Podcast 228: Subslab Ductwork, Safer Demo, and Insulating Walls Without Sheathing
Kiley, Matt, and Patrick hear from listeners about wood-fiber sheathing, humidifiers, and heat-pump water heaters before taking questions about how to demo a rickety carport, what to do about subslab ductwork, and how to insulate old walls without sheathing.
Follow the Fine Homebuilding Podcast on your favorite app. Subscribe now and don’t miss an episode:
![]() |
![]() |
![]() |
![]() |
Engineer Kevin writes in about the energy penalty of humidifying interior air. Architect Ethan talks about his Sanden split-system heat-pump water heater. Pro plumber Enoch talks about how to keep modern toilets flushing effectively. Kathryn writes in about the pros and cons of CO2 as a refrigerant. Former research assistant Bert weighs in on how old and new forests store carbon. Nate wants to know what he should do about the ductwork under the basement slab in his parents’ house. Ted wants to know the safe way to take down an existing carport before starting a new garage addition. Finally, Jourdan asks for the best way to insulate his old farmhouse which has no sheathing.
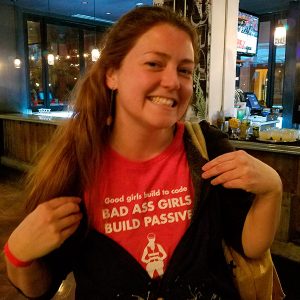
Editor’s Projects:
Leaving Las Vegas: Emu Systems, Passive Pods, Hoover Dam, and Mary Colter’s Hopi House
Kiley met Mariana Pickering, co-founder of Emu Systems, a company that offers builders Passive House training, at the #KeepCraftAlive event.
Patrick’s dryer repair.
![]() |
![]() |
![]() |
![]() |
![]() |
![]() |
![]() |
![]() |
Listener Feedback:
Listener feedback #1 — The energy needed to heat humid vs. dry air
Kevin writes, My day job is as an HVAC engineer. I’ve only work on commercial buildings, but the science is the same.
Humidification is not costly because it is harder to heat the air, it’s costly because it takes energy to evaporate the water. It’s a difficult concept to grasp, but I like to think of it in terms of “wet bulb” temperature. I’m sure you’ve heard the term “wet bulb” and knew that it was related to the humidity of the air and that is lower than the regular “dry bulb” temperature. The “wet bulb” temperature is defined as the temperature air would decrease to if passed over water. For example, air at 70 degree dry bulb temperature and 40% relative humidity has a wet bulb temperature of 55 degrees. So if you passed 70 degree 40% relative humidity air over enough water, the temperature of that air would decrease to 55 degrees. This is what your home humidifier is doing, it is adding humidity to your air at the cost of lowering the air temperature. This causes your furnace to work harder. How much harder? It depends on how much water you need to evaporate and the “latent heat of vaporization” of water, in other words, how much energy does it take to evaporate 1 pound of water, which is about 0.1 therms of energy per pound of water.
Let’s take an example of a really good 2,500 square foot house with 8′ ceilings, so 20,000 cubic feet, and 3 air changes per hour in a really bad climate on the worst hour of the year, 0 degree dry bulb and no humidity with enough wind to cause the pressure differential for 3 air changes which would be about 20 miles per hour. During this terrible hour you’ll pull in 60,000 cubic feet of outdoor air. In order to heat that air up to 70 degrees, your furnace will have to put out 0.75 therms. In order to bring that air up to 40% relative humidity, your humidifier is going to have to add 28 pounds of water, which will take 0.28 therms of energy, which in the end, your furnace will have to add.
So on the worst hour of the year, humidification can be about 25% of the cost of your air leakage. Where I’m at, 1 therm of natural gas costs about $1.25, so we’re not breaking the bank if we have a tight house, but it is a significant portion of your HVAC costs. If you are planning on humidifying your house, air sealing is even more important.
Energy costs is just one consideration to take into account when deciding whether to humidify our not. Condensation, drying potential, thermal comfort, and health all need to be taken into account. But I think I’ve been as dense as I can be for one email.
Related links:
Listener feedback #2
After a long process of “perfecting” wall, roof, and ceiling assemblies, it became clear that providing domestic hot water efficiently was the next most important thing to do. I ran various calculations regarding recirculating showers like the Orbital Systems [The call it the Tesla of showers.) but my family takes a lot of baths), hot water heat recovery (also less effective with baths), and finally settled on heat pump water heaters as the best solution to reducing domestic hot water energy use.
Concerns regarding GWP (global warming potential) of the majority of HPWH on the market, as well as concerns regarding the problems that “all-in-one” HPWH exhibit (winter cooling and dehumidification as well as noise) in this very tight (0.2 ACH50) drew me to the “split” Sanden. Also, I believe your analysis of CO2 as a refrigerant is incorrect. My understanding is that CO2 is a very effective “heating” refrigerant, but not as much so a “cooling” refrigerant, hence its absence from AC equipment. Also, CO2 has to be under high pressure, so the entire compression cycle happens outside, which means water runs between the house and the outdoor unit, which give many people pause. We insulated these pipes and ran heat trace, and the unit itself has a mechanism to avoid freezing.
I purchased the 119gal Sanden from 475 for about $4000. The install was done by our plumber, with electric tie-in by electrician. There was definitely more coordination required due to the split nature of the system, and some extra plumbing, but I don’t think it was out of the ordinary. Regarding cost, I mitigated this by installing one 119gal HPWH for this 2-unit building. I do share some of your concerns regarding servicing, etc. but basically decided that in this instance I should “be the change I wanted to see” as someone once said – basically so I could write letters like this one.
Regarding overall performance – so far hot water production has been sufficient, even through some major cold snaps this fall and winter. I installed a Sense meter with the hopes of measuring my electricity usage to produce DHW but that was wishful thinking in that it has not yet identified the Sanden and maybe never will.
I am happy to report back or provide more long range analysis of my experience with the Sanden as time goes on. One difference working with a smaller company such as Sanden is that in the few instances that I have run into trouble I have been able to speak directly with someone personally knowledgeable about the unit – something that infrequently happens when working with large multinational appliance companies.
Thanks for the podcast – keep up the good work!
Related links:
Listener feedback #3
Kathryn from Seattle, WA writes, I agree that there is a concern about the use of HFC refrigerants because of their very high global warming potentials. However, I don’t agree that that’s a reason to avoid heat pumps and go with a plain resistance water heater. The Kigali amendment has come into force and the whole world (minus the US) is shifting to low GWP refrigerants such as HFO-1234yf (already in use in many cars), pentane (already in use in many refrigerators) and CO2. The reason that CO2 isn’t in common use is not because it’s not a good refrigerant. In fact, most natural refrigerants have much better thermal properties than the CFC and HFC legacy refrigerants. CO2 must be used at extremely high pressures, and that has required the development of very specialized compressors to handle >73bar for a supercritical CO2 cycle. Both California and Washington are independently phasing out HFC refrigerants, which could raise the price of the final products by a whole 1%, because the refrigerants themselves are a very tiny fraction of the total system cost. I anticipate that the cost of heat pump components will come down as people start buying more of these systems.
Listener feedback #4
Bert writes, Hi there team, I’ve heard your discussion of Gutex insulation on a couple of recent episodes. You guys raised the perfectly reasonable question of whether the product’s eco bona fides should be trusted, given the idea that trees have to get cut down to produce, and deforestation is a major driver of climate change.
While I usually listen to your show in an attempt to soak up knowledge in a field I know little about, this point brings me into an area where I actually do have some expertise to offer. Years ago before pursuing my PhD, I was an undergraduate research assistant in a crop and forest physiology lab at the University of Illinois. One of the things I learned about there was the decline in the net amount of carbon stored by a forest per year over time – young forests store carbon much more rapidly than old-growth, and tree plantations that are managed to remain productive can absolutely be net sinks for soil carbon – on top of that, the carbon embedded with resin and used as insulation on houses is locked away and out of the atmosphere for a very long time.
Now, all of this is ignoring the fact that gutex is almost certainly made not from good lumber but from sawdust/fiber/other waste products that are traditionally burned to power a sawmill or landfilled – but that’s not an area I know as much about.
I have no idea if this product is any good, again that’s your area. But I’d love to hear more about it because knowing what I do about the carbon cycle, using wood fiber to make insulation seems like a great idea.
Related links:
Question 1: Why did someone bury HVAC ducts under my slab, and what can I do about it?
Nate writes, Hey FHB podcast, I’m a huge fan of the podcast and look forward to the creative ways that you convince people to air seal their homes. As an energy auditor by profession, I appreciate all that you do to make my job easier!
I live and have been working in New England for a number of years but have a question about my parent’s retirement home in Upstate New York. On my first summer visit I immediately felt the high humidity levels in the basement and noticed a faint moldy smell. The ductwork for the basement furnace was buried in the slab. I have never come across this in New England and could not imagine why anyone would ever attempt such a thing. Is this the poor mans’ radiant floor heating? Fast forward to when I was there over the holidays, the humidity was still very high, even with below freezing temperatures outside. They need to constantly run a basement dehumidifier and dump two 50 pint buckets a day. I had them place hygrometers in each room, which consistently read 70% RH. My hunch is that the warm, dry air going through the concrete is expediting capillary action through the slab, most likely from the front of the house where the slab is 8′ below grade and well below the frost line.
The ductwork was just scope by an HVAC contractor and the news was not good; crumbling concrete, rusted sheet metal etc.
My questions are fold:
1. Is there a way to salvage the ductwork? Perhaps a pressurized, liquid applied membrane similar to AeroSeal?
2. Why did a builder at any point think that this was a good idea? Is there something I’m missing?
I’m concerned for the homes’ performance, but especially the IAQ as they get older. I feel like the safest solution is to fill the ductwork in with concrete and install mini splits.
Any advice is greatly appreciated.
Related links:
- Can You Heat a House with Air Ducts in a Concrete Floor?
- Download: Heat Emission Characteristics of Warm-Air Perimeter Heating Ducts
Question 2: What is the safest way to demolish a carport that is attached to my house?
Ted writes, Hello Fine Homebuilding pod! Long time listener, love the pod and listen to it while I sand at work (I’m a cabinetmaker in a commercial millwork shop)
This spring I am adding an in-law suite and two-car garage/woodshop onto my house. I’m acting as the GC and subbing out what I think makes sense to speed along the build. My role will be to outfit the interior from drywall to cabinetry and trim etc.
My question has to do with an existing rotting carport I need to demo from the house.
As far as I can tell this carport is attached with a ledger board nestled underneath the “flat” roof on this mudroom. I think the carport is only attached with nails through the ledger. My plan to take it down is to attach some temporary support beams in the middle and ends and using a sawzall cut through the rafters and the push it over. After which I can rip the ledger board off and move on with the addition.
Do you see any issues with doing it this way? Is there an easier/better way to take this eyesore down?
I’ve included images of my house and carport as well as some cad drawings of the addition. I plan to make the “flat” of the mudroom a pitched roof when we start the addition so that rain and snow will fall off and not get trapped up there anymore.
![]() |
![]() |
![]() |
![]() |
Thanks so much for all you do! As a first-time homeowner since last December, I’ve had to learn a crazy amount. I find that I absorb good information through you guys. I like the variety of questions you answer. I end up having heard something about any problem I encounter in the house (it was built in 1912 so problems I got) and I feel empowered knowing I can find the information needed to tackle things. Like a new shower week one, blow in cellulose in every stud bay, fix a sump drain pipe, change dryer vent hose etc. etc….. why do I love this? I must be nuts.
Related links:
Question 3: Can you help me choose the best plan for insulating the walls and roof in an 18th-century house with no sheathing?
Jourdan from upstate New York writes, Hey FHB airsealing, insulating, and answerers to all weird building-science phenomena,
My name is Jourdan. My wife and I own a 2400 sq.ft. farmhouse that was built in 1780 in upstate New York about 10mins north of Saratoga springs. We purchased the home with the intent to renovate and flip while we live there. We purchased the home September of 2018 and my son was born November of that year. We have started demo on the upstairs portion of the house and have plastic of the doorways in the stairwells to avoid dust and debris getting into the living spaces.
I run my own small-time renovations company and grew up with a father that is a contractor. With all my years around and working in the trades I haven’t ran into some of the questions i have with this home. My question involves insulating and air sealing. My wall assembly is cedar lap siding right on the framing which I can see day light through in some spots now that we have the lath and plaster removed. Would you guys suggest spray foam in the stud bays right onto the backside of the siding? Open cell or closed cell? Or just caulk the siding and fiberglass? (I’m also trying to be cost conscious since we are redoing the entire interior of the house).
![]() |
![]() |
![]() |
![]() |
Same question applies to the ceiling of the upstairs. The roof assembly is metal roofing, OSB sheathing, the old barn board style sheathing that runs horizontal on top of the rafters. The rafters are true 3×4 beams that are spaced 3ft apart. Although it would lower my ceiling height some, I believe I will be adding in dimensional lumber 16 on center. One for more support and two for a larger stud cavity for added insulation in our cold climate. I vaguely remember you guys talking about collar ties in one of the podcasts. Is the rule of thumb that the collar ties can go no higher than a third of the length of the rafter? I would like to raise the collar ties but don’t want to compromise the strength by doing so. I’m sure I will have more questions for you guys along the way since this is the oldest home I’ve ever worked on, I can’t wait to breathe new life into this house and pass it onto a family that will enjoy it for years to come. I also wanted to let you guys know that I’ve only subscribed to the magazine for about 8 months now and wish I had done it sooner. I found the podcast shortly after subscribing and you guys are a wealth of knowledge. I appreciate you guys sharing your knowledge and helping me and others like myself to understand the building science behind the materials we work with on a day to day basis.
Thanks for all your help, hope to hear from you soon.
Related links:
- Insulating Walls in an Old House With No Sheathing
- Protect Your Family from Asbestos-Contaminated Vermiculite Insulation
- How it Works: Collar and Rafter Ties
End Notes:
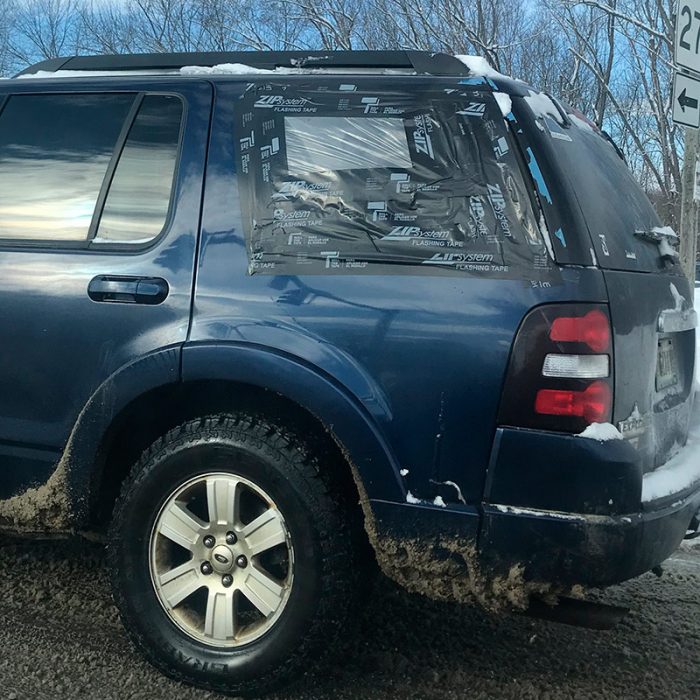
Isaiah writes: Hey guys I know you are all about air-sealing and flashing windows so I thought you’d enjoy seeing this car’s window. I wonder if it’s properly flashed. Thanks for all your work on the podcast.
If you have any questions you would like us to dig into for a future show, shoot an email our way: [email protected].
If we use your question we’ll send you a FHB Podcast sticker!
#KeepCraftAlive
KeepCraftAlive hats help celebrate the value of true craftsmanship–plus 50% of all proceeds from every hat sold go to the #KeepCraftAlive Scholarship Fund, supported by Fine Homebuilding and SkillsUSA.
Buy a #KeepCraftAlive hat or t-shirt
This episode is brought to you by Huber Engineered Woods, makers of AdvanTech and ZIP System products.
The Prove Tour product experience is coming to a lumber yard near you. Huber Engineered Woods fleet of traveling hands-on product demonstrations is hitting the road soon for lumberyard events across the country. Try ZIP System liquid flash, Zip System stretch tape, and AdvanTech subfloor adhesive in an immersive product experience. For event details, check out the stories and highlights on @huberwood on Instagram profile each week or ask your local Huber rep about a local “Prove It Tour” event near you.
Fine Homebuilding podcast listeners can now get 20% off anything in the Taunton store, including the Code Check series. These sturdy, spiral bound reference books will help you navigate the International Residential Code, The National Electric Code and the Universal Plumbing Code. Use the discount code FHBPODCAST to take advantage of this special offer.
We hope you will take advantage of a great offer for our podcast listeners: A special 20% off the discounted rate to subscribe to the Fine Homebuilding print magazine. That link goes to finehomebuilding.com/podoffer.
The show is driven by our listeners, so please subscribe and rate us on iTunes or Google Play, and if you have any questions you would like us to dig into for a future show, shoot an email our way: [email protected]. Also, be sure to follow Justin Fink and Fine Homebuilding on Instagram, and “like” the magazine on Facebook. Note that you can watch the show above, or on YouTube at the Fine Homebuilding YouTube Channel.
The Fine Homebuilding Podcast embodies Fine Homebuilding magazine’s commitment to the preservation of craftsmanship and the advancement of home performance in residential construction. The show is an informal but vigorous conversation about the techniques and principles that allow listeners to master their design and building challenges.
Other related links
-
- All FHB podcast show notes: FineHomebuilding.com/podcast.
- #KeepCraftAlive T-shirts and hats support scholarships for building trades students. So order some gear at KeepCraftAlive.org.
- The direct link to the online store is here.
View Comments
Patrick,
For the dryer I think the manufacturer just wants you to buy a new one.
There is a company that makes magnetic dryer vent couplings. https://www.magvent-dryervent.com/ I've recently replaced the dryer metallic hose with a proper duct. Between cleaning the damper outside and the metal duct it seems to work better, doesn't let so much cold air back in the house, and I feel safer.
I own four dryers from an old Fridgidaire to a Kenmore, and two Whirlpool duets, one a Kenmore. All of them have the same gas valve and burner assembly. The new ones have humidistats and expansive to replace circuitry.
My recommendation, use your skills making cabinets to cut those access panels in the in the case. I had a similar issue with one of my duets and what was minutes on the Kenmore was like an hour on the duet.
Whatever fire suppression you lose by breaching that panel is more than made up by the ability to service it properly. There are somewhere around 15000 washer and dryer fires every year in the US. A significant portion due to lint. There is a lot of talk of why there are no handyman. In addition to a general lack of respect to those who work with their hand there is a serious misunderstanding of the importance of keeping your dryer clean. Better performance, less energy usage, and much safer. You can get a new dryer but underneath it will likely be the substantially the same. While many of the new ones could be displayed at MOMA, fundamentally all they do is blow warm air over your clothes. Why someone would spend $500-600 on a warmed over version of the same appliance, and not $50-100 on someone to service it is beyond me. When they come up with a heat pump dryer I might consider it.
Why doesn't some consumer group crack down on these installations. I remember when the guy came over to my house, Its less than five minutes to install the dryer.
Patrick next time you have it open for about $100 in parts you can basically make the thing dryer like new. New belt, tensioner pulley, solenoids, flame sensor, and thermistor, along with regular cleaning and you will be happy as a clam.
I love your show, you make me laugh (though I am unusual in what I will laugh at) but please keep your day jobs. There aren't many places these days where sarcasm is served so generously and appropriately.
Take Care
Hi John, Thanks for your thoughts and your kind words about the show. There are heat-pump dryers available, but their expense and relatively long dry times make them uncommon. Here's a little more about Heat Pump and Condensing dryers. https://www.greenbuildingadvisor.com/article/heat-pump-clothes-dryers