Insulating Attic Stairs
The hatch or staircase leading up to an unfinished attic can be a big energy leak. Here are a few tips for sealing it up.
Better bought than built. A tight cap for pull-down attic stairs is hard to build. The weatherstripping details can be tough to execute, and the necessary weight of the hatch can be difficult to achieve. The Energy Guardian, shown here, costs about $185 plus shipping. ESS Energy Products (essnrg.com) also makes kits for kneewall access, walk-up stairways, and more.
Builders of energy-efficient homes often make attic access deliberately inconvenient—for example, by providing a small exterior door in the gable wall of the attic (accessible only with an extension ladder) rather than an interior attic hatch or stairs. That’s because both fixed and pull-down attic stairs present air-sealing and insulation challenges. It’s important to acknowledge the conflict between convenient attic access and energy efficiency. Although most homeowners want convenient access to their attic, it’s actually a bad idea to use an unconditioned attic for storage. If you have no other option, plan for storage by relocating insulation from the attic floor to the roof assembly, creating a conditioned attic.
Retrofit options
Most pull-down attic stairs are leaky and poorly insulated. You can remove the stairs and replace them with a smaller hatch. The hatch should be insulated with at least 6 in. of rigid foam, should have weatherstripping, and should be equipped with two latches that draw the hatch tightly closed.
Note that code requirements for hatches have recently been tightened. According to the 2009 IECC and IRC, “Access doors from conditioned spaces to unconditioned spaces … shall be weatherstripped and insulated to a level equivalent to … surrounding surfaces.” If you live in a climate zone where R-38 attic insulation is required, your access hatch also should be insulated to R-38.
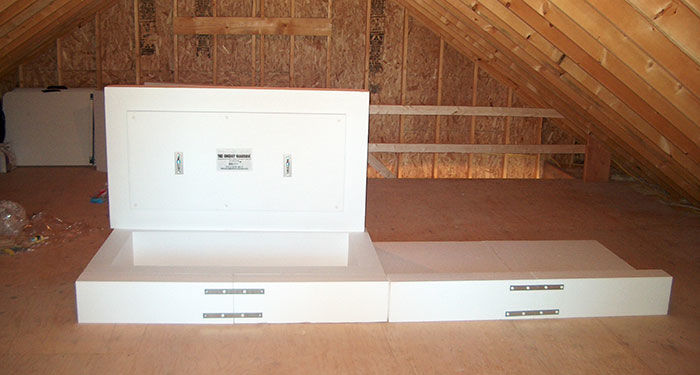
If you insist on keeping your pull-down stairs, you’ll need to purchase or make an insulated lid to cover the top of the stairs. Several manufacturers sell such lids; the best available product at this time appears to be the R-39 Energy Guardian Pull-Down Ladder Kit (photo above).
If you choose to build your own insulated lid, you’ll need to make a strong, airtight box out of thick rigid foam. The lid needs to be heavy enough to compress the weatherstripping at its base.
If your house has fixed stairs leading from a conditioned room to an unconditioned attic, you need to investigate whether the builder provided adequate insulation and air-barrier details. Your first question should be “Where is the air barrier?”
The usual location of the air barrier is at the base of the stairs. In this case, you’ll need to make sure that the door is insulated and weatherstripped. If you don’t want to buy an exterior door, you can attach a layer of rigid foam to the back of your existing door, and you can reduce air leaks by installing weatherstripping.
The two triangular walls on either side of the stairway need to be insulated. The underside of the attic stairs—the sloped ceiling created by the bottom of the stair stringers—also needs to be insulated and air sealed. This can be tricky; treads and risers usually leak air, and there isn’t much room above the sloped drywall to accommodate insulation. One approach is to remove the plaster or drywall under the stairs and to spray polyurethane foam against the treads and risers from below. Or, if the headroom is generous, it may be possible to install one or two layers of rigid foam in this location, followed by a new layer of drywall.
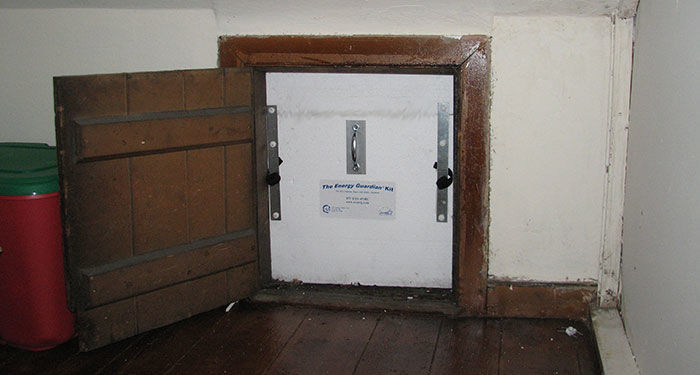
Some attic stairways lead to a small room that encloses the top of the stairway. In this case, there should be a door at the top of the stairs. This type of stairway is part of the conditioned space, and it is easier to insulate than one with the air barrier at the base of the stairs. First, make sure that the door is insulated and weatherstripped. Then check the walls and ceiling of the attic room to ensure they are well insulated. If necessary, install an attic-side air barrier (for example, sheets of foil-faced polyisocyanurate) at these locations to prevent air leaks and to improve the R-value of the insulated assemblies.
New construction details
If you are building a new house with stairs that lead from conditioned space to unconditioned space, you have a couple of options.
In most homes, the drywall is part of the air barrier. To maintain continuity of the air barrier above and below the stair stringers, it’s best to install some type of sheet good behind the stair stringers—usually a sloping band of 1⁄2-in. plywood—with an exposed lip above and below the stringers, in order to provide a surface to tape the drywall to. Another approach is to install a sloped 2×4 as blocking between the stringers and the studs; once the drywall is hung, the gap between the drywall and the 2×4 can be sealed with canned spray foam.
It’s best to insulate the walls on either side of the stairway before the stair stringers are installed. If the treads and risers separate conditioned space from unconditioned space, the underside of the stairs will need to be insulated—either with spray polyurethane foam or with a thick layer of rigid foam. In either case, pay attention to airbarrier continuity and thermal-barrier continuity at the edges of the sloped assembly.
Seal the gap behind the stringers
If there is a door at the bottom of your attic stairs that separates conditioned space from unconditioned space, then the stair assembly and adjacent walls need to be insulated and air-sealed. Because drywall typically is installed after the stairs are framed, you need to find a way to create a continuous air barrier up the walls. One way is to install 2×4 blocking behind the stringers. Once the drywall is installed, you can fill the gap with spray foam. The stairs themselves also need to be insulated, and the bottom of the stringers should be air-sealed with airtight drywall.
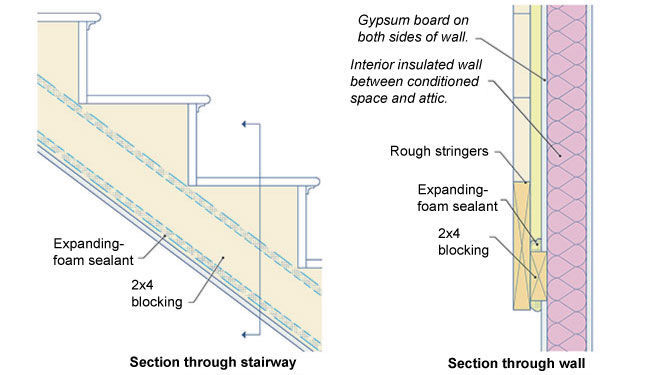
Requirements for Energy Star homes
Builders of Energy Star homes need to comply with the Thermal Bypass Checklist, a document that specifies air-sealing and insulation requirements for attic stairs. The EPA’s Thermal Bypass Checklist Guide includes these directions:
Staircases adjoining exterior walls, garages, or attics need complete air barriers throughout the framed assembly … A common area missing an air barrier at staircase walls occurs at small areas under enclosed landings or bottom stairs. Once framed, staircases can be difficult to complete with insulation and air barriers so it is important to coordinate details with the framing subcontractor …
- Structural sheathing can be used to extend above and below stringers to allow for taping with joint compound.
- Air barrier shall be fully aligned with insulation and any gaps are fully sealed with caulk or foam …
Similar to attic hatches, attic drop-down stairs represent very large thermal holes to the attic when not fully insulated and sealed … When insulating attic drop-down stairs, the insulation should not be installed between the steps … because it blocks the stairs themselves and is typically compressed in place, undermining its effective R-value …
- Attic drop-down stair shall be fully gasketed for a snug fit. However, gaps in weatherstripping to accommodate hinge hardware shall be acceptable …
- Factory made attic drop-down stair assemblies that are fully gasketed and include a rigid insulation panel much like an exterior insulated door are a great simple solution.
Photo: courtesy of ESS Energy Products.
Drawings: Steve Baczek, Architect.
Fine Homebuilding Recommended Products
Fine Homebuilding receives a commission for items purchased through links on this site, including Amazon Associates and other affiliate advertising programs.
Loctite Foamboard Adhesive
Disposable Suit
Respirator Mask