A New Approach to Coffered Ceilings
Foam-core beams and moldings make for an attractive, easy-to-install coffered ceiling.
Synopsis: A coffered ceiling can take a room from ordinary to impressive, but a conventional coffered ceiling is expensive and tricky to install. Drywall experts Brian Kitchin and Nick Aitchison have developed a technique for creating a coffered ceiling from EPS moldings and trim that are covered at the factory with a layer of joint compound. These pieces are easy to cut, are far lighter than wood, and don’t move with changes in humidity and temperature.
Click here to see a video of the Drywall Nation guys in action adding coffers to a flat ceiling.
As drywallers, we’re used to most of our work being the backdrop for other finishes. Increasingly, however, we’re adding those details that make a home’s interior stand out, such as the coffered ceiling shown here. Several manufacturers make EPS polystyrene moldings and trim for exterior and interior use. (Foamcore Architectural Mouldings, Toronto; foamcoremouldings.com.) These moldings are more commonly used for synthetic-stucco exteriors, sometimes called EIFS (exterior insulation and finish system). Recently, they have been adapted for interiors by applying a smooth coat of joint compound to the high-density EPS substrate. The visible surfaces are caulked and painted later.
We glue the moldings — which come in many profiles — to the ceiling and walls with polyurethane drywall adhesive, clamping them temporarily with coarse-thread drywall screws. Once the glue is dry, the bond is tenacious. We’ve had to scrape away misplaced moldings only a few hours later.
Once the pieces are hung, we fill any gaps that are larger than 3/8 in. with a squirt of the adhesive to act as a backer for the lightweight joint compound we apply to the seams and gaps. The moldings come with all of the visible surfaces coated with compound, and they accept paint like drywall. The finished product is often mistaken for painted wood. Because the EPS is very stable, it doesn’t move with changes in humidity and temperature, so the joints stay tight during our humid summers and cold winters.
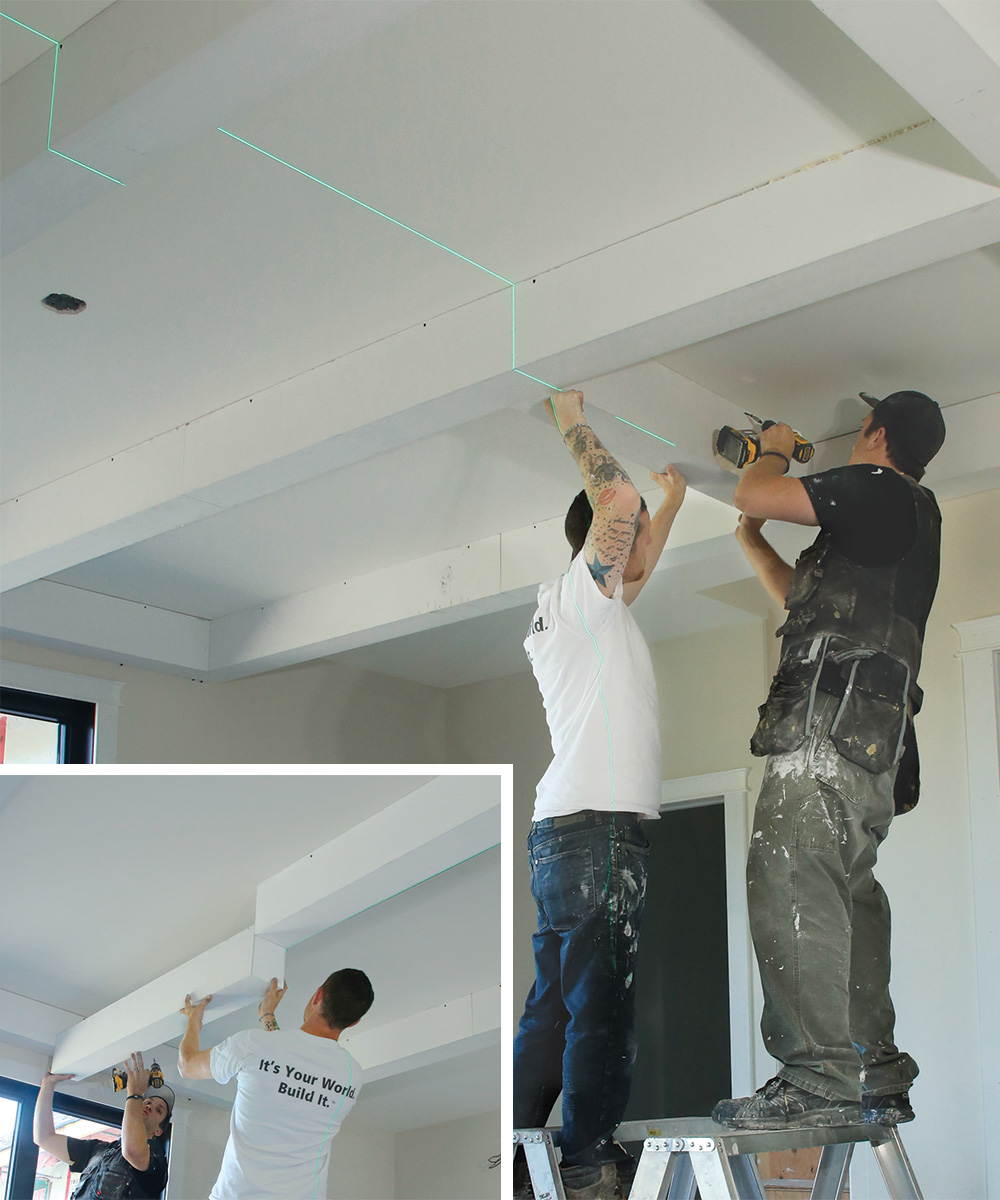
Why would a homeowner or builder choose to install a coffered ceiling or crown molding made from EPS and joint compound instead of wood or MDF? The answer is simple: speed and cost. With a crew of three, we installed the coffered ceiling shown here in half a day. Caulking all the gaps and inside corners took another two hours. The material cost $1400 (U.S.), a fraction of what it would cost a finish carpenter to install a similar ceiling made from wood moldings. The only downside we see is that the moldings only come in 8-ft. lengths, so you end up making more cuts and filling more seams than you would with longer material.
Cut and fit the crown molding![]() Once the grid of intersecting beams is complete, crown molding with a triangular cross section is installed around the inside. Inside corners are mitered rather than coped because of the material’s EPS core. Miters stay tight seasonally because the drywall substrate is dimensionally stable, as are the compound-coated foam moldings on top. Once all the crown is in place, the corners are caulked, and any butt joints are filled with compound (no tape) and sanded. |
What is this stuff?
Made from high-density expanded polystyrene (EPS), foam moldings like those used in this project have their origins in the architectural details found on synthetic-stucco exteriors. But instead of a fiberglass mesh that accepts acrylic stucco, the moldings made for interior use are coated at the factory with a thin layer of joint compound. Inside corners are mitered on-site rather than coped, and seams where the lengths of molding come together use butt joints rather than scarf joints. Corners are caulked, and gaps and seams are filled with compound and sanded with 220-grit paper when dry. Suppliers of foam moldings, who usually cater to the synthetic-stucco and drywall trades, have large catalogs of stock profiles and can make custom profiles subject to minimum order. Common profiles cost from $3 to $6 (U.S.) per ft.
From FineHomebuilding #264
Photos by Patrick McCombe