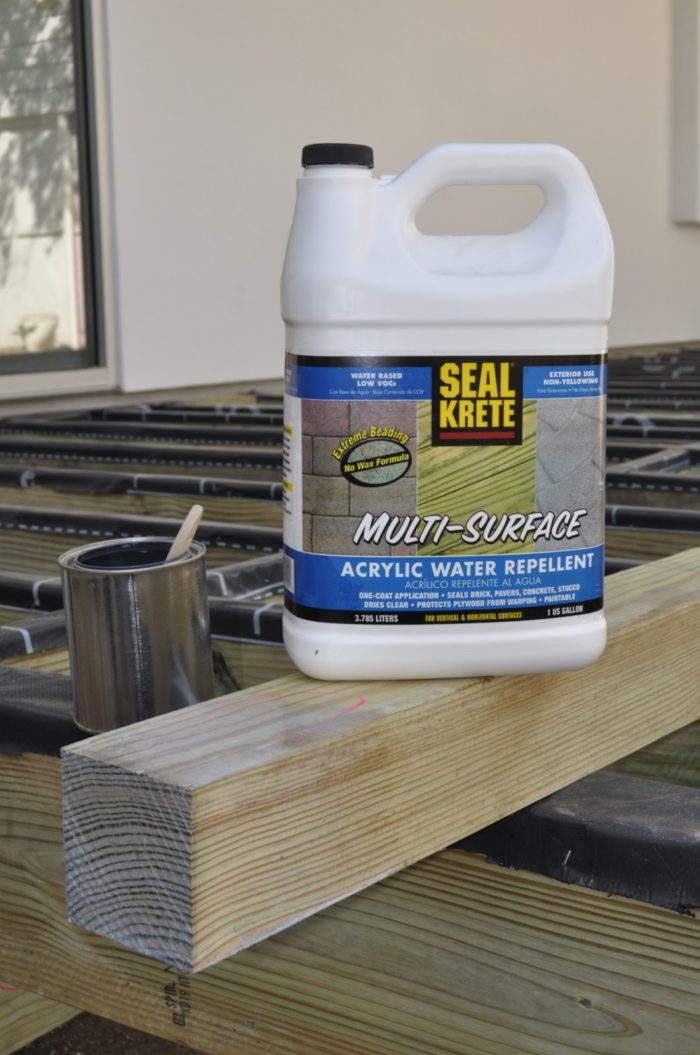
Best,
Matt Risinger – Risinger Homes in Austin, TX
Risinger Homes is a custom builder and whole house remodeling contractor that specializes in Architect driven and fine craftsmanship work. We utilize an in-house carpentry staff and the latest building science research to build dramatically more efficient, healthy and durable homes.
Be sure to check out my video blog on YouTube.
For more deck design and construction resources, visit the Fine Homebuilding Decks Project Guide.
View Comments
While applying water repellant to cut ends of posts is a good idea, a more important practice (and a building code requirement) is to treat the cut ends of lumber with a wood preservative. The building code requires either copper naphthenate or oxine copper based treatments. After the preservative is applied - then a water repellant can be applied for added protection.
What do you find the best way to apply the preservative? Brush on? Soak on end in bucket?
In what ways is the Vycor flashing product (product detail says not to walk on it because it is slippery) superior to Vycor Deck Protector?