Behind the Scenes at a Concrete Batch Plant
The batch plant is your partner in getting high-quality concrete delivered to your job site.
Synopsis: Senior editor Patrick McCombe discusses what he learned on a visit to a concrete batch plant, from the things to know when ordering concrete to the support a ready-mix plant and concrete truck operator can provide.
My friend Andy Grace and I share a nerdy interest in just about anything mechanical or building related, so when I was planning a visit to his new post-frame building to document placing and finishing 38 cu. yd. of concrete for its floor, he suggested visiting his concrete supplier’s batch plant for a tour.
As anyone who knows me would guess, I was extremely excited to see what’s behind the batch plant curtain, but what surprised me was how many other people were also interested when I told them about our field trip, even folks with no connection to the construction world. Andy and I came away with a new appreciation for concrete and the people who bring it our job sites, often in challenging conditions. Our field trip also demonstrated how a concrete ready-mix plant can be a huge help in ensuring your success with concrete. A good supplier will go to great lengths to create the ideal concrete batch for your project and get it there on time.
As anyone who has ever mixed any volume of concrete in a wheelbarrow or even a portable mixer will tell you, mixing concrete by hand is slow, back-breaking work. Instead of mixing raw ingredients or bagged concrete on-site, concrete batch plants combine the concrete ingredients with precision dispensing equipment and place them in the concrete mixing truck that brings the concrete to your job site ready to use. And they have far more offerings than you could ever get from bagged concrete at the home center. Their equipment and expertise helps ensure the concrete has the correct and proper amounts of ingredients, so it performs as intended both during the placing and finishing process and through its service life.
A concrete recipe
Modern concrete is made from four basic ingredients: large aggregate (stone), small aggregate (sand), cement (often a mix of Portland cement and either slag from steel-making or fly ash from coal-fired power plants), and water. Portland cement, fly ash, and slag are examples of pozzolans, minerals that, when in a powdered state and combined with water, create a slurry that turns into a hard stonelike material. Calcium and silicate minerals in Portland cement combine with water to create hardened concrete in a chemical reaction called hydration. Once the ingredients are combined in a concrete mixer, the reaction (curing) starts and continues for weeks, months, and even decades in the case of dams and other large infrastructure projects. The use of pozzolan hydration reactions to make concrete-like materials dates to the ancient Greeks in 400 BC, who used pozzolans from volcanic ash and accumulations of micro skeletons called diatoms (also known as diatomaceous earth).
Additives, also called “admixtures,” can be added to the concrete to increase slump, speed or slow set times, and protect from freezing temperatures. There are admixtures that can make concrete waterproof. You can also add glass-, steel, and synthetic-fiber reinforcing to the concrete mix for additional strength and crack resistance.
Those who do concrete work want predictable concrete, which depends on a consistent moisture content of the basic ingredients. A good concrete supplier will keep aggregates out of the weather and weigh them regularly so the amount of water added to the mix can be adjusted to compensate for wet aggregate. This is especially important for multiday and multiphase projects, so a slab poured one day will have the same color and general appearance as one placed and finished later.
Getting the right mix
AGGREGATE, 60% to 75%: Good batch plants get their aggregates and admixtures from the same quarries and suppliers so the concrete has consistent color and working properties. Decorative and high-strength aggregates for highway work should also come from consistent supplies. The aggregate hoppers on the batch plant are filled by a front end loader. Concrete deliveries are scheduled the previous day and the hopper is only loaded for what’s needed for a series of deliveries using a similar concrete mix.
WATER, 14% to 21%: Municipal water is considered the best source because it doesn’t have seasonal variability like onsite wells, which can be affected by rainfall amounts. Water with high mineral content can give concrete a blotchy or inconsistent color.
CEMENT, 7% to 15%: Stored in silos so it can be kept dry and easily dispensed, cement is literally the paste that holds concrete together. Generally concrete is a mix of Portland cement and slag, in a ratio of four to one. Slag makes the concrete slower to set and most finishers say it makes it easier to get a smooth finish. Both attributes make the addition of slag useful for big projects and hot conditions. The batch plant that I visited has one silo of Portland cement and one of slag. The raw materials are delivered by truck and moved to the top of the silos by auger.
Four things to know when ordering concrete
How much do you need?
Concrete is measured by the cubic yard; when the batch plant asks how much you need, that’s the measurement they use. One cubic yard is equal to 27 cubic feet. When figuring out amounts for your project, order 10% more concrete than the calculations would suggest. Not every project will use the surplus, but you may need extra to fill low spots or make up for spreading or leaking forms, or even the occasional spilled wheelbarrow. Have formwork for sidewalk-sized pavers or pads for trash cans, entry doors, or HVAC equipment ready to receive any excess. Ordering the exact amount you think you need is a mistake. I once had to order a second delivery of just 1⁄2 cu. yd. at great expense for cutting it too close.
If your job requires more than 10 cu. yd., you’ll need more than one delivery. You may want to schedule a second delivery 30 minutes to an hour after the first one so you have time to place the first load and take a breather before you’re frantically moving concrete again.
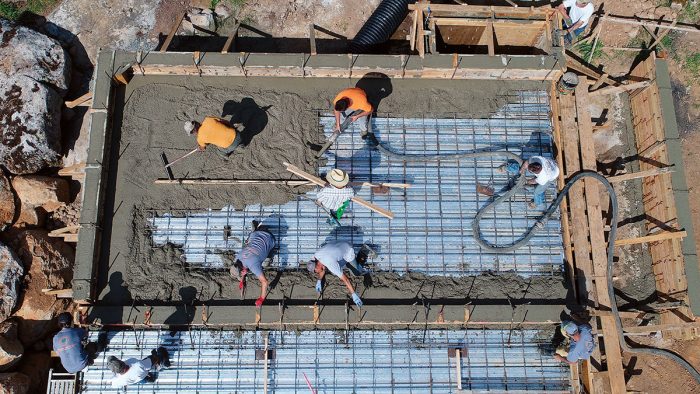
What is the strength?
Compressive forces push down on concrete—such as a house on its foundation or a car parked in the driveway—and are how we most commonly think of the forces acting on concrete. Residential concrete generally has a compressive strength between 2500 and 4000 psi (pounds per sq. in.). The amount of strength in a given batch is determined by a number of factors. The primary factor is the amount of Portland cement in the mix—the more Portland cement, the greater the concrete’s compressive strength.
Project engineering and prescriptive building codes specify the strength of concrete needed for concrete footings, foundation walls, and flatwork. Architects and municipalities can also specify the strength of concrete needed for a project. You’ll need to know the psi requirement for your project so you can tell the batch plant when you order—it will be one of the first questions asked. Many builders order concrete with a higher psi than required, which gives a safety margin and allows them to add some water to the mix for workability. Batch plants can also supply low-compressive-strength concrete for site stabilization and backfilling utility trenches, which is useful for trenches in roads or driveways.
Aside from compressive forces, there are other forces at work on concrete too. Concrete must resist forces pulling on the concrete, described as tensile forces—such as how a house pulls at the concrete foundation when it’s hit with strong wind. Concrete must also have shear strength, which prevents the concrete from breaking off when it’s not adequately and uniformly supported underneath. Shear failure in a residential setting, like a concrete footing breaking and sinking, can be caused by ground-water movement, seismic activity, and variations in the strength of bearing soil or soil compaction under the concrete.
Relative to its weight, concrete has low shear and tensile strength on its own, but steel’s high tensile strength makes it an ideal companion to concrete’s great compressive strength. Steel anchor bolts hold a house to its foundation and steel rebar can help a footing stretch across a soft section of soil or add tensile strength to concrete creating a cantilevered balcony or elevated parking deck.
What is the slump?
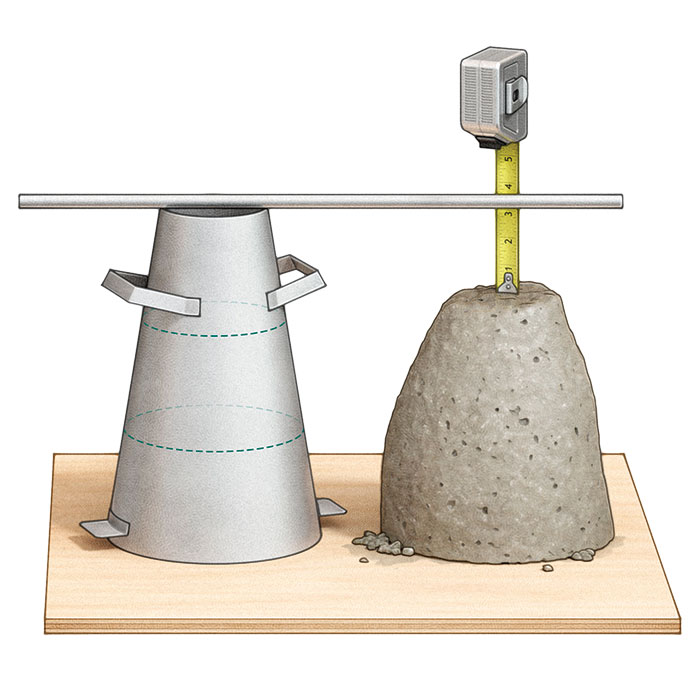
The workability of concrete is largely determined by how much water is in the mix and is measured as slump, on a scale of 1 to 10. The numbers refer to how many inches a sample of mixed, fresh concrete settles after you remove the conical test container. Most residential concrete leaves the plant with a slump between 4 and 6. Concrete with a low water-to-cement ratio can be difficult to work with. In footings or walls with rebar, concrete that doesn’t flow easily is difficult to get into the forms and fully around the rebar, resulting in a weakened or defective concrete assembly. Concrete with a high water-to-cement ratio is also difficult to work with, taking longer to set for finishing. More seriously, too much water weakens the concrete. Follow your engineer’s concrete specifications (or the guidance of an experienced concrete contractor).
On-site slump test
To assess the consistency of a concrete mix, a slump cone is filled with three equal layers and rodded between each layer to remove voids. Once filled, the cone is removed and used as a reference to measure how much the unrestrained concrete settles, or “slumps.” If it settles 3 in., for instance, the mix has a slump of 3.
Where is it going?
This might seem like the easiest question from your batch plant quiz, but my friend once had a concrete mixer show up at the wrong location because the town where his construction site was located and a neighboring town had a road with the same name. Confusing directions is not the only possible snafu. I once scheduled a delivery for a footing pour when I was a Habitat for Humanity construction supervisor, and then ended up rescheduling the pour for another day. I was reminded that I hadn’t alerted the batch plant when I got a call from the truck operator waiting at an empty job site. Fortunately and luckily for me, the kindly dispatcher sent the truck to another job and we didn’t have to eat the cost of a truck’s worth of concrete.
Given the potential for miscommunication, it is common for a batch plant to require a confirmation call or text before they’ll send a load of concrete to a site. All this to say, double-check that you and the batch plant are on the same page for delivery time and location. If you know that GPS navigation to the job site is problematic, give the batch plant more reliable directions.
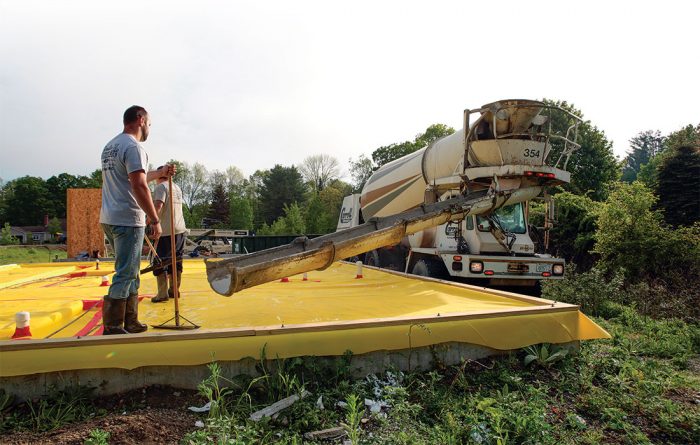
Successfully getting concrete from a ready-mix supplier also assumes the concrete truck can get to the construction site. If the roads or driveway to the job are too slippery from snow, ice, or mud, the driver may refuse to deliver with the reasonable assumption that his truck may become stuck or wrecked. Concrete mixers are top heavy, making them hard to control in slippery conditions, and the concrete sloshing around can make their handling even more unpredictable.
Consider delivery for small projects
Because mixing concrete by hand is so labor-intensive, I think it makes sense to order from a batch plant for any project that requires more than 1 cu. yd. of concrete. Concrete batch plants make more money when their trucks go out full with 8 cu. yd. to 10 cu. yd. of concrete, so it costs more per yard to buy smaller amounts. Extra charges for “short loads” vary by supplier, but generally apply when you’re buying less than 4 cu. yd. of concrete. For most projects, I think the convenience and time savings make it worth the extra cost.
Once the ingredients are in the truck’s mixing drum, the concrete needs to be placed within an hour, including the time it takes to clean off the truck before leaving the plant. If your project is more than an hour away, you’ll need an admixture to extend the working time. Operators continuously mix the concrete as they drive to prevent heat from the concrete’s curing process from hastening the cure. If the mixer is held up in traffic or if the truck breaks down, the concrete will be unusable and returned to the yard for recycling.
If the concrete is being placed where the truck can’t reach, it can sometimes be pumped or moved in wheelbarrows, or in motorized wheelbarrows called “mud buggies.” If your site is too far from the concrete supplier, you’ll need to mix by hand or bring in a volumetric concrete mixing truck, which most people call a “mobile batch plant.” These trucks haul all the concrete ingredients and mix them together on-site. Depending on the size of the truck they can haul enough material to make from 4 cu. yd. to 14 cu. yd. of concrete.
Four things a batch plant can provide
Help during hot or cold weather
The hydration reaction is exothermic, which means ambient temperature and temperature of the materials play a big role in how long it takes for the concrete to set firm. Extreme temperatures complicate batch plant operations and concrete delivery. Batch plants can provide hot water instead of cold so the concrete sets up faster in cold weather. In hot weather, bagged ice can be added to the truck at the plant to provide more placing and finishing time.
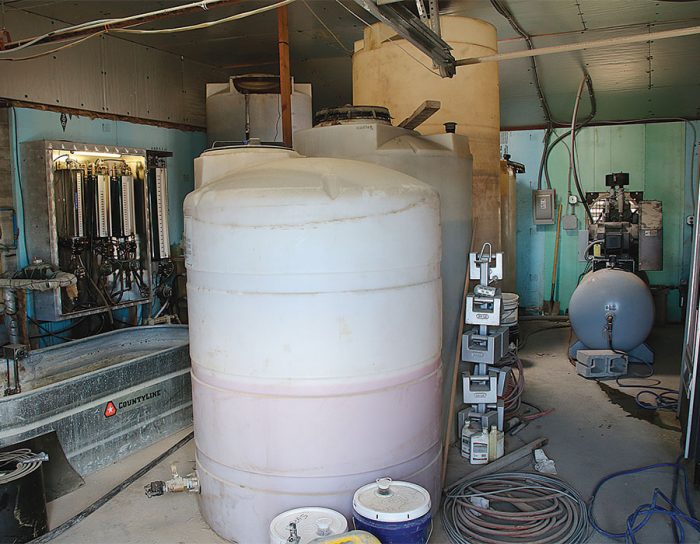
As you might imagine, the concrete mixer’s steel mixing drum is a poor insulator, so the effect of hot water or ice should only be expected to last about 30 minutes. Calcium chloride, a common admixture, makes the concrete gain strength faster, which is helpful in cold conditions and on large projects. Talk to your batch plant operator about unusual weather and site conditions that may require admixtures, ice, or hot water.
On-time delivery
Concrete batch plant dispatchers are experts at managing the available trucks and operators; once you have a delivery scheduled, you can expect it to arrive on time. Drivers and dispatchers are mindful of traffic and other slowdowns because once the ingredients are in the mixer’s drum, the clock starts ticking and a timely delivery and placement are key to successful concrete work. When a mixer is delayed and the concrete is at risk of curing in the drum, the operator floods the concrete with on-board water and keeps mixing to prevent the concrete from hardening inside the mixing drum. The concrete is lost, but cured concrete in the drum has to be broken out with a jackhammer—and in extreme cases can ruin the mixer.
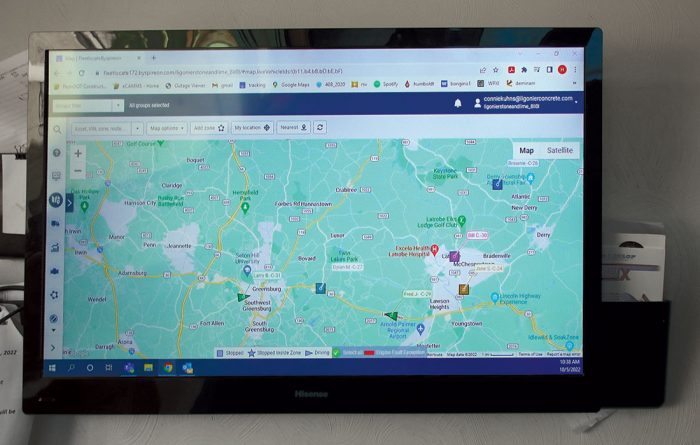
Batch-plant workers and drivers plan on one hour from the time the mix is put into the truck until placement is finished. But before the truck can even hit the road, the driver has to wash off any spilled or splashed concrete from the truck, which could take between 10 and 20 minutes. So in reality, you and your mixer operator have about 45 minutes to deliver and place the concrete for the greatest chance of success. Batch plants try to limit the amount of time the mixer is on the job by providing a reasonable time to unload— 6 to 8 minutes per cu. yd. is typical—and charge extra beyond that.
A place for leftover concrete
Disposing of leftover concrete on a job site is often controlled by local laws, but much of what’s not used is still good for other purposes. At the batch plant I visited, much of the concrete that comes back on the truck is placed in molds to cast as stackable retaining-wall blocks. You’ve probably seen similar blocks roadside as permanent or temporary retaining walls. They’re also used to create bins for storing sand, gravel, mulch, and road salt.

Concrete that’s too old to salvage is put into a recycler that separates the sand, gravel, and Portland cement. Settlement ponds with a slight pitch further separate the particle sizes. The sand and stone are sold as fill and the Portland cement is treated to reduce its alkalinity before it’s disposed of.
Another well-trained crew member
Mixer drivers must position the truck and discharge chute without hurting anyone or damaging the site. Then they have to manage the flow of concrete to the crew or the concrete pump. They also have to climb all over the truck in all weather to wash it and have knowledge of concrete and the various admixtures and their proper use. In recent years, it’s been difficult to find operators in many areas. Successful mixer operators must have a can-do attitude given the challenges of navigating a big truck while hauling expensive cargo with a very short shelf life.
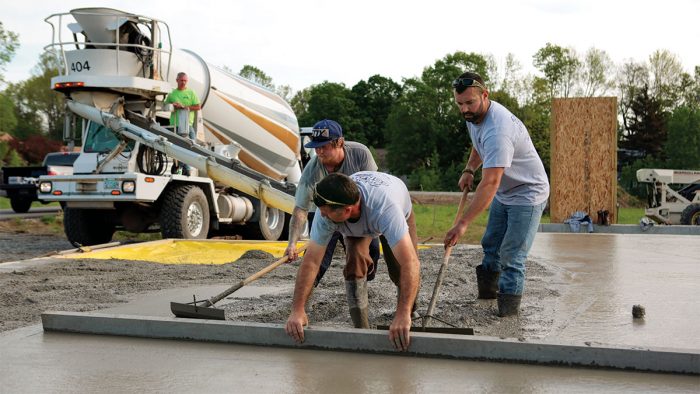
Be ready for a few questions
The bulk dispensing they do at the plant and the mixing of the ingredients during the drive to the site can save hours or days of labor on the construction site. But for the batch plant to be able to help you, you’ll need answers to a few fundamental questions when you place your order: When and where do you need the concrete? How much do you need? What strength do you need, and what slump? You will also need to discuss if you want fiberglass reinforcement, or any admixtures. By the end of this article you should be knowledgeable enough for an informed conversation with the ready-mix supplier.
I’d like to thank Connie Kuhns from Ligonier Stone and Lime Concrete in Ligonier, Pa., for answering our many questions and spending more than an hour showing us around. In recent years shortages of mixer operators and the building boom has led to longer wait times for deliveries. Be sure to contact your supplier days ahead of time to ensure you can get concrete when you need it. I’d also like to remind you to be courteous to concrete-mixer drivers you encounter on your job sites and on the road. They’re doing important work and delivering an expensive product with a short shelf life. How about giving them a little extra room?
—Patrick McCombe is a senior editor.
Photos by the author, except where noted.
From Fine Homebuilding #314
RELATED STORIES
View Comments
Yikes there are a lot of errors in this information. Contact me if you would like to clear some of this up. 541-621-5408.