Podcast 451: Finishing a Wet Basement, Ground-Source Heat Pumps, and Basement Garages
Andrew, Kiley, and Patrick hear from listeners about supply chains and music on the job before taking questions about finishing a wet basement, ground-source heat pumps, and squeaky floors.
Follow the Fine Homebuilding Podcast on your favorite app. Subscribe now and don’t miss an episode:
![]() |
![]() |
![]() |
Help us make better episodes and enter for a chance to win an FHB Podcast T-shirt:
www.finehomebuilding.com/podcastsurvey
Doug is surprised that we don’t know about hydro-air systems. Mike says better code enforcement will lead to better HVAC systems. Joey asks if he should vent under his asphalt shingles. Doug wonders why builders aren’t putting vapor retarders under foundation footings. Mark wants to know if whole-house fans are a good idea. Jesse needs a separation between his primary bath and bedroom.
Editor Updates:
- Ian framing, electrical box, service upgrade 100-200amp sorting tools
- Kiley’s garden tools, more gravel
- Jeff’s lawn
- Patrick’s Makita battery-powered lawnmower
Related Links:
![]() |
![]() |
![]() |
![]() |
![]() |
![]() |
Listener Feedback 1:
John writes: Dear Podcast, I have not written in a while. With much humility and all due respect let me offer this feedback on the supply chain issues.
I make no bones that I am not professional contractor, architect etc. I do have some professional experience in replenishment and forecasting.
Listening to the podcast today, brings up many times when you all have tried to address this issue, but maybe not so successfully. You hit the details well but necessarily the big picture.
I would recommend to your easily distractible listeners a book. The Goal, by Eliyahu M. Goldratt.
I believe the author is a physicist by trade but offered a critique on the manufacturing world using something called the Theory of Constraints.
TOC put simply, is finding the one thing in your entire process that is constraining your entire output.
The book is in a novel form, but his elegant metaphor is that of Scouts on a hike where they all have to make a destination and the rule is everyone has to keep their place in line.
If the slowest person is at the front of the line, it slows the entire line down. While this was being applied to manufacturing, it is the same pretty much anywhere else. In supply chain the product you are making is a delivery.
We have spent 40 years tuning supply chains to get to all of this Just in Time nirvana, as an industry an enormous amount of cooperation was required to achieve the state it was in at the end of 2019.
Quite suddenly it was every man (or woman) for themselves. Suddenly rather than optimizing the entire system. Like with lumber, from the forest to the mill to the distribution tiers etc. Everyone is making decisions to benefit their particular situation.
While there is a lot upward price pressure the system has actually held up quite well.
I don’t have a magic answer. The podcast gave a good point of view of how they have dealt with this.
In my experience when our 30-person group was experiencing lower service levels and management would tell us to buy more, we would buy less, because when the inventory came in they would be say, Why the heck to do have all of this stuff? At which point we would buy more. Without making this too lengthy, what Dr Deming would say is that sub optimums do not optimize a system.
If your Toyota and control everything aspect of what goes in to a car (and with the chip shortage even they are struggling) it is easier to keep the factory running. It seems from listening to your show there is nothing controlling any of the supply chain from end to end. And what many academic papers have shown is that small disruptions at one point in the chain are amplified throughout the supply chain.
Keep up the great content. We are working on requiring more efficiency in our homes in Oak Park. Heat Pumps are a hot topic. Who would have thought?
Thanks, and have nice weekend.
Related links:
- Will the Costs of Residential Building Go Down?
- Gross Profit Margin for Building Projects
- The Anatomy of a Building Project’s Price
Listener Feedback 2:
Steve writes: Hi guys – Here’s a non-air sealing, non-tape strength topic:
As a little kid, I remember the record player in my dad’s workshop (old country, like Porter Wagener or Ernest Tubb, or bluegrass. Later, in high school, we did a complete gut/rebuild and my class schedule allowed me to work with the crews 3 hours a day. First digging and schlepping materials, taking down brick chimneys, salvaging lumber, etc., but later on installing fire blocking and decks, and finally laying hardwood floors. They always had music going, usually country or bluegrass (we lived in Cincinnati) unless the guy who called himself Fern wasn’t there, then it was classic rock. One carpenter worked on Saturdays and he listened to the local classical station.
When I lived in Chicago, there was usually music coming out of worksites, often Polish or Mexican. These days, I rarely hear music on worksites in Michigan.
Is there something going on? Maybe as the music landscape has fragmented, crews can’t decide on a station that everyone will agree to? Maybe there are more mistakes if there is music interfering with communication? Is it less safe?
Curious about your thoughts.
Listener Feedback 3:
Rick Harrahill, Master Electrician, writes: FHB Podcast members, In Episode 447, there was some discussion regarding the height of electrical outlets from the finished floor. While it is true that there is no minimum or maximum height (as long as it is not a GFCI or other protective device), the NEC Handbook Appendix J has some helpful information regarding design considerations for American Disabilities Act (ADA) Standards. This Appendix is strictly for Information Use Only (not a requirement), but it does recommend outlet and switch box heights of greater than 15” and less than 48″ from the finished floor in order to make it easier for someone in a wheelchair to reasonably be able to plug in something or turn on the lights…etc.
That being said, if the homeowner wants their outlets placed relatively low, such as in the Trim pieces 3′ off the floor, that is most likely where I would install them. But, I would bring the ADA recommendations to their attention, in case it becomes important to them later on in their lives.
You have a heck of a good Podcast and I thoroughly enjoy listening to you. Thank you for what you do for all of the Skilled Trades.
Related links:
Question 1: Should I fill basement slab cracks with crack filler during slab prep?
Lucas writes: Hello and thank you for your great podcast!
If you are not completely bored with yet another question about basements and water!!! I am in need of some advice. I’m pretty much in the camp that basements (at least basements in 100-year-old houses) should not be finished. But, covid… rambunctious noisy kids… my wife… etc. and now I am going to finish the basement. I’ve watched a bunch of your videos and read your articles on this, but as with all projects there are always constraints and nuances!
THE CHALLENGES:
– water (no surprise there). water visibly leaks through the walls after a good rain (you can audibly hear a trickling sound!) and the slab cracks get dark with moisture (but no water visible). the sumps work hard!
– ceiling height is lowish (no surprise there either). so, need to be careful about adding too much height to subfloor.
CURRENT STATE: We have an interior perimeter drain and sumps, with about 4 inches of dimple mat tucked into the concrete to take the wall water into the drain. On the walls is a vapor barrier that goes from the floor up to grade (about 5′).
![]() |
![]() |
![]() |
CURRENT PLAN – SLAB:
– clean cement floor
– prime (something like MAPEI EcoPrim Grip)
– apply a leveler (something like MAPEI Leveler)
– lay down dimple mat (something like Delta FL) and tape seams
– lay down 1/2 plywood
– not sure if I will do vinyl plank or carpet or click tiles (maybe depends on how level it is)
CURRENT PLAN – WALLS:
– replace existing vapor barrier with dimple mat on walls
– add 2″ rigid foam to walls over dimple mat on walls and in joist cavities
– frame the walls using non treated studs on top of the plywood subfloor
– drywall on the studs
QUESTIONS:
– How’s this plan above sound? Would you do anything different?
– Should I fill slab cracks with crack filler during slab prep? They only get moist, no visible water.
– Would you also go with the Mapei product set, or a different approach? The whole basement is sloped to a central floor drain (which i will continue to use), and there are many bumps and valleys. So the leveling cement is hopefully going to just smooth things out a bit for the flooring (not totally level the floor).
– Should I bother replacing vapor barrier with dimple mat? I’m worried about mold under the vapor barrier. The walls leak a fair amount of water. Also, shouldn’t the rigid foam be tight on the wall for best insulation? So, should I do dimple mat OR foam, but not both?
– Is there a better way to do the subfloor? I worry about adding too much height. The approach above adds about 3/4″ (dimple + 1/2″ ply), but could go with a 1/2″ rigid foam + 1/2 plywood… but that may not give me enough room to let things dry out before moisture hits non-treated plywood… I think the recommended 1″ rigid foam + 2 layers of 1″ plywood would add too much height.
– Any other thoughts / considerations?
Related links:
Question 2: What are the pros and cons of a geothermal heating and cooling system vs. solar?
Kyle from Whidbey Island relocating to Topeka Kansas writes: Hello FHB Podcast, We are in the early stages of planning our new home build in NE Kansas. We have a 5-acre parcel (roughly 650’x350’). We are looking into the options of having either a geothermal heating and cooling system or the option of solar. In this area these options are not common place, as most homes are powered by NG/propane furnace/water heater and electric AC. We get all seasons, hot summers and cold winters. Most of my research in geothermal turns up older articles while most things seem to be shifting to solar. In my preliminary research with a local Geothermal and HVAC contractor. For our 2000 sq ft main floor home with full basement, the cost for a conventional HVAC system would be $12-13k. While the cost for a equivalent geothermal system would be $32k before a 27% tax credit. That price is inclusive of labor, equipment, drilling the 4 200-300’ deep wells. So roughly $10k more than the conventional system. This seems like an acceptable cost increase if geothermal is a better option. A few years ago, we got a quote to add a PV option to our old house and the estimate was $60k which was way more than we would ever spend in our market. Any info/articles/opinions are welcome.
Thanks, Kyle
This is a great question Kyle and thank you for listening. How much total SF are we talking about? What are your goals for the build with regard to windows and envelope? Do you have plans yet?
Thanks for the response. We haven’t designed the plans yet but are thinking we want to try and make a very modern home similar in style to this. We are thinking around 2000 sq ft on the main floor with a full 9’ walled basement. We will finish part of the basement maybe 1000 sq ft, leaving the rest unfinished for a gym and storage area.
We would love to build a high performance home but our budget($550k) won’t allow that. I have sent the recent article, Building a Zero-Energy Home for Less, to our builder as they haven’t really built like this before. We don’t expect a passive house or anything but want a well-built/efficient home. They are open to trying some of these approaches but we will see. We are hoping to start our plans in the next coming weeks.
Related links:
- Ground Source Heat Pumps and Air Source Heat Pumps: Are They as Energy Efficient and Green as Advertised?
- AeroBarrier: New Technology Improves Airtightness
Question 3: Should I build a basement garage?
Chris in Poestenkill, NY writes: Hey Guys, I’m building a new home in upstate NY just outside of Albany. I’ve been devouring your shows so thank you soooo much.
Here is my question…
I’m considering a basement garage for several reasons:
– I feel the design of the house would look far better without a garage.
– I think I could get more space for less money.
– I have a 1.5-acre lot and a smaller house footprint would work better.
– Shorter, less steep driveway.
– Garage would not obstruct view
– The garage would stay warmer in winter and cooler in summer.
The only downside I can think of is carrying stuff up the stairs. I feel exercise is good but I could also put in a dumbwaiter.
Thanks for your feedback.
ALSO: I have a Tesla and am a little nervous about charging it in the basement. Out of 2 million sold, there was one fire in CA that burned down the house. I am researching this topic using data from NHTSA. My theory is that the cause was the age of the car and the owner charging it to 100%. If the car is newer than 2015 and you set the charge limit to 90%, I believe the risk is extremely low or zero. I will let you know when I finalize my research. I will also be researching fireproofing for peace of mind.
Related links:
- Conditioned House Meets Unconditioned Garage, Part I
- Conditioned House Meets Unconditioned Garage, Part II
Question 4: How should I fasten a new 1/4” layer of plywood on my squeaky floor?
Chris in Fort Wayne, IN writes: Hello FHB podcast team! I purchased my house at auction just under two years ago. I’ve been redoing everything since. The house is larger than we need so I finished the necessary rooms and have two rooms upstairs that remain gutted. As a remodeling contractor I have seen a lot but I have a new one on this house. Every square foot of the house seems to have some sort of squeak in the floor. As I began remodeling it was easy to see the culprit. They had nailed down 5/8” plywood for their subfloor, then (after the walls were built) laid 1/4” plywood over it and nailed it on top. I can take guesses as to why they may have used two layers like this (maybe it didn’t pass inspection and this was a remedy, maybe 5/8” showed up instead of 3/4” and this was the solution) but at any rate the confusing part is that they used L-cleat nails to fasten all of the 1/4” plywood to the 5/8”. Have you ever seen this? Neither layer is glued. (Built in 60’s so glue wasn’t in practice). My first solution was to tediously find each squeak, find the closest joist and screw down. I had gotten 95% of the squeaks out with this method. But as we were living there more squeaks developed furthering my frustration. So, on the unfinished rooms I decided to pull up that 1/4” layer on top. I found the majority of the squeaks were from the nails fastening the 5/8” plywood. Joists were easy to find so I screwed about every 6” along every single joist. RIP my hands and knees and the big box of screws I went through.
Anyway, here’s my question… how would you go about fastening the new 1/4” layer down? Should I glue and staple? Try to find smaller screws to just fasten to the now overly fastened under layer? Or try to fasten directly to the joists with longer screws? My nervousness is that only being 1/4” thick it’s easy to over fasten and create the potential for more squeaks! Ahhh! Haha
Thanks for reading my long email. I love listening to the podcast as I’m working around the house. Keep up the good work.
END NOTES:
Building a Net-Positive House: Episode 1, ICCF Foundation
![]() |
![]() |
Check out our latest Project Guide: Siding & Exterior Trim!
Check out our FHB Houses:
Visit the Taunton Store • Magazine Index • Online Archive • Our First Issues • All Access
Help us make better episodes and enter for a chance to win an FHB Podcast T-shirt: www.finehomebuilding.com/podcastsurvey
If you have any questions you would like us to dig into for a future show, shoot an email our way: [email protected].
If we use your question we’ll send you a FHB Podcast sticker!
FHB Podcast T-shirts!
Represent your favorite podcast! Available in several styles and colors. Made from 100% cotton. Find the Podcast t-shirt and more cool products in the Fine Homebuilding Store.
This episode of the Fine Homebuilding podcast is brought to you by Bilco.
And also brought to you by JOBBER
If you run a home service business like – painting, contracting, lawn care or cleaning, your to-do list is endless. From hiring staff to mountains of paperwork, not to mention, doing the actual work that pays the bills! Jobber is a mobile and online app that helps you organize your business and look professional. With Jobber, you can quote jobs, schedule your crew, invoice and get paid all in one place. Try it free today at GetJobber.com/FineHomebuilding.
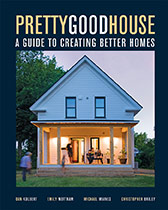
Fine Homebuilding podcast listeners can now get 20% off anything in the Taunton store, including Pretty Good House.
Use the discount code FHBPODCAST to take advantage of this special offer.
We hope you will take advantage of a great offer for our podcast listeners: A special 20% off the discounted rate to subscribe to the Fine Homebuilding print magazine. That link goes to finehomebuilding.com/podoffer.
The show is driven by our listeners, so please subscribe and rate us on iTunes or Google Play, and if you have any questions you would like us to dig into for a future show, shoot an email our way: [email protected]. Also, be sure to follow Fine Homebuilding on Instagram, and “like” us on Facebook. Note that you can watch the show above, or on YouTube at the Fine Homebuilding YouTube Channel.
The Fine Homebuilding Podcast embodies Fine Homebuilding magazine’s commitment to the preservation of craftsmanship and the advancement of home performance in residential construction. The show is an informal but vigorous conversation about the techniques and principles that allow listeners to master their design and building challenges.
Other related links
-
- All FHB podcast show notes: FineHomebuilding.com/podcast.
- #KeepCraftAlive T-shirts and hats support scholarships for building trades students. So order some gear at KeepCraftAlive.org.
- The direct link to the online store is here.