A Beginner’s Guide to Heating Systems
No matter what fuel you choose, look for a heating appliance that will use it efficiently.
With the results of a newly minted Manual J calculation or its equivalent in hand, a homeowner should have a good idea of how much energy it will take to stay comfortable on the coldest days of the year. As energy steadily seeps out of the house, the heater is pumping new energy in, balancing heat loss with heat gain. Yet by themselves the heat loss numbers that you or someone else has jotted down—so many British thermal units (Btu) needed per hour—do very little to guide you in choosing exactly what kind of heating equipment you should buy.
Any number of devices will do: a natural gas furnace, a boiler that runs on fuel oil, a heat pump, a direct-vent propane heater, or a woodstove or pellet stove. There is no one ideal option that will work for everyone in every situation. Advocates for particular heating systems are everywhere and always willing to give you an earful. Where to start?
It might help to break the decision down into manageable chunks: How much will it cost to buy the equipment initially? How much will it cost to operate it over time? Who will maintain the equipment, and repair if when it inevitably needs service? How will the equipment mesh with future decisions around the house, such as the addition of a renewable energy source or a building renovation? Will the floor plan of the house have a bearing on the heating system?
One of the earliest and biggest barriers to cross is whether you should rule out a combustion appliance. Let’s call it the Carbon Rubicon. As scientists give us a greater appreciation for the impact of carbon emissions on the climate and the environment, a growing number of activists are pressing for stricter controls on the use of natural gas. In some communities around the country, lawmakers have enacted bans on new gas connections to buildings. This is true even in some larger cities, such as San Jose, California, the 10th largest city in the U.S.
Carbon is not a topic that all builders or homebuyers care very much about. For example, the National Association of Home Builders, a powerful trade association for residential builders, has little to say on the topic. But, as the connection between residential energy use and overall carbon emissions becomes ever clearer, some residential designers have essentially stopped specifying fossil fuel heating systems, especially those who work on high-performance houses. “Yes, I try to talk clients out of fossil-fuel burning equipment,” Michael Maines, a residential designer in Maine, said in an email. Although some homes need gas-fired tankless water heaters, Maines said, “it’s been many years since I’ve spec’d a fossil-fuel burning appliance for primary heating. Some clients still want gas ranges or fire places; I try to talk them into better alternatives but tend to focus efforts elsewhere.”
Carbon emissions are but one of a number of considerations. Choosing a heating system is complicated and important. There is no one answer that meets every situation.
Comparing the price of different fuels
Even those who see an all-electric future may not be able to make that jump now, or may need supplemental heat that burns oil, propane or natural gas. In that case, a comparison of local fuel prices is a good place to start. Let’s crunch some numbers.
Different types of fuel are sold in different units, as the U.S. Energy Information Administration explains at its website. It’s not helpful to compare the cost of a gallon of propane to a cubic foot of natural gas, so some kind of conversion will be necessary. The agency suggests that the most useful comparison is the price of fuels based on their heat content—expressed as dollars per million Btu of heat content. The formula goes like this:
(Fuel price per unit) divided by (the heat content per unit) x 1,000,000
Consumers should be able to check local energy prices online. In Maine, where I live, the Governor’s Energy Office regularly posts average prices for a variety of fuels, including natural gas, fuel oil, propane, kerosene, cord wood, and wood pellets. The office even does the math for you. In late March, natural gas was the best heat bargain, with prices at $11.71 to $16.31 per million Btu, followed by cord wood ($12.50), heating oil ($16.15), wood pellets ($16.24), kerosene ($20.74), propane ($27.04), and baseboard electricity ($46.31 to $54.22). These comparisons were based on prices current at the time, and market forces affect different fuels in different ways.
The math changes completely in a state where electricity prices are typically much lower. If you lived in Washington State, according to the EIA, you’d be paying as little as 9.42 cents per kWh. Natural gas in Washington State was $10.24 per 1,000 cubic feet, or $9.88 per million Btu, using the formula above, much cheaper than the upper range of prices in Maine.
Other values that may come in handy for calculating the relative costs of heating with various fuels:
- 1 gallon of heating oil (sulfur content 15-500 parts per million): 138,500 Btu
- I cubic foot of natural gas: 1,036 Btu
- I gallon of propane: 91,333 Btu
- I kilowatt of electricity: 3,412 Btu
Now, factor in appliance efficiency
The cost of fuel is one thing. How efficiently the appliance uses the fuel is another consideration. The higher the efficiency, regardless of the metric used, the less fuel will be used to produce a given amount of heat.
Efficiencies are measured in different ways, depending on the appliance. For combustion appliances, the benchmark is the Annual Fuel Utilization Efficiency (AFUE). This is a measure of the average efficiency over a heating season, the ratio of energy output to energy input. For example, a modulating, condensing gas furnace with an AFUE of 98% converts all but 2% of the energy in the fuel to heat that can be used in the house. What’s left is what goes up the flue.
According to the Department of Energy, AFUEs for furnaces (forced hot air systems) ranges from 59% to 98%. Boiler efficiencies go from 50% to 90%.
Heat pumps, which are devices that move heat from one place to another but do not burn fuel directly, are rated differently. Heating efficiency can be described as the Heating Season Performance Factor (HSPF), which is the heat output in Btus over the heating season divided by the amount of electricity used, in watt-hours. The result is Btu/watt-hr.
Another way of describing efficiency is the Coefficient of Performance (COP). This is the ratio of how much energy the heat pump consumes to the heat energy it produces. This value is not a constant. Heat pumps don’t work as well in very cold weather as they do in milder temperatures, so the COP will go up and down over the course of a heating season. The COP can range up to about 4, four times the efficiency of a resistance electrical heater. But when the outdoor temperatures are very low the COP can fall sharply.
Buyers also can look for Energy Star qualified appliances. Energy Star is a federal program used to rate the relative performance of everything from houses to furnaces. In order to earn an Energy Star rating, a product has to show higher efficiency when compared to similar products on the market. Currently, a furnace must have an AFUE of 90% or more to be Energy Star qualified in the southern tier of the U.S., 95% in the northern part of the country. Furnaces and boilers running on fuel oil must have an AFUE of 85% or better.
How much difference does it really make? Over time, quite a lot. For a house that uses 750 gallons of fuel oil per year, a boiler with an AFUE of 85% will use 112 gallons less than one with an AFUE of 70%. That would add up to about $281 a year at current prices. The difference would, of course, change with the price of fuel.
Heat pumps are a high-performance favorite
Heat pumps were once mostly a fixture of the Southeast where winter temperatures are mild and summers are hot and humid. At one time, air-source heat pumps needed auxiliary resistance coils when temperatures dropped much below 40°F. Led by such companies as Mitsubishi and Fujitsu, manufacturers went on to develop air-source heat pumps that could operate efficiently in below-zero temperatures. The vastly improved technology has helped make heat pumps, especially a kind of air-source heat pump known as a ductless minisplit, a big player in the space heating market—even in cold regions like New England.
For architects like Chris Briley, whose Portland, Maine, firm Briburn specializes in high-performance designs, heat pumps are one of the first options to consider. “Heat pumps are our go-to,” he said. “The last 10 years have just been a revolution for heat pumps.”
A heat pump extracts heat from the air or water and moves it somewhere else, without burning any fuel directly. A heat pump with a COP of 4 gets 4 kW worth of heat for every 1 kW of electricity it consumes. That’s four times as efficient as an electric baseboard heater. Efficiency falls off sharply in colder temperatures, but some heat pumps can still produce heat when temperatures are well below zero. Mitsubishi Electric Trane US, for example, says its Hyper-Heating Inverter (H2i) units provide up to 100% of heating capacity at 5°F and up to 76% of capacity at -13°F.
Heat pumps do double duty as both heating appliances and air conditioners. Running in reverse, a heat pump pulls heat out of the house and dumps it into the air (an air-source heat pump) or the ground (a ground-source heat pump) in the summer. Unlike a conventional furnace or boiler that burns a fossil fuel, a heat pump isn’t a back-drafting risk and it doesn’t contribute directly to carbon emissions.
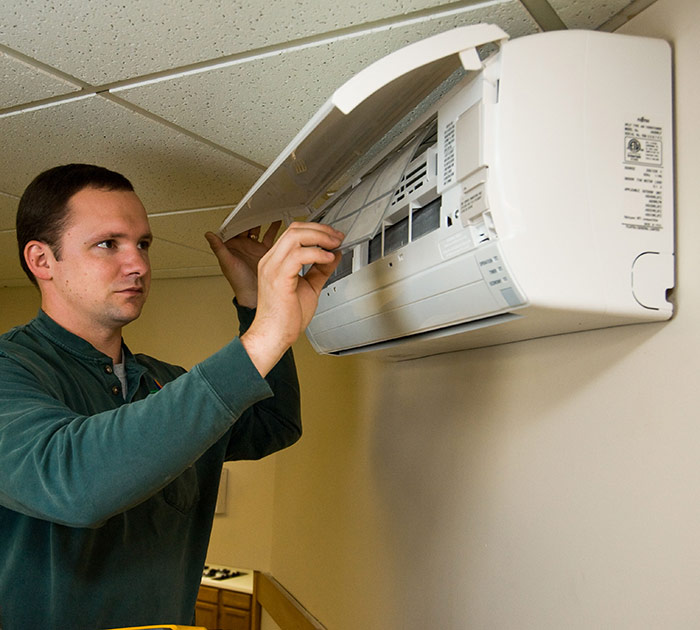
Air-source heat pumps come in several versions. They can be used with a conventional system of ducts that distribute conditioned air throughout the house, as a gas-fired furnace would do. They also come in smaller packages (ductless minisplits) that include an outdoor compressor and one or more indoor heads that send conditioned air directly into the room without the need for ducts. Ducted minisplits are a compromise. They provide conditioned air to a few adjoining spaces with a limited amount of ductwork.
Heather Buchicchio, director of product marketing for Mitsubishi Electric Trane, said in an email that field studies for the Center for Energy and Environment in Minnesota found ductless systems record higher COPs than ducted systems. COPs ranged from 4.0 to 4.5 during the shoulder season and from 1.0 to 1.5 during the coldest times of year.
Heat pumps also may feature what manufacturers call “inverter technology” in which the outside compressor converts AC to DC and modulates the amount of power to meet heating demands more precisely than a fixed-speed compressor in a traditional system. Those one-speed system, Buchicchio said, are either on or off. “This can lead to unpleasant temperature swings as the system strains to maintain a constant temperature,” she said.
“Inverter-driven compressors, on the other hand, are always running in the background,” she continued. “adjusting speeds in real time. By ramping up capacity when needed, an inverter-driven compressor provides a more accurate, on-demand approach to temperature control.”
Designers who specialize in very well insulated and air-sealed houses like the high efficiency of ductless minisplits. When heating loads are very low, just a few indoor units can heat and cool an entire house, particularly when floor plans are open. Massachusetts builder Carter Scott popularized this approach in the high-performance houses that he built. This is cheaper than installing a conventional HVAC system with a fuel-burning furnace or boiler, a distribution system, and separate air conditioning equipment.
Ductless systems work best when an outside compressor serves only one or two cassettes inside. Beyond that, performance and efficiency can suffer, Briley says. “The more zones you have the more cassettes you have, the more refrigerant lines you have, the more manifolds you may have,” he said. “And we all know that multizone systems are still suffering from some of those efficiency issues. So all of a sudden your wicked efficient, wicked simple heat pumps system has just gotten way more complex and way more expensive.”
Ground-source heat pumps have high upfront costs
Ground-source heat pumps can draw heat from the Earth via tubing sunk in one or more wells, in a network of trenches, or even in a body of water like a pond or river. These heat pumps (sometimes mistakenly called geothermal systems) are more expensive than air-source heat pumps because of the excavation they require. System costs can top $40,000, and they must be carefully engineered if they are going to work properly. One plus is that underground temperatures are higher and more stable than outdoor air during the winter, and ground-source units are more efficient than air-source heat pumps—the COP is higher.
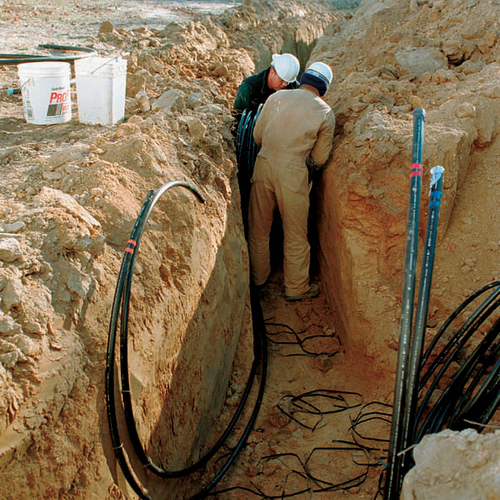
Wells are more common than trenches for heat transfer tubing because wells take up a lot less real estate. But if you have a really big back yard, the tubing can be placed in relatively shallow trenches.
Heating with a ground-source heat pump is less expensive than with an air-source heat pump, according to estimates provided by Ekotrope, an estimated $701 vs. $1,256 in a 2,000-square-foot Massachusetts home. But according to the Rocky Mountain Institute, the levelized cost of heat in dollars per million Btus was about $30 for an air-source heat pump and $35 for a ground-source heat pump in one study. (Levelized costs include both capital and operating costs over the lifetime of the equipment.)
[In both of these Ekotrope scenarios, heating with natural gas was even cheaper. What the future holds for the petroleum industry, however, is anyone’s guess.]
You’ll find both critics and boosters of ground-source systems. For a much more detailed look at this option, you might visit a series posted by Briley and fellow architect Phil Kaplan at the Green Architects’ Lounge at GBA, starting with Part 1.
Furnaces need ductwork
Gas-fired furnaces are the basic Chevys of the heating world. These central heating units distribute warm air through a network of ducts. Furnaces also can run on propane, fuel oil, and electricity. The same ductwork that distributes warm air in the winter can deliver cool air in the summer when a central AC unit is added to the system. Furnaces running on natural gas are very common and among the least expensive ways to heat a home (57% of U.S. homes use natural gas for heat, according to the Department of Energy).
Conventional furnaces are pretty simple. When the thermostat calls for heat, the burners are ignited, a blower motor is switched on, and a fan begins circulating warm air around the house. A return pulls cool air from the house back into the furnace’s heat exchanger to be reheated and recirculated. These units are a minimum of 80% efficient. The problem is that it’s all or nothing. A one-stage furnace is on or off: gusts of warm air followed by silence and gradual cooling. Also, furnaces are difficult to zone so different parts of the house can be set to different temperatures.
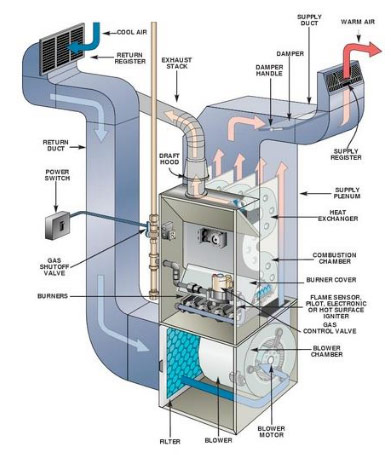
Newer furnaces are very efficient, with AFUEs of up to about 98%. At that rating, only 2% of the fuel is wasted. These condensing furnaces have a secondary heat exchanger where a few more Btus of heat are wrung out of the exhaust gases. Flue gases are so cool that they can be exhausted in a plastic pipe; the house doesn’t need a conventional masonry chimney or metal vent. Most models, according to the U.S. Department of Energy, are direct vent, meaning they do not need indoor air for combustion. This is an advantage on two levels: direct-vent devices can’t backdraft (a dangerous situation where low pressure inside the house pulls combustion gases back down the chimney), and dusty conditions inside the mechanical room won’t gunk up the furnace.
Furnaces that can modulate the level of the flame are another step forward. Instead of running at one speed, modulating furnaces are capable of running at lower heat outputs. So, they cycle on and off more often, but the temperature stays in a tighter range. The idea is that the house will be more comfortable because heat doesn’t fluctuate as much.
Furnaces typically have heat outputs down to about 40,000 Btu per hour. This was fine when houses were under-insulated and poorly air-sealed, but that’s way too much for a well-insulated home. The lack of a low-output furnace was frustrating to designers of energy-efficient houses, but now a Canadian company makes a modulating model with a rated output of as low as 6,000 Btu/h, as Martin Holladay describes in this article.
There are two things to keep in mind with a forced-air system. One is that leaky ducts are a problem, not only a source of wasted energy but also a potential source of contaminated air that can be drawn into the system from a dusty attic or moldy crawlspace. Ducts should be sealed with mastic, and run in a conditioned space. The other issue is that the blower can be an energy hog. As Allison Bailes explains in this article, furnaces with the same rated heat output can show big differences in the amount of electricity they draw for the blower. That can turn out to be a significant hidden cost.
Hot water and steam boilers
Boilers heat water instead of air and transfer the heat to the house via radiators, either baseboard, modern Euro-style wall mounts, or the old fashioned sectional cast iron versions, or tubing installed in the floor (radiant floor systems). Like furnaces, boilers run on several fuels and are now available in modulating-condensing units called mod-cons with efficiencies of 95% or higher. Boilers are still popular in some parts of the country, but overall account for a small percentage of all heating systems installed in the U.S.
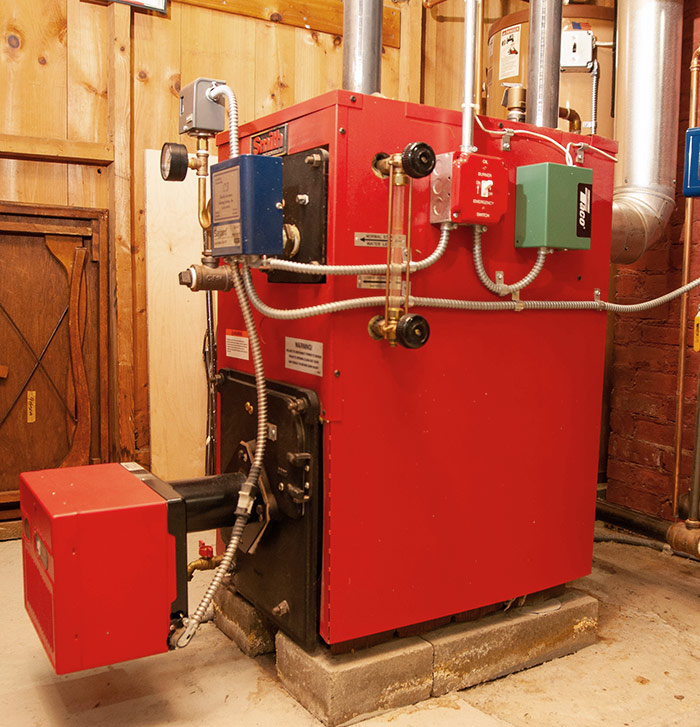
Boilers have a couple of advantages over furnaces, and also some disadvantages. On the plus side, it’s simple to create different heat zones in a house with a boiler by installing pumps or valves that direct hot water only to designated areas instead of the entire house. Each zone has its own thermostat. Also, the boiler can provide domestic hot water with an indirect tank, which in effect makes the water heater its own heating zone. Boilers, however, are usually more expensive than furnaces, and they can’t be used to provide air conditioning because they don’t have any air ducts.
Most radiators are designed for hot water, but some are still set up for steam. One-pipe steam radiators use the same pipe to direct steam to the radiator and carry condensed water back to the boiler to be reheated. These older systems run at very low pressures—just a pound or two—and use steam vents to regulate heat output at the radiator. In a more modern two-pipe system, one pipe carries steam to the radiator and the other removes the condensed water.
Heat also can be distributed through tubing, typically in the floor. In a radiant-floor system, tubing is cast directly into concrete, set in grooves of specialty subflooring, or stapled to the bottom of the subfloor from below. Tubing is usually a tough plastic called PEX, shorthand for cross-laminated polyethyene. Radiant-floor systems are expensive. They also are very quiet, and because there are no radiators the heating system is essentially invisible.
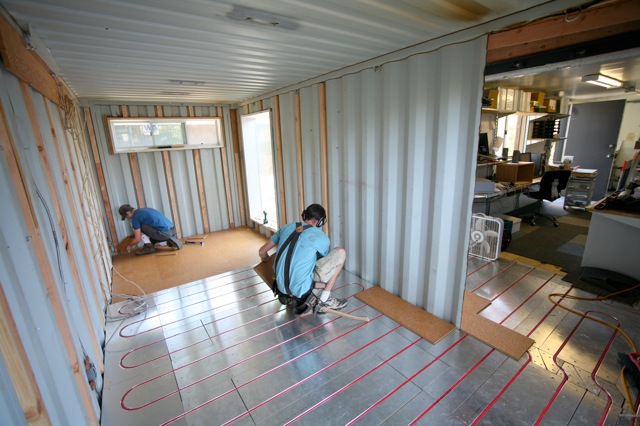
People sometimes think that radiant floors will be pleasantly warm during the winter. That’s usually not the case in a tight, well-insulated house. By the time the floors are noticeably warm, the house is likely to be way too hot—hot enough to throw the windows open. One reason is that water temperature is relatively low, much lower than is needed for a hot-water radiator. The best fit for radiant-floor heating is probably a house that isn’t that well insulated. In a small, tight house a radiant-floor system would probably be overkill.
The same tubing that warms the house in the winter also can be used to cool it off in summer—at least in theory—as long as the relative humidity is kept low enough so moisture doesn’t condense on cooler surfaces. Radiant cooling is uncommon. This issue was the topic for a Q&A Spotlight a few years ago.
Wood and pellet stoves
Wood stoves are still a fixture in many rural areas where firewood is easy to get. Prices have risen in the last decade but firewood may still compare favorably to other fuels, and homeowners lucky enough to have their own woodlots will have a relatively cheap source of fuel. Wood stoves can be good sources of heat in the shoulder seasons, and supplemental or backup heat in the winter. In New England, providing most or nearly all of winter heat with one or more wood stoves is not uncommon.
But there’s another side to this Norman Rockwellian portrait of country simplicity. Wood stoves need regular cleaning, may need a source of makeup air in order to work properly, and in a tight, well insulated house may produce too much heat. Wood stoves can cause problems for people with respiratory ailments, and the flue that carries away soot and smoke also represents a potential for back-drafting. If you’re not careful, creosote building up inside flues and chimneys is a fire hazard.
When local wood supplies are abundant, a good case can be made for using a wood stove—providing certain practices are followed. But as is the case with any type of heating appliance, it’s best to choose the most efficient model possible because it will make the best use of the fuel and lower emissions. The Environmental Protection Agency offers this guide for potential buyers; the New Hampshire Extension has this one. Just keep in mind there’s a learning curve to using a wood stove.
Pellet stoves are another type of biomass heater. Instead of firewood, these stoves use pellets of compressed wood. Pellet stoves don’t need the attention that a wood stove does; electrically powered augers move pellets from a hopper into the firebox at a rate determined by a thermostat. Pellet stoves also are designed to produce less ash than a wood stove, so they don’t need to be cleaned as often.
The environmental impact of using wood pellets is debatable. If they are manufactured locally from low-grade wood that normally would go to waste, there’s a good case for using them. But on a national scale, environmental activists in the Southeast are appalled by the practice of widespread forest clear-cuts to supply huge power plants in Europe.
Electric resistance heating
One of the great ironies of home heating would be the eventual return of electric baseboard heaters. When electricity was cheap, electric baseboard was appealing. Inexpensive and easy to install, baseboard heaters operate at near 100% efficiency.
That sounded pretty good until you could buy a heat pump with a COP of 3 or 4, the cost of electricity began to go up, and natural gas emerged as an abundant, low-cost fuel alternative. But it could still make sense under the right circumstances.
Houses with very low heating loads, a “Pretty Good House,” might be able to use electric resistance heat economically. For one thing, it’s easier to model because the efficiency is a known value that doesn’t change, Briley noted, and there’s no risk of a refrigerant leak or methane leak that would mar the advantages of a heat pump or natural gas appliance. As the cost of solar energy continues to fall, and house get tighter and better insulated, the math begins to look more interesting.
Briley says he hasn’t fully figured out whether a house in a cold region like Maine could rely on resistance heating economically. But, he added, “It’s interesting that this feature from the ’70s, which made no sense then, could totally make sense now.”
In the meantime, electric resistance heat is a good candidate for supplemental or spot use, such as a floor mat in a bathroom or a bedroom that’s a little cool at night.
Originally published on GreenBuildingAdvisor.com. Scott Gibson is a contributing writer at Green Building Advisor and Fine Homebuilding magazine.