Podcast 230: Wood Foundations, Thermostat Setback, and Housing Affordability
Listeners give feedback on the ethics of vacation homes, making good welds, and stacked washers and dryers before the editors take questions on good home-building content, the right foundation for a room addition, and setting back thermostats to save money.
Follow the Fine Homebuilding Podcast on your favorite app. Subscribe now and don’t miss an episode:
![]() |
![]() |
![]() |
![]() |
Regular listener Mikee sends in a photo showing him and the podcast gang at the The Builders’ Show. Eric asks if a second home is a waste. Mark describes how to verify the quality of welding, and Larry offers a common-sense solution for stacked washers and dryers. Chris asks the crew what they like in high-quality home building content. Matt asks about permanent wood foundations, and Mike wants to know if he should turn down the thermostat while he and his wife are at work. Finally, Doug asks if the building industry has abandoned people of ordinary means.
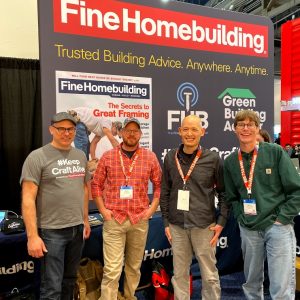
Listener Feedback:
Listener feedback #1
Mikee writes, Hey Guys, It was fantastic meeting you all at IBS. You really are the “real deal” as your podcast reflects!
Listener feedback #2
Eric writes, I look forward to listening to your podcast on my commute. It seems to be a bit less of a “fine air-sealing” podcast these days than it was in the past.
I listened with interest to your discussion about the ethics of doing an energy retrofit of a monstrously large home. A few episodes later, there was a question about doing a retrofit on a cabin so that the water wouldn’t have to be turned off and drained each time the owner used the house in the winter. I was surprised to *not* hear any discussion about whether this would be a waste of energy. The cost and embodied energy necessary to make a part-time second home tight enough to leave the water turned on and heated for the potential weeks that no one is there seems like a similar waste as making a grotesquely large primary home energy efficient. That said, I do see the appeal of having modern running water for the weekend visits. The idea of a smaller core that is well insulated and heated for the utilities and water seems like a good trade-off (if the existing floor-plan makes it feasible.)
Listener feedback #3
Mark writes, Several episodes back, the topic of welding inspection came up. I’m a welding and machining inspector in the nuclear pressure vessel industry. Our welds have to hold and although the welds done in Home building won’t be as critical, I wanted to offer a few tips for those who do not have much experience welding or inspecting welds.
1.) A weld should essentially look like a nice bead of untooled caulk between the two pieces being welded. The edges of the weld should fuse into the base metal fairly smooth and there shouldn’t be sharp notches or valleys along the edges or between beads. This is because the stress and strain applied to the welded structure will concentrate at the valleys and notches and cause cracks or failures. Keeping the weld free of notches allows the stress to flow through the weld.
2.) Don’t be afraid to run multiple beads. Don’t try to get it all in one shot if your weld is bigger than 3/16. Each bead should add roughly an 1/8″ thickness if it’s done correctly. Just be sure to wire brush or clean the weld between beads so you don’t trap slag or trash in it.
3.) Back-groove the weld for stronger welds. If you’re welding material 1/4″ or thicker, start by putting a bevel (usually 45 degree) on the edges of the joint, weld it from one side first then on the backside you want to grind into the weld and create a groove to remove any lack of fusion or incomplete penetration, etc. This is done to remove inconsistencies that could cause a weak spot in the weld. You’re only grinding until you get to good sound metal that doesn’t have trash or voids in it. Once that’s complete, weld the groove you created.
4.) Do a Bend Test. Bend-Tests are one of the best ways to check the strength of your welding. Companies use it frequently to test the quality of a weld. Typically, a strip of metal is cut out of a sample perpendicular to the weld and is then bent into a U shape. Then the weld is inspected for cracking. Before you weld your joint, create a mock-up using a piece of scrap as practice. This is a great idea and you can adjust your welder’s settings before you weld the actual joint. Once you’re done welding the mock-up, put it in a vise, smack the heck out of it with a hammer and see if you can break it.
These simple tips generally go a long way in helping people increase the quality of their welds, especially for those that don’t have much experience with it. I hope this helps.
P.S. – Thanks for the Email and Link to Larry Hahn’s framing videos. It covered so much information on tips and tricks and it’s going to speed me up a lot. I’d love to see more videos like that in the future. Thanks so much!
Larry from Ontario, Canada writes, Enjoy your podcast every episode. We are building a new cottage here in Canada but due some bedrock in the way we were delayed and now very cold weather delays our footings, ICF, and the rest. So I am always looking for a building ‘fix’, until the thaw.
Re: podcast #228 – I share Patrick’s beef with stacking washer/dryer combos. This has to be one of the worst engineered consumer products ever. The units are not designed to service in place. A replacement unit won’t stack with a survivor. And, they fail with what most would consider normal use.
At home, I already have two spare dryers in storage from two washer failures. When the washer failed again, the repair service wanted to charge for two servicemen to deal with the stacked unit.
I solved this problem once and for all with a 3/4″ MDF shelf above the front-loading washer, with cutouts for plumbing and electrical, sitting on 1 x 2″ cleats on the sides. The dryer is placed on top. A bit of routing and enamel spray to finish it, and it will never be an issue again. Before I positioned the shelf, I checked the common sizes of washers and dryers to position the height for future replacement of a unit.
We want the stacking footprint but will never again rely on stacked units, we will always build a shelf in anticipation of a future issue.
Sorry about the poor-quality photo.
Editor Updates:
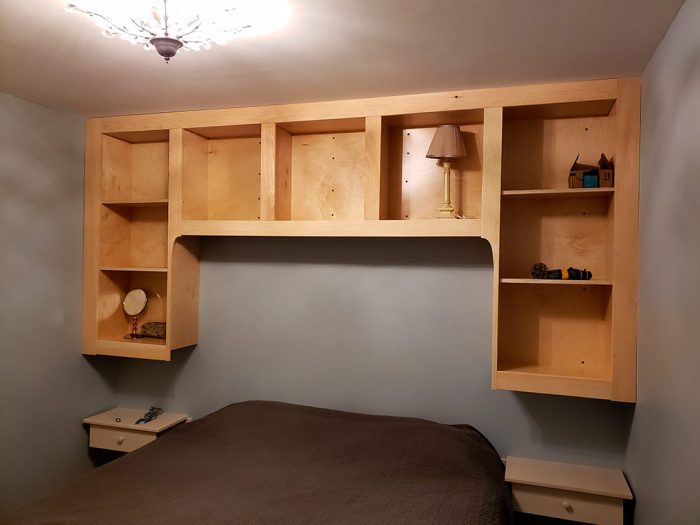
Kiley’s crispy wires
Patrick’s bedroom cabinets
Matt’s future cabinets
Question 1: What do Fine Homebuilding editors read, watch, or listen to (other than Fine Homebuilding) for coverage of the craft and science of working on houses??
Chris in Charlotte, NC writes, Hi FHB crew, I’ve heard you lament how bad HGTV style shows can be and I couldn’t agree more. I used to watch them when they were the only thing available but with the explosion of YouTube and streaming services I’ve cancelled cable and don’t miss it in the least.
I love the international diversity you can find on Netflix through shows like Grand Designs, and the production values on YouTube channels like Matt Risinger’s can feel just as polished as a “real” TV show. You can find most episodes of PBS classics like This Old House for free on their site and Instagram has exploded with great content from real professionals like Steve Baczek @stevenbaczekarchitect 🙂
I’m wondering, other than the fine publications of Taunton Press, what media do you consume about the craft and science of working on houses?.
Here are some of Chris’ favorites;
Grand Designs on Netflix
Matt Risinger on YouTube
RR Building on YouTube
This Old House on YouTube
House and Home on YouTube
Related links:
- Kiley: Podcasts— Modern Craftsmen, Clearstory, Greenbuilt Alliance
- Matt: Construction manuals
- Patrick: Hot Rod magazine, Motortrend’s Road Kill, Amazon’s Travels by Narrowboat
Question 2: Is a wood foundation suitable for a house addition in Minnesota?
Matt from Lanesboro, Minnesota writes, Dear FHB gang, I spend many an enjoyable work day listening to you folks on the podcast, marveling that you actually get paid to do it! I have been a residential building contractor in Minnesota for 27 years. About 15 years ago I moved to rural S.E. Minnesota and bought a 150-year-old brick farmhouse with a stone foundation. It had been gutted and remodeled before I bought it so it is in fine shape. I would like to add a 1 story 16′ x 16′ sunroom to it and am mulling over my foundation options. The addition will have a full basement since there currently is a cellar door leading into the existing basement so the new basement would have easy access to house basement. I am hoping to make the new basement into a legal bedroom by having an egress window. I have never laid block (CMU’s) but am up to the task (I am only 64 years young). But then I have to deal with the inside surface with insulation, electrical, drywall etc. I have a sister and brother-in-law who built an All-Weather Wood foundation for their house about 30 years ago and all is well with it. This system is easy to build, insulate and run wiring and hang drywall. Do you have any experience with wood foundations? I plan on pouring the basement slab first then building the foundation walls on top. What do you think the best way to “water proof” this foundation would be? Any other options I should consider? I am usually a one-man operation and am not sure if I want to deal with pumping concrete into ICFs.
Related links:
- What’s the Difference: Pressure-Treated Lumber
- American Wood Council: Permanent Wood Foundation Design Specifications
- InterNACHI: Permanent Wood Foundations
Question 3: Do thermostat setbacks save energy?
Mike from Wade Brothers Carpentry writes, Hey FHB podcast, I have a heating and probably cooling question (although I don’t have central air conditioning). I’ve listened to your show for several years now and don’t know if this has been discussed, or maybe I just missed it.
In my apartment in Chicago my wife and I have forced air heat. When we leave for the day we set the thermostat to 60 and the first one home raises the temp to 70. When we go to bed we turn the temp down to 65. While manually changing the temp every day isn’t ideal, we rent so swapping the thermostat for a new setback model isn’t an option.
My question is generally does it take more energy to bring the apartment up to 70 after it being 60 for the whole day vs. setting the daytime temp to say 65? If no one is home should we set the daytime temp even lower? If we did have a central A/C system would the opposite be true?
Thanks for all the great info you guys put out and keep up the good work.
Related links:
Question 4: Can the average homeowner afford to build a high-performance home?
Doug from Colorado writes, After watching the podcast with Steve Baczek from The Builders’ Show, I was struck by the conflict between best practice and what the home buyer can afford. He spoke about the long-term value of high-end materials. I don’t doubt that this is true, but how does that help the buyer who can barely afford a basic code-built house? Is the industry saying that only the affluent can have a new house? Even in parts of the country that used to be more affordable the median home price has risen to a level that excludes the average wage earner.
I don’t have an answer for this dilemma but I feel it’s a topic that needs more discussion by the building industry. A high-performance home is useless if you can’t afford it.
Related links:
- Is a “Pretty Good House” Good Enough?
- A Pretty Good House in Maine
- FHB House 2017: Introducing a Net-Zero, Production-Style Build
Joel VanderWeele, architect from Providence, RI, writes, Dear FHB Podcast Crew, I’m a recent convert to the Fine T-Stud Debate Podcast and I’m thoroughly enjoying it. I have been working my way through the back catalog whenever I go to the gym so, you know… it’s been slow going. As an architect and newbie home-owner/landlord, it’s fun to learn about all the things I’ve messed up along the way, as well as things to avoid in the future (flat roofs, irregularly shaped gazebos, and low VOC adhesives).
You’ve had a number of conversations about right-sized housing, which is something our firm thinks about a lot. There’s obviously a great need for “starter home” type housing, but what can we do about it? As architects, the people who can afford to hire a professional to design a custom home are rarely looking for something small and simple.
One strategy we’re experimenting with is something we’re calling the Side Hustle House. It’s a cheap set of house plans for a starter home specifically designed to support alternative means of making some supplementary income – renting a room out, using the extra space for your side job, etc. The plans include details for a 2-bedroom “base house” as well as optional additions that can be added later or as your budget allows.
This is a totally new thing for us that we hope catches on, but I’d be curious to hear from you what you think architects/builders/etc can and should be doing to encourage greater production of small, simple, quality homes that will last.
Love the show
![]() |
![]() |
If you have any questions you would like us to dig into for a future show, shoot an email our way: [email protected].
If we use your question we’ll send you a FHB Podcast sticker!
#KeepCraftAlive
KeepCraftAlive hats help celebrate the value of true craftsmanship–plus 50% of all proceeds from every hat sold go to the #KeepCraftAlive Scholarship Fund, supported by Fine Homebuilding and SkillsUSA.
Buy a #KeepCraftAlive hat or t-shirt
This episode is brought to you by Huber Engineered Woods, makers of AdvanTech and ZIP System products.
The Prove Tour product experience is coming to a lumber yard near you. Huber Engineered Woods fleet of traveling hands-on product demonstrations is hitting the road soon for lumberyard events across the country. Try ZIP System liquid flash, Zip System stretch tape, and AdvanTech subfloor adhesive in an immersive product experience. For event details, check out the stories and highlights on @huberwood on Instagram profile each week or ask your local Huber rep about a local “Prove It Tour” event near you.
Fine Homebuilding podcast listeners can now get 20% off anything in the Taunton store, including the Code Check series. These sturdy, spiral bound reference books will help you navigate the International Residential Code, The National Electric Code and the Universal Plumbing Code. Use the discount code FHBPODCAST to take advantage of this special offer.
We hope you will take advantage of a great offer for our podcast listeners: A special 20% off the discounted rate to subscribe to the Fine Homebuilding print magazine. That link goes to finehomebuilding.com/podoffer.
The show is driven by our listeners, so please subscribe and rate us on iTunes or Google Play, and if you have any questions you would like us to dig into for a future show, shoot an email our way: [email protected]. Also, be sure to follow Justin Fink and Fine Homebuilding on Instagram, and “like” the magazine on Facebook. Note that you can watch the show above, or on YouTube at the Fine Homebuilding YouTube Channel.
The Fine Homebuilding Podcast embodies Fine Homebuilding magazine’s commitment to the preservation of craftsmanship and the advancement of home performance in residential construction. The show is an informal but vigorous conversation about the techniques and principles that allow listeners to master their design and building challenges.
Other related links
-
- All FHB podcast show notes: FineHomebuilding.com/podcast.
- #KeepCraftAlive T-shirts and hats support scholarships for building trades students. So order some gear at KeepCraftAlive.org.
- The direct link to the online store is here.
View Comments
nice
Hi, folks! I enjoyed meeting Justin and Rob at IBS a few weeks ago.
Y'all totally missed the pun in "Side Hustle" with the pictured house.
On a different subject: the house I'm rehabbing in Gordonsville VA has two doghouse dormers in front and a shed bump-out in back - none of which had step flashes. Even though the roof appeared to be fairly new when we bought the house, we discovered it leaked along the side walls of the dormers. While all of the dormer/shed side walls had flashing, it was a single piece - of flattened 6" aluminum round duct. One end of the shed bump-out had a 2 inch long gash in the bend of the single flashing, so it funneled rain right through... right through the kitchen ceiling into the kitchen sink. I've added step flashing...
We call it "What were they thinking?" and at times a quote from the animated movie Meet the Robinsons: "I'm beginning to wonder how well this plan was thought out."
Wood foundations: you forget Creosote. Yuck, but i have a woodshed probably built in 1978, with a used railroad ties foundation, on the ground. (Alaska RR). Okay, he worked for them when he wasn't commercial fishing. So many of the "houses" in this area started as fishing shacks (Well, yeah. World famous Red Salmon and Silver Salmon runs - Kenai, Peninsula, South Central Alaska, south of Anchorage, on Cook Inlet). It was cheap and available - remember we 1) have a transportation and shipping cost penalty, 2) no building codes even today, if you aren't in a city, 3) lots of subsistence living, lots of seasonal.
As you go underground to a Virginia Mason Hospital garage in Seattle, WA, one wall is a wood foundation, lots of creosote. You are under a multistory building and it does make you wonder! Is that quake proof, he asked?
Yeah, no building codes and some of the houses are downright frightening. You are invited to imagine the wiring.
Keep up the great work.
P.S. add "Hand Tool Rescue" to the you-tube list. He's crazy, and i like it that way. A circular saw powered by a single-piston gas engine?!? Bought a Contractor friend his t-shirt featuring the patent on the Monkey Wrench. I thought that was a derisive term for a generic wrench, or even an urban myth.
Then there is "The Essential Craftsman": Blacksmith. Builder. Former logger. Amazing.
Take your pick of band-saw operators, but i like "Out of the Woods" and Matthew Cremona (Who built his own band saw mill, and now is on his second trailer) Urban logger.
Those two make me wish I'd known to get into the business 50 years ago.
Finally, "Engles Coach Shop". What a treat. What a multi-talented craftsman: Woodworker. Blacksmith. Machinist. Historian. Got a horse-drawn freight wagon or carriage needing repair? He's your man. Want need a new "40-mule-team-Borax-Wagon" set? He built it from scratch, but farmed out the riveted water tank. Hard to say enough about him. Only man i know who can drill through 8 inches of wood, from both sides, and hit the hole.
I echo the comment on watching The Essential Craftsman - his series on Spec House building is my usual lunch break viewing. The host Scott Wadsworth is a wealth of knowledge, and has such a kind demeanor, with calm and reasonable explanations to his work as it progresses, and things to watch out for. https://essentialcraftsman.com/about
He would make an awesome guest on the podcast.
Thanks,
Jim Collins
Burlington, Ontario
Greate Job!