Podcast 414: Insulating Band Joists, Saving Salvaged Material, and Fixing Wet Masonry
Mark, Kiley, and Patrick hear from listeners about window condensation and building a business before taking questions about insulating band joists, saving stuff from the dumpster, and dealing with a badly insulated masonry building.
Follow the Fine Homebuilding Podcast on your favorite app. Subscribe now and don’t miss an episode:
![]() |
![]() |
![]() |
![]() |
Help us make better episodes and enter for a chance to win an FHB Podcast T-shirt:
www.finehomebuilding.com/podcastsurvey
Jonathan tells us about his town’s lumber sale. Alex shares his masonry experience. Andrew needs help fixing part of an exterior wall behind a slab. Sean asks about improving a house with a vented attic with ductwork. Nick wants to know more about let-in bracing. Cole is curious about masonry products with lime instead of Portland cement.
Editor Updates:
- Mark’s house
- Kiley’s basement airsealing. What is GBA doing?
- Jeff’s deck
- Patrick’s stairs and his Pro Talk with electrician David Shapiro
Listener Feedback 1:
John writes: Hi Podcast, I’ve been listening to your podcast for a while now and recently was listening to episode #378. Got quite a laugh out of your discussion on condensation on windows. But first, I should back up a little. I’m an amateur DYIer that lives up in Calgary, Alberta Canada and I am also an engineer (it drives my family nuts that I’m constantly experimenting on things around the house, little do they know) and I love the podcast. Back to your comments on condensation on windows: my laugh came when you guys proceeded to indicate that double pane windows were all you really needed to keep condensation at bay, and if you still had condensation issues, it was probably because of a wet basement and you should solve that issue first.
The reason it caused me to chuckle is because just that morning I had opened the blinds in our bedroom and noticed some condensation starting in the corners of our double pane windows and thought to myself ‘better check the setting on the furnace humidifier’. Our nighttime lows were getting into the -5 C range (~20 F), so really not that cold yet, and our basement is definitely not a source of moisture. In fact, I’m sitting down here right now working away at my home office desk and the hygrometer on the little thermometer that I have on my desk says that I currently have 38% relative humidity in the basement (and it hasn’t strayed much from the 40% range since I started working down here in September). Anyways, I guess my point is that not all double pane windows are adequate to keep moisture off of them (I’ll chase condensation levels with our humidifier set point based on outdoor temps all winter long, otherwise they’ll ice up in really cold temps when I close the curtains or blinds), and not all basements are a constant source of moisture.Keep up the good work.
Listener Feedback 2:
Jason in Maine writes: Hi FHB Podcast, I recently listened to the KCA #7 podcast with Aaron Agosto. The topic of conversation went to the trade-gap issue and some of the issues touched on were lack of pay and lack of training. That is a huge issue as well in my location in Maine. I’m a 33-year-old business owner and I have 7 employees, all carpenters that work for me and the age ranges from 17 to 56. I’ve been able to build a solid team by providing good pay, a variety of work, and the willingness to train.
However, it is nearly impossible to find anyone “younger” with formal training. They’ve dropped the carpentry programs at the local community college and the shop classes have moved to computer courses. To continue to grow a business and bring up younger people in the trades I think it is very important to take the time to train, educate, and demonstrate that you can make nice career within the industry. I have found and probably to no fault of their own, very few high school-age or slightly older individuals that are interested in the trades, it seems they are being directed toward white color or tech jobs, which is unfortunate. I figured I’d add my two cents. I’m a regular listener to the podcasts and a subscriber to the magazine and website. Thanks for all the content and information.
Related Links:
- Roundtable: Filling the Trades Gap with Women
- Advice for People Entering the Skilled Trades
- Educational Opportunities are Key to Diversifying Builders
- KeepCraftAlive
Listener Feedback 3:
Evan writes: Dear FHB Podcast Crew, In a recent episode you all discussed paint and the reflection of light by various materials. You asked what happens when light is reflected from a building. I am a student of Appalachian (Appa-latch-un) State University in Building Science and in Physics.
My understanding of the situation is that a building is hit with light and the color that you see is the color that the siding or any other material reflects the most of. Other wavelengths of light are absorbed which does to an extent influence the temperature increase of the building (depending on insulation values). Black surfaces absorb the most light and white surfaces reflect the most light, with a spectrum in between the two. The amount of light not absorbed is called albedo, something you may have heard before. Some light reflected from the building would reach nearby buildings, and as you all suspected, the amount of light coming to them depends on the color of the first building. Other portions of the light will reach the ground, air, or leave the atmosphere. This can continue for a given beam of photons (light particles) until it is completely absorbed or exits the atmosphere. Just as with a building or individual object, the planet as a whole has an albedo, as not all light received is absorbed on earth.
Listener Feedback 4:
Chris writes: I just finished listening to podcast 406 where Kiley was talking about trying to fix her sand-point well which I, also, have never heard of. Coincidentally I was just checking out a house my brother is having inspected for possible purchase a couple of towns over from Kiley which has a standard well and lead in the soil around the house due to power washing old lead paint from the house without any concern for where that paint went. I asked the guys inspecting the well which was about 50 feet from the house to add lead to the water test just to be safe and I’m still waiting on those test results which we’re hoping will come back clean. Being that Kiley’s house is old and the well abuts the foundation and is very shallow I would think the concern for possible lead contamination would be far greater than in a standard well which is deeper and farther from a dwelling. I hope that all is well with the well Kiley!
Related Link:
Question 1: What’s the best way to insulate my basement with XPS on the exterior?
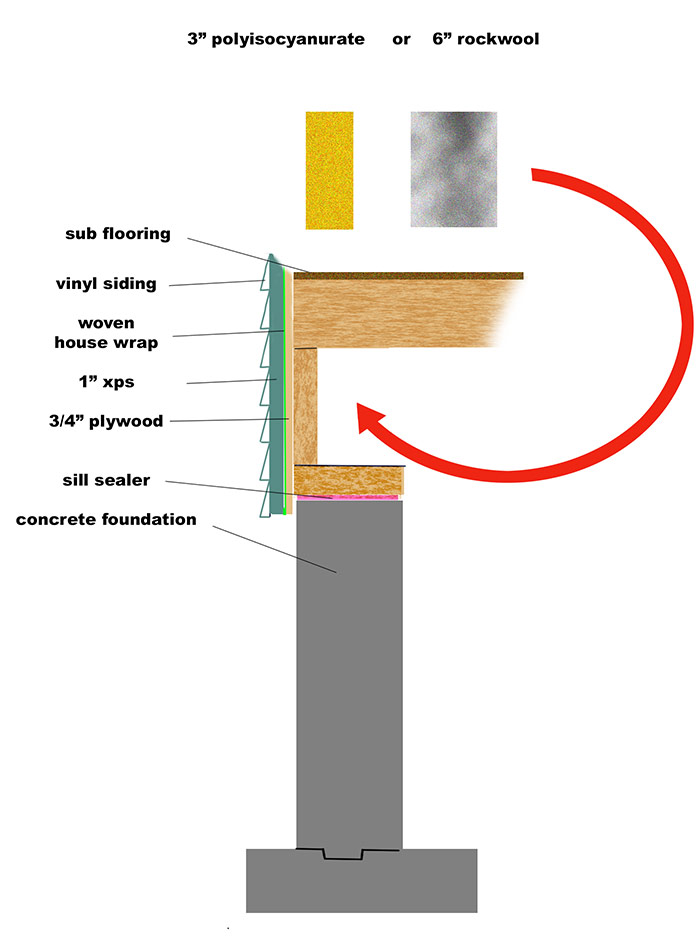
Tom writes: Hi podcasters, homeowner here. I have a vinyl sided house with weaved Tenneco housewrap and 1″ of XPS. (circa 2000) House built 1982 in Lawn Guyland, NY.
Project is to put 3″+ of polyiso on the interior poured concrete foundation in basement and crawlspace. Basement is damp except for heating season here. My dehumidifier runs all summer. Bringing humidity down to 70%. Winter is 40% with no dehumidifier. My concern is the rim joists above. Since the exterior has 1″ already. I worry about locking in moisture with polyiso and foam sealing gaps. Or using closed cell foam.
Currently rim joists are fiberglass insulated. Plan B was to stuff in Rockwool. I read thru Martin Holladay’s and Joe Lstiburek’s info and no mentions of my situation of exterior XPS insulation in place already. Pix may help. Contact me for any questions.
What do you recommend?
Related Links:
Question 2: How can I salvage materials I come across for future building projects?
JP writes: Like many tradespeople, I come across a lot of salvageable building materials in my work. Dumpsters are often teaming with potentially useful stuff for a future build or improvements to my house. But you can’t save everything and building stuff often takes up a lot of space. How do you decide what to save and what to let go? Do you ask your coworkers or other tradespeople to keep an eye out for stuff you’re looking for? Do you rescue stuff for other people? What are some of the things you brought home? Did you use the stuff or did you just end up storing it for months or years only to trash it later?
Related Links:
Question 3: What are some serious and common design blunders you’ve seen?
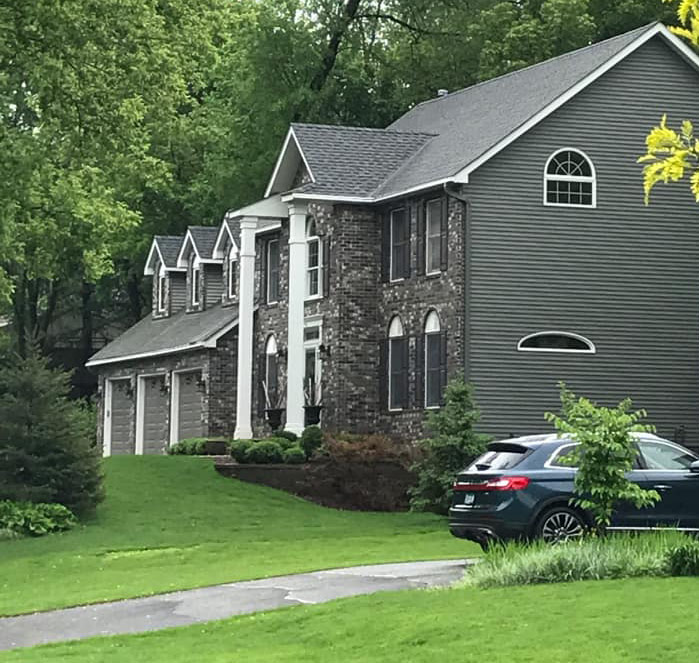
On social media: Hey FHB, What are some serious design blunders you’ve seen? What do you think people get wrong consistently? I routinely see odd window arrangements, details with odd proportions, and overly-complicated exteriors
Related Links:
- McMansion Hell
- Mike’s Marbleopolis – SNL
- Stunning Colonial
- 10 Common Mistakes Made by New Homebuilders
- 12 Restoration Blunders
Question 4: How do I remedy a botched interior insulation retrofit?
Scott writes: Hey Folks – So, I posted a bit about our situation last year. We purchased a home in Chicago, which is a 1914 brick 2 flat, last summer. We bought it from the builder who performed the gut rehab on the building. Long story short, their interior insulation retrofit did all the things you shouldn’t do, according to building science, and it has resulted in a significant amount of issues, including but not limited to spalling and accelerated degradation of both structure and finishes. We are not only concerned for the building, but also our health, as the assemblies are taking on a lot of moisture, from both from the interior and the exterior. Last winter, we opened up a few holes in the drywall to discover the interior face of the 3 wythe brick wall to be totally frozen over. For reference, the assembly from outside to in, is: 3 wythe brick, 2×4 wood frame offset slightly from the inside face of the brick, 3.5″ knauf kraft face batts, drywall.
We have been considering 2 options for fixing this mess:
1. The first being a proper interior insulation retrofit, whether it follows BSC’s recommendation of spray foam, or 475’s recommendation of Visconn liquid membrane, dense pack in 2×4 framing, and Intello smart vapor retarder. The hitch with this approach is having to uninstall all our finishes and completely demo back to the brick wall. The expense here would be significant. On top of this, we would have to still repair the exterior masonry, which we are getting quoted about $60k to bring it up to “standard quality”.
2. The second is an exterior insulation retrofit, where we’d likely follow BSC’s deep dish literature. We like a lot of things about this approach. It will provide a continuous air/water/thermal barrier on the exterior. It will transition the brick wall to the interior, bringing it within the thermal boundary, thus allowing for its thermal mass to remain more constant to interior temperatures. It will protect our embedded structural wood members from thermal bridging and condensation risk. It will also give the opportunity to expose some brick walls to the interior too, which will be a nice aesthetic touch. Most of all, we would not need to re-insulate, re-drywall, and re-paint the entire interior of the building.
Given that we would like to pursue the exterior insulation retrofit option, we shared the BSC article with our architect. The assembly from BSC is attached, but in short: fluid applied air barrier to the brick, 2×4 vertical furring, rigid foam between and continuous over the furring, 1×4 furring on the exterior face of the last layer of rigid foam, and then siding. Our architect proposed instead of all the individual components, to consider Zip Sheathing instead. Instead of installing the liquid air barrier, furring, and rigid foam individually, integrate it all together into 1 product. Execution wise this makes sense to me. It will probably reduce labor costs as well. It does limit us to R12.5, which is a bit less than I originally wanted.So – any thoughts on Zip on this application? It never occurred to me to consider it. Any other thoughts/feedback would be welcomed!
Related Links:
End Note:
’Twas a month before Christmas and all through my life
There’s no project completion, just turmoil and strife.
The subs were all scheduled and so were the parts
But pandemic times “schedules” are more like throwing darts.
Suppliers can’t say when their goods will arrive.
IF subs show it’s two, not the usual five.
With less crew on the work the delays they do mount
Bringing frustrated client email – too many to count.
Their projects run long and cost more but aren’t better
These extended durations make us the upsetter.
Now what to my sleep deprived eyes did appear
But more new housing starts and remodels next year.
Our materials pricey, our trade partners more-so
But with timelines so lengthy- our profits, they no-show.
Seasons once filled with joy are now full of “sorry!”
But there’s no end in sight for next year so I worry.
—Travis Brungardt, Catalyst Construction
Wednesday January 12th 9-6:30 — our first ever PRO TALK LIVE in Portland, Oregon!
- Register here: www.finehomebuilding.com/protalklive
- Tim Uhler of Pioneer Builders–Work Smarter, Not Harder
- Bryan Uhler of Pioneer Builders Better Spec Homes, Four Decades in the Making 1978
- Josh Salinger of Birdsmouth Design-Build— Good Intentions and Disastrous Results: How Not to do an Energy Retrofit
- Lindsey Shack–Love-Schack Architecture Delivering Beautiful and Nurturing Spaces for Clients
- Check out the cool space at The Redd on Salmon Street
Check out our latest Project Guide: Siding & Exterior Trim!
Check out our FHB Houses:
Visit the Taunton Store • Magazine Index • Online Archive • Our First Issues • All Access
Help us make better episodes and enter for a chance to win an FHB Podcast T-shirt: www.finehomebuilding.com/podcastsurvey
If you have any questions you would like us to dig into for a future show, shoot an email our way: [email protected].
If we use your question we’ll send you a FHB Podcast sticker!
FHB Podcast T-shirts!
Represent your favorite podcast! Available in several styles and colors. Made from 100% cotton. Find the Podcast t-shirt and more cool products in the Fine Homebuilding Store.
Fine Homebuilding podcast listeners can now get 20% off anything in the Taunton store, including Insulate & Weatherize.
Use the discount code FHBPODCAST to take advantage of this special offer.
We hope you will take advantage of a great offer for our podcast listeners: A special 20% off the discounted rate to subscribe to the Fine Homebuilding print magazine. That link goes to finehomebuilding.com/podoffer.
The show is driven by our listeners, so please subscribe and rate us on iTunes or Google Play, and if you have any questions you would like us to dig into for a future show, shoot an email our way: [email protected]. Also, be sure to follow Fine Homebuilding on Instagram, and “like” us on Facebook. Note that you can watch the show above, or on YouTube at the Fine Homebuilding YouTube Channel.
The Fine Homebuilding Podcast embodies Fine Homebuilding magazine’s commitment to the preservation of craftsmanship and the advancement of home performance in residential construction. The show is an informal but vigorous conversation about the techniques and principles that allow listeners to master their design and building challenges.
Other related links
-
- All FHB podcast show notes: FineHomebuilding.com/podcast.
- #KeepCraftAlive T-shirts and hats support scholarships for building trades students. So order some gear at KeepCraftAlive.org.
- The direct link to the online store is here.