Podcast 503: Not Quite a Scrape-Off, Too Tight for Insulation, and Weather-Beaten Felt Paper
Stopping sound between floors, the world’s worst drywall finishing, insulating inaccessible attic spaces, and leaving felt underlayment exposed.
Follow the Fine Homebuilding Podcast on your favorite app. Subscribe now and don’t miss an episode:
![]() |
![]() |
![]() |
Help us make better episodes and enter for a chance to win an FHB Podcast T-shirt:
www.finehomebuilding.com/podcastsurvey
Austin shares how he made his floor quieter. Dave has thoughts on owner-builder tests and the carbon impact of wood pellets. Greg tells Patrick that restricting airflow puts less load on blower motors. Alex asks why not finish the tear-down. Mark asks what he should do about the uninsulated parts of his ceiling. Jim wonders if weather-beaten roofing felt is up to the job.
Editor Updates:
- Jeff’s Dovetail Boot Camp with Bob Van Dyke
- Ian’s European vacation, Remodelers Advantage conference, and crazy boat deck project
- Mike’s Arizona house update
- Patrick’s cooler temperatures and mice have decided inside our house is better than outside
![]() |
![]() |
![]() |
![]() |
![]() |
![]() |
![]() |
Listener Feedback 1:
Austin writes: Hey podcaster! Austin (crazy diy-er from Columbus, Ohio) here! I was just listening to Andrew talk about insulating between his floors to help with sound transmission. Well, I have 1x subflooring with pretty big gaps on my 1st floor and I too, was concerned about how sound would transmit between floors—in my case, between the basement and 1st floor. So, I did a little research and landed on Steico Natural acoustic wood fiber underlayment from Lowes.
![]() |
![]() |
![]() |
![]() |
![]() |
It comes in rigid, green 24”x36”x 1/8” sheets. They were super simple to install. I used 2 layers with offset seams. And I nailed my hardwood flooring right over it—using a slightly longer nail to compensate for the extra 1/4.” And it works great! I was really just hoping for something to take the edge off between the floors. But I have say it works way better than I expected. And it wasn’t very expensive (compared to some of the other options.) If you also stuffed your joists with Rockwool, I think you’d have almost no ambient sound transmission. It won’t help with foot sounds, but that’s a whole lot of physics.
Alright keep up the good work. I swear I’m going to write an update soon. It’s just that it’s going to be a George R.R. Martin length novel, so, I like Martin, am having a hard time sitting down to finish it. In the meantime, here’s some pics of my little crew of friends working on the flooring. (Oh and we used the rosin paper mainly to keep the green dust from the underlayment from snowing down into the basement for the foreseeable future).
Related Links:
Listener Feedback 2:
Dave writes: Hi all! I have been working a small job that’s far from my house so I have had a chance to listen to more podcasts lately – as always, you all are doing a great job! Thanks for all the effort and thought you put into it!
I have a lot of feedback, so get ready!
In episode 485 you all discussed owner-builder tests. I live in an owner-built house and I work in the heavily owner- built state of Vermont. I really wish that owner-builders were made to pass some kind of test. I’m all for the creativity and outside-the-box thinking that outsider-artist builders can bring to bear, but wow… some of the errors and omissions can be overwhelming. Take my house, for instance. You, Patrick, years ago, called the drywall finishing “the worst [you] had ever seen” which I totally agree with, and it is still that way because I can’t find the time or inclination to empty the room of all my kid’s Lego’s to make the fix. I had to replace the owner-installed well pump; the plumber said “whoever did this either knew nothing about how to do this or really hated whoever they were installing it for… just about everything was done wrong!”. I also replaced the owner-built deck that was framed in hemlock and rotten after 4 years. The framing layout restarts at every window and door opening and, if you can guess, every sheet of plywood and drywall breaks at the openings and I’ve surrendered on fixing the cracked drywall. The stud “layout” situation is maddening when trying to do, oh, anything.
The house is also lovely, and, after no small amount of retrofit work, very air-tight and comfortable. The previous owner-builder is a friend, and our kids are best friends, so I’m complaining to you knowing he will never listen to this podcast. I’m not angry with him, at least not anymore, but he is not a builder. And! He was one of the better owner-builders out there from what I have seen. I think people build their dream house believing that it’s the last house for them, but they either don’t live forever or things change… It’s not the best situation for a buyer to purchase someone else’s ‘good’nuff’ house given how expensive repair work is. I really like the Canadian warranty that owner builders have to give – all my issues would have been paid for by not me; but maybe our kids wouldn’t be allowed to be friends, so… I don’t know…
I have been working a massive remodel project for the last 15 months (!) and it, too, was an owner-built structure. It has been a complicated headache producing nightmare of issues. None of us could have guessed this was the case because so much care and attention was given to the finishes that we all assumed the structure, too, was well executed. Not so much!
It has been my experience that one of the hardest learned lessons in the trades is patience. One of my mentors was a very patient carpenter and as my youthful enthusiasm began to morph into benign cynicism, I eventually came to understand that it’s best to work a task to total completion before moving on. Others always teased him about being slow, but it didn’t take me long to recognize that he worked significantly faster than his detractors once you factored in mistakes and errors and tearing things apart to add in the blocking, for example, for the kitchen cabinets that didn’t get installed because hanging the drywall was sexy for the clients to see. I don’t see a lot of owner-built structures demonstrating this level of methodical patience, and really, how could they? It’s a hard-earned skill to understand that “slow is smooth and smooth is fast”.
Lastly, I have been thinking about the carbon impact of wood pellets after you all read and mulled over my letter about pellet boilers replacing fossil fuel boilers. I looked into it a little and found it instantly overwhelming. The propane advocacy trade group will have you believing propane is not just a great bridge fuel, but the finest fuel ever known. Ditto for pellets. Finding a report that isn’t suspect of bias isn’t easy. In general, it looks like pellets might be about 50-60% less carbon intensive than oil, at least. I don’t know how this stacks up against propane. I also don’t know at what point in the process it’s reasonable to start factoring things in. All this being said, pontificating one way or the other is not just a fun time, it’s also clearly out of my depth. I guess I land on the feeling that trees represent a faster carbon cycle compared to any fossil fuel. I don’t think we can argue the point that a gallon of fossil fuel burned is gone effectively forever from a carbon perspective. But I wouldn’t have thought we could argue that the Earth is round, either, sooo… A tree burned is gone for 20-50+ years. Still a long time, but not millions of years long. I think about this a lot. I have landed on thinking that there isn’t such a thing as a pretty energy source. A tree looks way better as a tree than as pellets, pallets, houses, or even cabinetry (although some of Mike Pekovich’s boxes do trees some measure of justice). Oil and gas looks better under the ground as permanently stored carbon than it does as a hot world our kids have to adapt to. What’s the solution!?! Please don’t ask me – I do not know! That everyone and every company needs to turn a profit makes it hard to tease out what’s true and what’s corporate spin.
And if you actually read this on air, first round is on me!
Related Links:
Listener Feedback 3:
Greg writes: Patrick and crew, In regards to the pre-filter on the mini-split increasing the “load” on the fan motor; the suggestion that it does is incorrect: The motor load is less if you constrict the incoming airflow. Reducing the amount fluid that the impeller has to move decreases the resistive load. Maybe they are thinking of sucking on a straw. Different principles at work.
Question 1: How do you decide between demolition and remodeling?
Alex writes: Hello FHB gang, In my neighborhood it’s not uncommon for an older home to be torn down or almost completely torn down. I know there are cases where an existing home is encroaching upon an existing setback so a portion of the house is left, grandfathering in the building. But more often than not, I can’t figure out why builders in my area, Silver Spring, MD, tear down 80%-90% of a house just to leave a fraction of the foundation and walls.
Why would builders do this? What benefit is there leaving just a small portion of a home? It seems like it would make design and demolition costs more expensive. You also couldn’t get a vapor barrier under the older portion of the basement slab along with a host of other things. Attached are some photographs of a house across the street from me with the front and a side wall left standing.
![]() |
![]() |
![]() |
Related Links:
- A Better Way to Demo
- A New Floor Plan Saves an Old House
- Passive House Remodel in a Historic Neighborhood
Question 2: Should I re-sheathe with Zip System or apply a liquid WRB?
Marc writes: Hey guys, thanks for answering my questions! I like the solution to use beefy joist hangars and a jack post to bring each floor joist up, I have a few in the basement that aren’t being used. I’d love to provide more information on the soffit issue. The roof sections where my soffits are letting air in do not have attic space over them and channels were never installed to connect those cavities to the main attic space so any air coming in is not working it’s way to the attic. In my bedroom I actually replaced the insulation in the ceiling, filled the cavity between the rafters over the top plates with R13 foam board and sealed it up. The rest of that side of the house is still subject to the leakage though. I will be doing new siding outside and I want to start on that back wall. My plan was to either re-sheathe with zip system (costly and labor intensive) or apply a liquid ARB/WRB. A recent Matt Risinger video shows a builder closing off the entire soffit area with zip system. I thought about doing something like this. I’ve been renovating the entire house and doing my best to re-insulate and air-seal but I think the most effective efforts will occur when I pull the siding off and apply some kind of ARB/WRB from the outside. My goal is to eventually have a conditioned attic as that is where my ductwork and HVAC equipment is installed.
Unfortunately, when I went to take more thermal images the temperature here in NJ dropped significantly, but I still managed to get something. Earlier in the summer the pictures were more dramatic. I am able to see that my efforts made somewhat of an impact in the bedroom though, now I just need to move on to the rest of the house.
![]() |
![]() |
![]() |
![]() |
![]() |
![]() |
![]() |
I attached photos so you can see the situation better. The whole side of the house is all addition. I’ve been recently working in the one bedroom where the pictures are from. The part that has the silver roll roofing over it was a screened in porch. All of it has a low pitch roof that meets up with the main attic. I hope this helps add some context. Love the show and I value the time and advice you’re willing to share. Building science is awesome ?
Respectfully,
Marc
Related Links:
- Air-Seal an Attic Series: Sealing Soffits and Chases
- How to Use a Spray-Applied Water-Resistive Barrier
Question 3: What’s going on with the felt on this roof?
Jim writes: Spotted this in my neighborhood. This felt has been up there all spring and summer. Is this a good plan? In the photo it looks brown but it’s actually black felt. That housewrap isn’t getting taped either. “a house gotta breath”
Related Links:
END NOTES:
Members-only Aftershow Podcast 503: In our members-only podcast aftershow, Patrick and Mike drill Ian on how he and his company benefit from their involvement in Remodelers Advantage. Then they discuss the barriers to building more affordable housing, including permitting, zoning, and the slim profits inherent to building small new homes with basic finishes..
Check out one of our Project Guides: Siding & Exterior Trim!
Check out our FHB Houses:
Visit the Taunton Store • Magazine Index • Online Archive • Our First Issues • All Access
Help us make better episodes and enter for a chance to win an FHB Podcast T-shirt: www.finehomebuilding.com/podcastsurvey
If you have any questions you would like us to dig into for a future show, shoot an email our way: fhbpodcast@taunton.com.
If we use your question we’ll send you a FHB Podcast sticker!
FHB Podcast T-shirts!
Represent your favorite podcast! Available in several styles and colors. Made from 100% cotton. Find the Podcast t-shirt and more cool products in the Fine Homebuilding Store.
This episode of the Fine Homebuilding podcast is brought to you by Loctite’s TITE FOAM.
The best builders take weatherization seriously. When they need to seal a gap that’s too small for insulation but big enough to create a draft, they reach for Loctite’s TITE FOAM. With three formulations for everything from small cracks to the biggest gaps, there’s a TITE FOAM product for every job, including a low-expanding product designed to seal the rough opening around windows and doors. The high-density foam forms a tenacious bond to most common building materials, stays flexible to prevent cracking when materials move, and keeps air, moisture, and pests out of the house. Builders who care about energy efficiency, comfort, and durability choose TITE FOAM. Visit Loctiteproducts.com for more information.
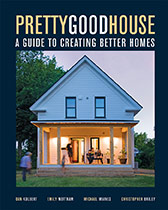
Fine Homebuilding podcast listeners can now get 20% off anything in the Taunton store, including Pretty Good House.
Use the discount code FHBPODCAST to take advantage of this special offer.
We hope you will take advantage of a great offer for our podcast listeners: A special 20% off the discounted rate to subscribe to the Fine Homebuilding print magazine. That link goes to finehomebuilding.com/podoffer.
The show is driven by our listeners, so please subscribe and rate us on iTunes or Google Play, and if you have any questions you would like us to dig into for a future show, shoot an email our way: fhbpodcast@taunton.com. Also, be sure to follow Fine Homebuilding on Instagram, and “like” us on Facebook. Note that you can watch the show above, or on YouTube at the Fine Homebuilding YouTube Channel.
The Fine Homebuilding Podcast embodies Fine Homebuilding magazine’s commitment to the preservation of craftsmanship and the advancement of home performance in residential construction. The show is an informal but vigorous conversation about the techniques and principles that allow listeners to master their design and building challenges.
Other related links
-
- All FHB podcast show notes: FineHomebuilding.com/podcast.
- #KeepCraftAlive T-shirts and hats support scholarships for building trades students. So order some gear at KeepCraftAlive.org.
- The direct link to the online store is here.