Podcast 247: Insulating Rim Joists, Installing Batt Insulation, and Getting Schooled in Building Science
Rob, Kiley and Patrick hear from listeners about poison ivy and minisplits before taking questions on spray foaming rim joists, insulating from the outside with batts, and air sealing a house with second-story cantilevers.
Follow the Fine Homebuilding Podcast on your favorite app. Subscribe now and don’t miss an episode:
![]() |
![]() |
![]() |
![]() |
Randy writes with his recipe for a homemade poison ivy cure. Joseph shares some thoughts on minisplits. Ken wants to know what kind of foam for his home’s band joist. Sean asks if he can install batt insulation and a vapor barrier from the outside. Adam asks for guidance on insulating and air-sealing his unusually-constructed house and AJ asks if the team knows of a complete building science curriculum.
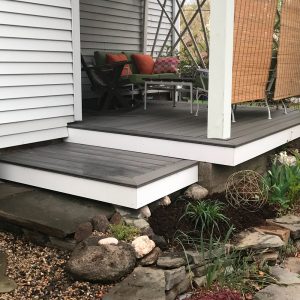
Editor Updates:
Kiley: Weed-whacking
Rob: Side porch step
Jeff: Oven issues
Patrick: Liam’s bedroom, truck brakes
Listener Feedback 1:
Randy from North Carolina writes: Hey FHB podcast folk, I always enjoy your banter (oh…..uh…..and the “practical advice” too)…..LOL
In episode 176 I heard the discussion about Matt having an altercation with Poison Ivy, and the Zanfel/Tecnu/GoJo approach didn’t seem to help. I’m a lifelong victim of Poison Ivy also (I capitalize it out of karmic respect).
The MOST practical thing I discovered was divulged in an internet blog on “Poison Ivy Remedies”. It was posted by a person that led “hiking trips” for nature groups. On every hike they carried a spray bottle filled with household AMMONIA diluted at 9:1. The allergen (urushiol) in the “Poison Ivy/Oak/Sumac” family is mildly acidic, and also oily. Theoretically the diluted ammonia solution instantly neutralizes the acidic urushiol while also dissolving the oil to help it release from clothing/tools
I have used this approach for the past 15+ years and have had zero rashes. I must caution that I am also EXTREMELY careful to avoid contacting Poison Ivy in the first place. Therefore I have the age old problem of “how do you PROVE something that did not happen?” (Sorry, my past rashes were so annoying that I’ve never taken the scientific approach by intentionally rubbing Poison Ivy on my skin and then treating it with ammonia to ‘prove’ it works).
I’m not a chemist or a dermatologist, so “use this with caution on your clothing, boots and tools that may have contacted poison ivy”. I’m sure ammonia is “not recommended” for direct skin contact by the medical community, so make your own decisions in that regard and “for sure” don’t inhale the stuff.
The other option to try as an acid neutralizer is the much safer Bicarbonate of Soda (aka “baking soda”). I’ve never tried soda because the 9:1 diluted ammonia has been effective thus far, and I had it “available” the first time I needed to treat something (but had “no baking soda” in the house on that day).
Lastly, the “time before treatment” MATTERS. I read one dermatology study that said 50% of the urushiol had already penetrated the skin in 10 minutes. After 1 hour, it was basically 100% penetrated. In other words “act fast to avoid the rash”. The study also indicated that past resistance does not guarantee future resistance: similar to uncured epoxy reagents, repeated exposure can lead to a developed sensitivity where none existed in the past.
Apologies for the long note, but as a long-time viewer of FHB podcasts I know there’s usually a discussion afterwards of “I wonder if the person tried THIS, or THAT……..what about the OTHER info?”. This is not a criticism of the staff……..I usually react to snippets of “advice” from “anecdotal” sources in the same way.
Keep up the good work. I’m a long-time viewer, and an even longer-time subscriber!
Listener Feedback 2:
Long time listener writes: I often hear you talk about the wonders of a mini split system and I want to provide some of my experiences.
I would say it is not the panacea of HVAC. We have a tight efficient house in central Texas. The HVAC was designed for July/August days where delta T can be 35° (110° and humid outside). Our issue with the mini split is on mild winter days when we just need a little heat. The Mitsubishi units have a minimum operating output (I think 6000 BTUs) that exceeds the requirements on these days. We go to bed with the thermostat set at 68 and by morning the temp is mid 75 because the unit can’t go to zero output. We end up just not heating the house because I’d rather sleep cold than wake up hot. Also, in spring / fall, one day it might be 85 outside and the next day 55. We have to run around and switch all the units from cooling to heating.
I know, first world problems, but we are in the beginning stages of building a new house and we are going back to central forced air.
I lived in Norwich for 4 years and don’t miss your winters.
Take care from the Lone Star State!
Question 1: Should I use open-cell or closed-cell spray foam to insulate a rim joist?
Ken from NJ by way of NH writes, Hi, Really enjoying the podcast, especially since I have more free time on my hands these days. As a private school teacher and part-time carpenter, I am able to relocate to NH and continue renovation work on our house, checking off jobs much faster than if I had stayed in NJ. So far I have installed the kitchen boxes (Ikea) and most of the drawer fronts (Plykea). Also gutted a bathroom, painted two rooms, installed a shower pan, lots of trim, and expecting a door delivery tomorrow.
Upcoming over the next few weeks – more painting, running baseboard, cable railings on the deck. I really enjoy the part of the show where you each talk about the projects you are working on in your own houses. Patrick’s new windows came out great.
We are teaching our classes via Zoom and have found the new normal to be very do-able, at least for this school year. Wouldn’t want to do it forever though.
My question has to do with the FHB white paper on insulating the rim joist with Versi-Foam. I’ll get this one done this summer – no need to do it right now but do I use closed-cell or open-cell? I understand the difference but which is right for my heating climate. I have a full cellar which is pretty dry, unconditioned space and has our oil-fired heating boiler (Superstore for hot water) and laundry in it. Eight foot uninsulated ceiling (no barrier there) and yes I believe there is a vapor barrier under the cement floor as the house was build in 1999 and that was probably practice here in southern NH. The foundation was poured concrete and it looks like it was ICF since there is 3” of foam panels both inside and outside the foundation. Does it even matter if I use open or closed cell on the rim joist?
Lastly, do you ever invite regular folks on the show (hint hint). Given how we’re all working separately these days, it might be fun to have a regular guy on the show, even if he has been reading FHB since the 90’s hahaha. Take care and would love to know if any of you have used the Versi-foam kits in your houses.
Related links:
Question 2: What’s an affordable way to insulate an old home from the outside?
Sean writes, Hi Crew, I enjoy the podcast and I’m thrilled we’ve tabled the air sealing conversations for a bit. My company is starting a renovation on a house in Newtown. It is a 1950’s 2300 square foot cape. I bought the house as a foreclosure and it is in need of a lot of work. It is 2×4 stud framed and the interior walls are all plaster (this scares me). The previous owner was a jack of all trades and replaced some of the siding, left some parts without siding, and left some of the original clapboard. My plan is to remove all of the siding and existing sheathing and re-sheath then side the house. My concern is the insulation is going to need to be replaced as well but I do not want to gut the plaster to properly re-insulate. Most of the interior walls are in good condition and definitely worth saving. Spray foam is out of my budget especially since with 2×4 walls I would need closed cell to satisfy code. I’m thinking of using unfaced rolled insulation installed from the outside, then installing a vapor barrier before the sheathing. Keep in mind budget is a concern here as well as time. I’d be open to any suggestions you may have. If you ever want a socially distanced tour the house is close to your offices feel free to reach out.
Related links:
Question 3: What’s the best way to insulate an old cape-style house?
Adam from Watertown (southern) Ontario writes, Hey gang, I love the podcast! I’m an electrician by trade but am in the middle of a remodel and addition of a house in southern Ontario that we intend to live in with our family of 4.
I will lay it all out for you and then ask a couple questions. I understand you probably can’t use all this but if you pick and choose any to answer on the show or privately, your vast experience would be greatly appreciated!
We are talking about a 2 Story house with block wall foundation and poured concrete floor in the basement. 2×10 4 ply laminated beam for main floor with 2×10 joists. 4” tongue and groove sub floor on the main floor. 2nd story is 2×8 joists with old crate planks (mostly 3/4”) for a subfloor that will definitely be replaced!
The roof is 2×4 rafters with collar ties and a knee wall. The upper floor overhangs the house 21” on all sides. So that’s the roof overhanging on the sides and the floor joists overhang front and back.
Outer walls are 2×4 framing with mostly 12” wide plank sheathing. Currently has vinyl siding which is to be replaced.
![]() |
![]() |
![]() |
![]() |
![]() |
![]() |
![]() |
Addition is to be a 20×24’ garage with bedroom above.
The biggest things I’m struggling with is exterior wall assembly. Initially I was planning for closed cell spray foam 3”. A new wrb on exterior, then exterior insulation and a vented rain screen. Likely with a cement board style horizontal siding. It has come to my attention that exterior insulation with cc spray foam is a no no because it can’t dry inward due to the spray foam. You all have any suggestions? I’d prefer not to lose more room on the interior otherwise flash and batt would work well I think. Also, am I better with peel and stick wrb or not? I’m concerned with the peel and stick sticking to the old planks with so many seams. It would provide a good air barrier though. What are your thoughts on header hangers to save on wood around windows and add more insulation? Second biggest problem is leveling the main floor. It varies up to 1 1/4”. The 2×10 joists are attached to the beam with a square cut out and sitting on 2×4. It seems as though they are sagging at the attachment point. The only thing I can come up with is to detach each joist, sister a small piece and reattach it to the beam with a double joist hanger. Thoughts? If I go this route how long would the sistered pieces need to be? There are a few spots on the subfloor to patch and I was thinking about attaching new subfloor sheathing over the existing after the patches are in. Do you think that’s a good idea? If so should I screw to the old subfloor or to the joists below. The intention is to have engineered hardwood flooring.
Last, the sloped ceilings on the 2nd floor. I intend to strap an extra 2” on the existing 2×4 giving a 6” cavity for cc spray foam. The roof sheathing is 12” wide 3/4“ thick planks. Is there anything to watch out for or is there a better way to insulate? Where the slope meets the outer walls it overhangs. Is it better to spray the overhang and soffit or put up a backer board flush to the sheathing and essentially extend the wall to the sloped ceiling and then spray foam? Any other ideas?
Thanks so much for all your hard work in an amazing show! It provides me with so much learning and entertainment while working and driving!
Related links:
Question 4: What’s the best way to learn more about building science?
AJ writes, Heya! You guys have been doing a great job with the remote podcasts and I’m greatly enjoying the Pro Talk podcasts as well.
I just listened to the episode with Peter Yost and one question that Patrick brought up is something I’ve been curious about for a long while: where can you learn accurate info on building science? I feel the genre is piecemealed. I’m thirsty for info on it, but my learning comes from scattered articles – and as mentioned, very few schools are teaching it. It would be wonderful if there were an online course. Maybe Peter can help develop it?? 🙂 Building Science Corp??
I’m currently reading Buildings Don’t Lie (from one of your podcaster’s suggestions) and it’s an excellent source of info. Joe Lstiburek is coming to my area this fall for a talk, but who knows if it will be cancelled. He might be a good guest.
A couple of other suggestions for guests on pro talk is Dr Decks and someone who does blower door tests / energy audits discussing their findings and common mistakes in builds.
Thanks for all you do!!
Related links:
END NOTE:
Fancy discussion
If you have any questions you would like us to dig into for a future show, shoot an email our way: [email protected].
If we use your question we’ll send you a FHB Podcast sticker!
#KeepCraftAlive
KeepCraftAlive hats help celebrate the value of true craftsmanship–plus 50% of all proceeds from every hat sold go to the #KeepCraftAlive Scholarship Fund, supported by Fine Homebuilding and SkillsUSA.
Buy a #KeepCraftAlive hat or t-shirt
This episode of the Fine Homebuilding podcast is brought to you by Danner.
If you believe in timeless ideas like quality, craftsmanship, and blazing your own path, I want to introduce you to our friends at Danner who sponsor this podcast. A Pacific Northwest original for over 85 years, Danner makes boots for people with purpose in their step. Boots like the new Steelyard family—featuring 8 different models with game-changing comfort, legendary durability, and performance features for any jobsite. Earn a pair and join the family at Danner.com.
Fine Homebuilding podcast listeners can now get 20% off anything in the Taunton store, including the Renovation 5th Edition.
Use the discount code FHBPODCAST to take advantage of this special offer.
We hope you will take advantage of a great offer for our podcast listeners: A special 20% off the discounted rate to subscribe to the Fine Homebuilding print magazine. That link goes to finehomebuilding.com/podoffer.
The show is driven by our listeners, so please subscribe and rate us on iTunes or Google Play, and if you have any questions you would like us to dig into for a future show, shoot an email our way: [email protected]. Also, be sure to follow Justin Fink and Fine Homebuilding on Instagram, and “like” the magazine on Facebook. Note that you can watch the show above, or on YouTube at the Fine Homebuilding YouTube Channel.
The Fine Homebuilding Podcast embodies Fine Homebuilding magazine’s commitment to the preservation of craftsmanship and the advancement of home performance in residential construction. The show is an informal but vigorous conversation about the techniques and principles that allow listeners to master their design and building challenges.
Other related links
-
- All FHB podcast show notes: FineHomebuilding.com/podcast.
- #KeepCraftAlive T-shirts and hats support scholarships for building trades students. So order some gear at KeepCraftAlive.org.
- The direct link to the online store is here.