10 Essentials for Quality Trim Carpentry
Remodeler Tyler Grace lays out a handful of tips, tricks, and principles that will help you become the best finish carpenter that you can be.
Synopsis: Tyler Grace, remodeling contractor and Fine Homebuilding ambassador, shares professional tips and techniques for executing finish carpentry projects with confidence and skill. From acclimating your materials to taking care of your tools, being precise with fasteners, and keeping your workspace neat, these 10 essentials describe what’s needed to accomplish trim installations that are precise, effortless, painless, and pristine.
As a remodeling contractor in southern New Jersey, I perform the work of various trades on each of my projects, but finish carpentry is something I enjoy more than almost anything else. I am a bit of a perfectionist and a stickler for the details, so what could be better than getting paid to possess those personality traits on the job and then manifest them through my work?
By the time you get to the finish stage of a job, you do not want to be aggravated, stressed, frustrated, and out of patience. Trim installations should be precise, effortless, painless, and pristine. You are past the point of heavy hammers, beater blocks, and brute force. In my opinion, what separates a good carpenter from a great carpenter is someone who can think ahead and plan, cover their tail, account for inconsistencies, remain organized, work fluidly, and be efficient while doing so. Here you will find a handful of tips, tricks, and principles that will help you hone your skills and become the best finish carpenter that you can be.
1. Plan for trim from the get-go
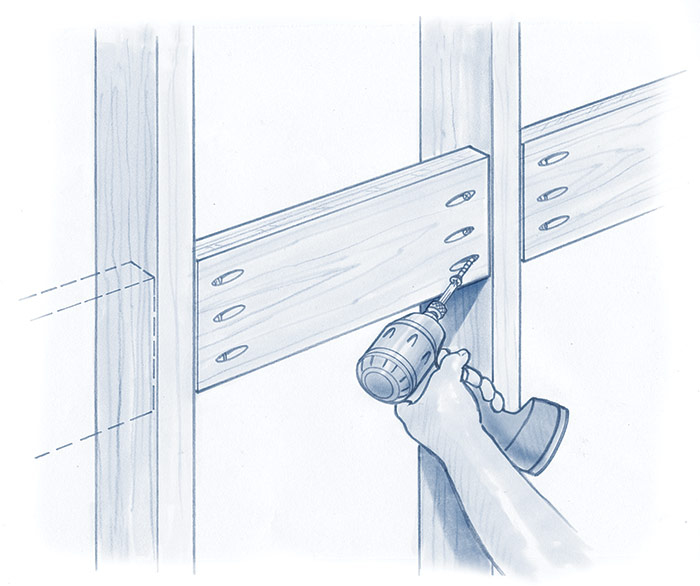
A quality finish-carpentry project requires adequate forethought and planning. Success is not a fluke or coincidence. If you want to deliver a great product, you need to plan to do so. You cannot simply show up on day one with your tool belt and expect to knock it out of the park.
One of the best things you can do is take the time to walk the job after mechanical rough-ins are complete. Mark all of your studs on the subfloor, and highlight critical areas such as the location of utilities and where blocking is needed. And document the job site with photos. I constantly refer back to my phone while trimming to see what is behind the walls. It’s saved me many errant nails over the years.
Now is also a great time to install any blocking that will aid in your trim, millwork, or cabinetry installation. Ensuring you have structure where kitchen crown will be installed, cabinets will be hung, stair skirts are located, and trim will be installed will save you boatloads of time throughout the duration of the project. It will also reduce the number of callbacks you have down the road. Start wrapping your head around the finish carpentry to come at the rough-carpentry phase of the project. It will make your life much easier when the time comes to break out the compressors and saws.
2. Acclimate your materials
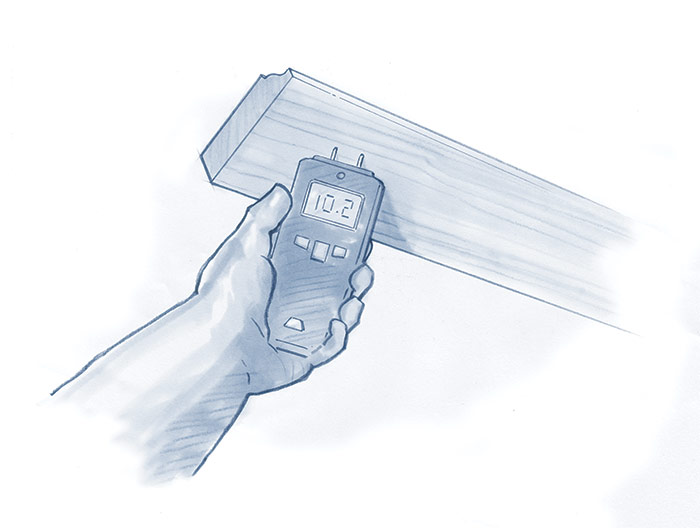
Wood moves. It is affected by temperature and moisture. You must do everything that you can to get your material to the job site as early as possible to acclimate. The job site must also be conditioned. It does not matter if your trim or cabinets show up to a job a year early if they’re sitting in a hot and humid work site. As soon as the HVAC is fired up, and the moisture is drawn from the space, those tight joints will not be so tight anymore.
There is no specific amount of time that it will take for your trim and millwork to acclimate to a site. You have to measure the moisture content of the wood and the substrate to which you are applying the material. I have had molding dropped that was in a safe range to install on day one, and I have had lumber dropped that after a week still required dehumidifiers to reduce the moisture content of the wood. I recommend getting to the job when the material is delivered, measuring the existing site conditions and the moisture content of the wood, and tracking them until they are both within a stable range independently and with respect to each other.
I do my best to ensure that the moisture content of trim in a conditioned space is between 6% and 10% prior to installation. Typically it gets delivered from an unconditioned space and arrives with a moisture content between 12% and 14%. The relative humidity in the room will affect how quickly that newly delivered trim will acclimate. I also aim for the moisture content between the material and the substrate to which it will be applied to be within 2% to 3% of each other. Installing properly acclimated trim with a 7% moisture content onto plywood or drywall that has a moisture content of 16% will wreak havoc on that installation. They are 9% off from each other and the trim will draw the moisture from the substrate.
3. Stabilize your materials
Acclimating your materials and dialing in site conditioning is a fantastic start, but it is not always enough. My feeling is that we should do all that we can to ensure our installation remains intact for years to come. How do we do that aside from acclimation? Here are a few things that I do to help control pesky material movement.
Prime all of your drywall or plaster prior to installing trim. Primer seals the surface of the substrate and reduces the transmission of moisture from one material to another. Also, back-prime any unfinished lumber to ensure the material is completely sealed. The more we can control how much moisture can penetrate the materials, the better off we are.
Ensure that areas around windows, mudsills, doors, and floors are air-sealed. Leaking air will create temperature fluctuations within the space which will affect your installations. I carry around a can of spray foam while installing trim. That way, I can seal off any drafts prior to installation.
For interior millwork, I do not seal my end cuts with primer. With proper acclimation, you should not have enough movement to create any major moisture transmission through those surfaces. I do use mechanical joinery whenever possible. Although nothing can actually prevent wood from moving when it wants to move, glue, adhesive, tenons, pocket screws, biscuits, and other mechanical joinery will help immensely. It is an additional layer of protection to ensure a long-lasting installation.
4. Sort and break down stock wisely
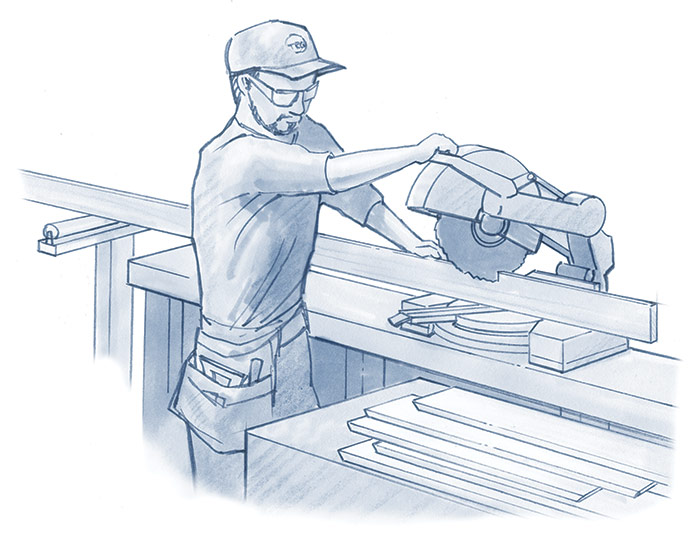
Properly sorting and breaking down trim and millwork parts is not only one of the first steps of many trim jobs, but done right, it improves the quality of the work, makes the most of the material, and saves you trips to the lumberyard when you run short.
Running baseboard is a good example. While it may be more convenient to run down your cutlist and cut each piece of baseboard in sequential order, you should instead cut all of your longest lengths first and set them aside. There is nothing worse than needing to purchase more stock because you ran short of long lengths, and there is no need to cut a 16-in. piece of baseboard out of a 16-ft. piece of stock unless you have no other choice. As you go, save all of your scrap pieces to use for returns, closets, and other choppy areas like halls and bathrooms.
Place damaged boards aside to use in an inconspicuous area. Painters can often fix damaged boards, but use them inside of a closet, behind a sofa, or in an attic or basement space where imperfections matter less. Do not use the worst piece of trim in the foyer of the home where it will be seen as soon as you walk in the door.
Finally, always double-check your lumber at delivery, not when you are strapping on your tool belt and setting up your saw. Ensure that you have extra stock and that what was dropped at the site is what you ordered. It would be very disappointing to show up to a job with the finish-carpentry crew only to realize that you are short on material, or the material is incorrect or damaged. That’s time and money lost while the crew waits for the right material to arrive.
5. Use the right fasteners the right way
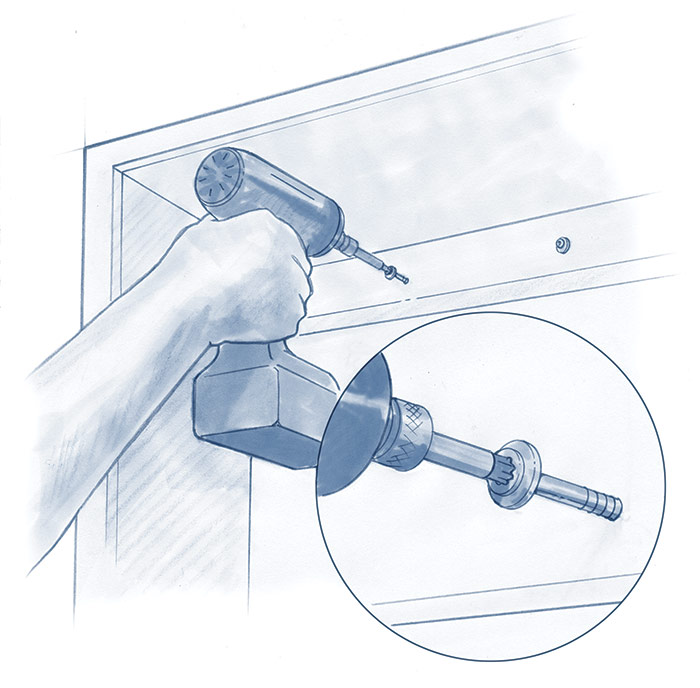
Not all fasteners are created equal. It is important to understand how fasteners work, when to use various gauges, and why we use different fasteners for different applications. Some hold better than others, some have more drawing power, some are easier to conceal, some are used in the place of clamps, and some have a higher shear strength.
When I first started installing trim, I always questioned which fastener to use when. I believe there are no steadfast rules, but common sense is an incredibly powerful start. Most trim is ornamental and simply needs to be able to support its own weight, such as casing, baseboard, wall details, crown molding, and cornices. Other trim and millwork needs to be able to handle loads, like door jambs, cabinetry, and thresholds. I prefer to use the smallest fastener possible for each job to help create a better paint or stain finish.
Cabinetry must be held in place with structural fasteners. Drywall screws have very little shear strength, and cannot support the load of the cabinet and their contents. If you have gotten away with installing cabinets with drywall screws in the past, it is probably because of the friction caused by the pressure between the wall and the cabinet, and not the shank of the screw. You must ensure that you penetrate the framing adequately as well and choose an appropriate-length fastener for cabinetry. I prefer using a fine-thread structural screw with a head that locks into a specialized drill bit. These screws are stronger and easier to drive, and your driver won’t jump off the fastener and damage the cabinetry.
Prehung doors and door jambs require a fastener that is long enough to penetrate the framing, but also thick enough with a substantial head to reduce movement. Typically jambs and prehungs are installed with 15-ga. nails, but I often get away with 16-ga. nails, ensuring that I adequately nail my casing into my jamb. This locks the assembly together and secures it as one unit.
Baseboard, casing, and crown molding can be installed with 18-ga. or 16-ga. fasteners depending on how much holding power you need. I like assisting my installation with adhesive so I can use a smaller-gauge fastener, which finishes better and the piece is still fully supported with the adhesive. This technique is great for prefinished cabinetry trim and millwork. You can back-glue the trim and use a headless pin to hold it in place until the adhesive cures, which requires less putty and results in a cleaner install.
6. Be precise with placement
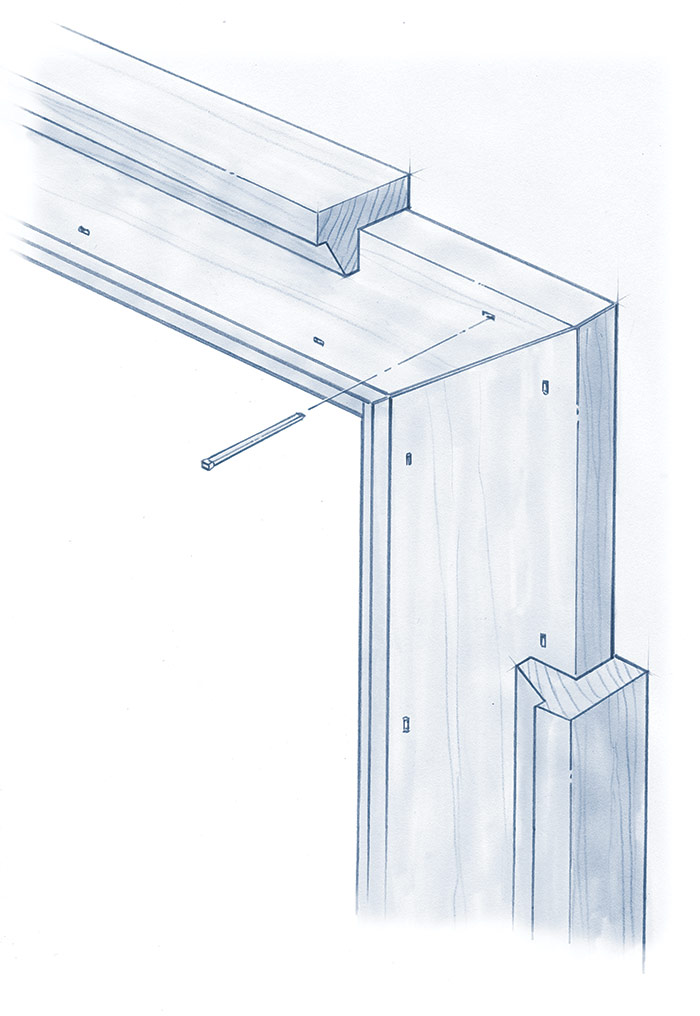
Every subtrade should have the following trade in mind. Carpenters are not an exception to this rule. Typically the painters follow the trim carpenters, and you should do all that is within your power to make their lives easier. Whenever it is possible, you should attempt to hide nails where they will be covered by succeeding layers of trim. Nail casing where a backband will cover your holes, nail baseboard low enough that the shoe molding or quarter-round laps over the fasteners, nail fascia or frieze where the bed molding will hide the brads, and so on.
Moldings should be fastened in a specific pattern and consistent manner. Ensure that nails penetrating the jamb are in the same horizontal plane as the nails for the casing. Line your nails up on baseboard, cap molding, and transitional moldings. Does this affect the structural integrity of the installation? It does not, but it shows that you care, it makes the painters’ lives easier by not having to search for fasteners, and it ensures that you do not miss any necessary fastening locations.
When fastening prefinished moldings or stain-grade trim, nail placement is even more critical. Divide your material length into equal segments so that any visible fasteners are uniform and neat, ensure the nail is not proud or too deep, and nail with the grain where possible to disrupt the grain of the wood as little as possible. A nail placed with the grain of the wood will enter the material and set itself without crushing and damaging the area around the fastener. All of these efforts show that you have integrity for your craft, and they also make for a better finished product.
7. Take care with your tools
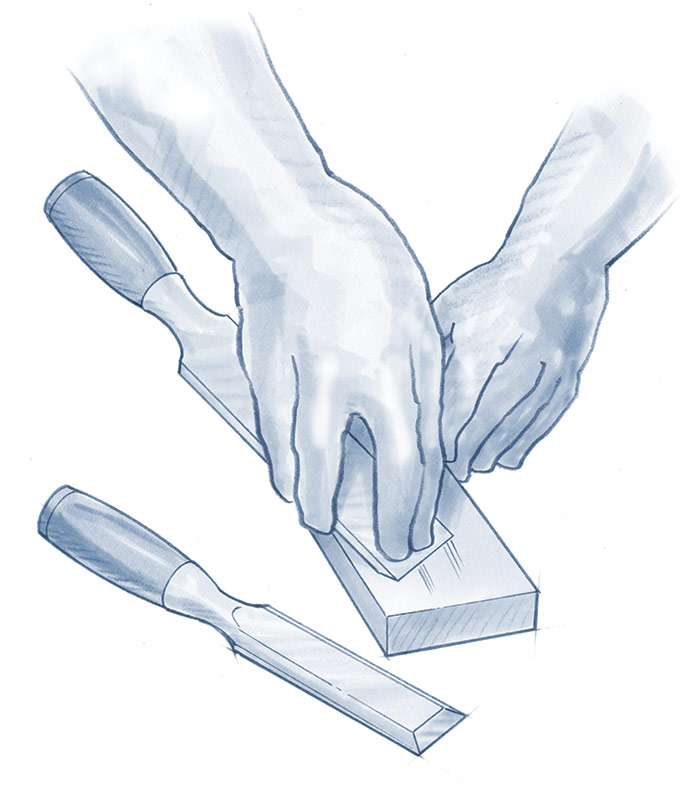
You can own the best tools in the world, but if you do not know how to use them, how to maintain them, or how to tune them, they are worthless. Always protect your tools. One violent drop of a miter saw can create out-of-square cuts that will make you want to pack it in and quit. Every good carpenter should know how to tune their miter saw. You need to understand how to ensure that the fence is square to the blade and coplanar on each side of the blade. You should be able to inspect the table of the saw and adjust the height, detents, bevels, and miters. A well-tuned miter saw is worth its weight in gold.
Make sure that you know when it is time to sharpen your bits and blades. A good carpenter understands when you can get away with a quick cleaning, when you need a full sharpening, and when you must replace a bit, blade, or chisel. After every job I sort through my sawblades, router bits, knife blades, chisels, and plane irons and inspect them. I dispose of those items that are past their usable life span, I package blades that need to be shipped off to be professionally sharpened, I clean pitch off blades that are still in decent shape, and I sharpen my irons and chisels on sharpening stones. Having sharp blades is not only safer, but it creates cleaner and tighter joinery.
It is also important to clean your tools to ensure that metal is not rusting, bearings are lubed, electronics are clean, and brushes are fresh. At the end of the day I always vacuum the sawdust off of my tools. Many people blow compressed air into their tools, which drives dust and debris into the motor, electronics, bearings, and seals. This is not ideal and will create issues down the road. Invest in high-quality tools and routinely take care of them; you will be rewarded with well-performing, reliable equipment for years to come.
8. Minimize your steps

In order to be efficient as a finish carpenter, you must understand economy of motion. Each task and movement must be purposeful and deliberate. Each added step and trip back to the saw reduces efficiency and in turn reduces profitability. Therefore, each project should be broken down into repeatable tasks. If possible you should complete each task prior to moving onto the next. For example, you should prep your entire job for trim prior to beginning trimming. It is not as efficient to cut back drywall, sand down mud, and address out-of-square corners as you go as it is to do it all at once. If you have to stop what you are doing to grab different tools and then clean up before getting back to it, you are losing a lot of time and wasting a lot of energy.
Do your best to batch-cut parts. It is possible to measure each window and/or door and then calculate all of your dimensions for stools, aprons, and casing at once. You can do it at a workstation or at the saw—it does not need to be done at each window or door. You can pre-cope all your ends at once, so that you do not need to constantly be adjusting and switching the saw, back-cutting, and filing. It is much faster to line up all your cuts at once and blow through each task entirely than it is to hop back and forth.
Use hand planes whenever possible. You can save a lot of footsteps and trips back to the saw by having a quality low-angle block plane to adjust miters, back-bevel a scribe, or relieve the back of a piece of molding to flush out a miter. Every finish carpenter should have a high-quality plane in their tool belt.
Do your best to reduce the amount of times you switch between nail guns or fastener sizes. Ideally, use multiple nailers—but if that is not financially feasible, learn to nail off molding in a way that allows you to switch nailers once throughout the task. Bouncing back and forth between an 18-ga. and a 16-ga. nailer for every door, window, and baseboard can waste a lot of time.
9. Know when and how to scribe
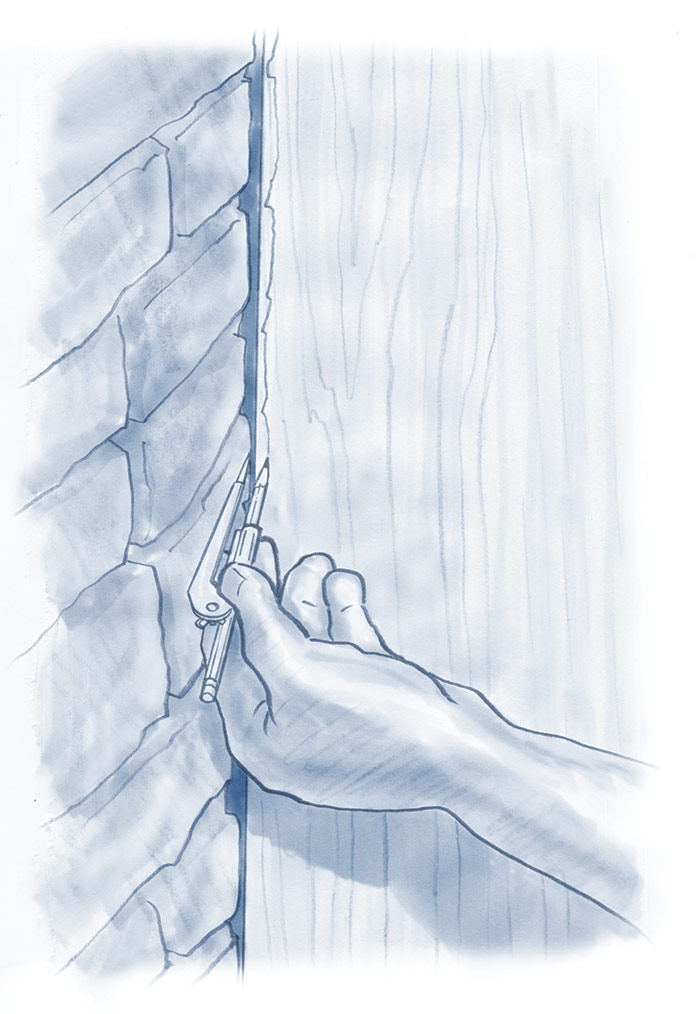
A decent finish carpenter should comprehend the fundamentals of scribing. You must understand if you are scribing to be parallel or scribing to be plumb, level, and square. Not all situations call for plumb, level, and square, and doing so can, at times, make the irregularities more pronounced. You must be able to grasp the nuances of each and know when to apply the appropriate principle.
Scribing to an irregular surface will draw attention to that transition. At times this is good, and at times this is less than desirable. A complex scribe around a natural stone or brick wall can showcase your carpentry talent and create a tight joint that makes an incredible focal point. On the other hand, scribing a baseboard to an irregular or uneven tiled floor can highlight the undesirable floor irregularities, and is at times better disguised with one gradual cut.
Scribing should be an accurate and finely tuned technique. It helps to back-bevel the molding you are scribing, so that once you are ready to make a final pass, you do not have to hog out so much material. It is easier and more accurate to only remove a portion of the stock when fine-tuning your scribes. I typically use a combination of a tablesaw, a track saw, a belt sander, a Festool RAS (a grinder-type tool with dust collection), and a hand plane to scribe moldings and millwork.
10. Keep it neat
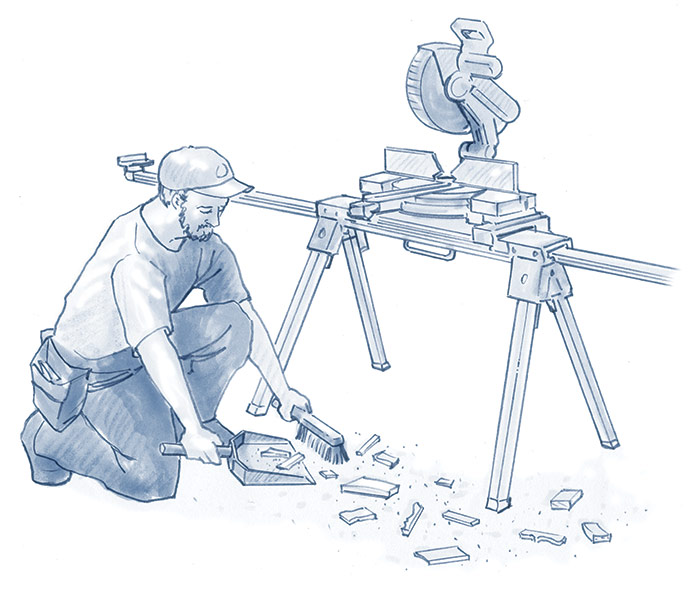
Last but not least, you must maintain a clean and organized workspace. Finish carpentry requires skill and patience. You are often working in and around completed spaces and components that must not be dirtied or damaged. Having a tidy, well-thought-out, organized workspace can make or break morale and the overall project.
A carpenter should have the forethought to set up their workspace for the duration of the project. You do not want to be constantly altering, adjusting, or moving your setup for various tasks. Adequate space to function and prevent damage to existing surfaces is critical.
I prefer to create stations to perform each task. I will create a cut station for my miter saw, a station for my tablesaw and outfeed, a large area for assembly, a place to break down larger pieces of plywood or cabinet parts, a space for scribing, and a place for fasteners and tools. At the end of each day you must reorganize, neaten up, and provide a clean slate for the following day. Starting each day with clutter creates haste, inefficiencies, and mistakes, and reduces quality. Having a clean, organized workspace and job site also shows your customer that you respect their home, you respect your craft, and you respect yourself.
Tyler Grace is a Fine Homebuilding ambassador and owner of TRG Home Concepts in Haddon Heights, N.J. Drawings by Dan Thornton.
To read the entire article, please click the View PDF button below.
RELATED LINKS
Fine Homebuilding Recommended Products
Fine Homebuilding receives a commission for items purchased through links on this site, including Amazon Associates and other affiliate advertising programs.
Metabo HPT Impact Driver (WH18DBDL2)
Makita Top-Handle Jigsaw (4350FCt)