An Introduction to Insulated Concrete Forms
Get an overview of what ICFs are, how they create energy-efficient foundation walls, and how to incorporate them into your next project.
ABOUT ICF WALLS
ICF homes are tight, strong, and quiet—One way to insulate a poured concrete wall is with permanent forms made of insulation. Insulating concrete forms (ICFs) are panels or hollow blocks that are stacked, braced, and then filled with concrete. They are most commonly solid pieces of rigid foam, but some are composites of cement and other insulating materials.
ICF walls should be seriously considered for any home built in a region subject to regular hurricanes.
Proponents of ICF walls tout at least two energy benefits: low rates of air leakage; and a thermal mass benefit. In many climates, an ICF wall provides no thermal mass benefit. Whether an ICF wall saves energy depends upon what the wall is being compared to.
Most homes with ICF walls have lower levels of air leakage than typical wood-framed homes. However, wood-frame homes can be made very airtight.
MORE ABOUT ICF WALLS
ICFs have a relatively low R-value—Concrete has virtually no insulating value — just R-0.08 per inch. According to tests conducted by Oak Ridge National Laboratory (ORNL), the clear wall R-value for ICF walls is about 12, less than many builders assume. Some types of ICFs that have thicker-than-average foam may have higher R-values.
The R-value of an ICF wall depends upon the details of the ICF blocks and can be the same as or less than the added R-value of the two foam walls, depending on the configuration of the concrete.
Some designers who specify ICFs beef up the performance of the walls by gluing additional rigid foam to the exterior. For example, architect Rachel Wagner specified an ICF foundation for a low-energy-use home in Duluth, Minn. Dissatisfied with the ICF R-value of 25, she specified the installation of an additional 4 inches of extruded polystyrene on the exterior of the ICF walls to raise their R-value to 45.
The benefit of thermal mass depends on climate
ORNL research has found that ICF houses use less energy than the typical wood-framed home. But the thermal mass benefits of ICF houses depend on location: Houses in Minneapolis and Chicago showed the least savings from the thermal mass effect, while those in Phoenix and in Bakersfield, Calif., had the most. In all cases, potential whole-house energy savings were 10% or less when the R-value of the wall was 25.
Canadian researchers who closely monitored the performance of a multiunit residential building with ICF walls reported, “The overall building is relatively airtight, due in large part to the continuity of the ICF wall assembly, as no extraordinary air leakage control measures were undertaken at the roof and foundation levels.” One of the researchers, Duncan Hill, commented, “The concrete is a poured-in-place air barrier.” However, the researchers concluded that an ICF wall offers no thermal mass benefits in Canada.
According to two articles in Environmental Building News (“Thermal Mass and R-value” and “Thermal Mass”), high mass can enhance energy performance, but only when outdoor temperatures cycle above and below the indoor temperature in a 24-hour period. In parts of the country where outside temperatures remain well below the indoor set temperature for weeks at a time, the mass effect isn’t really a factor.
Bird’s-Eye View
Stay-in-place foam forms are well insulated, airtight, and strong—Most brands of insulated concrete forms (ICFs) consist of two parallel panels of foam held apart by rigid plastic spacers. Builders stack ICFs like Lego blocks, brace the forms, and fill the forms with concrete delivered by a pumper truck. The ICFs are left in place as a permanent part of the building.
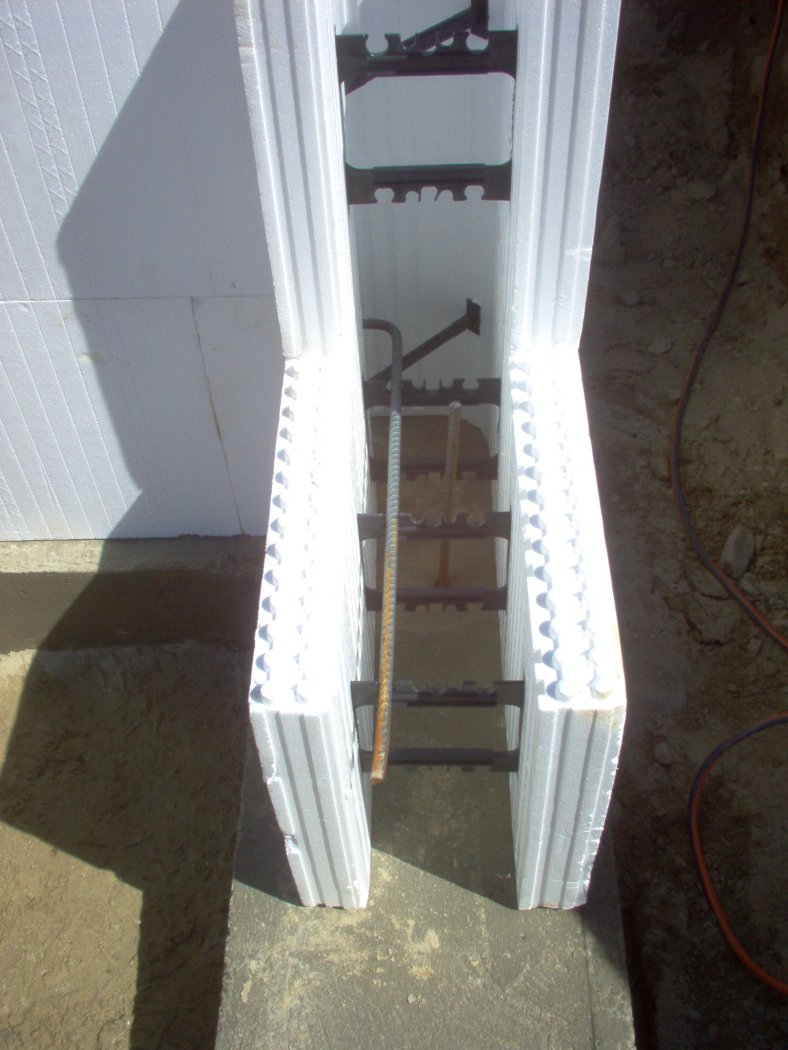
ICFs are becoming increasingly common. Among their advantages over conventional wood-frame construction are low air infiltration, high thermal mass, high strength and fire resistance, good sound-deadening qualities, and much higher insulating values than standard masonry construction. They can be used to form basement walls alone or for an entire wall system, including above-grade walls. According to the Portland Cement Association, using ICFs adds about 3% to overall construction costs compared with a conventional wood-frame building.
Types of ICFs
A variety of shapes and sizes—Most ICFs are made from expanded polystyrene (EPS), although some manufacturers used different types of foam.
A common type of ICF is a hollow block with 2-inch-thick foam on each side, typically 16 inches high and 48 inches long. Concrete thickness can vary, depending on the application, from 4 inches to 12 inches. ICFs also are available as planks, usually 1x8s, and panels as large as 4x8s.
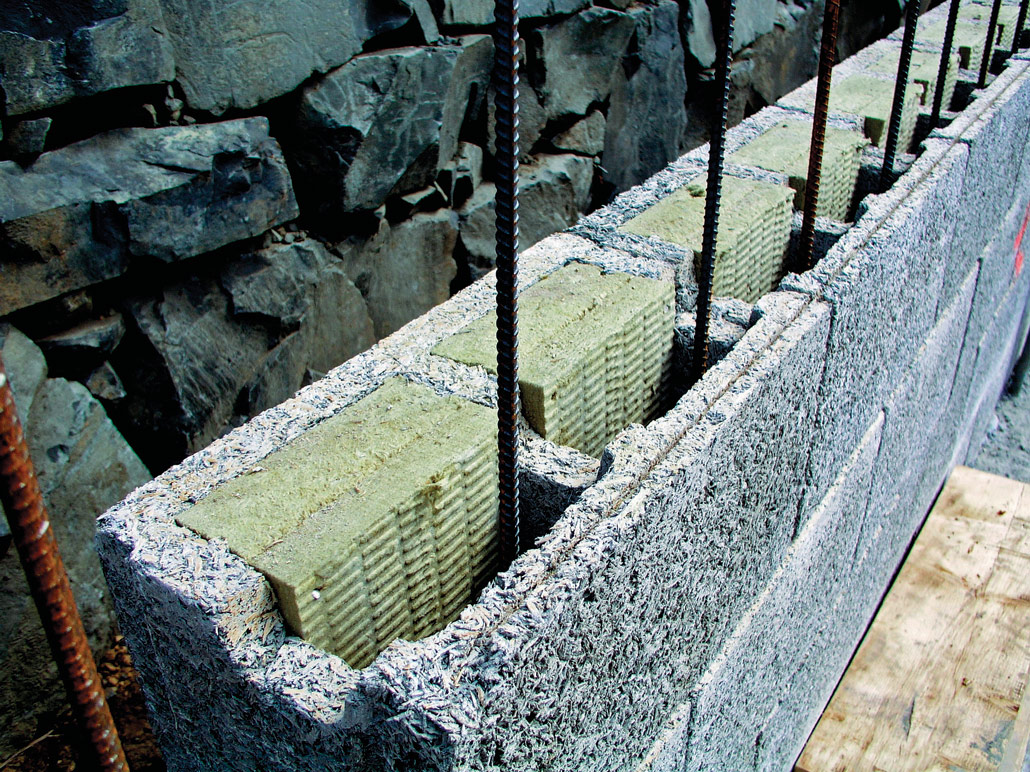
Image Credit: Nathan Good
Internally, ICFs can form concrete in one of several ways: as a flat wall, as a grid, or in a post-and-beam pattern.
Design Notes
Good ICFs are adaptable and easy to erect—Besides being a system that goes together quickly and easily, ICFs give designers more flexibility than conventional concrete forms. Most ICF systems can be manipulated into curves and angles that require only minor on-site trimming and bending. Many form manufacturers will even create custom blocks or panels to execute your designs with no modifications, saving time and reducing construction waste.
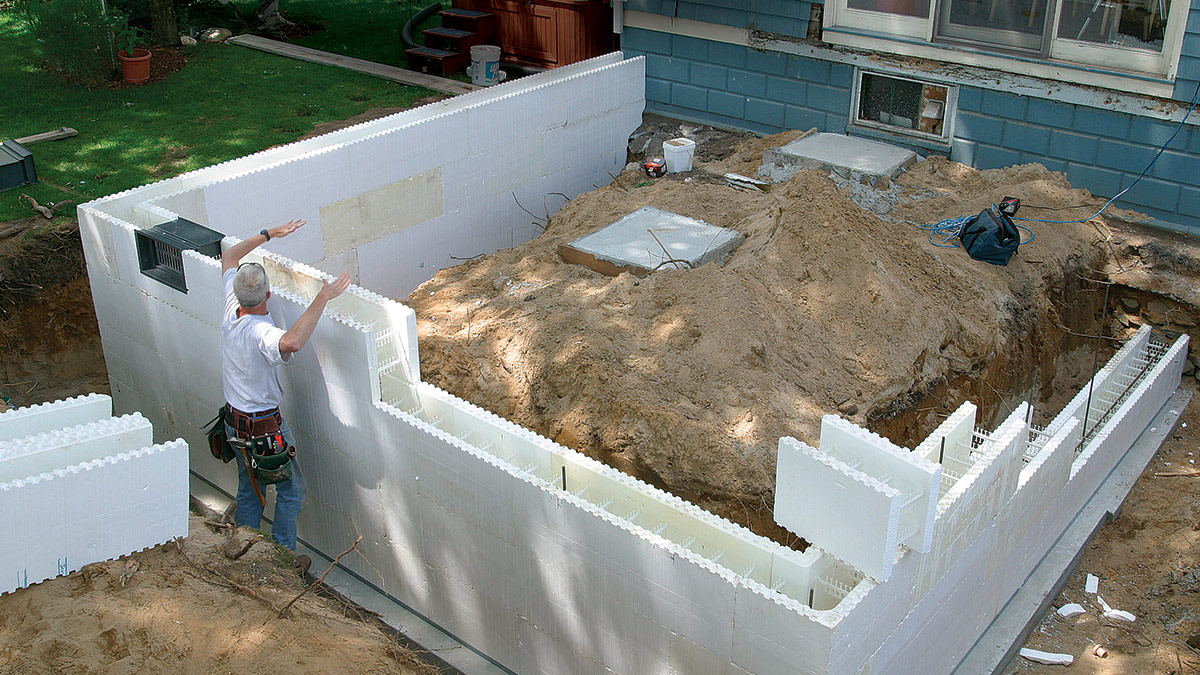
Builder Tips
ICF assembly is easy if you know what you’re doing—In practice, it’s relatively simple to stack ICFs into walls, although bracing and leveling before the pour are critical. Each system goes together a little differently, so the manufacturer’s instructions are a must-read before you start. Just like bricks or concrete masonry units, the first course sets the tone for the rest of the installation, so extra attention at the beginning will pay off. Cuts in the forms can make the concrete pour more shaky; avoid cutting corner blocks, use plenty of bracing, and secure large joints with scabs of plywood.
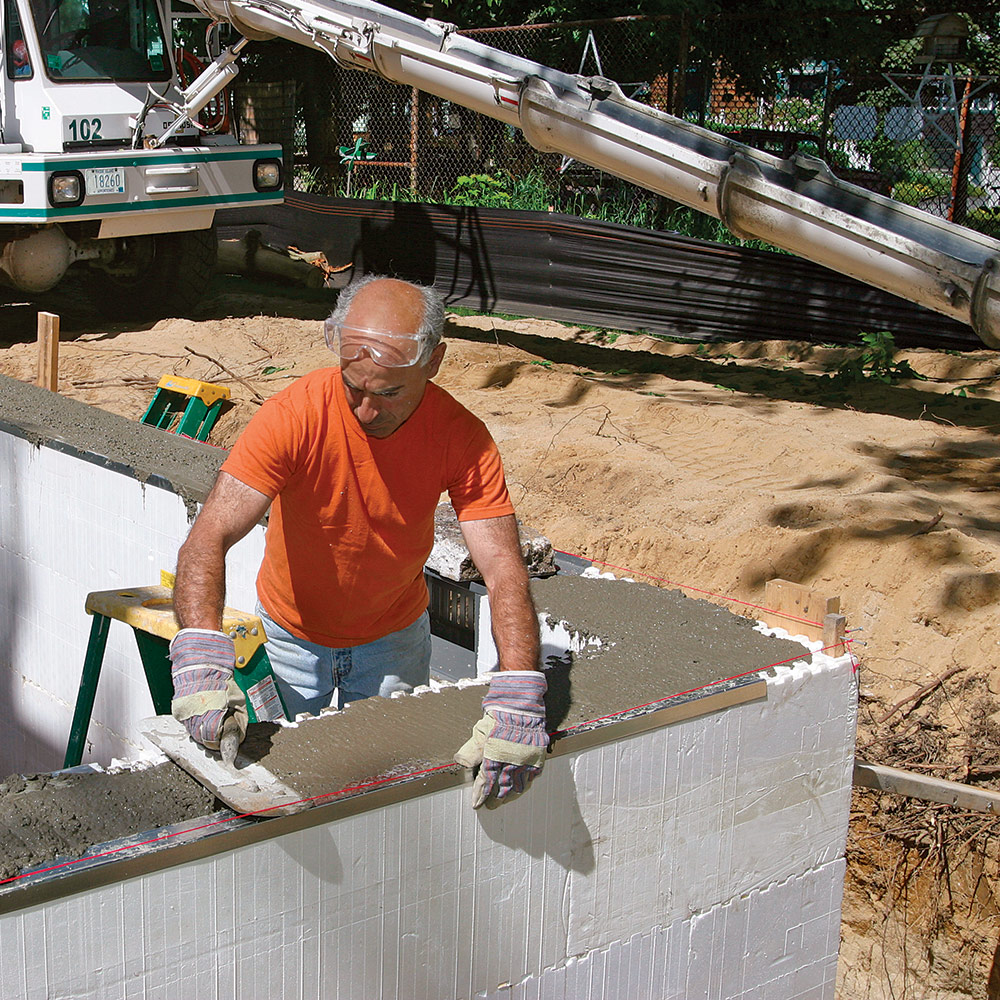
How do I attach an ICF wall to the rest of the house?
Steel channels secure the forms to a poured concrete footing; anchor bolts penetrate the top of the concrete as in a typical poured wall. Window and door openings that are framed with dimensional lumber go in before the concrete is poured. It may not always be necessary, but using spray foam to seal the forms to existing foundation walls will probably keep the pour a little neater.
The Code
Requirements for Insulating Concrete Form (ICF) wall construction can be found in Section 611 of the IRC. Almost 30 pages in length, Section 611 includes numerous detail drawings and tables that help explain the code-approved use of ICFs.
If the building’s design follows the prescriptive guidelines outlined in the code book, plans don’t require the seal of an engineer or architect. Reinforcement specifications can be found in Tables 611.3 through 611.7. Standard floor and roof connection details are identified in Figure 611.7(1). Window and door opening details can be found Figure 611.7(2).
Plates that connect roof framing to ICF walls must be secured with 1/2-inch anchor bolts embedded a minimum of 7 in. and placed a maximum of 6 ft. on-center (611.9).
OTHER CONSIDERATIONS
Rastra is one familiar brand of cement-composite ICF. Blocks consist of 85% recycled polystyrene and cement and are available in several thicknesses. The blocks used on this project in Montana were made by Ener-Grid (which is now defunct) and are similar to Rastra block. Each one measured 10 inches deep, 15 inches tall, and 10 feet long and weighed about 160 pounds. The material is fairly soft, so the blocks are easy to shape and cut. Blocks are stacked into walls, reinforced with steel, and filled with concrete. A concrete pump is a big help for tall-wall pours.
R-values are something of a moving target. The “steady state” R-value of a 10-inch-thick wall is between 7.7 and 8.2, according to ORNL tests. Rastra, however, claims higher R-values because of the thermal mass benefit. This is the same as the mass effect that affects the thermal performance of more typical ICF walls. Thermal mass benefit, if any, varies according to climate.
ICF blocks also can be made with a mixture of cement and recycled wood chips, such as those made by Durisol. R-values range from about 8 for an 8-inch-thick wall to R-20 for a 12-inch block with an insert of mineral wool insulation. One unique characteristic of wood-chip ICFs is that they are able to absorb large amounts of moisture without damage. The blocks can be cut with carbide-tipped tools, and some interior and exterior finishes can be applied directly to the surface.
GREEN POINTS
Wall system influences thermal performance, potentially affecting 3 to 5 points in EA1 (Energy & Atmosphere), EA2, and/or EA3. ICFs are not considered environmentally preferable materials in MR2.2 (Materials & Resources).
Under Chapter 7, “Energy Efficiency”: ICFs can contribute to points for superior energy efficiency under either the prescriptive path (703) or the performance path (702). Under Chapter 6, Resource Efficiency: up to 4 points for recycled content (fly ash or slag substitution for portland cement in concrete) (604.1).
Originally published on GreenBuilding Advisor.com.