Podcast 210: Sealing Can Lights, Protecting Foundation Foam, and Fixing Bouncy Floors
The crew tackles questions about rigid insulation for foundations and strengthening an over-spanned kitchen floor, plus Patrick shares his idea of the perfect deck, which is also a boat.
Follow the Fine Homebuilding Podcast on your favorite app. Subscribe now and don’t miss an episode:
![]() |
![]() |
![]() |
![]() |
Matt, Rob, and Patrick hear from listeners on HVAC zoning and protecting cold-sensitive materials in an unconditioned shop. Dan asks how to air seal the ceiling penetrations when he removes his old can lights. Jeff is looking for the best way to cover up the foam he’s installed on the outside of his foundation walls. Ben asks about strengthening his bouncy floor. Matthew, who’s a certified welding inspector asks who’s making sure that residential project with steel are welded correctly.
Listener Feedback:
Listener feedback #1
Mike from RI writes, Greetings Podcast Hosts, I anxiously await for the automatic Friday morning download of the FHB Podcast and listen to it as soon as possible just waiting for any egregious error one of you may make so I can send in a correction. For the past year or more I’ve been disappointed. You’ve given no misguided advice to listeners to write in about.
So I’m writing just to add a little to your discussion of HVAC zoning and comfort – a topic prompted by a listener question on Podcast 207.
I use frequently install single zone air-delivered heating and AC in homes I build and those I rehab for rentals. Using my own 3 story house as an example – the temperature difference between the top floor and bottom floor and room-to-room varies by only 2 to 3 degrees F at the most. Periodic monitoring in my 6 rental houses (a mix of 1, 2 and 3 level homes) shows similar temperature uniformity. I attribute this to two things: energy efficiency and central return HVAC ducting .
Air tightness makes a tremendous difference in comfort. In a tight home there is little stack effect. Without warm air leaking out of the top of a house there is no cold air leaking in on lower levels so the temperature stratification is minimal. Well insulated exterior walls and ceilings reduce the rate of heat flow so the temperature of the wall and ceiling surfaces is similar to the interior air temperature. This means your body doesn’t lose heat to a cold wall or ceiling in winter or vice versa in summer – so you feel more comfortable.
And though central return systems are considered inferior to fully ducted return systems they can help circulate conditioned air more evenly throughout a house if planned out well. By using either generous door undercuts or other return air pathways like passive wall ducts with high/low grills on opposite sides of the wall, ‘jump ducts’ through the ceiling, or devices like Tamarack Technologies RAP (return air pathway) grills – air is more fully circulated throughout the house leading to more-even temperature.
Another thing that can help keep the temperature even throughout a home is a continuous ventilation system like an ERV or HRV. This equipment gently circulates fresh air through the house and in doing so can help balance out temperature variations.
Comfort in a home is very complex. Air temperature, air movement, humidity, air quality, and mean radiant temperature of the exterior walls and windows all play a part and have to be considered holistically when designing and building a house. Comfort isn’t solely the realm of HVAC.
Listener feedback #2
Phillip from Columbia, MD writes, Hi FHB pod-guys and Kiley, On a recent home remodeling project and addition on a 1970s split-foyer the homeowner had complained that the HVAC would make it cold on one half of the house and hot on the other in winter and the opposite in the summer. The ducting was all original and but the HVAC unit had been upgraded within the last 5 years or so. As part of our contract we installed a two zone mini split for the 2-story addition. One zone for the living room upstairs and a second for the bedroom down stairs.
What we also ended up doing was having the HVAC company that installed the mini-split system was do what he called a “rebalancing” the existing system. This included testing the air-flow at each supply vent and assessing the duct sizing throughout the house. They determined that one side of the houses duct work was over-sized and the other end of the house was drastically undersized. That coupled with the fact that the basement level was half underground complicated the matter. The home was also poorly insulated and had air leaks galore, but that is very typical of the homes that were mass produced here in Columbia, Maryland in the 70s-80s.
The fix was to add a diverter in the top of the plenum, which directed more of the air to one side of the house. They also restricted a few of the oversized ducts and also installed more free-flowing vent covers replacing the plastic ones she had bought from Depot. All for the balancing work for the reasonable price fo $450. After the work they re-tested the air-for at each vent assuring they were all equal.
The homeowner raved about the very noticeable difference and said it was some of the best money she ever spent.
The only caveat I have was that all the work was done by my longtime and trusted HVAC guy who retired almost immediately after work was complete. He was a surly and knowledgable old-timer who is greatly missed as I have swung and struck out on everyone else I’ve tried since.
Keep up the good work!
Related links:
Listener feedback #3
Jon writes, Hello, The part of your podcast talking about unheated shops and storing temperature sensitive things like paints and stains, epoxies, etc, has a reasonably easy solution, one that I have used, but I can’t take credit for. I read this many years ago on a boat builders forum for storing the epoxies that are used so often.
An old refrigerator can be picked up for free from almost anywhere. It doesn’t need to work (if it does, you don’t need to plug it in). It is a nice size, insulated, already has shelves, and is mostly airtight. Since it is insulated and airtight you just drop in a small incandescent light bulb in cold weather to keep it warm inside. Your supplies will be kept organized and at a nice temperature, and the cost is really only what it takes to run a 60 watt light bulb.
Hope this is helpful, and I am sincerely interested in hearing about all of reasons this is a bad idea.
Related links:
- A Rust-free Winterized Woodshop (from FineWoodworking.com)
Question 1: How can I safely air-seal and insulate over recessed lights?
Dan from West Chester, PA writes, Hi, Patrick, Kylie, Rob, and Jeff, First, I love the podcast. Even though I’m not a builder or anywhere in the trades, I get a lot out of it and enjoy the banter immensely.
Real question: When we bought our mid-70’s Split Level, there were no ceiling lights and we had several installed across the bedrooms, hallway, and kitchen. This was before I learned about energy penalties. (Unrelated, I also cut a hole in my roof for an attic exhaust fan, but oh well you can’t stop stupid sometimes.)
I’d like to replace the recessed can lights with the slimline ones, but am wondering if you have any best practices for how to cover them after the fact. Solid foam on top or would loose fill be sufficient? Any suggestions are appreciated to have the best positive impact from the change.
Thanks very much, and keep the podcast going. Oh and go Bucs!
![]() |
![]() |
Related links:
Question 2: What’s the best way to finish above-grade rigid foam insulation?
Jeff from Henderson, KY writes, Hello FHB podcast! I hope that you are well and having a good day!
I have a question on what to use for a covering of external insulation on a block stem wall.
I have a 1902 farm house remodel that I am insulating from the exterior. I was even going to insulate the block foundation wall, with EPS or Xps foam because of ground contact. I currently have 4 “ of Polyiso on the exterior wood wall and stopped the insulation at the top of the concrete block wall. Below this Poly ISO foam I had planned on using 2” of xps but I do not know what to cover this with to make it presentable, because I am not a fan of the look of blue or pink foam as my exterior finish. I have looked on GBA wall details, and the detail just points to using metal. So, what type of metal, Just used 24” flashing metal?? There has got to be a nice-looking covering to put on this foam for it not to look so cheaply done beside putting a layer of concrete or masonry, just to cover the foam. Any suggestions would be appreciated. Thanks!
![]() |
![]() |
![]() |
![]() |
![]() |
![]() |
![]() |
![]() |
Related links:
- How to Finish Exterior Foundation Insulation
- Glavel
- Foamglas Insulation Exits U.S. Residential Market
Question 3: How can I stop my floor framing from flexing?
Ben writes, Hi, I’m a general contractor/carpenter in the Minneapolis area and look forward to hearing the podcast each week. It has been very helpful to hear from others around the country and what projects they are taking on.
Over the past 5 years we have been renovating our home, a 1920s farm house. We are finally getting close to finishing and that last project is the basement. Before drywall goes up on the ceiling, I have been struggling with how to achieve a strong floor system above. The main level has 2×8 Douglas fir joists (at 16” o.c.) spanning around 13ft. There is a lot of sag and deflection and so I have sistered on 7 1/2” LVLs to each joist with adhesive and lag screws, as well as adding cross blocking in between joists to help stiffen it up. Even with those measures, it’s still deflects a lot. I am guessing that the diagonal 1x subfloor is probably a weak link in tying the floor system together, and I will at some point remove the original hardwood flooring and install plywood subfloor, along with leveling it. Just curious if there are any thoughts or recommendations of more ways to address the issue from below? I’ve considered some type of center support, but the ceiling height is barely 7ft as is, and I also don’t plan to do any partition walls down there, since it’s just one open room.
Hopefully that’s enough information. Appreciate any feedback on the situation. Thank you!
Related links:
Question 4: Who inspects the quality of work when heavy steel is installed in residential framing?
Matthew writes, Hi, All, The recent talk about Patrick’s oxy/fuel bottles and his trip to the welding store, has sparked a question! I am a Certified Welding Inspector and work on various commercial building projects yet no home building projects, the closest would be certifying a company for the welding of extensions onto metal screws in helical piles. My question is, when welded structural steel is used for construction is this work done by a certified welder or someone that has a welder and knows how to burn rod? Are the architects/engineers that call out the use of metal members calculating out the shear strength of welds and inspecting them to a code or just having the welder place a weld of an undetermined size and checking to see if metal is melted? If welding codes are called out, are they normally AWS, ICC, or some other governing body? Any insight would be greatly appreciated. Keep up the great work as I enjoy learning new things every podcast as an aspiring DIYer. Thanks!
Related Links:
Question 5: Is there anything inherently wrong about a really big house?
Editors ask you! Matt explains the conversation we had with Justin yesterday and we ask for feedback from listeners for a later podcast conversation with Kiley.
Related Links:
And finally…
The Perfect Deck:
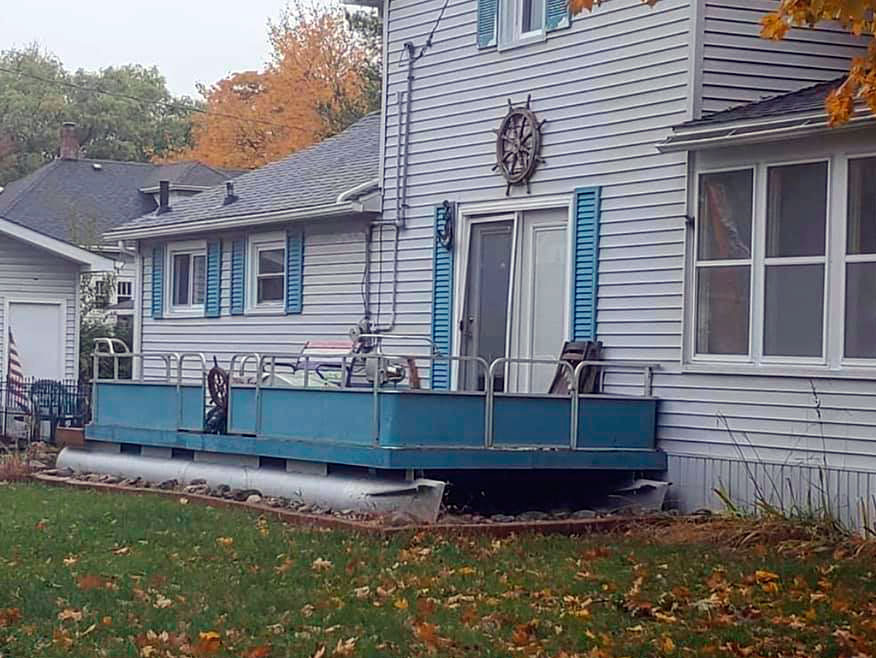
If you have any questions you would like us to dig into for a future show, shoot an email our way: [email protected].
If we use your question we’ll send you a FHB Podcast sticker!
#KeepCraftAlive
KeepCraftAlive hats help celebrate the value of true craftsmanship–plus 50% of all proceeds from every hat sold go to the #KeepCraftAlive Scholarship Fund, supported by Fine Homebuilding and SkillsUSA.
Buy a #KeepCraftAlive hat or t-shirt
This episode of the podcast is brought to you by Danner
We’d like to thank Danner, who sponsors this podcast because they believe in us. They believe in quality, and craftsmanship…but more than anything, they believe in the power of following your own path.
For more than 80 years Danner has made boots for those who have a trail to blaze. Boots like the Bull Run. Hand built in the USA with durable, full-grain leather uppers, and stitch-down construction for strength and stability. The Bull Run is built in a timeless design for both men and women with unmatched quality and durability that stands the test of time. The Bull Run boot by Danner offers iconic style and legendary craftsmanship for those who earn their independence.
You can find yours at Danner.com.
Fine Homebuilding podcast listeners can now get 20% off anything in the Taunton store, including the Code Check series. These sturdy, spiral bound reference books will help you navigate the International Residential Code, The National Electric Code and the Universal Plumbing Code. Use the discount code FHBPODCAST to take advantage of this special offer.
We hope you will take advantage of a great offer for our podcast listeners: A special 20% off the discounted rate to subscribe to the Fine Homebuilding print magazine. That link goes to finehomebuilding.com/podoffer.
The show is driven by our listeners, so please subscribe and rate us on iTunes or Google Play, and if you have any questions you would like us to dig into for a future show, shoot an email our way: [email protected]. Also, be sure to follow Justin Fink and Fine Homebuilding on Instagram, and “like” the magazine on Facebook. Note that you can watch the show above, or on YouTube at the Fine Homebuilding YouTube Channel.
The Fine Homebuilding Podcast embodies Fine Homebuilding magazine’s commitment to the preservation of craftsmanship and the advancement of home performance in residential construction. The show is an informal but vigorous conversation about the techniques and principles that allow listeners to master their design and building challenges.
Other related links
-
- All FHB podcast show notes: FineHomebuilding.com/podcast.
- #KeepCraftAlive T-shirts and hats support scholarships for building trades students. So order some gear at KeepCraftAlive.org.
- The direct link to the online store is here.
View Comments
Regarding welded steel connections in residential light construction - our firm will do our own details for accessory items like awnings or porches and we generally go for the 'overkill' method you mentioned.
For a structural steel beam with welded connections we do defer to an engineer.
However, in either case we add the following note as required by our area jurisdictions:
NOTE: STEEL ASSEMBLIES TO BE FABRICATED BY WABO CERTIFIED FABRICATOR OR FIELD INSPECTED BY A SPECIAL INSPECTOR.
This is in Washington state where, as the note implies, the certified welder is usually the route to go to not have to do costly special inspections.
https://www.wabo.org/welder-program
Jeff
Seattle, WA
I've drawn three 9,000 sf and up homes and I never really felt good about any of them from an environmental perspective. I did appreciate the paycheck and that they would employ other tradespeople for thousands of hours. All 3 homes had 4 occupants.
An energy retrofit seems like a worthwhile endeavor when looking at the lifetime of the home. After all a 9,000 sf home is more likely to be kept up and stay around for 100 plus years versus a 1,000 sf home.
I also wonder in our housing crunched, gig economy if the next step (or probably a few steps) is to subdivide these overly large homes in to several dwelling units - Living/Dining in to one unit; Kitchen, Nook, Family in to another and so on.
(With automated driving I have also wondered if 20-30 years from now we will be tearing up every other street where there is a city grid of streets to develop microhousing and gardens in these right-of-way areas.)
Jeff
Seattle, WA