Podcast 358: Workshop Ceiling Heights, Foamglas, and Low-Slope Metal Roofs
Rob, Kiley and Patrick hear from listeners about business books for contractors and pool kits before taking listener questions about shop-ceiling heights, Foamglas insulation, and home-energy efficiency.
Follow the Fine Homebuilding Podcast on your favorite app. Subscribe now and don’t miss an episode:
![]() |
![]() |
![]() |
![]() |
Help us make better episodes and enter for a chance to win an FHB Podcast T-shirt:
www.finehomebuilding.com/podcastsurvey
Dan reminds us about David Gerstel’s business books for contractors. A listener from YouTube asks about the in-ground pool kits Rob mentioned. Ted wants to know if 8-ft. ceilings will work in a woodshop. Kathryn wonders about pros and cons of Foamglas insulation. Jeff seeks advice on his badly built greedy dormer. Floyd wonders if he should air-seal his Florida attic.
Editor Updates:
- Rob’s stone work
- Kiley’s little stone wall
- Jeff’s back yard
- Patrick’s aching back
![]() |
![]() |
![]() |
![]() |
![]() |
Listener Feedback 1:
Dan writes: I must be getting really old. Don’t answer that. It used to be pretty rare that a conversation on starting out in the construction business proceeded for more than a minute without someone recommending David Gerstel’s classic Running a Successful Construction Company. A book probably older than the young guy in Boise (1991). My first copy discussed making sure your calculator had a paper ribbon and mused on whether personal computers would prove useful, but still essential reading.
In the interim, David has published his magnum opus, Nail Your Numbers. It’s huge but every chapter is an education in itself.
I have helpfully included my review from JLC.
Listener Feedback 2:
UIL1980 from Youtube writes: What’s the link for the pool kit?
Related Link:
Question 1: How important is the floor to ceiling height of my sub-garage workshop?
Ted writes: Hi Patrick and Podcast Crew – I am working with a client to design and build a workshop underneath their new garage addition using precast concrete slabs for the garage deck. The original goal was a 9-ft. floor to ceiling height for the workshop. However, that puts the workshop floor over 2 ft. to 6 in. lower than the adjacent basement concrete slab floor. Obviously the lower we go the more difficult it becomes to build and costs go up both internally at the intersection of old and new and outside in trying to make the grading work.
My question – How important is a 9-ft. floor to ceiling height? Would an 8-ft. floor to ceiling height be a huge compromise or no big deal? Client is a passionate DIYer who is very excited about his new workshop space and I want to make sure the space exceeds his expectations and is worth the investment he is putting into it. Most of his projects are wood related including: re-purposing cabinets, interior trim renovations, and other fun with wood. Love your show.
Related Links:
Question 2: What are your thoughts on using Foamglas insulation?
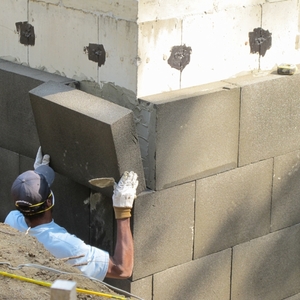
Kathryn writes: Dear FHB Podcast, I was noodling around and found that Foamglas (the glass-based insulation) had returned to the US. This seems like the perfect below-ground insulation and might even work for exterior roof insulation because of its high strength and fire resistance. It seems like an interesting complement to Rockwool. Do you have any thoughts about it? Obviously, the embodied carbon might be high, so that’s a concern.
Related Links:
- GBA: Foamglas Exits U.S. Residential Market
- GBA: Foamglas – My New Favorite Insulation Material
- GBA: On the Jobsite with Foamglas
Question 3: How can I make sure my low-slope roof can handle snow melt?
Jeff writes: Hi Fine Home Bonfiglioli team. You have helped me every step of the way in renovating my foreclosure house and have not led me astray yet! Now I need to go back and fix work done before I owned the house and sprayed closed-cell foam everywhere.
The previous owner put on a greedy dormer and did it terribly. The slope is too low (less than 2:12), he only used 2×6 rafter and had no ridge beam. Plus, the roof is too low to have a legal bedroom ceiling height. In hindsight, I should have ripped it off and put trusses up. Instead, for expediency and cost savings, I had the full cavity filled with closed-cell foam, put in a load-bearing center wall, and hoped the new-ish metal roof would handle the snow melt.
My plan works somewhat but there are a few wet spots when snow is melting. What do I do!? The easiest plan would be to take off the ridge cap and seal up the ridge in hopes that is the problem (they left a vent strip). Or I could pull up the roof a section at a time, run ice and water shield on the whole surface (vertically?) and reattach the roof. Or while I’m at it, I can put down the ice and water shield, put furring strips (vertically and then horizontally?) and put the panels back down with a good airspace. Or is it so low slope I should have it roofed with EPDM? The last option would be to leave it, save money, then rip the whole second floor off and start again, but that’s big money. What do you think? As always, thank you for your expertise and realistic thoughts!
![]() |
![]() |
Related Links:
Question 4: Will the upfront cost to reduce my power bills by improving the air-seal in my home be financially worth it in the long run?
Floyd from Florida writes: Hello there; Floyd here. I moved into an existing home 4 years ago that was built in 2000 and we are in climate zone 9-10 ( Lakeland, Fl.). My first power bill was almost $350.00, which I thought was crazy high. So I started to work on said power bill and changed all light bulbs to LED then programmed the thermostat and installed a newer water heater and changed all of our appliances to new (all were original to the home ). Current state is 5- 6 months of the year we are sub $100.00 power bill. The high now is $178.00.
In the main living area I have issues of moisture around a couple AC vents (poor air-sealing is my thought). I would love to go up in the attic and remove all insulation and air seal the ceiling (vaulted), build a dam, and blow in new insulation. While up there, I would love to put in a radiant barrier with foam sheathing as well, but the cost is the problem. Would i see any monetary benefit? While up there, I would love to put in a whole-house dehumidifier to make it comfy. So if I did all this, I am thinking I would not get a return on investment?
Related Links:
End Note:
From landscape architect Jim Collins of Burlington, Ontario: The latest federal government push: Ottawa looking for 2,000 new energy auditors to get home retrofit program going
Check out our new 2021 FHB Houses:
Visit the Taunton Store • Magazine Index • Online Archive • Our First Issues • All Access
Help us make better episodes and enter for a chance to win an FHB Podcast T-shirt: www.finehomebuilding.com/podcastsurvey
If you have any questions you would like us to dig into for a future show, shoot an email our way: [email protected].
If we use your question we’ll send you a FHB Podcast sticker!
FHB Podcast T-shirts!
Represent your favorite podcast! Available in several styles and colors. Made from 100% cotton. Find the Podcast t-shirt and more cool products in the Fine Homebuilding Store.
This episode of the Fine Homebuilding podcast is brought to you by BUILDBOOK.
A lot of construction pros have a common problem; your construction management software is either non-existent, or it is too slow and too complex. It shouldn’t be bogged down with complicated features that you have to attend an academy to learn how to use. You need software you can start using DAY ONE without training… That is faster and more reliable than your notepad. That allows you, your team and your clients to always know what’s getting done and when. And your software should reduce stress, not increase it. The solution? BuildBook.
BuildBook is built for today’s modern builder with everything you need, nothing you don’t. Whether you’re a one man operation or a business with a large crew, BuildBook has plans to fit your budget. No nagging sales calls, tricky upsells or hidden fees. Head over to BuildBook.co and sign up for a free 10-day trial — and don’t forget to mention that you heard about them on the Fine Homebuilding podcast.
Fine Homebuilding podcast listeners can now get 20% off anything in the Taunton store, including Insulate & Weatherize.
Use the discount code FHBPODCAST to take advantage of this special offer.
We hope you will take advantage of a great offer for our podcast listeners: A special 20% off the discounted rate to subscribe to the Fine Homebuilding print magazine. That link goes to finehomebuilding.com/podoffer.
The show is driven by our listeners, so please subscribe and rate us on iTunes or Google Play, and if you have any questions you would like us to dig into for a future show, shoot an email our way: [email protected]. Also, be sure to follow Fine Homebuilding on Instagram, and “like” us on Facebook. Note that you can watch the show above, or on YouTube at the Fine Homebuilding YouTube Channel.
The Fine Homebuilding Podcast embodies Fine Homebuilding magazine’s commitment to the preservation of craftsmanship and the advancement of home performance in residential construction. The show is an informal but vigorous conversation about the techniques and principles that allow listeners to master their design and building challenges.
Other related links
-
- All FHB podcast show notes: FineHomebuilding.com/podcast.
- #KeepCraftAlive T-shirts and hats support scholarships for building trades students. So order some gear at KeepCraftAlive.org.
- The direct link to the online store is here.