Podcast 449: Venting Under Shingles, Subslab Vapor Retarders, and Whole-House Fans
Ian, Kiley, and Patrick hear from listeners about hydro air and rustic decks before taking listener questions about ventilation under asphalt shingles, vapor barriers under concrete footings, and keeping cool with a whole-house fan.
Follow the Fine Homebuilding Podcast on your favorite app. Subscribe now and don’t miss an episode:
![]() |
![]() |
![]() |
Help us make better episodes and enter for a chance to win an FHB Podcast T-shirt:
www.finehomebuilding.com/podcastsurvey
Doug is surprised that we don’t know about hydro-air systems. Mike says better code enforcement will lead to better HVAC systems. Joey asks if he should vent under his asphalt shingles. Doug wonders why builders aren’t putting vapor retarders under foundation footings. Mark wants to know if whole-house fans are a good idea. Jesse needs a separation between his primary bath and bedroom.
Editor Updates:
- Kiley’s gravel parking pad
- Ian tweaking door hardware, outdoor stove, and sorting tools
- Jeff’s new outbuilding
- Patrick’s trip to JLC Live: labor burden, finish carpentry, indoor-air quality
Listener Feedback 1:
Jim writes: Hi All, I was surprised at the seeming lack of knowledge as to hydro air. Unless I am misunderstanding the discussion, this sounds like a smaller version of what is standard practice on large institutional projects. There is an air handler with both a hot deck and a cold deck. The hot deck is fed from a boiler and the cold deck from chiller. No, I am not an HVAC person I am a retired high school teacher. In the early 1990’s my school underwent a 4 year 20-million-dollar renovation. I was the building level rep with the architects and contractors. During this time, I learned far more about HVAC than I ever desired. The whole project was a great learning experience for me even if it was info I didn’t really need. I have seen residential Hydro Air featured in several This Old House projects.
Related links:
Listener Feedback 2:
Mike Guertin writes: Hi Patrick, I enjoyed and learned quite a bit listening to your ProTalk podcast interviews with Rich Lavoie and Chad from Mitsubishi (particularly liked his wall-hung cover ideas). Several mentions of problem ductwork during those interviews and the regular podcast 443. In one (or perhaps all of them) you asked something to the effect “what can we do to improve the way ducts are installed.”
I had lunch with Rich Trethewey and John Siegenthaler – author of Modern Hydronics – at the old CBTC expo in 97. Rich pointed out that in the early 1900s through the 1940s or 1950s that 30% of the cost of a new home was the heating system. Then as cost of equipment came down and other costs went up so home owners / buyers no longer valued HVAC. Then came the race to the bottom.
Rich’s insight and reflection won’t change ductwork but it does illustrate that homeowners don’t place high value on something that they don’t see – even if it impacts their comfort (well, at least not until it doesn’t work at all). Homeowners usually don’t know what they are getting when they buy an HVAC system package. And they wouldn’t know a good design and installation from a bad one.
I truly believe that the only pathway to good ductwork is minimum building code enforcement. First, every house needs a blower door test. Whether it’s a new home or an existing one. The IRC requires that HVAC systems be sized to meet Manual J. In order for that calculation, the modeler needs to know the air-leakage rate, the insulation levels, the surface areas, the window Ufactors and sizes and other inputs. Second, a Manual D calculation needs to be made to size ductwork for a system. Third – A manual S needs to be followed to match the equipment to the J and D. Finally, those calculations should be reviewed by the mechanical inspector prior to issuing a permit for a new or replacement HVAC system.
Education, complaining clients, and your disgust on the FHB podcast won’t change much in the realm of ductwork but following the code minimum requirements will improve ductwork and system sizing. When I build a home or a major reno where the HVAC system will be upgraded, I gladly pay $750 to $2500 for a qualified mechanical engineer to review the plans, make the calculations, help plan the ductwork layout, size the equipment, and advise our HVAC installer. The engineer’s fee more than pays for itself both in cost savings on equipment (they right-size everything rather than oversizing which costs more) and my piece of mind. The builder / remodeler is ultimately responsible for the decisions. And if the HVAC system doesn’t perform well – we’re the ones who get the call. I have a feeling that Rich Lavoie’s company takes the time to do an energy audit of existing homes and then designs replacement systems to suite. That’s rare from what I see. Please continue complaining about ductwork and typical HVAC installations – and add “We need code enforcement.” to your plea.
Related links:
- Building Codes for Insulation and HVAC in Attics
- Why is There Water in My HVAC Ducts?
- HVAC Ducting: Rigid Metal vs. Flex
- Sizing HVAC Equipment
Listener Feedback 3:
Trey writes: Hi, I completed this deck project and was wondering if your team at FHB provides critiques, suggestions,… thanks, Trey.
![]() |
![]() |
![]() |
![]() |
![]() |
![]() |
![]() |
![]() |
Question 1: Can I use Cedar Breather under roof asphalt shingles to create a drainage space above my unvented attic?
Joey writes: Hey podcast crew, Love the show guys! I’m in the early stages of construction of building my family’s new home outside of Houston (Climate Zone 2), and I’m curious if I could use the Cedar Breather product from Benjamin Obdyke under asphalt shingles to create a drainage/venting space above our unvented/conditioned attic which will house our mechanical systems. I’m comfortable with the insulation & vapor diffusion port details of the attic/roof as laid out by Joe Lsitburek, but I’d like to vent the roof itself, & the roof area is quite large, & with material costs being so elevated, adding furring strips and a second layer of Zip or OSB isn’t in the budget. I looked online but couldn’t find any insight on using Cedar Breather with asphalt, (which might be all the insight I need).
Thanks for everything you do.
Related links:
Question 2: Why don’t people just extend their 10-15 mil subslab vapor barrier underneath their footing and tie into external foundation/wall air barrier?
Doug in Potomac, Md writes: Why don’t people just extend their 10-15 mil subslab vapor barrier underneath their footing and tie into external foundation/wall air barrier? This could be accomplished by laying out a 6-foot strip of the poly/stego etc underneath footing forms before concrete, then taping later to subslab vapor barrier and external foundational water proofing. This immediately prevents ANY vapor entry water wicking up foundation wall, and ANY radon entry into basement. It also eliminates ANY thermal bridging by allowing two inches of insulation isolation between side of slab, footing and vertical foundation wall without worrying about water vapor/radon entering at the perimeter.
Related links:
Question 3: Is a whole-house ventilation strategy at odds with the goals of building performance and energy efficiency?
Mark writes: Hi Patrick and FHB Podcast Crew! Every spring I swear I am going to install some attic fan-type ventilation in my home to exhaust the coming summer’s heat while drawing in Vermont’s cool evening air. I’ve yet to bite the project bullet however because of the need to punch a commensurately-sized opening in my home’s building envelope to ventilate that exhausted air. Cutting a 2.8 square foot net free area hole in my weatherized, dense-packed Cape roof, ridge and soffit vent plugged, basement box-sill foamed home seems nuts!
So, here’s the question: Am I nuts to consider it? A ventilation contractor colleague of mine who I consulted about the project said to me in his best Brooklyn accent, “Fugetaboutit! Buy an air-exchange heat pump instead.”
I remember my grandparents’ home where a window fan was turned on to ‘exhaust mode’ after all but one window was closed to the outside. I can still hear the roar of that ancient Hunter fan as the hot air fled the house. I keep imagining one of Tamarack Ventilation’s 1600 CFM energy-efficient whole-house units with self-sealing insulated shutters installed in the 2nd floor ceiling, perhaps paired with a Vermont lazy window in the roof gable, open in summer, closed in the fall.
So my question is whether a whole house ventilation strategy is totally at odds with the goals of building performance and energy efficiency? Is a higher-tech solution like an air-exchange heat pump the only means to achieve what you and Kiley call ‘climate resiliency’? Thoughts?
Related links:
Question 4: How do I separate the primary bedroom and bathroom with a decorate popout in the way?
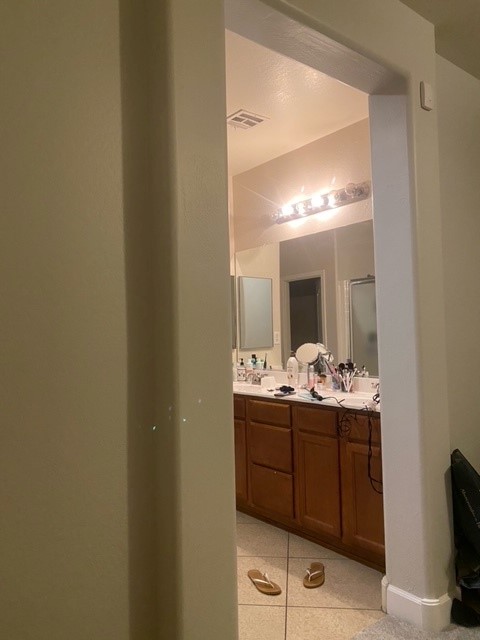
Jesse writes: Hi FHB podcast, After getting married in a couple weeks, my fiancé and I will be living in a home where there is no door between the primary bedroom and bath. We both work in healthcare and wake up about 4am but don’t always work the same days. I’d like to add a door or separate the bathroom so we do not disturb each other on those days that we work different shifts. However, the wall leading into the bathroom has a decorative pop out about 6inches from the wall. The entrance is about 3ft by 9ft. so the pop out and the size leaves me unsure how to separate the bathroom from the bedroom. Please help.
END NOTES:
![]() |
Check out our latest Project Guide: Siding & Exterior Trim!
Check out our FHB Houses:
Visit the Taunton Store • Magazine Index • Online Archive • Our First Issues • All Access
Help us make better episodes and enter for a chance to win an FHB Podcast T-shirt: www.finehomebuilding.com/podcastsurvey
If you have any questions you would like us to dig into for a future show, shoot an email our way: [email protected].
If we use your question we’ll send you a FHB Podcast sticker!
FHB Podcast T-shirts!
Represent your favorite podcast! Available in several styles and colors. Made from 100% cotton. Find the Podcast t-shirt and more cool products in the Fine Homebuilding Store.
This episode of the Fine Homebuilding podcast is brought to you by Bilco.
And also brought to you by JOBBER
If you run a home service business like – painting, contracting, lawn care or cleaning, your to-do list is endless. From hiring staff to mountains of paperwork, not to mention, doing the actual work that pays the bills! Jobber is a mobile and online app that helps you organize your business and look professional. With Jobber, you can quote jobs, schedule your crew, invoice and get paid all in one place. Try it free today at GetJobber.com/FineHomebuilding.
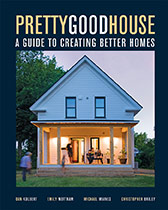
Fine Homebuilding podcast listeners can now get 20% off anything in the Taunton store, including Pretty Good House.
Use the discount code FHBPODCAST to take advantage of this special offer.
We hope you will take advantage of a great offer for our podcast listeners: A special 20% off the discounted rate to subscribe to the Fine Homebuilding print magazine. That link goes to finehomebuilding.com/podoffer.
The show is driven by our listeners, so please subscribe and rate us on iTunes or Google Play, and if you have any questions you would like us to dig into for a future show, shoot an email our way: [email protected]. Also, be sure to follow Fine Homebuilding on Instagram, and “like” us on Facebook. Note that you can watch the show above, or on YouTube at the Fine Homebuilding YouTube Channel.
The Fine Homebuilding Podcast embodies Fine Homebuilding magazine’s commitment to the preservation of craftsmanship and the advancement of home performance in residential construction. The show is an informal but vigorous conversation about the techniques and principles that allow listeners to master their design and building challenges.
Other related links
-
- All FHB podcast show notes: FineHomebuilding.com/podcast.
- #KeepCraftAlive T-shirts and hats support scholarships for building trades students. So order some gear at KeepCraftAlive.org.
- The direct link to the online store is here.