A Guide to Choosing Insulation
Is there a "best" kind of insulation? There are many variables to consider, not just R-value.
Insulation is often chosen mostly on the basis of how well it stops the flow of heat—its R-value. Insulation with a high R-value—such as spray polyurethane foam or rigid polyisocyanurate—is at least twice as effective as, say, loose-fill fiberglass. Wall or roof assemblies with higher R-values typically cost more but translate into lower heating and cooling bills.
In reality, choosing insulation is rarely as simple as comparing R-values, and relying on R-values alone can be misleading and short-sighted. To be sure, the thermal properties of insulation are important, but builders and homeowners have many variables to consider:
- How much does it cost?
- How difficult is it to install?
- How available is it?
- How safe is it?
- Is it an air or moisture barrier?
- What are the environmental consequences of choosing a particular kind of insulation?
A good place to start is the International Residential Code (IRC), which spells out the minimum amount of insulation for basements, walls, and roofs. This information is summarized in a table (R401.1.2) that breaks down minimum R-values by application (where it will be used) and location (the climate zone where the house will be built). Take, for example, wood-framed walls. In climate zone 1, which encompasses the warmest areas of the continental U.S., R-13 insulation meets code minimums for exterior walls. If you live in climate zone 6 or 7, you will need insulation between the wall studs plus a layer of continuous insulation to control thermal bridging. The code offers two possible ways of doing that: R-20 insulation in the wall cavities and a continuous layer of R-5, or R-13 in the wall cavities plus R-10 of continuous insulation.
These values are code minimums for new construction, but many builders are aiming for better performance than that. Insulation for a “Pretty Good House,” a building with better-than-code performance, uses a simple formula for insulation summarized as “60-40-20-10.” It means R-60 in the roof, R-40 in above-grade exterior walls, R-20 in basement walls, and R-10 below the slab (these values are intended for houses in climate zone 6). These are not unbreakable rules but good approximations for a house that will be comfortable and less expensive to heat and cool than one that just meets code minimums.
If you’re shooting for Passive House certification, things get more complicated. First, there are two certifying bodies—the German-based Passive House Institute and the Passive House Institute U.S. (PHIUS)—each with its own rule book. Computer modeling is required to determine how much energy the building will use, at least on paper, so a designer can calculate how much insulation you would need to get there. The same kind of modeling process would be used to build a net-zero-energy home.
Those performance levels are not the norm. Still, the first question should be, “What am I trying to accomplish, and what are reasonable goals for the thermal efficiency of the building?” If you have an old house and are simply trying to cut your energy bills, that’s one thing. Anything is better than nothing. If you want to hang a Passive House plaque by the front door when you’re done, that’s something else.
R-value also comes into play in another way: how much room does the assembly allow for insulation? This question frequently pops up when someone is insulating an attic at the roofline—in other words, turning the attic into conditioned (heated and cooled) space just like the rest of the house. Rafters may not be deep enough to permit the use of insulation with a low R-value. This factor can drive the decision in favor of a type of insulation with a high R-value per inch even if there are environmental or cost tradeoffs.
When insulating an attic at the roofline, another question pops up: how vapor permeable is the insulation you plan on using? In some climate zones, the answer to that question helps determine what you should be using for insulation and how the assembly should be designed. Point being, R-values are a part of the mix, but not the whole deal.
How difficult is it to install?
Some types of insulation are ideally suited to installation by inexperienced owner-builders while other kinds of insulation require specialized skills and equipment. This is one reason that the most common type of insulation are fiberglass batts, which are not only inexpensive but also available at just about any lumberyard or big-box store. They’re also simple to install. Assuming the framing is built to a recognized standard (16 or 24 in. on center), the installer just cuts the batt to length and tucks it into the stud cavity. Batts that are faced with kraft paper can be stapled in place.
Batt insulation has to be worked around obstructions—plumbing and wiring runs, electrical boxes, and the like—and this complicates installation and potentially reduces its effectiveness. But at least in theory, batt insulation is very easy to install.
Things get a little harder with cellulose. The insulation is chopped newspaper or cardboard with some additives, nothing complicated here, but it requires a blower. Some retailers will rent you the equipment to blow loose cellulose into an attic, but these machines aren’t well suited to installing dense-pack cellulose into a wall cavity. Blowing cellulose to a consistent density of 3 or 4lb. per cu. ft. is not a skill that most homeowners have.
Installation becomes even more daunting when the insulation is spray polyurethane foam. Kits designed for DIYers are available, but in most cases spray polyurethane foam is installed by professionals who go to work wearing protective clothing and respirators for a reason. The two chemicals, toxic before they are allowed to cure, are shipped in separate containers and delivered to the spray gun in heated lines. There’s plenty of room for error even for a trained installer.
Complexity of installation is important in another way: the smaller the job, the better a simple solution looks. Suppose spray polyurethane foam looks like the best match for a job from a performance standpoint, but the area to be insulated is very small—such as a wall in a single, small room. In that case, it makes more sense to look for an alternative that is easier to use even if that means a marginal sacrifice in performance.
How available is it?
Some types of insulation are readily available. This category includes fiberglass batts, cellulose, spray polyurethane, and rigid foams, such as extruded and expanded polystyrene. Other types may be a special order or not available at all.
It seems obvious that if a particular kind of insulation isn’t available locally, you’d best pick something else. But sometimes builders or homeowners think they have compelling reasons to order something from afar because of its unique performance attributes. Wood fiberboard panels are one example. Some green builders like this insulation because it sequesters carbon, is completely recyclable, and is manufactured without toxic petrochemicals. The problem is that wood fiberboard insulation is not currently manufactured in North America. The best known brands come from Europe.
Shipping increases costs and comes with a carbon penalty. That’s certainly a factor, but builders also have to look forward. If they never look beyond what’s immediately available at the local lumberyard, the palette of available materials will never change. Materials with promise, such as hempcrete or wood fiberboard, may be hard to find now but they have performance characteristics that make them attractive to green builders. Demand equals greater market access over time. This is the theory behind the Living Building Challenge. It challenges architects to design buildings with rigorously curated materials in hopes that as interest in these approved products grows, they will be easier to find and less expensive than they are now.
Does it impede the flow of air or moisture?
Sometimes insulation can do more than one job. In addition to resisting the flow of heat, certain types of insulation are effective air barriers or moisture barriers as well. This can be a factor in deciding what type of insulation will work best, or how the insulation must be used in order to avoid problems.
Spray polyurethane foam provides a good example. It comes in two forms—open and closed-cell. Open-cell foam is the lighter of the two, at about 1/2 lb. per cu. ft. It has a lower R-value than closed-cell foam and is less expensive. When sprayed into a cavity, closed-cell foam—at about 2 lb. per cu. ft.—has a higher R-value and expands at a much lower rate than open-cell foam. But one of the most important differences has nothing to do with R-value or its density; it’s the material’s ability to block moisture. Open-cell foam is a good air barrier but not a good moisture barrier. Closed-cell foam is both an effective moisture barrier and air barrier. When open-cell spray foam is used to insulate the bottom of a roof deck to create a conditioned attic, it does not block the passage of moisture. When moist air strikes cold roof sheathing in the winter, water can condense there, and over time it can accumulate and cause problems in the form of mold or rot. In this instance, it would be wise to either choose another type of insulation, detail the insulation in such a way that moist air is not allowed to pass through the foam, or design a ventilated roof assembly.
Likewise, cellulose has many qualities that green builders like, but it is not a great air barrier. Even dense-pack cellulose installed in the roof will not completely stop the flow of air or moisture. Fibrous insulation such as fiberglass has the same problem. There are ways to deal with this, such as adding a separate air barrier or smart vapor retarder. And sometimes it doesn’t matter, as when a fibrous insulation is used in conjunction with another type of insulation or when an assembly is detailed to allow moisture to escape harmlessly. But vapor permeance is not something that a builder should ignore or be unaware of.
New construction or retrofit?
As a house is being built, and walls and ceilings are still open, a builder has a free hand to decide which type of insulation is best. Options narrow considerably when a renovator is dealing with as-built conditions and the house is not going to be gutted.
To use an obvious example, unless walls are open and accessible, a builder does not have the option of using fiberglass or cotton batts, even though either might have many of the necessary attributes for that application. This is why blown-in cellulose is such a popular choice for retrofits and weatherization projects. An installer can work from the outside, temporarily removing strips of siding, drilling holes in the sheathing and pumping in enough cellulose to fill the wall cavity.
When a homeowner is trying to upgrade or add insulation to an existing house, he or she may also run into the dilemma of not having enough room to use the preferred type of insulation. This is why builders may choose to use spray foam, even if they otherwise would prefer not to use it. The decision becomes a compromise between performance requirements and environmental objectives.
A related question is whether adding insulation will eventually do damage to the building. This comes up for owners of older masonry buildings in particular because as exterior walls become better insulated, the exterior masonry also becomes colder, wetter, and more susceptible to damage from continuous freeze-thaw cycles. Renovators in historic homes may also consider whether the insulation process is reversible—meaning, can the insulation be removed later without damaging the structure itself? In the case of spray foam, the answer is no. Once installed, that type of insulation is more or less a permanent fixture of the house, where loose-fill fiberglass or cellulose blown into an attic could, if need be, removed without doing any harm to the building.
What about environmental credentials?
This last category is becoming important to more builders, and there are several ways of looking at it. The most obvious is whether a particular kind of insulation is made from toxic materials, or is dangerous to handle. Foam insulation in all of its forms is manufactured from petrochemicals and various chemical ingredients, but when the insulation has cured (either in the factory where it was produced or in the house where it was installed) it is stable and inert. There are instances where this is not the case, as when spray polyurethane foam is mixed improperly, or when the foam burns in a house fire and emits toxic smoke. Some builders and homeowners avoid foam altogether because of what it’s made from. The New York City retailer 475 High Performance Building Supply is a vocal advocate of foam-free construction, and there are many others.
Flame retardants are added to foam insulation, but these chemicals themselves can be the subject of concern. U.S. makers of XPS and expanded polystyrene (EPS) have switched to a flame retardant called Polymeric FR and stopped using one called HBCD, a brominated flame retardant that was considered too dangerous. Polyisocyanurate insulation is treated with a flame retardant called TCPP, which is not classified as a chemical of concern by U.S. or European authorities, according to this polyiso trade group. But the issue underscores the tradeoffs we sometimes make in choosing materials that have the potential to benefit us (by saving energy) while exposing us to potential risks.
The blowing agents used to manufacture foam insulation have become a big issue for architects and designers worried about the global warming potential (GWP) of the materials they use. These chemical components of foam insulation are crucial, but they also have outsized environmental impacts, many hundreds of times that of carbon dioxide. Spray polyurethane foam and extruded polystyrene board have been two of the most egregious offenders, but manufacturers are beginning to use new generation blowing agents with substantially lower GWPs called hydrofluoroolefins. Some products already contain these blowing agents, and other manufacturers are likely to adopt them in the future as government crackdowns on older chemistry continue to pick up steam.
Many green builders consider cellulose to be an unusually benign type of insulation, like hempcrete or straw bales but more readily available. As noted, it’s made from shredded newspaper or cardboard and treated with borates for flame and pest resistance. Consequently, it gets good environmental grades.
The importance of carbon counting
Another emerging area of interest is embodied carbon. Why is it important? Research by Chris Magwood of Builders for Climate Action shows that the short-term effects of choosing building materials with low embodied carbon will do more to limit climate change than the long-term energy savings from building net-zero houses with carbon-intensive materials. In other words, carbon reduction over the short term is more important than long-term benefits of energy conservation.
Some types of insulation have very high levels of embodied carbon while others store carbon, and thus have a positive net effect on the environment. Extruded polystyrene and closed-cell spray foam with an HFC blowing agent are the among the worst offenders, while straw bales, hempcrete, wood fiberboard, and cellulose store more carbon than they are responsible for emitting.
Magwood and his colleagues have developed a program called BEAM (Building Emissions Accounting for Materials) that quantifies the carbon contribution of different building materials. The calculator draws on Environmental Product Declarations, which are standardized life-cycle assessments, to report net emissions as a number: kilograms of carbon dioxide equivalent per sq. m. (the chart shows the calculations for a square meter of insulation rated at R-10). Magwood explained in an email that certain assumptions go into the calculations, and that not everyone will agree with all of them. Even so, the data allow designers to calculate carbon impact with some precision.
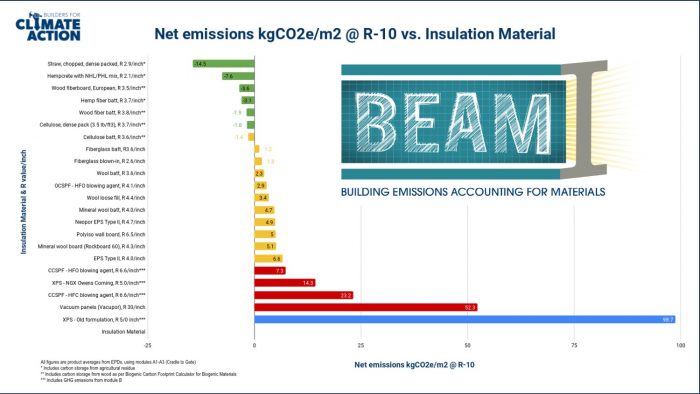
Originally published on Green Building Advisor.
Fine Homebuilding Recommended Products
Fine Homebuilding receives a commission for items purchased through links on this site, including Amazon Associates and other affiliate advertising programs.
Staple Gun
Nitrile Work Gloves
Insulation Knife
View Comments
That BEAM graph would be great if it were legible. To be useful, it needs to be an image you can expand to be readable, not one that expands to big fuzz in place of little fuzz.