Podcast 231: Heat Pumps, Old-School Air Barriers, and Rehabbing Cordless Tools
The regular crew hears from listeners about apprentices, subslab ductwork, and the risks of bungee cords before taking questions on cold-climate heat pumps, tying old plaster to new framing, and what to do when cordless power tools lose their punch.
Follow the Fine Homebuilding Podcast on your favorite app. Subscribe now and don’t miss an episode:
![]() |
![]() |
![]() |
![]() |
Matt, Kiley, and Patrick hear from Ian about apprentices and Josh writes in about Sanden heat pump water heaters. Doug describes demolition of neglect in Charleston and ophthalmologist Dr. Lee talks about the dangers of bungee cords. Matt asks if an air-source heat pump can keep up in cold weather and Dan wants to know how to tie the existing plaster to his new bathroom framing. Andrew asks why there are two layers of plaster in his Wisconsin farmhouse and Barbara is looking for guidance on fixing or replacing cordless power tools.
Listener Feedback:
Listener feedback #1
Ian, lead carpenter at Hudson Valley Preservation writes, Patrick and podcast crew, In my not so humble opinion if a company is going to bestow upon a new hire the title of “apprentice” the company has an obligation to teach that individual the basics of the trade performed by that company. The misclassification of laborers as apprentices is a serious issue in the building trades. Too many companies lack the resources or the true desire to teach a young person the trade. They are really just after cheaper labor. (For a thorough breakdown of the True Cost of an Apprentice see Gerstel’s book Nail Your Numbers). You guys are right that a young worker would prefer to be called an apprentice than a laborer as the former is viewed as the first step in starting a career.
On top of all of that if you read this link to the Department of Labor website you will find that the terms “apprentice” and “apprenticeship” have legal definitions for the responsibilities of both the employer and the employee.
Rant over…for now
Listener feedback #2
Josh writes, Hi, I love to listen to you guys on my 1-hour commute. I know you’ve kinda beat the Sanden Hot Water heater topic to death. But one thing I hadn’t heard mentioned is:
The refrigeration circuit is self contained in the outdoor unit. All you do is hook up the water lines to the indoor tank and power it. There is no inside condensing unit. I mention this because you had said one of the negatives was CO2 specific refrigeration tools and knowledge being in short supply. In a new install, a plumber and electrician should be able to do everything. There are some best practices to avoid freezing the water line in cold climates that Sanden covers.
I don’t have one, but I keep my eye on promising up-and-coming technologies.
Listener feedback #3
Doug writes, Hi “Y all”, It was fun to have Brian on podcast #229. In 2007 our daughter flew to Charlestown to visit a friend. While there she met guy who was more interesting than us and she ended up moving there. They were married in 2009 and have lived in the area since. They don’t live in Charlestown proper because of the cost, but on our visits we have spent a lot of time in the city. According to our son in-law it is almost impossible to get permission to tear down an old house regardless of the condition. This has led to what is referred to as “demolition by neglect”. Once a house has collapsed they can clear the debris and build new.
Keep up the good work.
Listener feedback #4
Brad in Michigan writes, Hi there – first time listener. Enjoyed the question and answer section!
I have a mid-century modern house, slab on grade with ductwork also under the slab in Michigan, so I was particularly interested in that question. What do you all think about something like Duct Armor for coating the ducts? Abandoning them isn’t really an option – no attic, and radiant retrofit is too cost prohibitive. Would that remedy all the concerns?
Thank you!
Listener feedback #5
Dr. Lee in Bay City, Michigan writes, Hello FHB podcast crew, My name is Dr. Lee Newton. I am an eye doctor and a real estate developer in Bay City, Michigan. I always enjoy your podcast and the mention of bungee cords on a recent show was particularly meaningful to me because of my work.
I have at least one patient with a prosthetic eye due to a bungee cord misadventure, and others who have experienced sight-threatening injuries from bungee cords.
Here is my opinion on bungee cords: They are garbage. Do not use them. Do not go within 50 feet of a bungee cord that is in use. They are made cheaply – no matter where they are made. Why else do you think that we commonly see metal hooks and frayed ends along the side of the road and in parking lots? The hook is small enough to fit within the confines of the bones that collectively make up the eye socket (orbit). Something this small causes more eye damage because the force of impact is imparted to the eye itself and not the bones. It’s the same reason a racquet ball causes more eye damage than a basketball.
My advice is to use a ratchet strap instead and do not allow anyone you know to use bungee cords. They should be outlawed because they are stupid and dangerous.
Thanks for letting me vent! Keep up the great work!
Related links:
- Dr. Matt Weed, Ophthalmologist: Beware of Bungee Cords
“I have seen people with severe traumatic injuries to their eyes from every possible cause you can imagine: knives, guns, pencils, fists, fireworks, Christmas stocking holders, tennis court net cranks, lasers, bleach, acid, fire, baseballs, hammering, bailing wire, you name it. But, surprisingly, I have seen more patients with severe eye injuries due to bungee cords than any other single mechanism I can think of” - Workplace Safety North: The Risky Business of Bungee Cords
“The backlash from the bungee cord can be so powerful that it can reach speeds of up to 100 kilometres an hour. This amount of power can result in cuts to eyes, internal bleeding of the eye, traumatic cataracts and possibly detachment/tearing of the retina. Victims can experience mild to severe loss of vision and in most serious cases victims have had to have their eye removed.”
Editor Updates:
Matt’s roof flashing
Kiley’s Hudson Valley Preservation and Connecticut Building Science & Beer gathering
Patrick’s bedroom cabinets
Question 1: Should I install an oversize mini-split HVAC system so I have enough heat on the coldest days of the year?
Lee in Pine Bush NY writes, Hi FHB podcast, I have a question about sizing mini split heat pumps in a cold climate. I ran a quick manual J and learned I will need about 12,670 BTUs for cooling and 14,629 BTUs for heating in our Northeast climate (southern Ulster County NY: Pine Bush). I decided on a Fujitsu 12RLS3HY with a base pan heater, which states it supplies 12,000 BTUs in cooling and 16,000 BTUs in heating. The minimum operating temperature for heating was rated at -15° F. Problem solved right?… Nope. Upon reading the AHRI rating, I learned that the unit’s High Heat Rating @ 47° F is 16,000 BTUs of heat, but it’s Low Heat Rating @ 17° F is only 9,600 BTUs. This Low Heat Rating seems to occur when it is really cold and I would need every last BTU. I checked some other units and this seems to be the norm, which makes perfect sense because heat pumps lose efficiency in the cold, but I thought that meant more power consumption not less BTUs. I hope I am misunderstanding the relationship between the Manual J recommendations and the AHRI Low Heat Ratings. To further muddy the waters more, Fujitsu stated in their Submittal Form under “capacities” that the unit is “rated” for 16,000 BTUs of heat, but it has a minimum of 3,100 BTUs and a maximum of 22,100 BTUs. I have heard not to oversize mini split heat pumps because they will lose efficiency and that incorrect sizing can also lead to the condenser becoming a block of ice. Is the only solution to install inefficient back up electrical baseboard heating or massively oversizing the unit? I do not have natural gas available. I would appreciate any insights.
Thanks and keep up the good work!
House specs:
– Vented Attic R-49 unfaced fiberglass batts in the floor joists with Membrain vapor retarder on the underside
– Walls 2×6 24oc studs with taped sheathing and R-23 Mineral Wool Batts, Membrain vapor retarder interior side
– Full unconditioned basement 2″ R-13 foil faced polyiso cut and cobble to the interior foundation and rim joists with R-13 unfaced fiberglass batt insulation in stud cavities.
– Caulk and foamed double pane windows and insulated fiberglass doors with storm doors.
![]() |
![]() |
![]() |
Related links:
Question 2: Is there an adhesive I can use to connect the back of existing plaster lath to new wall studs?
Appreciate all you do!
Related links:
Question 3: Why is there another layer of plater and lath buried in the walls of our old house?
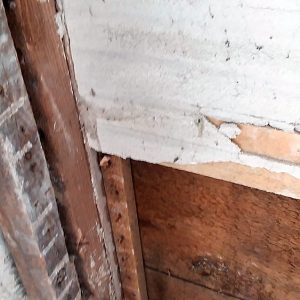
Andrew in Wisconsin writes, Hello All, Here is the first of many questions about our new farmhouse. We are gutting everything down to the studs due to water damage and mold. We are coming across lath and plaster within the stud cavities on both the first and second floor exterior walls. The house was very well built in 1900, was this some old school air barrier? Love the show!
Related links:
Question 4: Should I replace my failing cordless impact driver, or can I fix it?
Barbara writes, Greetings, I can’t get my trusty Milwaukee cordless impact driver to drive screws like it used to. Nowadays it’s more of an influencer.
I got a new battery, the highest amp hour choice at Home Depot. It cost over $50, more than half the cost of kits with new tools and inferior batteries. I thought it was wasteful to get more than just what I needed. I already have a good tool (I thought), plus a drill, charger, and a handsome bag. Now I’m thinking I should’ve gotten another kit.
I have killed two sets of batteries and most of my high frequency hearing with this tool. I got it in about 2006 after I gave up on the Makita impact driver I wore out building my house. I like this Milwaukee a lot. It fits my hand. I don’t like the ones with massive batteries that let it stand up. Too heavy. Should I get a new one just like this one? Wasn’t there some new technology that was supposed to make impact drivers quieter? Hydraulics or something?
Barbara follow up: Hey Y’all! I wanted to follow up on my question about the senescence of power tools. Matt suggested I try a new motor in my 12 year old 12 volt Milwaukee impact driver. So I did. I’ll be damned if that didn’t work a treat! It can snap the head right off a sheet metal screw again!
I did some more research into the physics of what exactly is happening in an aging motor. As far as I can tell the windings in the motor can have a failure of the insulation, get crammed with carbon dust or other conductive crud which lowers the resistance and pulls more current from the battery. (Seriously, don’t use compressed air to blow out a motor housing) All these extra amps are burned up as heat instead of turning into torque. This is basic Ohm’s Law logic. Motors are supposed to have a really high insulation resistance. When it starts to fall off then the motor no longer does the same amount of work with the given voltage. Apparently. None of the sources I found come right out and say this. But that’s the manifestation of the issue for me in particular. My research did reveal that the smell I associate with my grandmother’s old Sunbeam mixer creaming butter and sugar for pound cake is actually ozone and vaporized graphite. When my impact driver started making that smell it made me hungry for pound cake, but in fact it should’ve told me the brushes were breaking down. I always thought worn brushes manifested as an on/off problem. Apparently this other failure mode is also common.
There’s a film that forms on the commutator made of copper and carbon and water vapor. It requires the exact right amount of current and humidity to make this protective film that is constantly broken down and reformed. I expect my very humid climate and only using my tool occasionally made it prone to over-filming which lowered the resistance even more, burning off even more of my current as heat, running down my battery really fast without even delivering enough torque to get the job done. And also making that smell that makes me think of butter and vanilla.
I have a lot of tools now that are brushless, substituting permanent magnets and microcontrollers for carbon contacts. I will miss the sense memory of my grandmother’s kitchen, but I don’t have a lot of patience for a screw that won’t pull the work together.
When Matt and I were discussing the new Surge impact drivers that are quieter with less vibration I found a deal on the 18V set that came with a free mud mixer. I had a 5 gallon bucket of paint to mix and wanted it so bad! But I decided to buy the motor ($$) instead of the kit ($$$). That is when I had the brilliant idea to mix paint with my drill press, which I also emailed you about. Since nobody emailed me to warn me to absolutely not do that I went ahead and tried it. It worked great!
It made for a way better video than the impact driver. That impact driver video is the first time I’ve used voiceover in a video. It makes me cringe, but I have to just put it out there and move on or I’ll never improve.
This paint mixing video is unlisted right now because I want to use it to promote my new YouTube series about fixing another mid-century aluminum trailer. (You can see the trailers at the end of the paint video.) I’m not ready to launch the bi-weekly Buck Rivet Report videos yet, but I was dying to share what it’s like to mix paint with a drill press. Mostly I’m so proud of myself for being able to find that mixing paddle. I bought it 24 years ago but was never able to use it because my drill didn’t have a big enough chuck. It still had the zip tie from the tag on it.
My dad gave me that drill press a few weeks ago because I wanted something slow to use with a nylon brush on weathered wood for an art project. He got a new better drill press with electronic speed control. Anyway, the aluminum trailer was in my shed and I had to get it out to make room for the drill press. Everything cascaded from there. Painting the shed, running power to the shed, restoring the trailer. You know how it is. It could be years before I get back to that artwork.
Anyway, thanks for the tip, Matt!
Related links:
- Cordless Drill Repair Parts (eReplacementParts.com)
End Note:
KDKA Investigates: Siding Is Melting Off Nearly 50 Homes In South Fayette
The media relations manager pointed KDKA’s Meghan Schiller to research showing the focused rays can reach 200 degrees: more than enough to melt any nearby plastic, like siding, or as the homeowners showed us — the safety covers on the posts of the family’s trampoline.
“You just need to fix this and let everybody get on with their lives. You just need to fix it,” said Fuselier.
We called Ryan Homes, the developer of the neighborhood, to find out if they plan to help these nearly 50 homeowners.
A spokesman for NVR, Inc. the holding company that owns Ryan Homes, told KDKA’s Meghan Schiller “no comment” and said it’s company policy to not speak to reporters about anything.
But wait there’s more…
A month after filing a lawsuit against the stars of HGTV’s “Windy City Rehab,” a Chicago couple is now pushing for the show to be pulled off television permanently. The couple, who purchased a $1.36 million home featured on the reality television program, claim they were “deceived into thinking the hosts were experts in their fields,” the Chicago Sun-Times reports.
From Remodeling.com: “Attorneys for homeowners James and Anna Morrissey cite the Illinois Consumer Fraud and Deceptive Business Practices act in a motion to add Discovery, the parent company of HGTV, to the lawsuit against “Windy City Rehab” stars Allison Victoria and Donovan Eckhardt. The filing claims the episode represented “the renovation of the property was complete and was of the highest quality.” However, the homeowners said within a day of moving into the home, issues were discovered, including major leaks, poorly installed windows, and defective and shoddy work.”
If you have any questions you would like us to dig into for a future show, shoot an email our way: [email protected].
If we use your question we’ll send you a FHB Podcast sticker!
#KeepCraftAlive
KeepCraftAlive hats help celebrate the value of true craftsmanship–plus 50% of all proceeds from every hat sold go to the #KeepCraftAlive Scholarship Fund, supported by Fine Homebuilding and SkillsUSA.
Buy a #KeepCraftAlive hat or t-shirt
This episode of the Fine Homebuilding podcast is brought to you by ZIP System building enclosures.
By creating the integrated sheathing alternative to “layered” roof and wall assemblies, ZIP System sheathing and flashing options provide a streamlined approach to exterior water, air and thermal management. Did you know ZIP System has been on the market for over 10 years and not only comes with a 180-Day Exposure Guarantee and 30-Year Limited Warranty, but decades of research from the scientists and innovators at Huber Engineered Woods. Learn why so many building teams have make the switch to ZIP System building enclosures and how to get it on your next project at the new ZIPSystem.com.
Also brought to you by Danner:
If you believe in timeless ideas like quality, craftsmanship, and blazing your own path, I want to introduce you to our friends at Danner who sponsor this podcast. A Pacific Northwest original for over 85 years, Danner makes boots for people with purpose in their step. Boots like the new Steelyard family—featuring 8 different models with game-changing comfort, legendary durability, and performance features for any jobsite. Earn a pair and join the family at Danner.com.
Also brought to you by Benjamin Obdyke:
Benjamin Obdyke would like to use the special occasion of our 150th anniversary to thank the nuisances that builders and homeowners despise. Our premium products protect from those pesky things like rain, snow, UV rays and the neighbor’s sprinkler system. Take HydroGap, a drainable housewrap that eliminates moisture from your wall assembly. Or the new InvisiWrap UV, an all-black WRB, perfect for long-term moisture protection behind open joint siding. Come hang out with our awesome team and see our sexy new solutions at JLC Live, booth 311.
Fine Homebuilding podcast listeners can now get 20% off anything in the Taunton store, including the Renovation 5th Edition.
Use the discount code FHBPODCAST to take advantage of this special offer.
We hope you will take advantage of a great offer for our podcast listeners: A special 20% off the discounted rate to subscribe to the Fine Homebuilding print magazine. That link goes to finehomebuilding.com/podoffer.
The show is driven by our listeners, so please subscribe and rate us on iTunes or Google Play, and if you have any questions you would like us to dig into for a future show, shoot an email our way: [email protected]. Also, be sure to follow Justin Fink and Fine Homebuilding on Instagram, and “like” the magazine on Facebook. Note that you can watch the show above, or on YouTube at the Fine Homebuilding YouTube Channel.
The Fine Homebuilding Podcast embodies Fine Homebuilding magazine’s commitment to the preservation of craftsmanship and the advancement of home performance in residential construction. The show is an informal but vigorous conversation about the techniques and principles that allow listeners to master their design and building challenges.
Other related links
-
- All FHB podcast show notes: FineHomebuilding.com/podcast.
- #KeepCraftAlive T-shirts and hats support scholarships for building trades students. So order some gear at KeepCraftAlive.org.
- The direct link to the online store is here.