Dos and Don’ts of a Pretty Good House
Two example assemblies demonstrate how to incorporate low-carbon strategies for better comfort and energy savings.
I’ve written previously about a few techniques I use when designing high-performance, low-carbon homes, such as building a concrete-free slab foundation (see “Minimizing concrete in a slab-on-grade home,” FHB #282). What follow are two concept houses that show examples of how proponents of the original Pretty Good House (PGH) movement can incorporate low-carbon strategies. While somewhat more complicated and more expensive than code-minimum assemblies, they provide much better comfort and energy savings. They also allow for smaller heating and cooling systems without much increase in embodied carbon or changes to conventional practices.
Concept House #1
Foundation
Concrete has high embodied carbon, but a slab on grade with sealed concrete as the finished floor is usually the least expensive approach, and up to 50% of the carbon-polluting Portland cement can be replaced with pozzolan admixes. With most slab-on-grade homes that have insulation under the slab, the insulation is located directly below the concrete, but this makes it hard to do a good job with the insulation, and there should be insulation below the turned-down footing anyway.
A simple approach is to grade and compact crushed stone, then form the perimeter with foam, add a layer of foam, and top with compactible fill. I spec borate-treated EPS insulation for use below grade; recycled XPS is another option. Don’t use polyiso because it absorbs too much water, and don’t use new XPS because the energy savings will never make up for the climate impact of its manufacturing process. For the form edges, consider WarmFörm by ByggHouse. Compact the fill in 6-in. lifts, cover with a heavy-duty vapor retarder, add reinforcing steel where necessary, use a concrete mix with microfibers to reduce fine cracking, and allow the mix to damp-cure slowly to improve the strength—most concrete needs to be kept damp for a week to reach 90% of its design strength. In cold climates, consider adding a frost wing even if it’s not required by code—thick insulation under the footing can leave it susceptible to frost heave. The thermal mass of this floor system will help maintain even heat levels. (Don’t bother with in-floor heating—in a well-insulated, air-sealed house, you won’t get the warm-floor effect.)
Windows
Windows, like double-glazed, flanged fiberglass windows, perform best when located near the center of the wall. In cold climates, triple glazing provides improved comfort and mold resistance —the added cost compared to energy savings depends on the choice of window.
Roof
The roof framing is a gusseted rafter system, which is a good way to get decent levels of insulation and ventilation without having to use foam. To maintain ventilation space between the roof deck and the insulation, I spec 11/2-in.-thick AccuVent from Brentwood Industries. It is made of 100% recycled PVC. (PVC, an environmentally damaging plastic, should generally be avoided unless the material has been fully recycled). If you can afford the cost of a bit more labor and materials, an even better approach is to make your own insulation baffles from 1⁄4-in. plywood and softwood 1x2s. Conventional lightweight foam baffles won’t stand up to dense-pack cellulose insulation, which is installed here at 161/2 in. thick for a total of R-60. Dense-pack fiberglass or wood fiber are other insulation options.
At the interior, painted drywall can control air and water-vapor movement, but for safer performance (in Maine’s cold climate) I usually spec a variable-permeance membrane. In New England we always fur down ceilings with strapping, but with the gusseted rafter system it’s not necessary. (Where there are lights or other penetrations in the ceiling, don’t rely on airtight fixtures, which are never truly airtight—instead, make a simple box from 2x4s, plywood, and tape.) For airtightness, it’s important to connect the air control layer at the wall—in this case, the sheathing—to the air control layer at the ceiling—in this case, drywall. A continuous plywood ledger provides nailing for the subrafters and code-required fire blocking; when taped to the top plate, it also acts as the air control layer.
Walls
Continuous exterior insulation essentially eliminates thermal bridging and keeps the sheathing warm and dry. Rigid foam is the typical choice, and recycled foam of any type can work; new foam comes with relatively high embodied carbon. Rigid wood-fiber insulation, such as Gutex or Steico, is a great choice. Even after shipping from Europe, the carbon footprint is smaller than alternatives, and it’s easy and safe to work with. Its price tag is on the high side, but GO Lab is gearing up to start producing wood-fiber insulation in Maine, with plans for an affordable price point. Siding is real wood over a ventilated rainscreen, which greatly extends the lifespan of the wood and any coatings. Framing is 2×6 with dense-pack cellulose in the bays. Cellulose has the lowest upfront carbon emissions of any commonly available insulation, and it has several performance and safety advantages. GO Lab also has plans to produce a wood-fiber product that will compete with cellulose. Another option is to fill the bays with fiberglass. Although many environmentally minded designers and builders prefer mineral wool to fiberglass, mineral wool has much higher upfront carbon emissions. Fiberglass installed tightly in a fully airtight cavity, with exterior insulation, performs as advertised. With acrylic tape sealing the joints, the sheathing doubles as the air control layer.
Concept House #2
Foundation
A pier-and-beam system using helical metal piers has much lower upfront carbon emissions than a concrete foundation. Piers are located to carry pressure-treated wood beams to support the floor framing. When the top of the piers are more than a few inches above grade they need bracing, so instead I’m showing a bolster system to create the height needed to allow code-minimum 18-in. clearance from grade to the bottom of the floor system. The beams are inset enough to allow for ventilated skirting. The floor system can be dimensional or engineered lumber; I prefer I-joists because the narrow webs nearly eliminate thermal bridging, allowing for about R-40 for the whole floor system when insulated with dense-pack cellulose, wood fiber, or fiberglass. To keep out air and critters, 1⁄2-in. sheathing is installed below the joists and sealed to the beams. (If you’re in an earthquake-prone zone, this system may not work for you, but it pairs well with a partial basement that can provide additional lateral support and a place for utilities.)
Windows
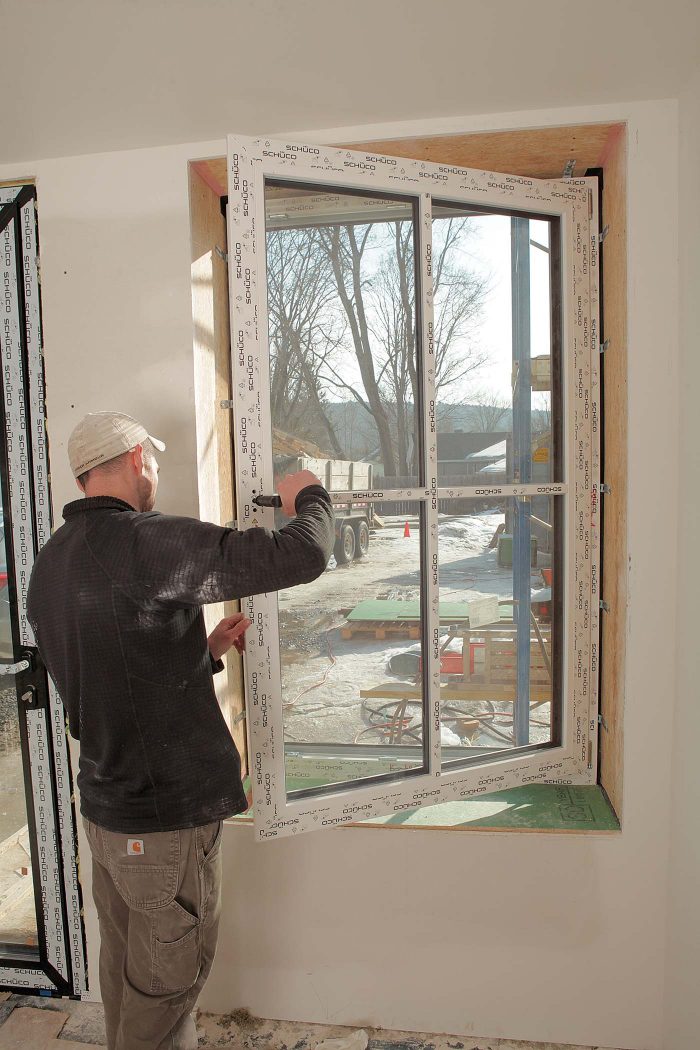
European-style triple-glazed tiltturn windows are significantly different than standard American-style windows, but once you’ve experienced their quality and comfort, it’s hard to go back to comparatively flimsy American windows. They are best installed at the center of the wall, but with a minor performance penalty they can be flush with the sheathing. They are usually installed with clips instead of flanges; specialty tapes are available to keep water out and provide airtightness.
Roof
The least expensive, lowest-carbon way to build and insulate a roof is usually a raised-heel truss with loose-blown insulation. I typically spec R-60 cellulose at 16 in. deep. Raised heels can make walls look tall, so I reduce the insulation depth at the eaves to 10 in. to 12 in. The air control layer is at the ceiling, in the form of a variable-permeance membrane, but taped 1⁄2-in. sheathing works too. Inside of that, install furring to create spaces that can be used to install lights and run wires without puncturing the air control layer.
Walls
Builders have strong feelings about double-stud walls, but they have a long track record in New England, and the builders I work with tend to like them. In a cold climate, they need to have a ventilated rainscreen so they can dry easily to the exterior. In cold climates I am most comfortable when a variable-permeance membrane is used at the interior, though many builders just use painted drywall. With a 12-in. insulation cavity, the wall will perform at about R-40. The sheathing doubles as the air control layer.
Products to minimize or avoid when building a Pretty Good House
When it comes to building a PGH, everything in the equation must also come into consideration, including materials and appliances that are being incorporated. Here are a few products you want to try and skip when building a home.
Concrete—specifically Portland cement, which contributes over 8 % of all global warming emissions. Consider modern additives such as CarbonCure or more traditional pozzolan admixes. Helical metal piers, which are screwed into the soil to support structures, are gaining ground as an alternative foundation to concrete pours. Steel is also carbon-heavy, but emissions from this type of foundation are much lower than from a concrete foundation.
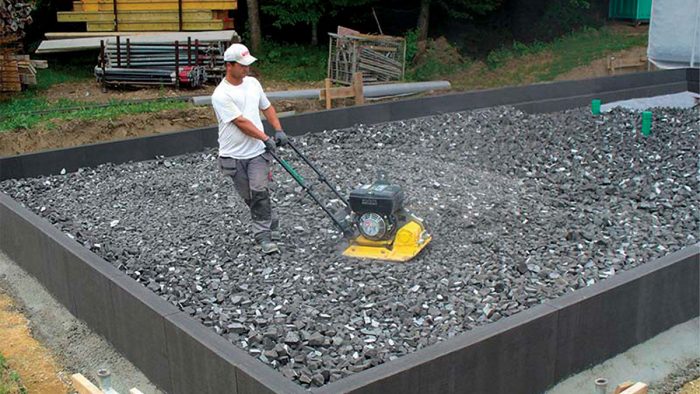
Foam, particularly hydrofluorocarbon (HFC)-blown closed-cell spray foam and extruded polystyrene (XPS) rigid insulation. A PGH uses no foam above grade. If you do use it, try to find a source for recycled rigid foam, or use foam with relatively low global warming potential, such as EPS and polyisocyanurate instead of XPS, and spec hydrofluoroolefin (HFO)- blown spray foam rather than HFC-blown.
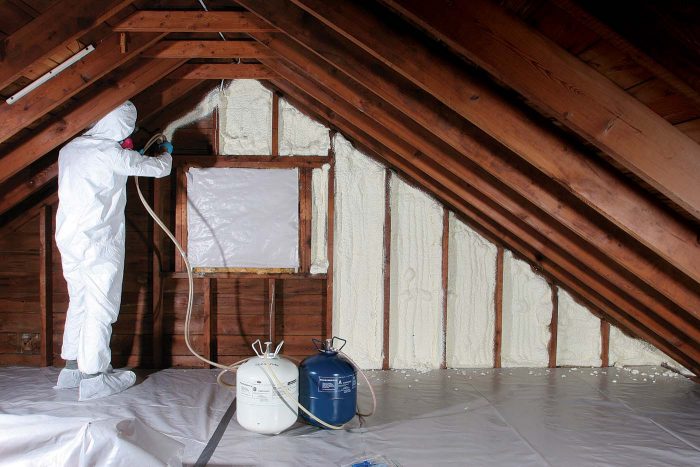
Combustion appliances, especially those that burn fossil fuels. You can have a woodstove in a PGH, but make sure it is EPA-certified and properly installed; and use dry, sustainably harvested firewood.
Unhealthy materials—Fortunately asbestos is no longer allowed in homes, but fiberglass fibers have a similar shape, which is not a problem for occupants if the batts are sealed inside a cavity, but can be an issue if air moves through the assembly. Formaldehyde is commonly used as an adhesive in sheet goods such as those in inexpensive cabinets—avoid it. Avoid, also, plasticizers in flexible vinyl products such as shower curtains; choose nylon curtains instead. Carpeting, even with natural fibers, collects detritus, which can affect air quality. In general, natural products are safer than manufactured products.
Photos courtesy of Brian McAward, Matthew Millham, Justin Fink and Glavel (manufacturer).
RELATED STORIES