Rammed Earth Construction
One of Ontario’s first insulated rammed earth home is a testament to the method’s attributes.
“It’s an interesting material—you might think it’s like concrete but it’s much more ductile.” —Terrell Wong
According to Sylvia Cook, principal of Aerecura Rammed Earth Builders, the rammed earth construction technique is several thousand years old and is thought to have originated independently in both China, where original rammed earth sections of the Great Wall are still standing, and the Iberian Peninsula. Examples dating to the 13th century are the Hakka Tulou—a series of five-story round apartment buildings in China—and the Alhambra Palace in Spain.
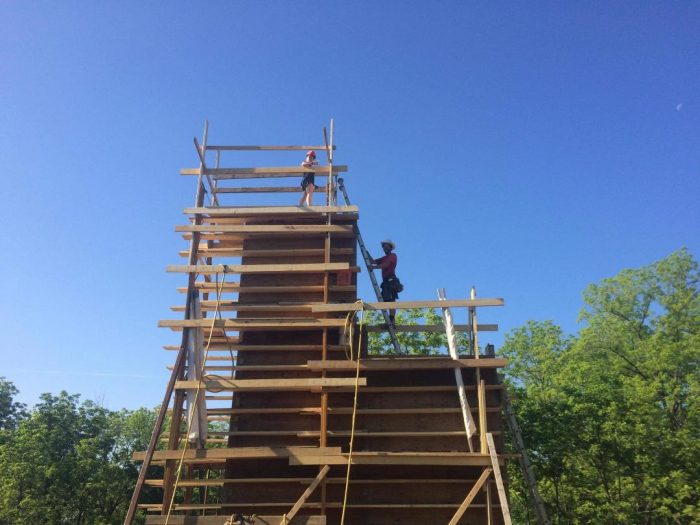
The technique has a lot to recommend it. The green building benefits include low embodied energy, recyclability, high thermal mass/low energy loads, and non-toxicity. For those reasons Terrell Wong, principal of Stone’s Throw Design Inc. in Ontario, Canada, is a fan of the material and the method. She also appreciates the durability and longevity of rammed earth houses. When describing rammed earth to her clients, Terrell says: “It is the structure, the insulation, the finish, and the thermal mass for a building. It will never need painting and it will last 500 years, if not more.”
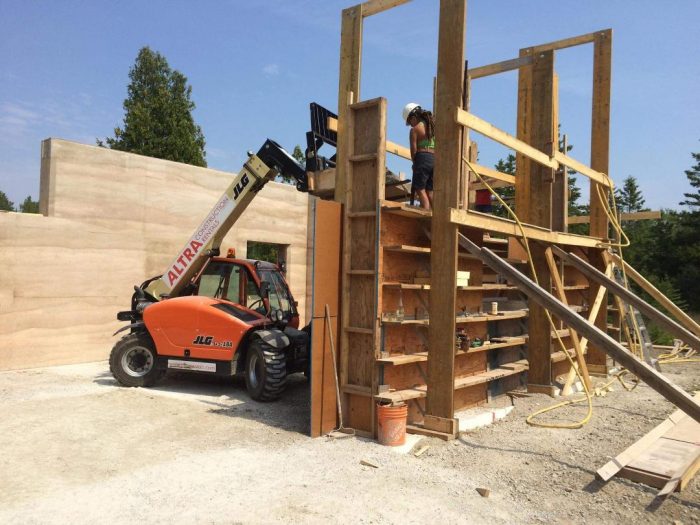
Rammed earth walls are built in panels of approximately 11.5 ft. in length with flexible joints. The material is a mix of 20% to 30% clay, sand, and 5% to 10% cement for strength and durability. In cold, wet climates, a silicate-based waterproofing agent is often added to the mix. A foot of material is layered into formwork and compressed down to 6 in. with a pneumatic tamper. The forms are about 20 in. wide and 4 ft. tall and are often built of Marine-grade plywood and 2×12 walers. When a wall has more than one panel, a recess is added to one end of the first panel, and the second panel is molded into that space, locking them together. Walls are rammed in place, and conduits for pipes and wires are added during the process. As with concrete pours, it’s important to know where conduit and windows are going because they can’t be moved once the wall is up. Typically, walls dry and are done in 24 hours, and they have a load-bearing capacity on par with concrete.
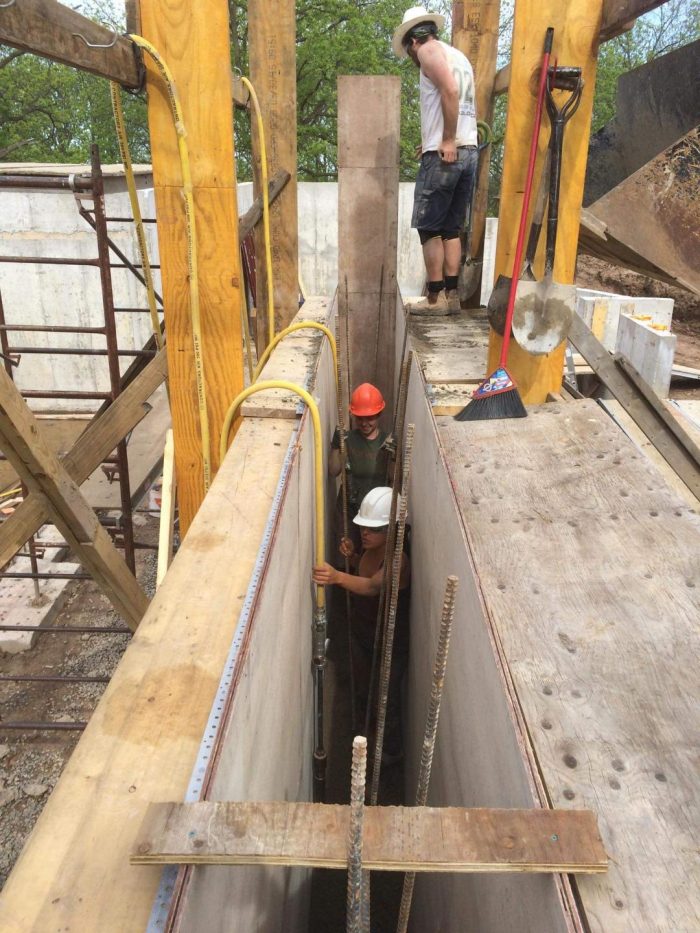
For the past 10 years, Terrell has designed three to four rammed earth houses per year. She says it’s still something of a fringe method in Canada and the States, noting that there are just two or three builders doing rammed earth construction in all of Ontario. Though often said to work best in arid climates, Sylvia makes this point: “The thermal mass effect works equally well for hot climates, where heat gain is delayed, and for cold climates, where heat loss gets shifted from the middle of the night to the middle of the day, when the sun makes up the difference. This keeps the temperature consistent year-round. Our belief is that it remains a ‘fringe method’ due to lack of knowledge of the system and the fact that it will work equally well in all climates.”
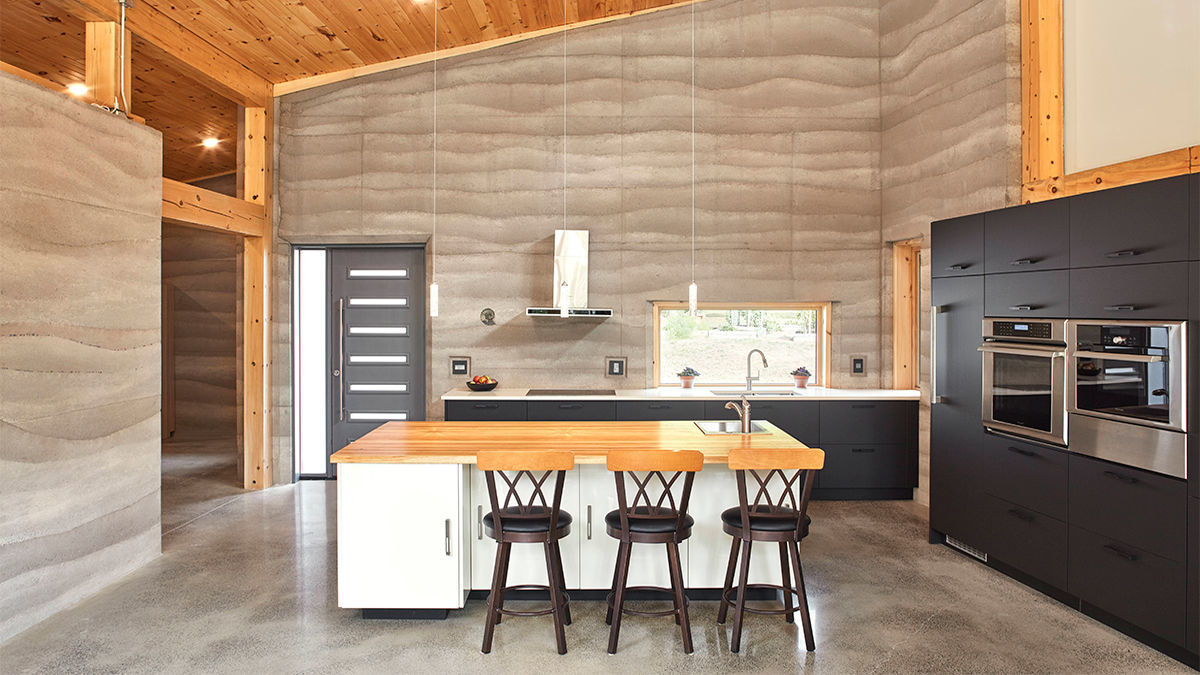
Of course, rammed earth walls are also notable for their earthy-toned striations. To get that look, pigment is added to the cement, which the ramming process moves to the edges of the board form so the colors are visible on the wall’s outermost layer. “You get this natural umbrage of color,” says Terrell. “And you can make those waves by exaggerating the up and down hills in the formwork.”
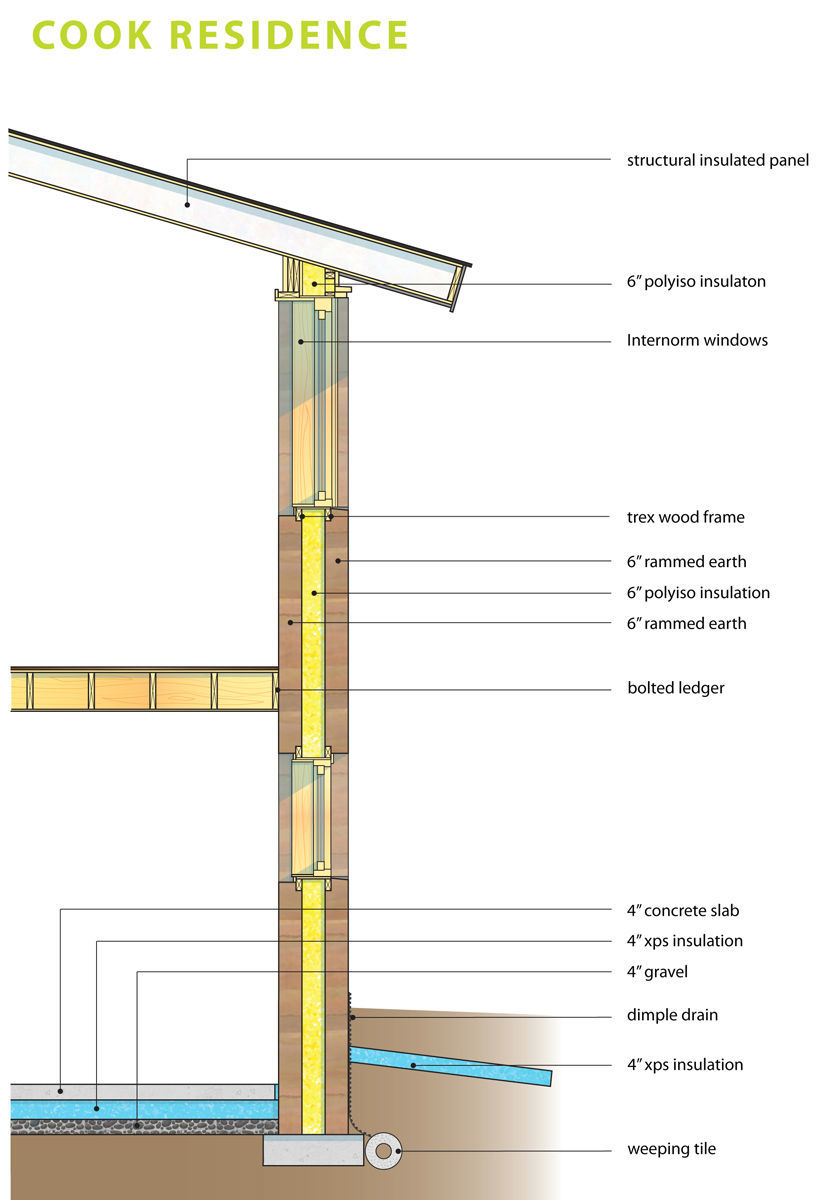
Though rammed earth construction has been modernized, North America has not yet adopted building codes for it. In Australia and New Zealand, where rammed earth houses are more common, codes have been formalized. In fact, research conducted in earthquake-prone New Zealand suggests that monolithic earth walls withstand earthquake conditions better than brick or block walls. “In Canada, we use an alternative solution that demonstrates rammed earth meets code requirements because it is much like concrete or concrete block,” Terrell explains, adding that in colder, wetter climates like Ontario’s, fiberglass rebar is needed to stabilize structures. She also integrates recycled polyiso insulation into the middle of rammed earth walls to minimize thermal bridging.
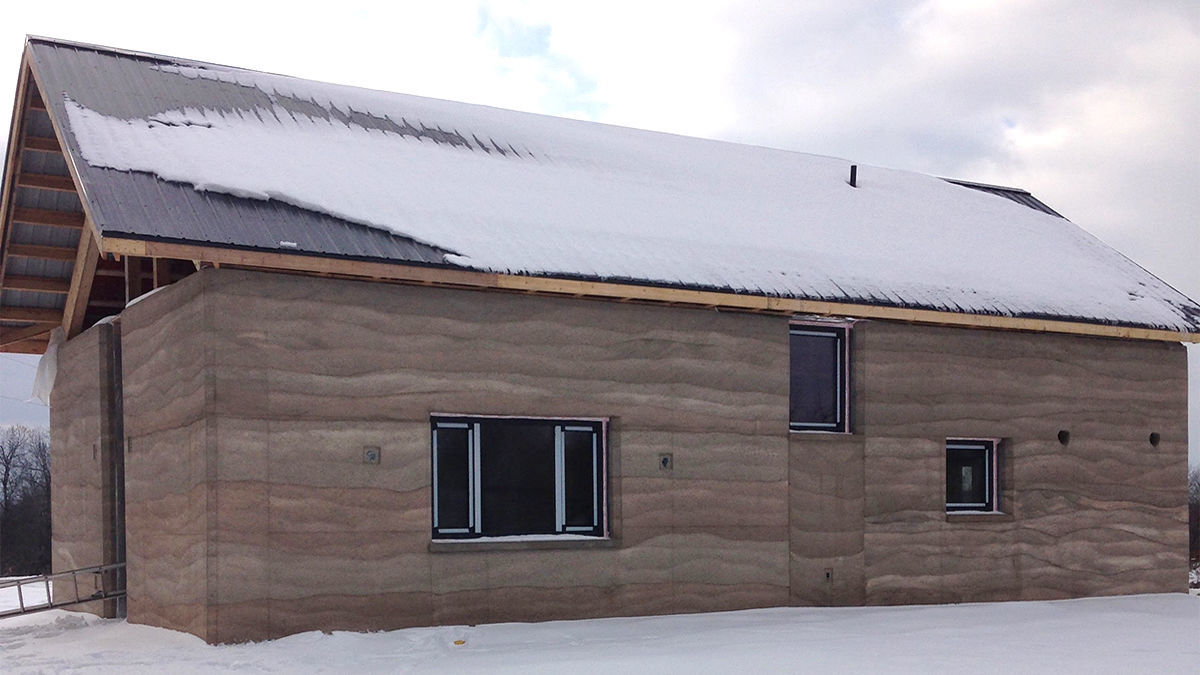
Predictably, the complexity of a project influences cost—curved or angled walls are going to be more expensive than their conventional counterparts because the rammed earth method is labor-intensive. But by keeping the design and formwork simple, Terrell was able to use the method for an affordable housing project (above) spec’d for Passive House standards.
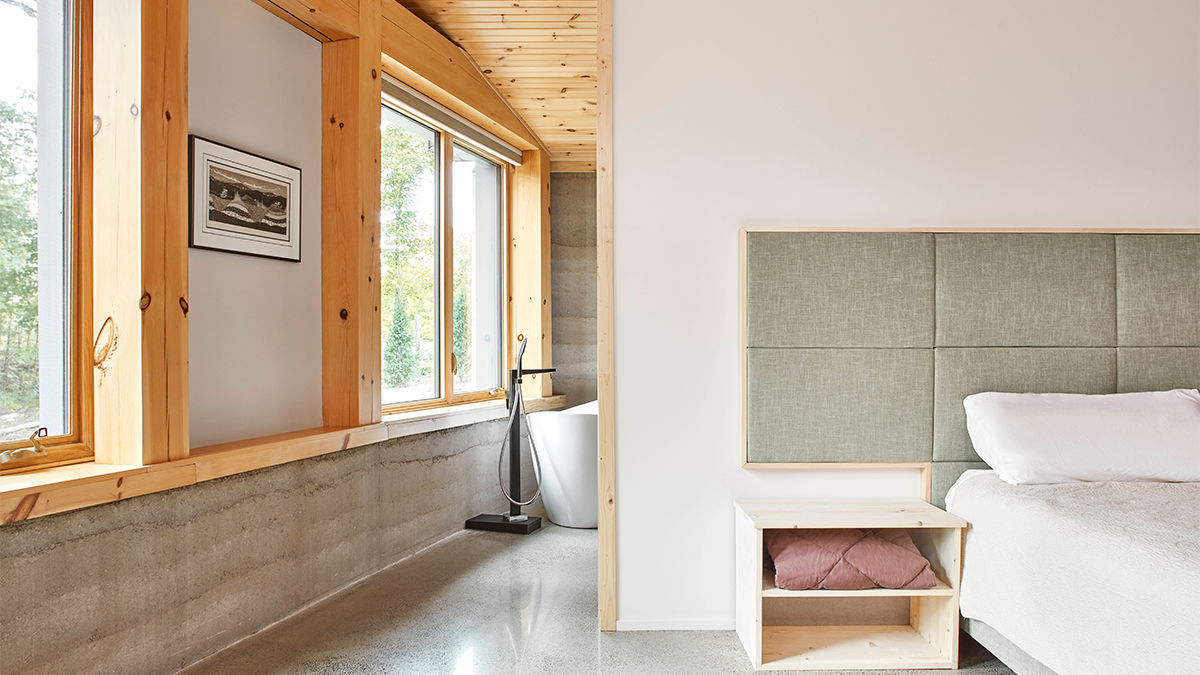
Many rammed earth homes are hybrids. They can be a combination of stick- or timer-frame walls, particularly for interior partitions though Terrell regularly uses cabinetry to divide spaces. Some have insulated framed external walls with rammed earth internal walls. Terrell likes the combination of rammed earth on the bottom floor and a straw-bale upper floor; she has also seen CLT-panel roof versions.
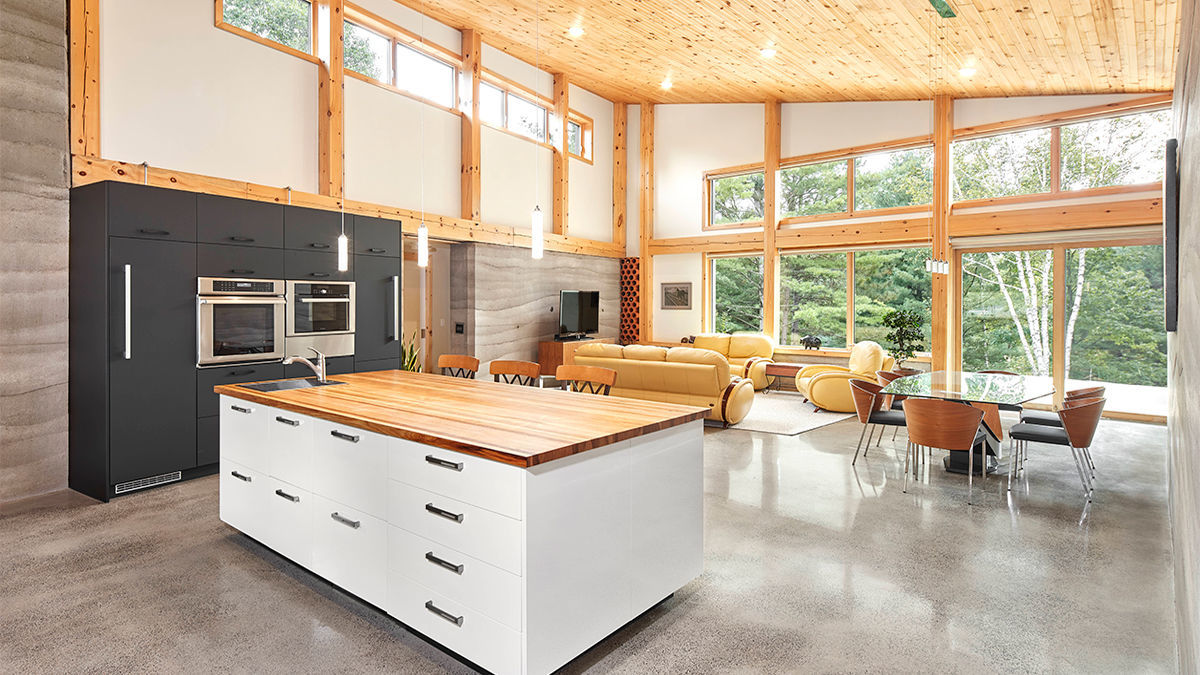
For the project featured here, Terrell was charged with designing a single-family home in a small rural subdivision surrounded by woodlands. Using Passive House strategies, she worked with Aerecura to reduce energy use by: maximizing the thermal mass potential of rammed earth, harvesting southern light and cross breezes (the rammed earth walls enhance the passive ventilation), and adding windows and overhangs where appropriate. The result is a home whose natural cooling capacity omits the need for mechanical equipment. For heat, the house uses roughly 20kW/h/m2 annually.
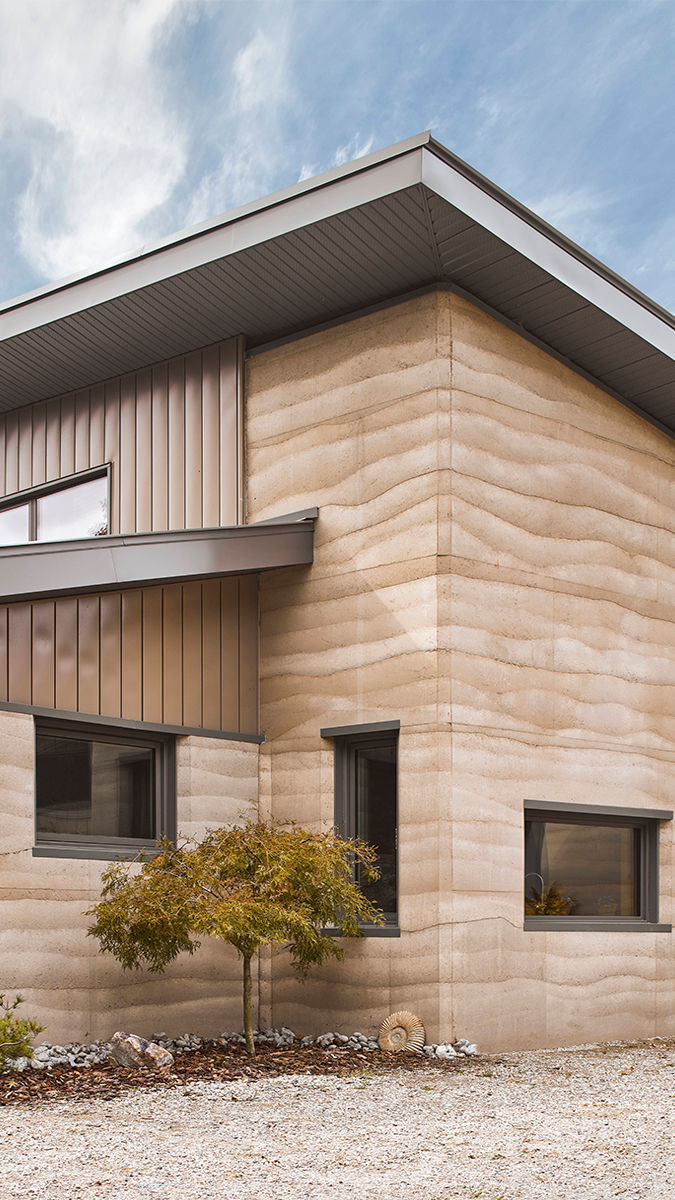
The exterior walls comprise 530 tons of thermal mass in the form of two 6-in. wythes of rammed earth around 6 in. of insulation. Because 90% of the unprocessed material came from a nearby gravel pit, the embodied energy of this house is exceptionally low. Recycling efforts included repurposing some of the formwork on the interior, and the main stair is salvaged wood from a local roundhouse.
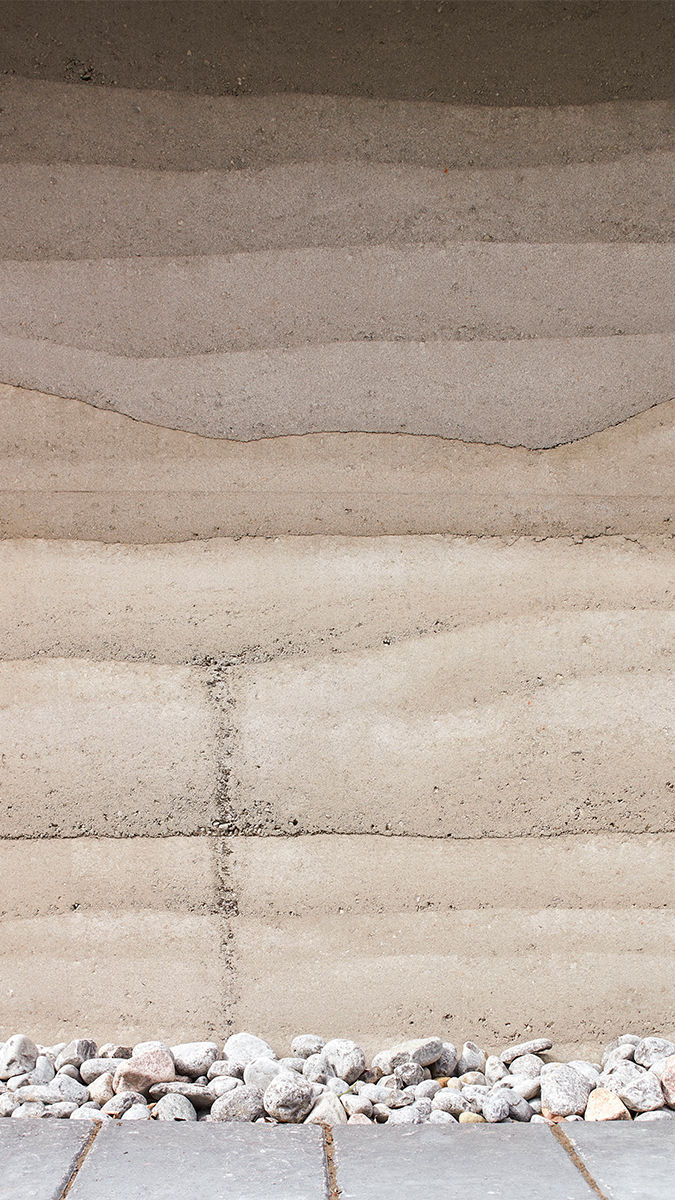
Photos by Riley Snelling, courtesy of Stone’s Throw Design, except where noted
For more houses built from alternative materials:
Fine Homebuilding Recommended Products
Fine Homebuilding receives a commission for items purchased through links on this site, including Amazon Associates and other affiliate advertising programs.
Get Your House Right: Architectural Elements to Use & Avoid
Homebody: A Guide to Creating Spaces You Never Want to Leave
Not So Big House
View Comments
fascinating
Dents the the aluminum siding already?
This architect doesn't have a clue what she is doing. 530 tons of thermal mass. That's OK if one never changes the thermostat. Otherwise it takes forever (and a vast amount of energy) to heat up or cool down.
This is much the same insulating principle as the ICF, with even worse lag times and energy consumed. 530 tons of mass, with half of it on the interior. That means that every time that you turn the thermostat back up, for some reason, you're heating up 265 tons of rammed earth. What a waste of energy!!
I've experienced this problem first hand in a friend's recreational house (3 hours north of Toronto, Ontario), built with ICFs. After arriving Friday night in the middle of winter, the house is still cold on Saturday night. Yes, by Sunday when you're ready to go home, it was nice and comfortable. You say, "Put in a larger furnace". Oh yeah, that makes sense (besides the fact that over-sized furnaces are inefficient).
You say, "Get an Internet thermostat so that you can begin heating it up a day in advance" First, let's not use technology, even if it is available in a rural location, to overcome a fundamentally flawed building technique. Secondly, it doesn't address the enormous waste of energy required to heat 265 tons of mass.
Is one supposed to turn the thermostat down a day before leaving and just accept the fact that you'll gradually get colder and colder until you finally leave? Modern homes are supposed to be comfortable.
I was a Professional Engineer before retiring and know what I'm talking about. These high mass structures/building methods are only suitable in temperate climates with very moderate temperature swings (west coast) or continental climates (hot in the day and cold at night). Hopefully, I've helped prevent someone from making a grave mistake.
I think the key words there are "recreational house". Thermal mass makes little sense for a building used that way, but it makes a great deal of sense when it's a main residence, as this project seems to be. Just set the thermostat at 72F year round and you're good to go.