Podcast 453: DIY Data Logging, Native Pine Paneling in an Unheated Space, and Gurgling Pipes
Andrew, Ian, and Patrick hear from listeners about construction costs, SIP panels, and sliding doors before taking questions about monitoring humidity levels, pine paneling in an unheated outbuilding, and noisy pipes.
Follow the Fine Homebuilding Podcast on your favorite app. Subscribe now and don’t miss an episode:
![]() |
![]() |
![]() |
Help us make better episodes and enter for a chance to win an FHB Podcast T-shirt:
www.finehomebuilding.com/podcastsurvey
Chris decided to buy rather than build. Dack asks, “Why can’t we save the planet and solve the housing shortage, in style?” Kenneth thinks a sliding barn door should separate an en-suite bedroom. Brian builds a homemade hygrometer. Alex asks if it’s okay to panel his unheated barn. Hans needs help finishing the insulation on his rebuilt roof.
Editor Updates:
- Ian’s Belize trip
- Andrew’s lumber
- Jeff’s basement
- Patrick’s been decorating
![]() |
![]() |
![]() |
![]() |
![]() |
![]() |
![]() |
![]() |
Listener Feedback 1:
Chris from Binghamton (soon to be GREENE, NY) writes: Greetings FHB Crew, I just wanted to take a minute and update you all. A couple weeks ago my wife and I had a meeting with our builder and he shared some numbers that made my eyes pop out of my head. We spent a couple weeks trying to make the math work. In the end, we couldn’t do it. So we have abandoned our plans to build. It was an excruciating decision, but in the long term, it makes much more financial sense.
In total, the failed experiment will cost us money, but I have to say that it wasn’t a complete waste. Engaging in the planning process has changed the way I view and understand homes on a number of different levels. Understanding the home as a system, acknowledging the carbon embodied in materials and not just emissions, recognizing the difference between temperature and comfort, just to name a few. So, I know my experience as a homeowner will be much different moving forward after having gone through this effort.
Speaking of being a homeowner, after making the final decision to give up on home-building, I turned, as many do, to doom scrolling on Zillow. I came across this property … and decided to get back on the proverbial horse. My wife and I viewed the house this morning, put in an offer and have signed a contract. Although we won’t be sticking with the eternal blue theme for long, the home has many of the qualities we were looking to include in our designed home. We think it is the embodiment of “pretty good” for us.
Built in 2018 on a 2.53-acre double lot, the home has a 42,000 btu 5 zone Mitsubishi mini-split heat pump system. Awesome 🙂 Before I put in my bid, I ran the numbers through the energy model spreadsheet Ian helped me with and the system seems to be sized correctly. Thanks Ian! The house runs off municipal electricity which currently charges a measly 7.5 cents per kilowatt hour. Sweet. The blower door test in 2019 showed 1.34 air changes/hour. Not so bad. It has mechanical ventilation of some sort, though I need to get up in the attic to check it out to see exactly what kind of unit they have running. I could go on, but I’ll stop myself. Just wanted to share a twist in our journey and also thank the entire collective crew, past and present, of the FHB podcast. I’ve learned a lot and will continue to do so, all while thoroughly enjoying the various content you all produce.
Take care,
Chris
Binghamton (soon to be GREENE, NY)
Still Zone 6a
Related Links:
Listener Feedback 2:
Dack writes: Hello podcast guys and gal: Just listened to episode 443. Ian, could your company’s move towards panelization be accomplished with … panels? I’m not in the industry but SIPs seem like an obvious solution, veering towards no-brainer. Mark LaLiberte and Justin Wilson (the Construction Instruction guys) are both big fans, and Lstiburek wrote a book about them. That’s good enough for me.
I’m working on a small cottage project with Minneapolis-based timber framer. It’s only 900 square feet, but the estimate to have a frame cut, erected, enclosed in SIPs, and a 5-man crew to drive from MN to northern WI (and back) and spend 5 days putting it up is $80K. Granted, it’s missing a lot of things, like a foundation, but this seems like an affordable, fast way to get stylish, durable, high R-value shelter.
In fact, I see an opportunity here:
* automate the labor-intensive timber framing piece (the Germans, naturally: https://www.homag.com/)
* enclose in SIPs
* offer consumers a range of combinable modules (like https://www.thebackcountryhutcompany.com/ but practical)
* PV-ready roofs for net zero
Let’s save the planet and solve the housing shortage, in style. Who’s with me?
Dack
Related Links:
Listener Feedback 3:
Kenneth from YouTube writes: In episode 449 Jesse was wondering about a door for his bath. How about a contemporary barn door? Minimal trim. Easier (?) to create a custom sized barn door. The only drawback is the door and door hardware would need to extend off the wall to match the depth of the decorative column.
Related Link:
Question 1: Is there a DIY budget friendly way to monitor humidity in wall assemblies?
Brian writes: Wall Humidity Monitoring? We are finishing a portion of our basement and I am curious if you or anyone on the show/audience has found a DIY/homeowner budget friendly way to monitor humidity in wall assemblies? I know consumer hygrometers aren’t super well calibrated, but after finding an old terrarium hygrometer I had laying around I was wondering if this would help discover if there is any dramatic changes inside wall assemblies (specifically the laundry room). My DIY thought was basically to just drill a hole in the drywall and snake the probe through and leave it in the wall in a place I would see when doing laundry, but I didn’t want to reinvent the wheel if there is a better way to do this without doubling the cost of a wall.
Dryer Vent Specifically: The dryer vent is going to be buried in the wall and I believe I have covered my bases with a short run (12 ft or so) all seams screwed, taped and clamped and then using a full 2×6 wall so the vent isn’t being compressed to fit through 4″ cavities, but I am still terrified of the disasters I have seen with these vents causing issues in walls.
Anyway, thanks again for all that you guys do with the show, it’s been a huge source of help and motivation to keep getting my ’56 cape back into fighting shape after the previous owner let things go for about a decade.
Related Links:
Question 2: Can I use pine paneling on the walls of my barn with no drywall or vapor barrier behind it?
Alex writes: Hello Podcast crew, I’m wondering if you guys would approve of my using pine paneling on the walls of my barn, with no drywall or other vapor/air/whatever barrier behind it.
Here are the circumstances: It is a 130-year-old balloon frame structure in Western Mass. It was falling apart when I bought it, and I have gradually fixed the framing, re-sided, added doors and windows, and am basically turning it into a workshop/cabin/teenagers’ hangout. Building code, um, doesn’t really apply.
For now, I heat it only when I’m there, with a wood stove. I am gradually insulating it, one wall at a time, with cobbled rigid foam or mineral wool or whatever I find cheap. I have then found myself covering it with tongue-and-groove pine, or in the case of my kids’ space upstairs, rough sawn one-by pine, and all the while in the back of my head hearing segments from past episodes of the podcast where you guys talk about water problems in homes with pine paneling, from the moist, warm interior air seeping through the gaps in the boards and condensing on cold framing. Is this something I really have to worry about in this semi-inhabited structure? Though I don’t heat it full time, I can imagine someday having some sort of heat source that keeps it at 60 degrees or so. There will never be any running water or significant cooking going on here, and it will never be inhabited full time. What do you think? Is there some sort of easy barrier I should be using behind the pine?
Question 3: Why does my sewage pump cause the toilets and sinks to gurgle throughout parts of my house?
Perry in Duluth, MN writes: I have a sewage pump that pumps discharge from our basement washer, laundry sink and bathroom into our septic tank. After it stops pumping, the toilets and sinks gurgle throughout the house. This gurgling doesn’t happen with our main floor bathroom or sinks, which gravity feed to our septic tank. Is this a venting issue?
Thanks.
Related Link:
Question 4: How should I insulate the interior side of a roof without creating an ill performing or risky assembly in terms of moisture?
Hans writes: Good afternoon Fine Homebuilding crew. I have been a listener since I bought my fixer-upper house 3 years ago when I stumbled upon the podcast while trying to figure out how to fix the ice damming problem we were having. Little did I know that the discovery of Fine Homebuilding and subsequently Green Building Advisor would take me down a never-ending path of fixing my house, not just for energy efficiency but structurally as well.
My house is an early 1900s small cape cod in zone 6 in central Wisconsin, that has been added onto a few times over the years. When we first moved in, it was very poorly insulated and air sealed (think gable vents for the knee walls with no insulation in the floor) with asbestos shingle siding that was falling off in places. What we thought would be small changes on our way to quickly reselling the place, has turned into fully re-framing and re-sheathing the house due to rot and deciding to go all in and do a chain saw retrofit and full exterior insulation. All while living in the house while we do the work. See attached photos for some of the extensive work.
![]() |
![]() |
![]() |
![]() |
![]() |
![]() |
Onto my question. This question isn’t going to have the typical answer you usually give to these types of roof insulation questions (exterior insulation) as I have already gone ahead with that part of the project. Rather I am looking for some insight on how to best insulate on the interior side of the roof without creating an ill performing or risky assembly in terms of moisture.
I am re-roofing and adding dormers, 1 shed and 2 gable dormers to the house with the assembly structure as follows (general assembly cutaway is shown in attachment), beefing up the old spliced 2×4 rafters to 2x12s, Grace ice and water over the old board sheathing as an air barrier wrapped down onto the walls, 2 layers of 2″ polyiso rigid insulation, 2x material for creating an air gap and for the applied overhangs and then a second roof deck with shingles as the roof covering. A profile of this assembly is attached along with a few other photos of the work. To address some previous podcast discussions on finding people to do this type of work, I didn’t have too much trouble finding a contractor to do the exterior insulation, as I am rather ambitious (aka cheap) and am doing all of the work myself with the help of family and friends.
My question is based upon reading some articles on Green Building Advisor regarding combining rigid insulation and fluffy insulation and building a cathedral ceiling that works. The dilemma, the 2 layers of polyiso will give me roughly R25, which is about the minimum for my climate zone, and should make up about 50% of the insulation compared to the fluffy insulation. This would result in about 6.5″ of fluffy insulation. Since I am using 2×12 framing, I would only be filling the rafter bay 1/2 full which from what I understand is not going to make the batt insulation effective. I will be using wafer lights as well as potentially running a few pieces of duct work in the rafter bays, if that changes any suggestions.
So, in general the question is, how should I detail the interior insulation to not make my assembly risky?
My current thought is to partially fill the bay with insulation and then use a smart membrane against the insulation and taped to the rafters to add an interior air barrier against the insulation. And to answer another question you may have been thinking as you read all of this, yes, I am an engineer.
Thanks in advance for the answer(s) you may provide as well as for inspiring myself as well as others to take on these kinds of house projects in an effort to make our homes better than they were.
Related links:
END NOTES:
![]() |
Check out our latest Project Guide: Siding & Exterior Trim!
Check out our FHB Houses:
Visit the Taunton Store • Magazine Index • Online Archive • Our First Issues • All Access
Help us make better episodes and enter for a chance to win an FHB Podcast T-shirt: www.finehomebuilding.com/podcastsurvey
If you have any questions you would like us to dig into for a future show, shoot an email our way: [email protected].
If we use your question we’ll send you a FHB Podcast sticker!
FHB Podcast T-shirts!
Represent your favorite podcast! Available in several styles and colors. Made from 100% cotton. Find the Podcast t-shirt and more cool products in the Fine Homebuilding Store.
This episode of the Fine Homebuilding podcast is brought to you by Bilco.
And also brought to you by JOBBER
If you run a home service business like – painting, contracting, lawn care or cleaning, your to-do list is endless. From hiring staff to mountains of paperwork, not to mention, doing the actual work that pays the bills! Jobber is a mobile and online app that helps you organize your business and look professional. With Jobber, you can quote jobs, schedule your crew, invoice and get paid all in one place. Try it free today at GetJobber.com/FineHomebuilding.
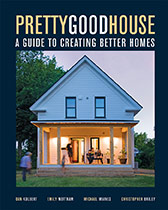
Fine Homebuilding podcast listeners can now get 20% off anything in the Taunton store, including Pretty Good House.
Use the discount code FHBPODCAST to take advantage of this special offer.
We hope you will take advantage of a great offer for our podcast listeners: A special 20% off the discounted rate to subscribe to the Fine Homebuilding print magazine. That link goes to finehomebuilding.com/podoffer.
The show is driven by our listeners, so please subscribe and rate us on iTunes or Google Play, and if you have any questions you would like us to dig into for a future show, shoot an email our way: [email protected]. Also, be sure to follow Fine Homebuilding on Instagram, and “like” us on Facebook. Note that you can watch the show above, or on YouTube at the Fine Homebuilding YouTube Channel.
The Fine Homebuilding Podcast embodies Fine Homebuilding magazine’s commitment to the preservation of craftsmanship and the advancement of home performance in residential construction. The show is an informal but vigorous conversation about the techniques and principles that allow listeners to master their design and building challenges.
Other related links
-
- All FHB podcast show notes: FineHomebuilding.com/podcast.
- #KeepCraftAlive T-shirts and hats support scholarships for building trades students. So order some gear at KeepCraftAlive.org.
- The direct link to the online store is here.