Better Window, Door, and Trim Cap Flashing
Don't let your guard down just because these flashings are on vertical surfaces—learn to install drip caps to reliably block water from leaking into your walls.
Do you ever give cap flashing (aka “drip cap”) over windows, doors, skirtboards, and deck ledgers a second thought? I thought I did a good job installing flashing on the walls of the homes I built and remodeled until discovering a problem on my own house. After just 10 years, a tiny hole in the housewrap at the end of a window cap flashing resulted in saturated insulation and rotted sheathing and studs. It was a wake-up call that I’d better take the details of good cap-flashing design and installation more seriously.
What was wrong with my cap flashing? Several things. I used the 3/4-in. aluminum cap flashing stocked at my local lumberyard. The wall leg was only 1-1/4 in. tall, so the overlap of the housewrap and siding was too short—less than an inch if you were to hold the siding off the cap by 3/8 in. The cap-leg-to-wall-leg angle was bent at 90°, so water didn’t drain off the front edge quickly and puddled. The drip leg along the front was only 1/4 in. tall, which leaves it prone to wind-driven rain getting under it, and it didn’t kick the water away from the trim below. It was thin—only 0.011 in. thick, about half the thickness required of other flashings in the building code. And my installation practices were poor: I placed the cedar shingles tight to the top of the cap flashing (I should have left a gap). And to make matters worse, there is a small roof over a bump-out just above the window without a kickout flashing. So water draining off the roof flooded onto the cap flashing.
What does the building code say about wall flashing?
The International Residential Code (IRC) is often referred to as a “minimum code,” and for that reason it may be disregarded as a serious basis for flashing, but it gives us a starting point. The IRC’s section on flashing (R703.4) says: “Approved corrosion-resistant flashing shall be applied shingle-fashion in a manner to prevent entry of water into the wall cavity or penetration of water to the building structural framing components.” It goes on to list the locations where flashing is required: exterior porches, decks and stairs attached to a wall or floor; above trim; at wall and roof intersections; under and at ends of masonry, wood or metal copings, and sills; at intersection of chimneys or other masonry; at window and door openings. It goes on to note: “The flashing shall extend to the surface of the exterior wall finish.”
The code section is written in performance language. It doesn’t get into the specifics of how to design and install flashing, but focuses on what our flashing must do: “…prevent entry of water into the wall cavity.” The cap flashing I installed over the window trim didn’t prevent water entry, so it didn’t comply with the code.
IRC chapter 7 doesn’t specify the minimum thickness of wall flashing, but the International Building Code does—0.019 in. or 26-ga. metal. The IRC does require 0.019-in. metal flashing for roof-to-wall flashing in chapter 9, so with these two indicators I’d say 0.019 in. / 26 ga. is a minimum thickness for wall flashings too. Unfortunately, many of the stock cap flashings found at lumberyards are 0.011 in.—just slightly over half the minimum thickness. Aluminum coil stock is 0.019 in. thick, readily available in a number of color coatings and easy to work with, so that’s my usual go-to material unless the job calls for copper, lead, or stainless-steel flashing due to design or proximity to saltwater.
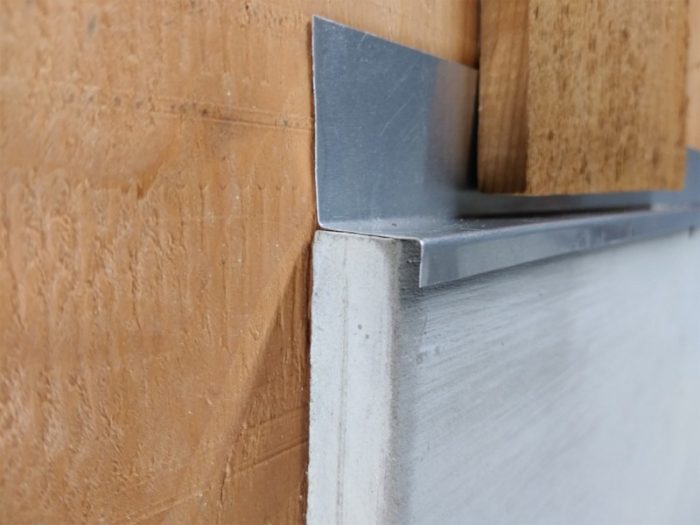
Cap-flashing design
I haven found a stock cap flashing design that I like. Stock cap flashing usually has a short wall leg, a flat cap leg, and a narrow drip leg aside from being made of metal too thin to meet building code requirements. So to get a good cap flashing I recommend bending your own.
That means you’ll need a sheet-metal brake—or a friend who owns one. You can often rent a brake for a reasonable price. A metal brake is a must-have tool for any pro who installs siding and roofing. Cap flashings are an easy design to bend—they’re just a simple “Z” shape. The key features are the wall-leg height, cap angle, drip-leg height and bottom-edge kick, and end profile.
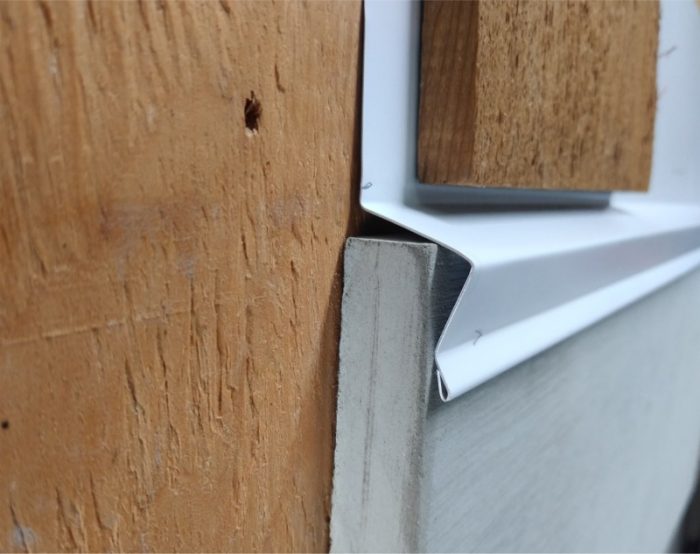
The wall leg has to be tall enough for the water-resistive barrier (WRB) and the siding to lap over the top with several inches of coverage. How tall you make it depends on the wind exposure of the house. A strong wind-driven rain can drive water vertically several inches even beneath tight overlapping siding. I recommend a minimum of 3 in. tall in low-exposure areas and 5 in. or taller in high-exposure areas. This leaves enough wall-leg height so the siding can be spaced 1/4 in. to 1/2 in. above the cap leg. For deck-ledger cap flashing I recommend a 5-in.- to 8-in.-tall wall leg. A tall wall leg is necessary to account for the decking thickness and the minimum required space between the top of the decking and the siding. Some sidings like fiber cement and red cedar lap require a minimum of 2 in. of space from the top of the decking to the siding.
The cap leg should be sloped outward 10° to 15° to drain water rapidly off of the top of the flashing. The slope makes it less likely water will run horizontally and off the end of the flashing—the problem that lead to the leak on my house. Commercially available flashing is usually bent at 90°. If you use one you can open up the angle by pressing the flashing gently between two boards.
I like the drip leg that wraps over the face of the trim to be at least 3/4 in. tall with hem along the bottom edge and an additional kick bend 1/4 in. up from the bottom to kick water away from the trim and resist water being drawn on top of the trim by capillary action. The hem and kick bend stiffen the drip leg so it will stay straight and not warp when the flashing expands in hot weather. I make the drip leg bend 90° to 95° to the cap so the drip leg will press tight to the trim and resist wind-driven rain blowing between the cap flashing and the trim.
Three ways to finish the ends of your flashing
The most common end detail is none at all—the flashing is cut flush with the end of the trim like in the photo above. This leaves a small open triangle area between the flashing and the top of the trim due to the slope of the cap. Water can enter at the end so I don’t recommend leaving it open.
The gap can be closed by bending an end leg down in much the same way as the face of the flashing is treated.
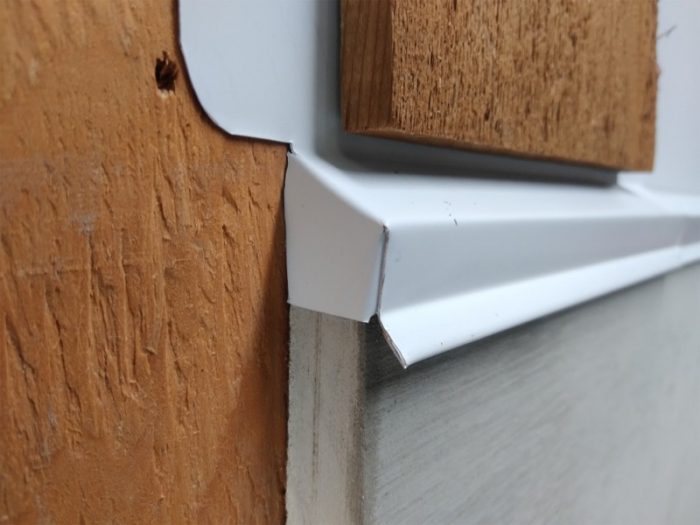
The end leg will block water from blowing in between the flashing and the end of the trim. The weak point here is any water that drains off the end of the flashing is directed into the joint between the siding and end of the trim; but if the cap leg of the flashing is sloped outward there’s probably little water reaching the end to begin with.
Another way to detail end of a cap flashing is with an end dam.
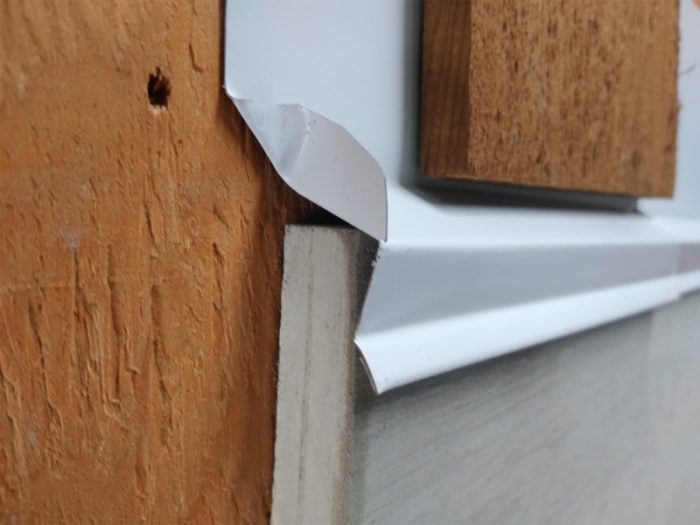
An end dam is an upturned fold that blocks water from running off the end of the flashing and directs it off the face. It also guides siding installers to leave a gap between the siding course and the top of the flashing. It takes a little more folding to bend a 3/8-in.- to 1/2-in.-tall upturned leg to block water rolling off the end of the flashing. On the downside, the end-dam profile leaves the same open triangle gap between the cap-leg slope and the top of the trim.
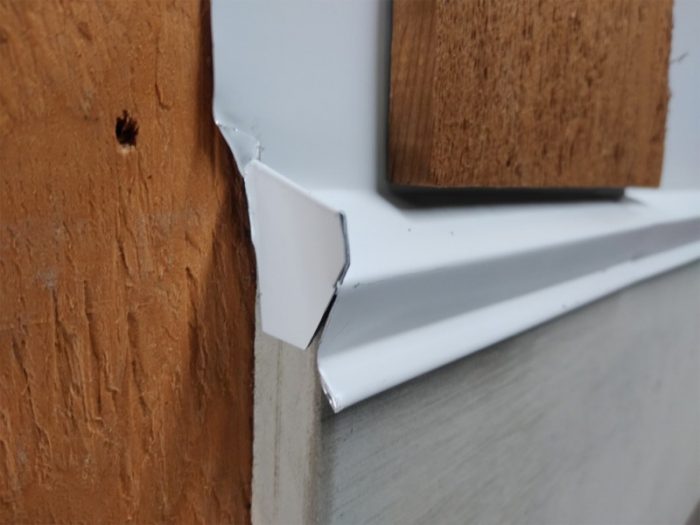
A modification to the end dam closes the gap. Just leave an extended end-dam leg and fold it down to cover the end of the trim. It takes some practice to bend and trim an end dam with a closure, so try it out with small pieces of metal before cutting a full cap flashing.
RELATED ARTICLES