Refinish Your Wood Floors
Uncover the beauty in old hardwood flooring with a little patience and some great professional advice.
Synopsis: The ingredients needed to refinish wood floors are straightforward: just a single coat of stain over a carefully sanded surface, a coat of sealer to lock in the stain, and two coats of polyurethane to provide the wear layer. But the job also requires the right tools used in the right sequence, and it demands as much patience as it does skill. Author Brent Kelosky explains his process for refinishing a wood floor, including how to handle damaged areas.
Although my company does all types of flooring installations, our bread and butter has always been refinishing worn hardwood. Our goal is to uncover the beauty under the decrepit surface of the floor, which involves no small amount of labor. When we arrived on-site for the job shown here, the wall-to-wall carpeting had already been removed, revealing 750 sq. ft. of severely worn red-oak flooring that appeared original to this old Pennsylvania farmhouse. Although we got back down to bare wood quickly, that’s just the beginning of a job like this.
The job took a two-person crew just under five days to complete and cost about $4.50 per sq. ft. in labor and materials. Refinishing a hardwood floor is an admittedly disruptive process, but you realize it’s worth it when you first set eyes on the results.
The materials are straightforward — just a single coat of stain, a coat of sealer to lock in the stain, and two coats of polyurethane to provide the wear layer — but breathing new life into an old wood floor takes a lot of patience. It all starts with sanding.
Sanding will make or break your job
Without question, the critical difference between a professional-looking finished floor and a poor attempt is how much care is taken during the sanding stage. Although you’re only removing 1⁄16in. or so of actual wood, the sanding process takes multiple days — that is, if it’s done correctly.
In addition to some common hand and power tools, there are three specialized tools we use on our jobs: a belt floor sander, an orbital edger, and a buffer.
The bulk of the sanding work is handled by the large, very aggressive, 220v belt sander. Run back and forth through the room, working in the same direction as the floor’s wood grain, the belt sander is used to take slow, overlapping passes.
Although an upright orbital sander is the most common tool available at rental yards, we prefer to use a belt sander. (A drum sander is also an improvement over the orbital.) An orbital sander is a fairly gentle and forgiving tool, which may seem appealing if you’re unsure of your abilities, but it also requires much more time to do the job. On badly damaged floors, you’ll likely give up long before you get the blemishes sanded out.
A belt sander runs on wheels and uses a lever to lower the machine — which puts the sanding belt in contact with the floor surface — and then to lift it away. Because the machine is so aggressive, you can’t allow it to sit in one spot for even a couple of seconds or you will end up with significant gouges. It should be lowered to the floor as it’s being moved forward to start a pass, then lifted back off at the end of each pass.
A powerful handheld orbital sander called an edger is used to sand the perimeter of the room and any areas where the larger machine won’t fit. The smallest details and corners are done by hand with a scraper and sandpaper. Later in the process, a buffing machine is outfitted for finer sanding, but first comes the rough cut.
Get back to bare wood
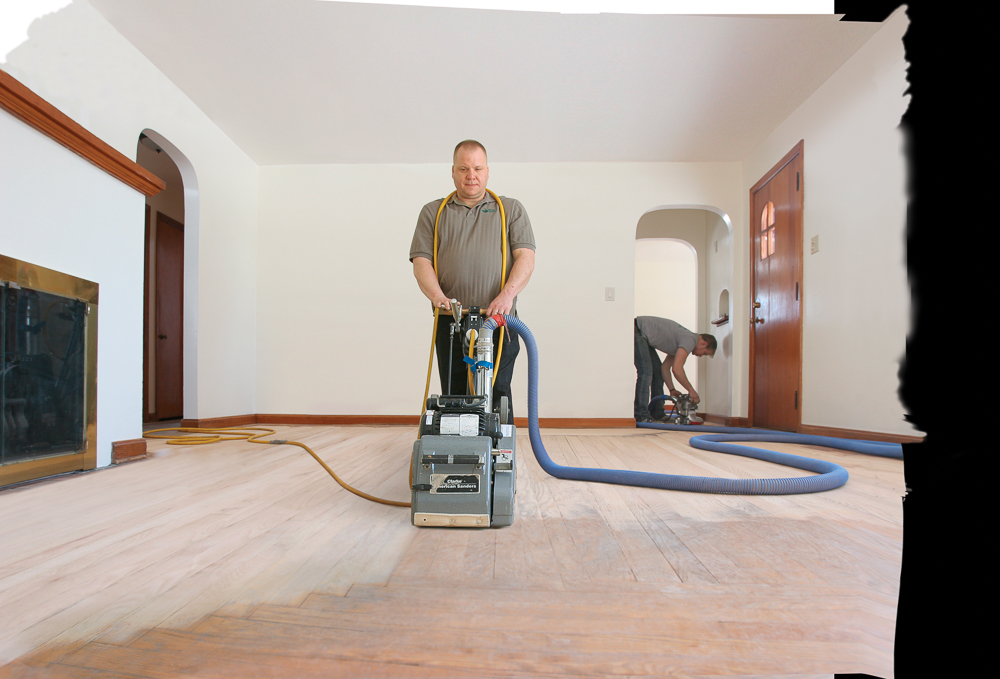
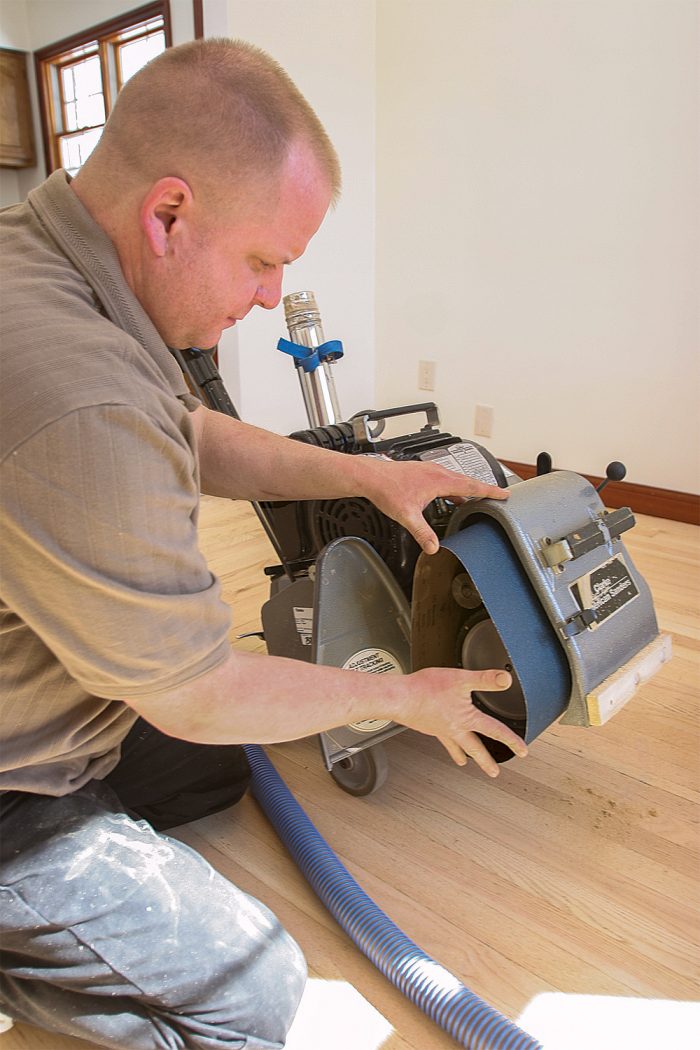
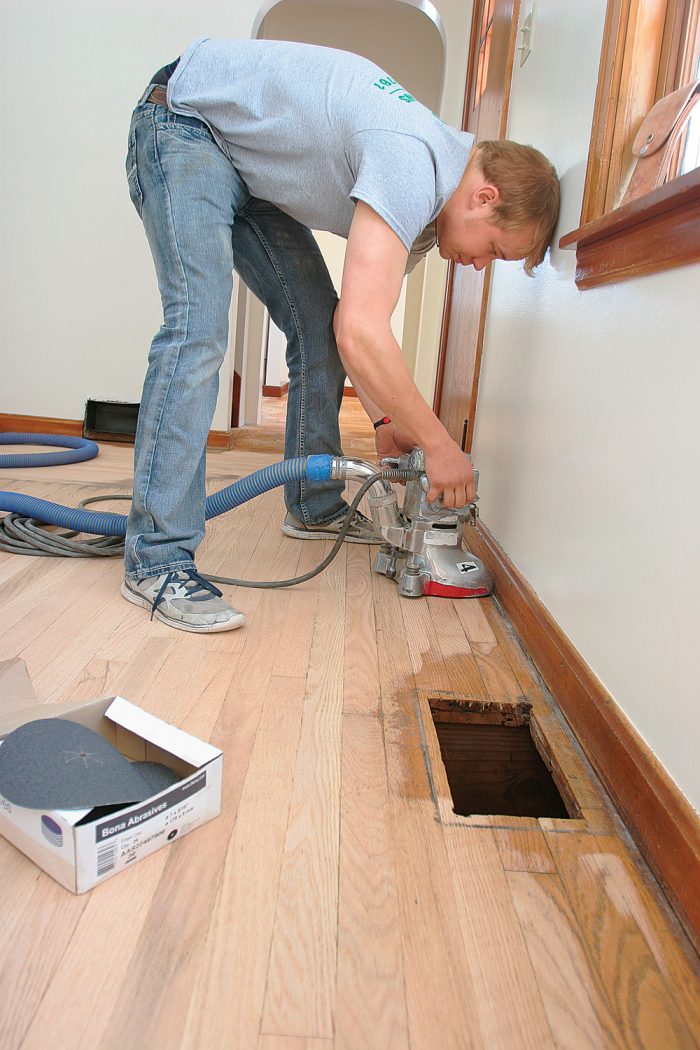
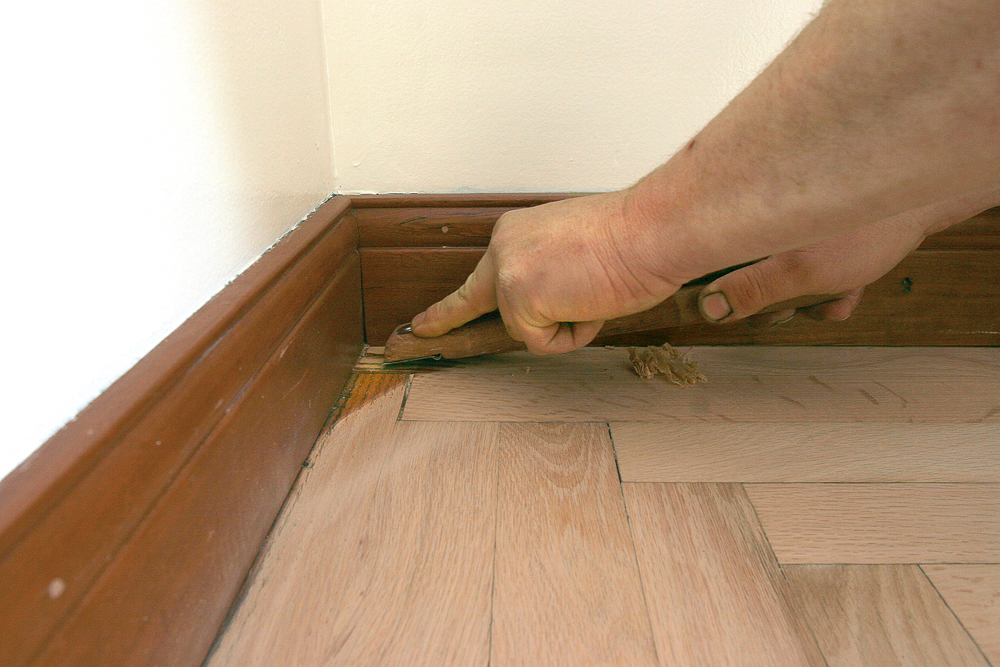
Sand incrementally and patiently
Although it’s not the coarsest option in our arsenal, 24 is typically the lowest grit we use for the rough cut. Such a coarse grit is only necessary when a floor has lots of built-up wax on the surface, and even then it’s pretty inefficient for removing actual wood. In most cases, we start with 36-grit sandpaper, which removes the existing topcoats and stain, revealing fresh wood across most of the floor. From there, we sand the floor twice more with 50-grit and 80-grit paper, spending additional time on problem areas such as deep scratches or surface stains (see “Dealing with damage”).
A crucial step that’s often not considered by first-timers is blending together the sanding patterns from the belt sander and the edger. Because they have different weights, operate at different speeds, and are run in different directions, these two machines leave the sanded floor looking and feeling inconsistent, even when they’re equipped with the same grit of sandpaper. The remedy for this problem is a random-orbit sander.
Even though we use 80-grit paper with the belt sander and the edger, experience has taught us that the random-orbit sander should be equipped with 60-grit paper, which roughs up the perimeter of the room and any other areas where the two machines had overlapping passes. Although it seems counterintuitive, this ensures that the stain penetrates evenly. A final pass with the upright buffer machine is the last step in the sanding process before the floor undergoes a thorough vacuuming.
Dealing with damage
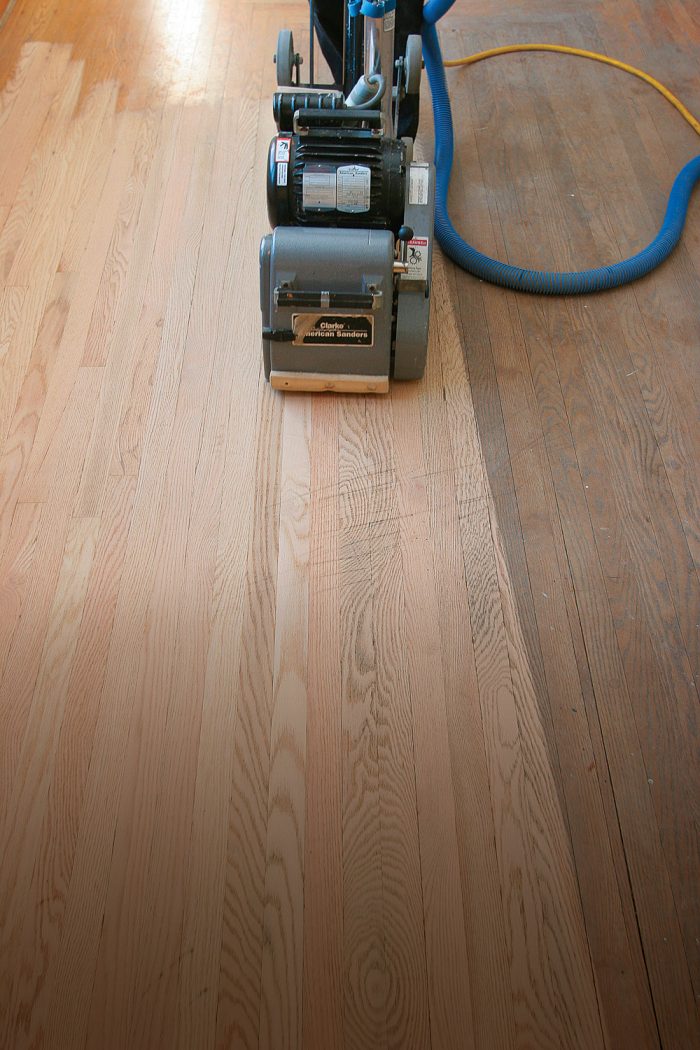
We often see pet stains, traffic patterns, knife marks along the edges of the room left from the carpet installation, and missing wood or abandoned registers. Our first choice is always to sand out the damage if we can, but damage often extends beyond the missing, scratched, or dented wood.
Sanding can’t fix everything, and often it’s impossible to predict whether a damaged section can be sanded out until you try. For areas that can’t be remedied with sanding, there are two options: acceptance or board replacement.
When sanding damaged areas, we take several passes with the belt sander at a slight angle to the wood grain, alternating the angle of the machine between each series of passes. It sometimes helps to spray the surface of the damaged flooring with water—just enough to wet it evenly—between passes with the belt sander. The water raises the grain of the wood, lifting deeper stains to be within reach of the sander.
We typically don’t bother filling large gaps with putty. Experience has taught us that the camouflage rarely lasts and that this repair isn’t worth the effort. It’s extremely difficult to fill an entire void, and seasonal movement combined with vibrations of walking usually open the gaps again. These imperfections are often best left as they are.
Sand with patience
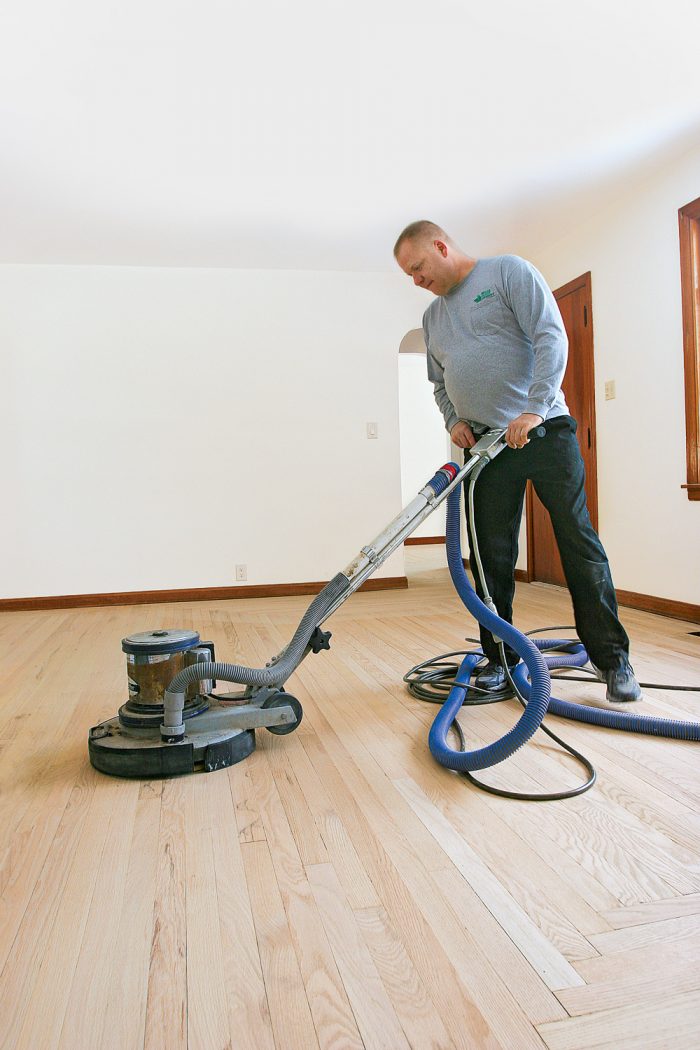
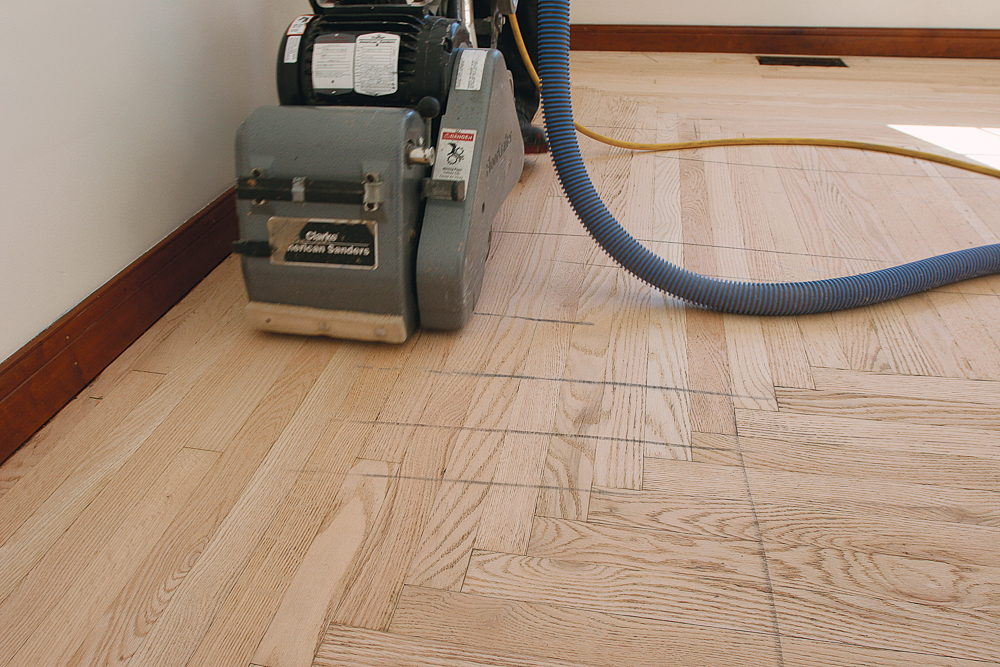
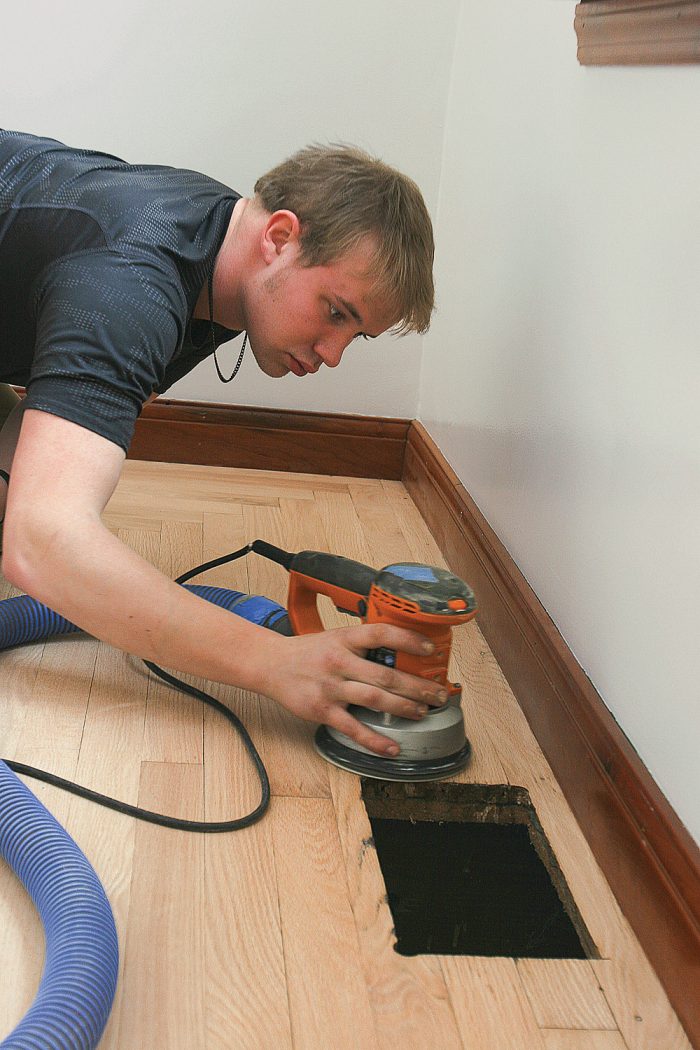
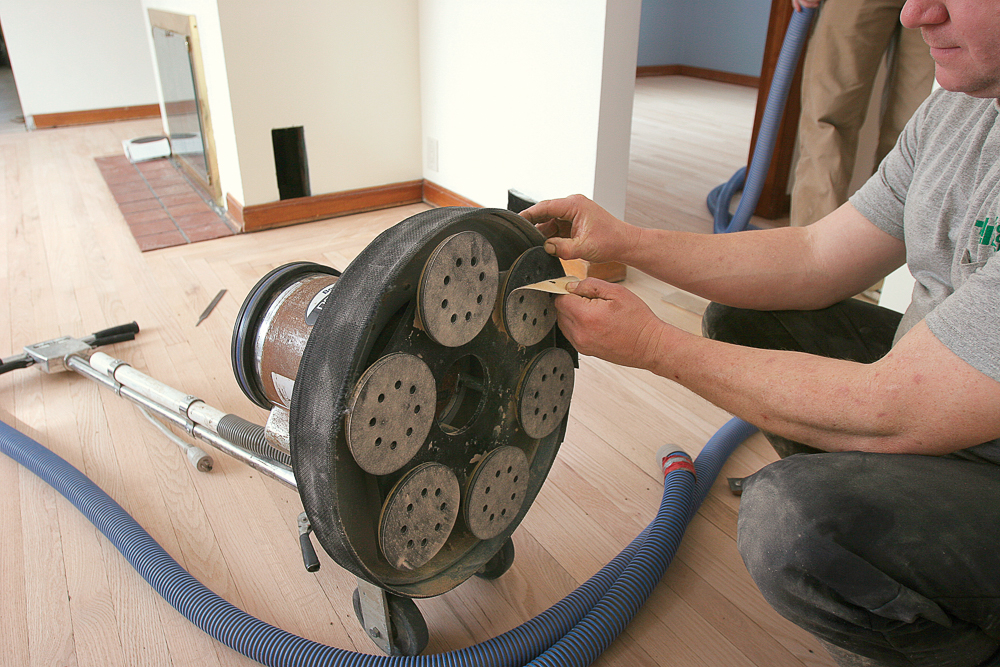
Staining is done by hand
Although water-based stains are an option, I’ve found them to be inferior to oil-based products, especially in getting even stain color in large rooms. Along with the sealer and topcoats that come after it, we use stain from Bona Kemi. When using multiple cans of stain, we combine them in one bucket to ensure that the color is uniform. We apply the stain with a lint-free cloth, then wipe the excess before it dries in place.
It’s critical to protect the unstained portions of the floor from moisture as you work. Water in the wood causes that part of the floor to absorb pigment differently, and even something as subtle as perspiration through the knees of your pants can leave discolored blotches in the finished floor. Always use disposable shoe covers when you’re walking the floor; bare or socked feet are an absolute no. Kneepads are essential, as well as a rag under each hand. In hot weather, a cloth tied around the head will catch sweat dripping from your brow.
Sandpaper scratches that went unnoticed during the previous floor-prep phase often become obvious as they trap pigment during the stain application. These scratches can be sanded by hand with the same 80-grit paper used in the last pass of the sanders and then recoated right away with stain. There’s no need to bother with the vacuum.
When the schedule allows, we like to let the stain dry overnight. If the sealer will be applied later the same day, we check for dryness by wiping a white cotton cloth across the stained surface. If no stain is transferred to the cloth, it’s dry enough to move on to the seal coat, which is a waterborne product used to separate the stain from the topcoats that come next. Depending on the brand of polyurethane, the sealer may not be a strict prerequisite, but we use it to provide an extra layer of build above the stain, which enhances the visual depth of the topcoats. After the sealer dries, minor blemishes and nail holes can be filled with a putty that matches the stain color before the entire floor is abraded with the buffer. Then the floor gets another pass with the vacuum, followed by a pass with tack cloths to pick up any remaining dust.
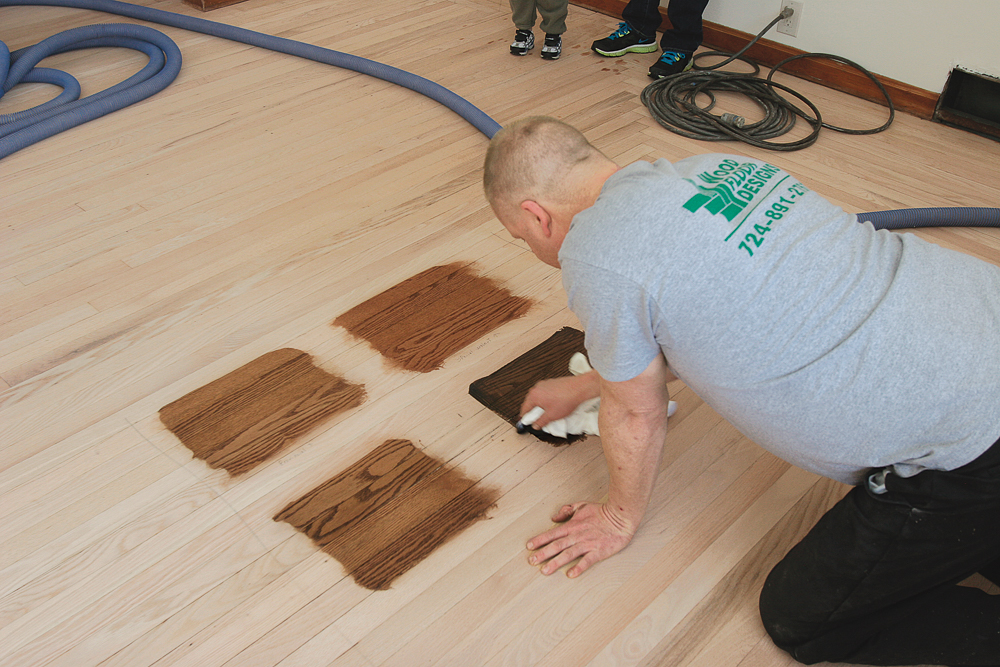
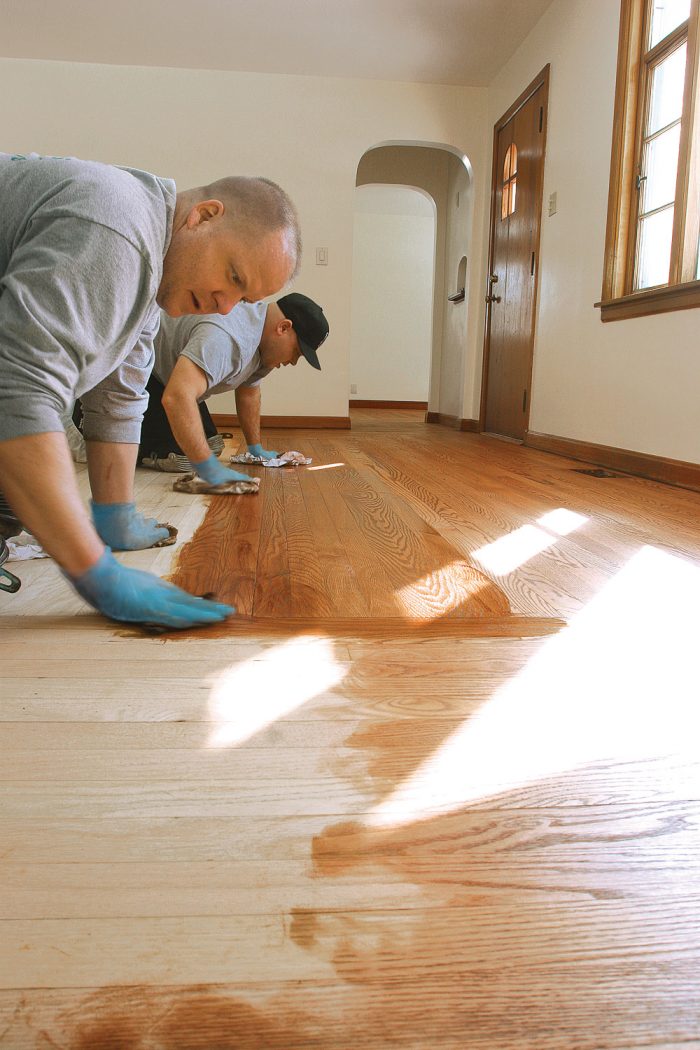
Waterborne polyurethane is the most durable choice
Although we use oil-based stain, we switch to a waterborne product for the polyurethane topcoats because the waterborne products have lower odor and faster dry times and are actually more durable than oil-based topcoats. For sheen, I encourage customers to opt for either satin or semigloss because wear patterns from pets and foot traffic are more obvious on floors with high-gloss finishes.
A small handheld foam pad is used to apply the polyurethane around the perimeter of the room, around details such as balusters and hearths, and in small areas. While the edges and details are still wet, a T-bar with a spongy applicator pad spreads finish across the rest of the floor in rows that follow the direction of the grain.
Optimum conditions for drying the topcoat are temperatures between 65°F and 80°F, with 40% to 60% relative humidity and some air movement to help wick away moisture, but not so much that it blows dust around.
The coat of sealer and the first coat of polyurethane are typically dry enough for a recoating in about four hours, but we never apply more than two coats of finish in a single day. My advice here is not to rush it, because the most recent coat of finish always dries faster than what’s under it, and you don’t want to risk trapping moisture, which leads to adhesion problems.
There should be no need for sanding between or after coats of polyurethane. After the last coat, the floor can be walked on gently in about four or five hours, but restrict normal foot traffic for 24 hours. Anything that might prevent drying, such as an area rug, shouldn’t be replaced until after seven days to allow the finish to cure fully.
Topcoats share the same technique
The topcoats on a floor—from the single coat of sealer through the two coats of water-based polyurethane—are applied using the same tools and techniques. Make sure to buff the floor after the seal coat, but you shouldn’t need to sand between or after the coats of polyurethane.
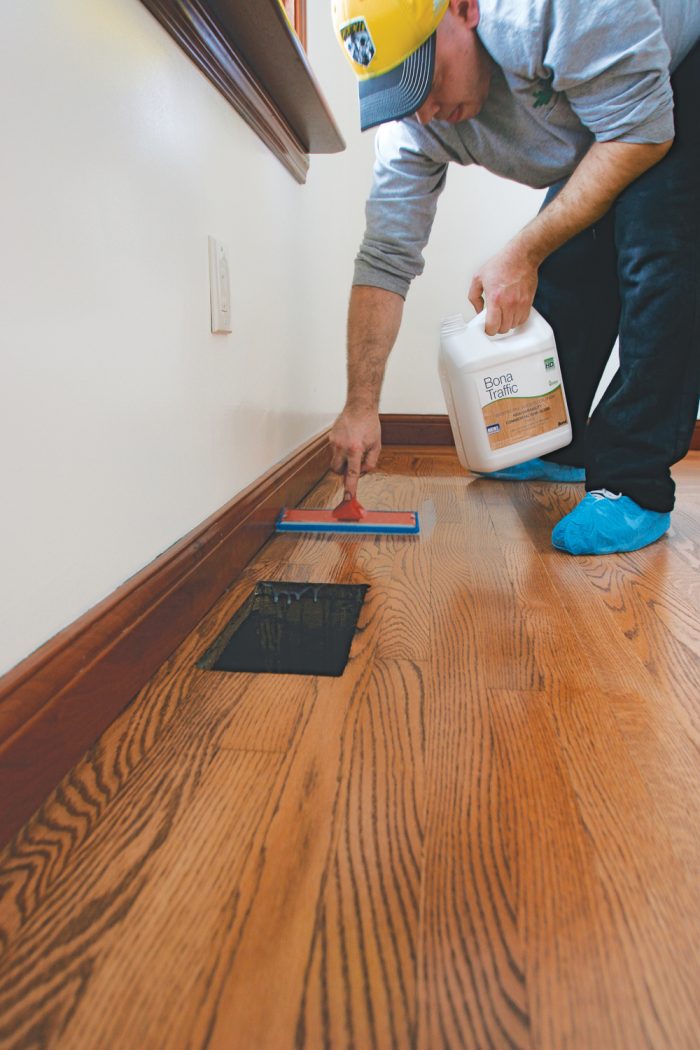
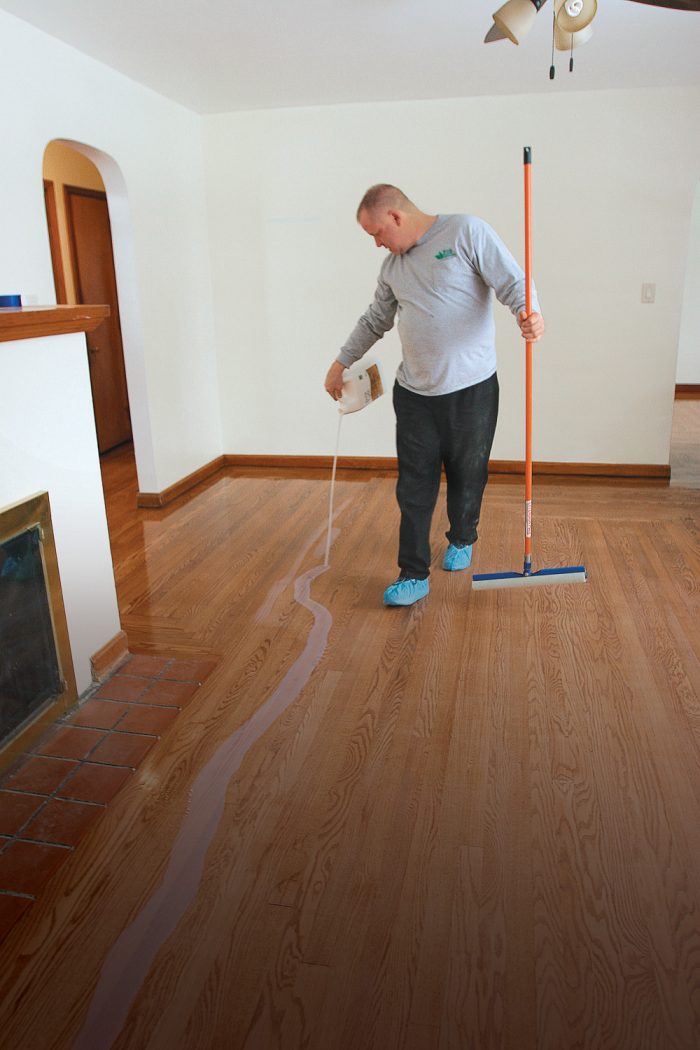
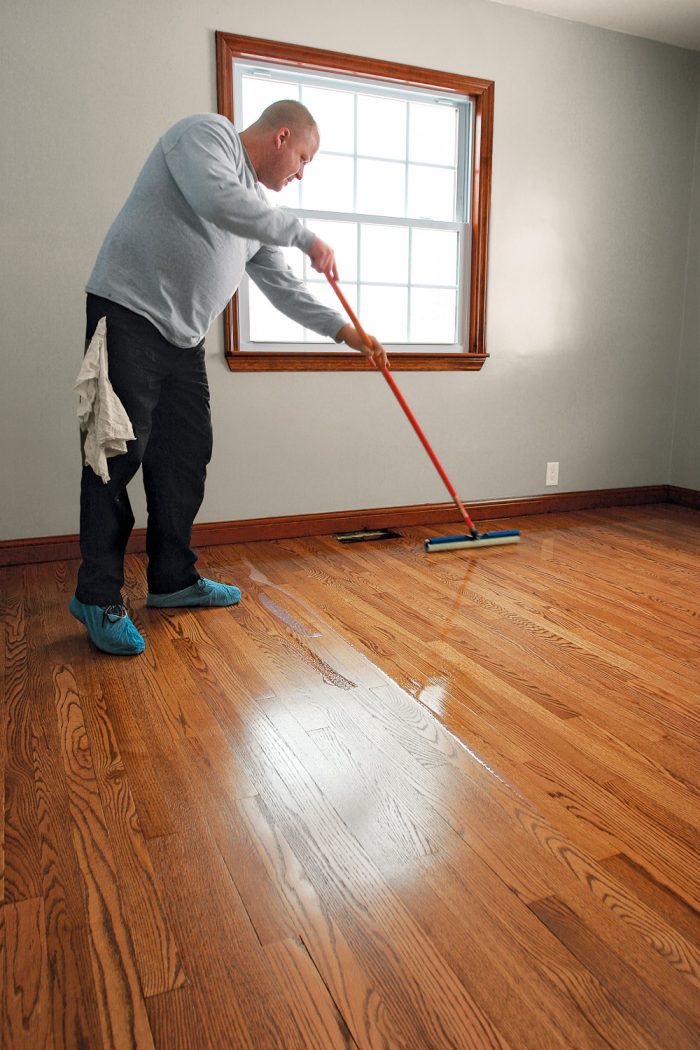
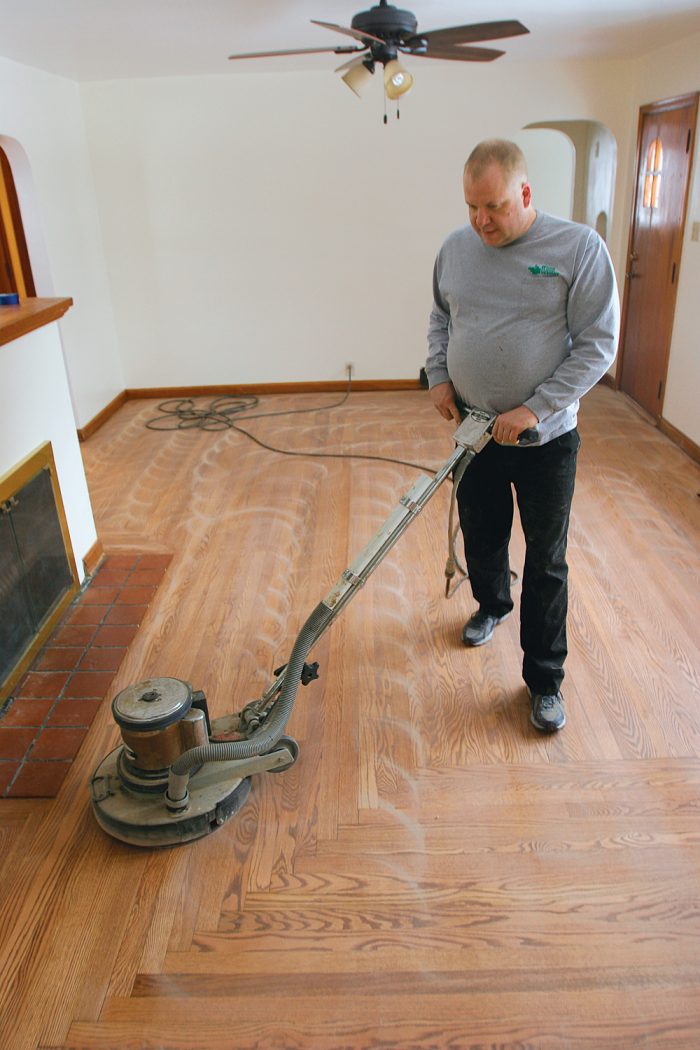
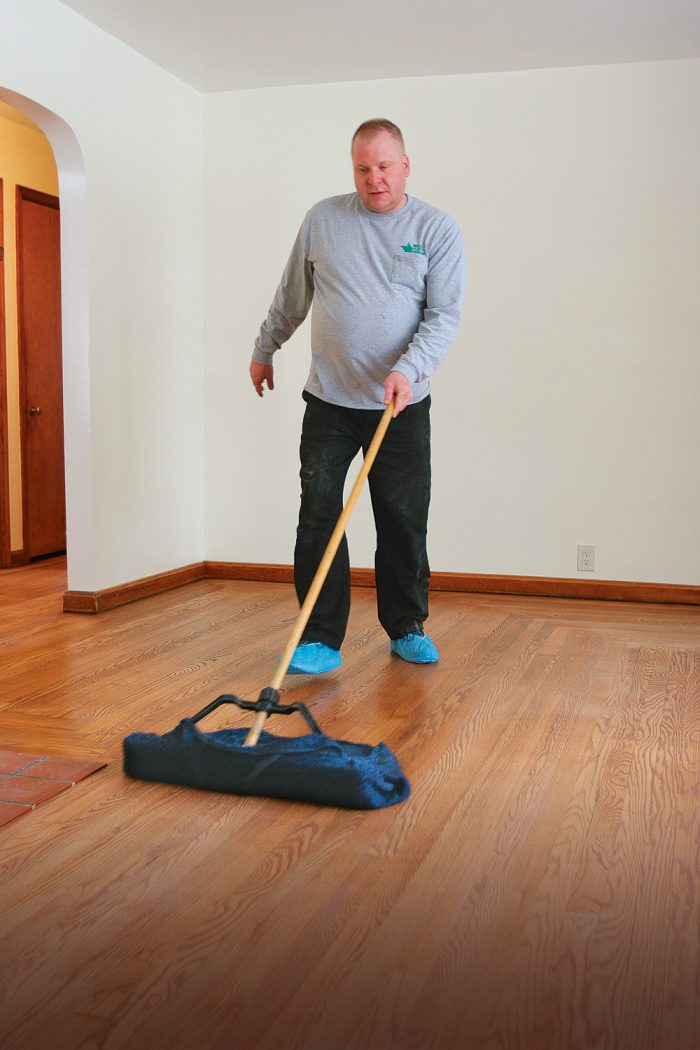
Photos by Justin Fink
Related stories:
- 11 Wood-Flooring Problems and Their Solutions
- Refinishing Floors Safely
- Invisible Repairs for a Hardwood Floor
From Fine Homebuilding #253
For many more photos and practical advice on framing eaves, please click the View PDF button below.