Passive House Meets Pueblo
Three projects by a Santa Fe architect demonstrate how well the Passive House performance standard and the Southwest style work together.
Synopsis: In this article, Andrew Michler presents three Passive Houses he built in the Southwest United States and how they seamlessly fit the style of the local New Mexican architecture. Using the Passive House focus on energy conservation as a cost-effective approach to efficiency, Michler turned his attention to the envelope of each home, particularly the insulation and air-sealing details and how these would create energy-efficient air and vapor barriers. For as little as $175 per square foot, Michler built the Balance Project, the Taos House, and the Olsen House, incorporating the New Mexican style of thick, adobe-brick walls into his Passive House envelope-first approach.
Northern New Mexico has one of the oldest design traditions in the United States. A mix of cultures intersecting for the past 500 years has led to distinctive architecture that speaks as much to the arid Southwest region as it does the people who live there. The oldest building still inhabited in the United States is the Taos Pueblo (taospueblo.com), built with a stepped, boxy form and massive adobe-brick walls. When the Spanish entered the region, they brought the hacienda with its long front portals, tall windows, and intricate woodwork. The railroad brought manufactured materials like corrugated steel and standardized lumber and trim, leading to the Territorial style. Many new buildings in the region are a mash-up of these influences.
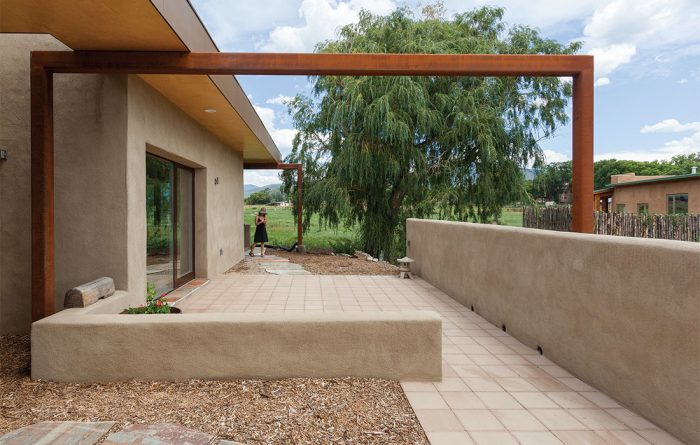
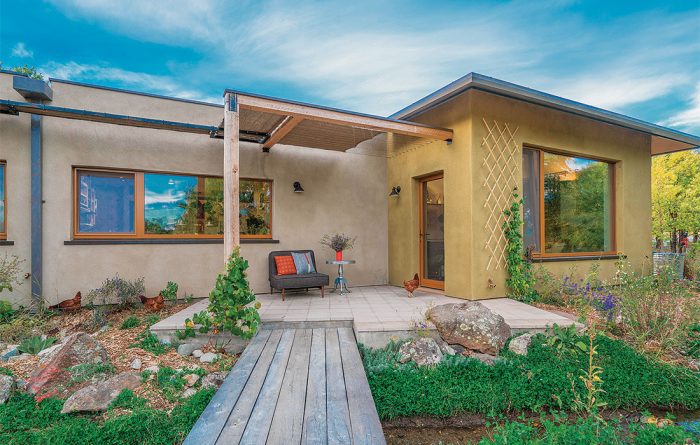
It is in this rich backdrop that NEEDBASED, Inc. — a design firm where I work under my colleague, architect Jonah Stanford — built three certified Passive Houses: the Balance Project, the Taos House, and the Olsen House. For these projects, we were looking for a robust, energy-efficient system for building homes that would also be affordable. We prefer a contemporary design approach that draws on traditional qualities like the parapet roof, natural materials, and, of course, the thick walls that are ubiquitous in the Southwest. We have found that we can design Passive Houses at market prices that use a fraction of the energy of a code-built home. We’ve built these houses for as little as $175 per sq. ft. and feel that $300 per sq. ft. is a budget that we can regularly hit. When this cost increases, it is commonly due to challenges with the building site.
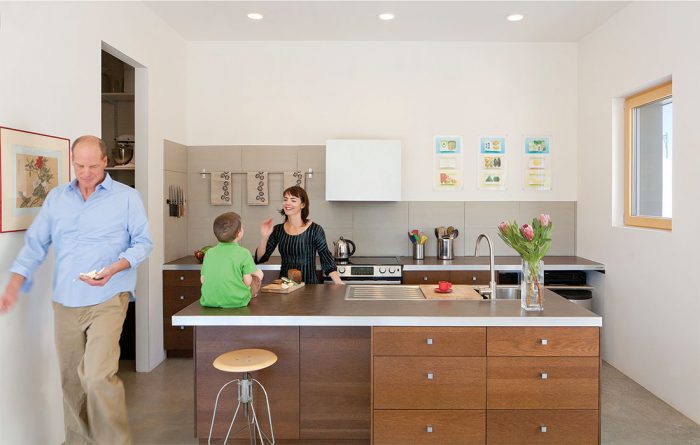
The Balance Project: A Modern Home Office
The Balance Project is a home and office in the Railyard District of Santa Fe and the first certified Passive House in New Mexico. It has a modern design, but it fits in neatly with the age-old Pueblo-style buildings surrounding it. It has a solar thermal domestic water heater with a radiant slab that supplies 100% of the heating and 96% of the hot water. The wall system is constructed of 2×6 framing with a taped plywood air barrier, off of which are hung Larsen trusses filled with cellulose insulation. Furring strips for the fiber-cement siding create a rain-screen cavity that helps the wall dry quickly.
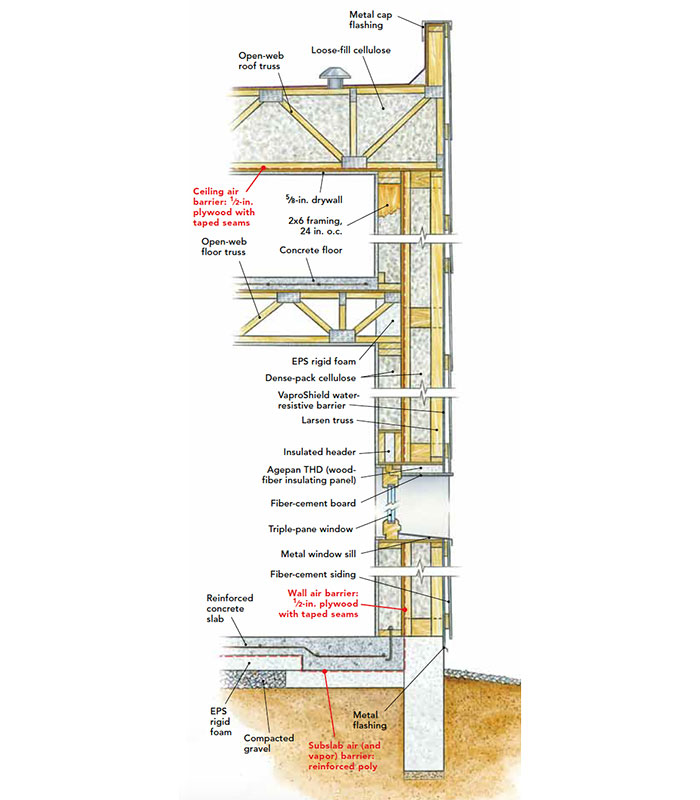
Envelope Specs
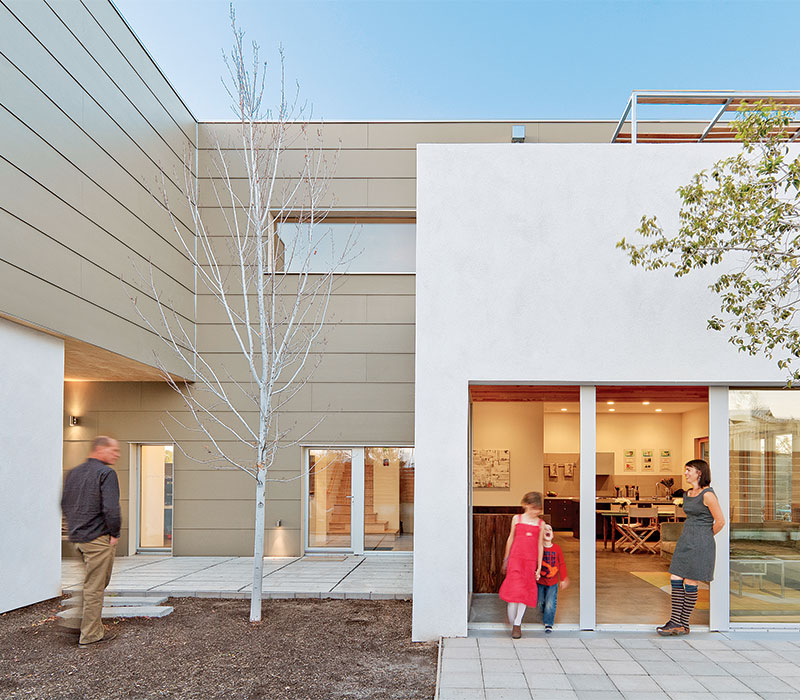
Slab R-26 EPS rigid foam
Walls R-58 dense-pack cellulose
Roof R-98 loose-fill cellulose
Air barrier Poly sheeting under slab; plywood sheathing (seams taped with Isocell airstop tape) on walls and roof
Windows Optiwin tilt-turn (U-0.137/R-7.2/SHGC 0.60)
Blower-door test results 0.47 ACH50
System Specs
Ventilation Zehnder 350 and 200 ERV
Heating In-floor hydronic radiant
Hot water Solar-tank heat exchanger
Cooling Passive shading and night-sky cooling via ventilation system
Measured Building Performance
Heated sq. ft. 3,452
Average energy intensity 1.82 kBtu per sq. ft. per year
Average total energy use 6,314 kBtu per year
Not passive solar, Passive House
There has long been a lively passive-solar design movement in New Mexico due to the 300 days of sun a year and the thermal mass inherent in adobe buildings. In our experience, though, we have found that passive-solar design has been inadequate for comfort and predictability. It is also too site specific, making it hard to scale or adapt to different conditions. Without significant owner interaction, these homes tend to overheat, even in the winter, but especially in spring and fall. Yet because these homes are so reliant on the sun, a few cloudy days or cold nights will still require large heating systems.
We have worked with the LEED for Homes certification program and the National Association of Home Builder’s Green Building program, too, but found the design processes to be very generalized and prescriptive, lacking any opportunity for solutions based on actual local conditions. While working on an affordable housing development, for instance, we could not justify a $5,000 increase in mechanical equipment simply to move from an 85% to a 90%-efficient boiler, which would provide so little return for our clients. It was during this time that we heard about the Passive House system and its focus on energy conservation as a cost-effective approach to efficiency. We could take that same money to greatly increase the home’s insulation levels and address air-sealing, yielding significant reductions in energy use and utility expenses. This focus on the envelope—a “fabric first” approach—is now the core of our design process.
The Passive House standard was developed 25 years ago in Germany and employs a strict performance metric to achieve a comfortable interior without using significant energy resources. With a very tight, superinsulated envelope that is properly energy-modeled and free of thermal bridges, this type of building works equally well during both heating and cooling periods with very small mechanical systems. The Southern Rockies is a very desirable environment for designing a Passive House, as the elevation of over 7,000 ft. above sea level brings cold winter nights while consistent sun provides for relatively warmer daytime temperatures. A Passive House–certified project can use no more than 4.75 kBtu per sq. ft. per year in heating and cooling energy and 38 kBtu per sq. ft. per year in other energy usage—or roughly 80% less than most code-built buildings.
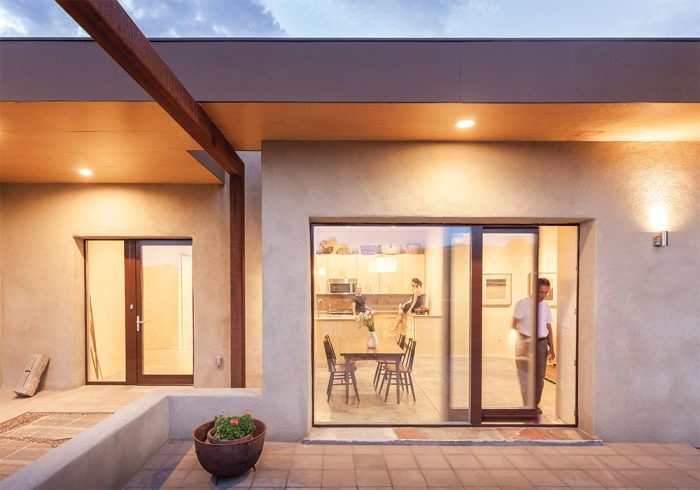
With an additional focus on comfort, a Passive House stands out compared to other approaches. Most buildings rely principally on convection through heating and cooling equipment to maintain air temperature. But comfort is also subject to radiation—we feel the radiant temperatures of cold windows and hot ceilings, and often find the difference between surfaces and interior air temperature uncomfortable. A Passive House will have only a slight contrast in temperature between the ambient air and interior surfaces, providing thermal stability and comfort. This is one of the most talked about benefits by occupants and is rarely experienced in average homes.
We have learned how to optimize widow-to-wall ratios and massing, and the Passive House Planning Package design and verification software is very good at predicting heating needs as well as overheating potential. That was one of our first lessons with the Balance Project: for a few reasons, we added more glass than the energy model called for. Indeed, the home was overheating and we had to add sunshading devices.
In this climate, a smaller Passive House will have about R-60 walls, R-100 roofs, and R-30 insulation beneath the slab. This allows us to eliminate the need for pricey heating and cooling systems and use those savings to upgrade the envelope. We have successfully been able to meet nearly 100% of heating and hot water needs with small solar-thermal systems. With proper shading, operable windows for ventilation, and the ability to flush the indoor air at night with the energy recovery ventilators (ERVs), the homes require little, if any, air conditioning, even during 90°F days. Dramatically reducing this demand not only simplifies energy systems, but also lowers costs and improves the resilience of the house. And best of all, insulation doesn’t have any operating costs and doesn’t break down after a few years like complex mechanical equipment, making it a lifelong investment.
The Taos House: Reminiscent of a historic neighbor
With the Taos House, we again incorporated simple forms and emphasized the relationship with its surroundings, including the historic Taos Pueblo only three miles away. Here, we used ZIP System sheathing as an air barrier. The house has 10 in. of exterior EPS rigid foam with a three-coat stucco system. A solar thermal system heats the domestic hot water and an electric on-demand water heater feeds the radiant slab. Energy usage is more than offset annually by a 2.75kw photovoltaic system.
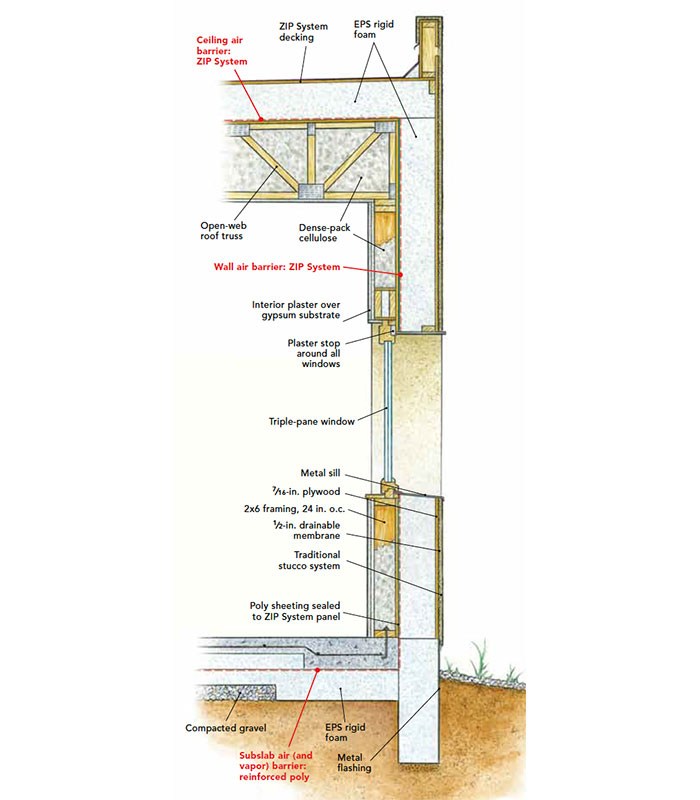

Envelope Specs
Slab R-30 EPS rigid foam
Walls R-58 dense-pack cellulose and EPS rigid foam
Roof R-104 dense-pack cellulose and EPS rigid foam
Air barrier Poly sheeting under slab; taped ZIP System sheathing on walls and ceiling
Windows Zola (U-0.123/R-8.1/SHGC 0.62)
Blower-door test results 0.42 ACH50
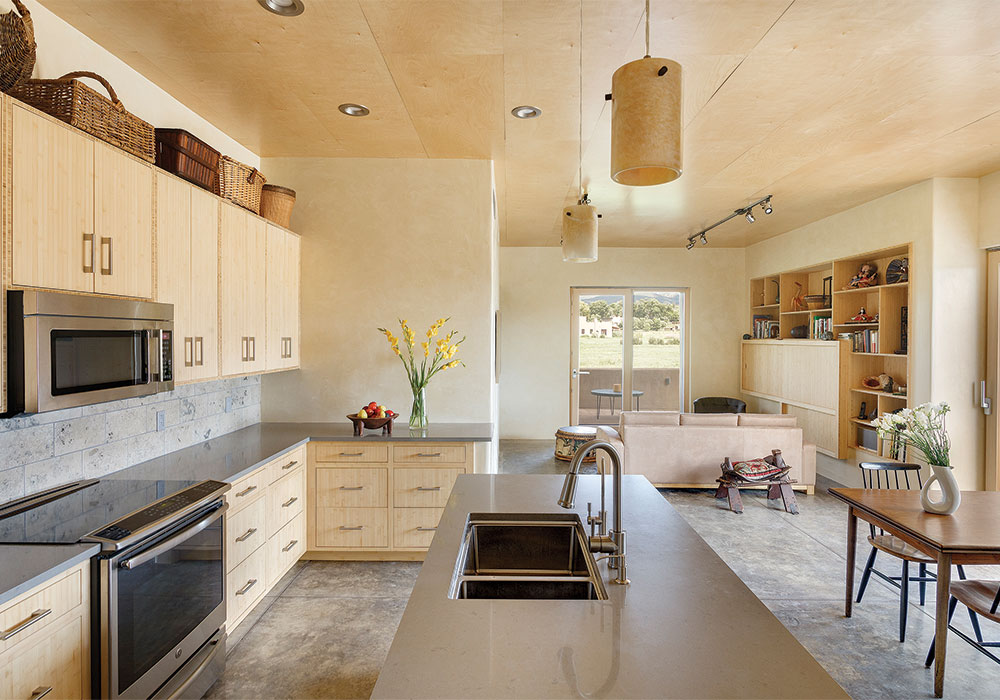
System Specs
Ventilation Zehnder 350 ERV
Heating In-floor hydronic radiant with electric boiler
Hot water Solar thermal with 80-gal. storage tank and electric on-demand backup
Cooling Passive shading and night-sky cooling via ERV
On-site energy generation 2.75kw photovoltaic system
Measured Building Performance
Heated sq. ft. 1,620
Average energy intensity 2.11 kBtu per sq. ft. per year
Average total energy use 3,417 kBtu per year
Average total energy generation 3.532 kBtu per year
Embracing thick walls
Massive walls have been part of the local vernacular since the first days of adobe-brick-building. In our contemporary designs, the thickened walls can enhance the occupant’s experience. Not only do they create a sense of stability and scale, but thick walls also provide the opportunity to create alcoves, shelves, and informal sitting nooks.
Airtightness is as important to energy loss as insulation. We have found the Passive House airtightness standard is very achievable and all our projects test close to half of the 0.60 ACH50 threshold while under construction. Moreover, it’s important that the house remain airtight over time, so we use quality materials and make sure they are well protected in the building assembly.
The key is to design a dedicated air-barrier system that properly connects the floors to the walls and the walls to the roof. Most of our assemblies use a combination of tapes and either a solid substrate like plywood or ZIP System sheathing in addition to smart membranes, which also provide vapor control. We work very closely with the contractors to ensure the whole team is aware of the importance of airtightness. A blower-door test is done before covering the air barrier’s components and again after installing the majority of finishes. Interestingly, the homes test leakier when finished, so it is critical to be very diligent with the air barrier during construction.
With such a tight envelope, a balanced air-exchange system is a critical component of a Passive House. We now spec professionally commissioned Zehnder ERVs in all of our projects to exchange indoor air. We found lower-cost brands can perform poorly, leading the occupants to turn them off if they haven’t broken down altogether—and neither is good for indoor air quality or comfort. The Passive House Institute (PHI) certifies components like ERVs, and will discount the labeled efficiency automatically if they are not independently tested.
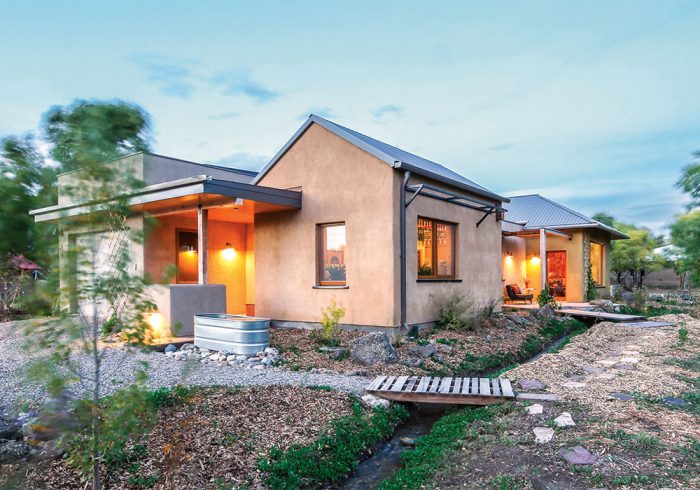
One of the weakest links in a home’s thermal envelope is the window frame. All of our projects have large triple-pane windows, which minimize the frame-to-glass ratio and are also certified by PHI. We can improve window performance by insulating over the frame from the exterior as well.
One of the most important lessons we learned when designing a Passive House envelope is that it is crucial to make sure every single building component is chosen for a specific task. There are dozens of ways to build a high-quality, high performance wall. Each is based on a systems approach that is airtight, thermal-bridge free, and vapor controlled while still providing room for mechanical services, structure, and cladding. If you try to force components to perform multiple tasks at the same time, they can fail in performance or durability. For instance, using spray-foam insulation as an air-seal will not provide an airtight envelope; similarly, installing an air barrier in the wrong place could lead to condensation and complicate mechanical penetrations. This will lead to expensive repairs and unsatisfactory performance results in addition to unhappy contractors and owners.
Each project has its own distinctive assembly drawn from the specific needs of the homeowners and the site as well as our lessons learned on past projects. By incorporating the Passive House program into our practice we are confident that our buildings will provide many generations with comfortable, efficient, and affordable homes—even with unpredictable future climates.
The Olsen House: Territorial with pitched roofs
Simple and discreet with pitched metal roofs, the Olsen House design borrows from the Territorial style. We sited the garage to avoid northwest-facing windows, which tend to overheat the interior. The double-stud walls are insulated with cellulose and are sheathed with ZIP System. The vaulted ceiling has an Intello smart vapor retarder and air barrier. We again utilized a combination solar thermal system that provides hydronic heating and domestic hot water. The owner opted for a 2.5kw solar electric system, which is sized for a future plug-in car.
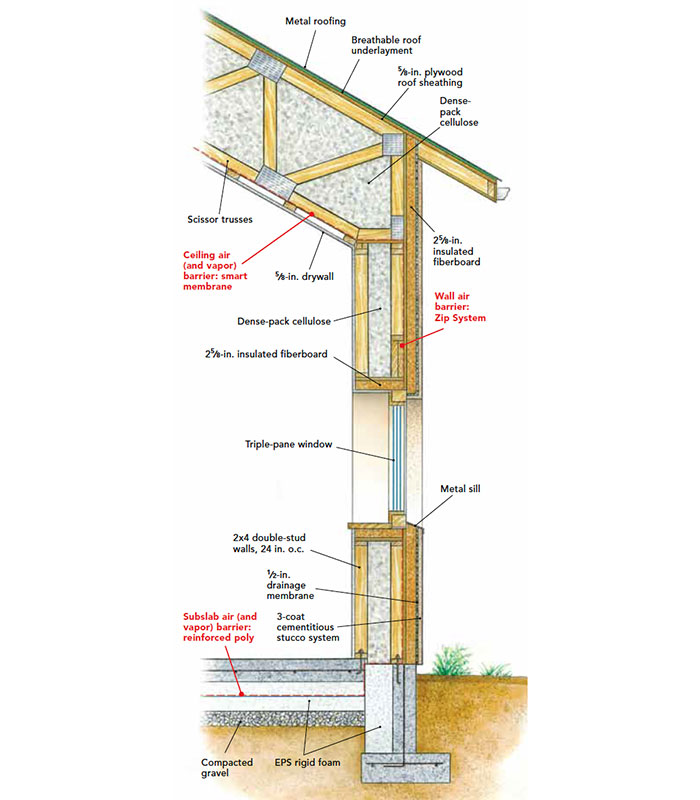
Envelope Specs
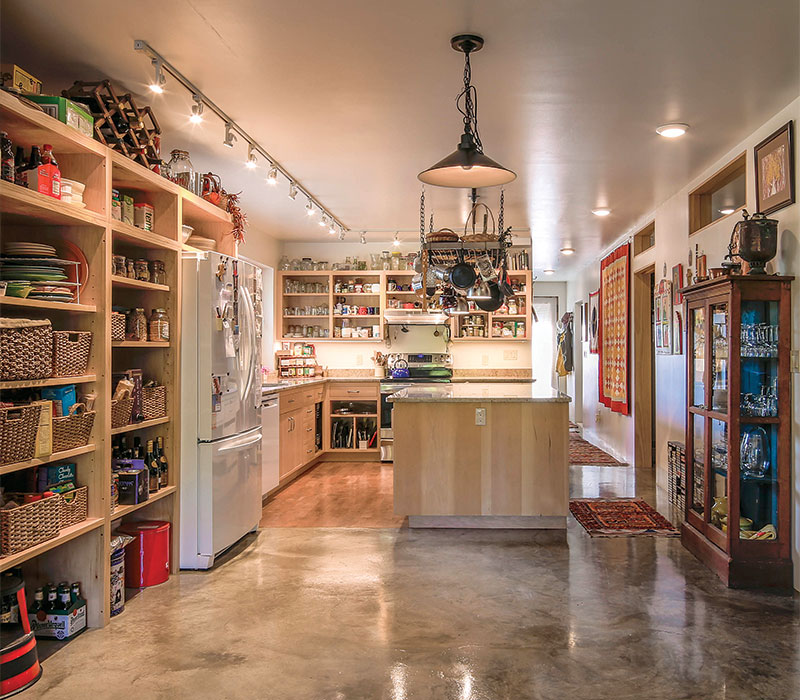
Slab R-30 2-lb. EPS foam
Walls R-56 dense-pack cellulose and fiberboard
Roof R-98 dense-pack cellulose
Air barrier Poly sheeting under slab; taped ZIP System sheathing on walls; Pro Clima Intello smart vapor-barrier ceiling
Windows Zola (U-0.123/R-8.1/SHGC 0.62)
Blower-door test results 0.43 ACH50
System Specs
Ventilation Zehnder 350 ERV
Heating Solar thermal in-floor hydronic radiant with electric boiler backup
Hot water Solar thermal with electric on-demand backup
Cooling Passive shading and night-sky cooling via ventilation system
Generation 2.5kw photovoltaic system (sized for future electric car)
Modeled Building Performance*
Heated sq. ft. 1,759
Average energy intensity 1.71 kBtu per sq. ft. per year
Average total energy use 3,015 kBtu per year
Average total energy generation 3.991 kBtu per year
*Actual energy use data is unavailable due to the project’s recent completion
—Andrew Michler is a Passive House consultant and the Social & Creative Instigator at NEEDBASED, Inc. He is the author of [ours] Hyperlocalization of Architecture.
Photos courtesy of NEEDBASED, Inc.
For more photos, drawings, and details, click the View PDF button below:
From Fine Homebuilding #266