Podcast 569: Bath Fan Installs, Sunroom Trim, and Basement Control Layers
Induction cooking, battery pack adapters, HVAC in the attic, bath fans, exterior trim, health benefits of fireplaces, and basement air- and water-management.
Follow the Fine Homebuilding Podcast on your favorite app. Subscribe now and don’t miss an episode:
![]() |
![]() |
![]() |
Help us make better episodes and enter for a chance to win an FHB Podcast T-shirt:
www.finehomebuilding.com/podcastsurvey
Eric weighs in on induction cooking. Jerry shares resources on carbon and then asks about exterior trim. Richard says we need a southern phone-a-friend. Ethan wants to know who installs the bath fan. A podcast listener inquires about fireplaces. Patrick shows us his deepened basement.
Editor Updates:
- Rob’s addition
- Jeff’s spring cleaning
- Patrick’s PT, tree work, woodstove
- Mike’s tool repairs
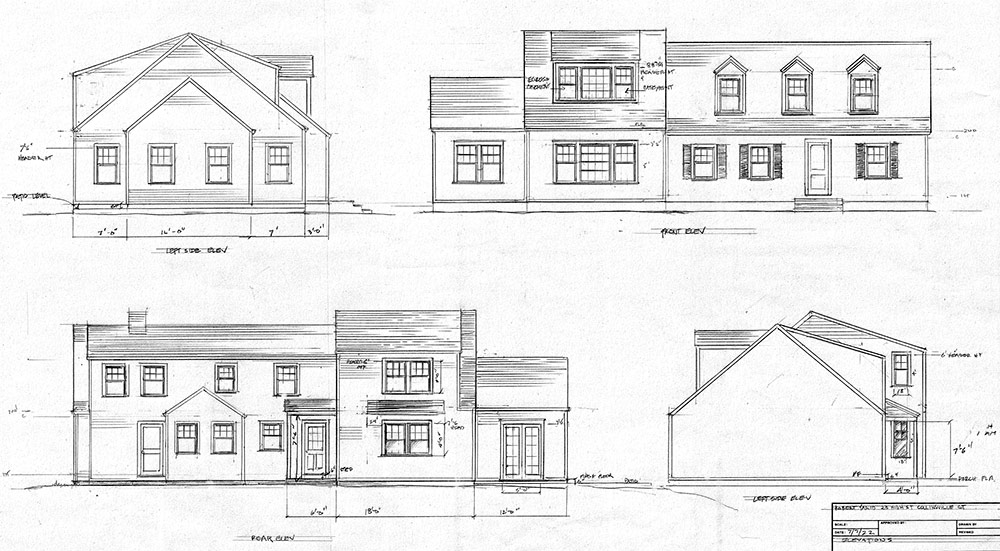
Listener Feedback 1:
Eric writes: Thanks for your recent podcasts that finally talk about some of the possibilities and complications of induction cooking. Based on a number of YouTube videos (and some searching online for other independent reviewers such as Consumer Reports), I bought a portable induction cooktop. It was only $116, but similar models can be found for less than $100.
I was surprised that the whole “cooking with gas” bit was 1930s propaganda. The environmental/climate change channel Climate Town did a great job of talking about the history of gas advertising: YouTube: It’s Time To Break Up With Our Gas Stoves
The video that finally made me switch was a comparison by the excellent YouTube channel Technology Connections (and second channel Connextras): YouTube: Gas stoves aren’t really that fast – even standard electric is faster! This video is over an hour long! But it has some excellent demonstrations with actual measurements of air quality and speed.
America’s Test Kitchen recommended Duxtop (not the super-expensive, the other one).
I was very surprised when I first used it how cool it was to cook with it. Now I realize that was because the previous gas and electric resistive stoves I’ve used heat up much of the air around the pan as much as the pan itself. The induction heats the pan . . . only the pan.
Related Links:
Listener Feedback 2:
Jerry writes: Hi Podcasters,
I love the podcast, look forward to it every week, and love that the midweek Pro Talk podcasts are coming out regularly too! I have a few thoughts to share on some topics you’ve covered recently.
First, I have a book recommendation for people interested in carbon accounting. How Bad Are Bananas by Mike Berners-Lee talks about the carbon cost of different things like a text message, pouring a glass of water, or writing an email (all less than 10g as of 2011).
Some home-building-related things are 1 kg of concrete, which registers somewhere around 100g of carbon; 1 kg of steel is much higher. There are definitely principles we can apply to reduce carbon in our buildings like buy local, don’t waste, use wood not concrete, and avoid plastic and glue—all easier said than done. I would bet that the Simpson Strong-Ties, nails, and glue in any given project outweigh the lumber in terms of carbon.
I liked hearing Preston’s comments about batteries. At the company I work for we employ 8-10 carpenters fully kitted out with Dewalt tools. Over the past three years or so we’ve switched the bulk of their tools from corded to cordless. One snag was for 23-gauge pin nailers. For a while the only one on the market was made by Ryobi. We had a couple floating around the company, but it meant carrying a charger and battery for one tool, which can be a pain. Ryobi also makes a battery-powered hot glue gun that one carpenter liked. We used the adapter that Preston mentioned to run that one with a Dewalt battery converter. Dewalt now has a pinner, so we’ve adopted that one. There are some off-brand Amazon sellers that have hot glue guns made for each battery platform, so we’ve gotten Dewalt versions for some of our carpenters. The rechargeable AA and AAA battery packs are perfect for lasers, probably also for moisture meters and other small tools.
Related Links:
- GBA.com: A Cobalt Supply Chain to a Hell on Earth
- GBA.com: BEAM Estimator for Measuring Embodied Carbon
- Reduce Embodied Carbon With Simple Forms
Listener Feedback 3:
Richard writes: Almost all these houses are in the South and West: YouTube: CRAPPY ATTICS are Standard in America! Here’s how to BUILD – DECENT or AWESOME
You guys could use a phone a friend like Matt during the podcast, especially around southern issues like these and HVAC (the only reason the South is as populated as it is).
Related Links:
- Building in the Southwest
- Smart Design Advice for Hot & Humid Climates
- 4 Tips to Building an Efficient House in a Hot Climate
Question 1: Who installs the bathroom fan?
Ethan writes: Hello Fine Homebuilding Podcast!
I can’t tell you how many jobs I’ve been on where it comes down to this question: Who installs the bath-fan tubing and exterior vent?
It’s not the electrician, it’s beneath the HVAC guy, it’s not the plumber, it’s not the carpenter. Should it be general conditions for the GC? If you’re lucky!
I’d like to get this sorted out before my next job gets underway.
Thanks,
Ethan
Related Links:
Question 2: Will cedar posts for my sunroom work with my exterior trim and siding?
Jerry writes: I have a design question for you all! We’re starting on a sunroom, and I would love to hear your take on finish material choices. The deck will be a PT frame with Azek decking. There will be kneewalls with Hardie siding on the exterior with Azek trim (to match the house). It will have screens above the half wall and cedar-wrapped posts and beams. I’m worried that the cedar posts and beams will look funny paired with Hardie siding and white Azek trim on the exterior. I’m attaching a pic of the rendering our architect did.
Thanks for everything you do!
-Jerry
Related Links:
Question 3: What are the health benefits of fireplaces?
A listener writes: Hi Patrick –
I wanted to call your attention to some new research that found that adding a fireplace in the home can not only help promote relaxation, but it also can actually promote healthy aging as well. This news is especially exciting for builders, remodelers, architects, and designers who are on the front lines of consumer requests for wellness in the home. Now, simply adding a fireplace will transform any space in the home into a sanctuary and can also encourage healthy aging.
Napoleon—maker of gas, electric, and wood fireplaces—partnered with the University of Illinois and University of Alabama to study the health impacts of fire on our lives. Everyone knows that firelight is relaxing and that relaxed people are healthier. But Napoleon was thrilled to learn that the studies uncovered the unexpected positive impacts that exposure to fire can have on our mental well-being as we age.
I’ve attached some additional details about the studies. I’d be happy to put you in touch with someone from Napoleon or the universities involved with the studies who could tell you more about how exposure to firelight can foster wellness and healthy aging.
Related Links:
- The Fireplace Effect: Exposure to Firelight Improves Health and Wellness
- Napoleon: The Power of Fire Study
- Can Burning Wood Be Green?
Question 4: What are the best insulation and water-control details in my newly deepened basement?
Patrick writes: Good morning FHB team!
Patrick here from Dartmouth, Nova Scotia, Canada. I’ve been a long-time magazine reader and podcast listener of Fine Homebuilding (and more recently GBA) while working on a very significant renovation of our 1942 1.5-story classic Dartmouth home that we purchased in 2015. A classic Dartmouth home is one that sits on a hill with no driveway access to the home or yard. A short parking spot is typically below at street level with stairs up to the yard for access. This can make renovation work far more challenging.
I am not a tradesperson by training, but I was extremely fortunate to grow up immersed in construction and renovation work and learn from my father and his best friend of many years along the way. Now, a few decades and several properties later, I am confident enough to go online, do my research, and tackle some very sizeable design and build projects that would likely be very intimidating to the average homeowner. Fine Homebuilding archives have been an incredible resource during many projects, and I am always thankful for the little nuggets I get from the podcast. Since buying our current home I’ve knocked off a few large projects including a large deck teardown and redesign, a complete bathroom renovation, and, during the height of COVID, I took down a structural wall to combine two upstairs rooms together into a larger master bedroom. Although most of these projects tended to drag on due to the realities of life, my wife hasn’t divorced me (yet).
![]() |
![]() |
![]() |
![]() |
All of those projects pale in comparison to what I’ve gotten myself into this time around. As you’ll see from the attached photos, I’ve taken on the ominous project of digging down my basement. The basement stood at just barely 6 ft. previously, and the plan is for a full finished 7 ft. 6 in. by the time I’m done. Interestingly, the idea to dig down and use an interior retrofit footing came from Fine Homebuilding (issue 95 Q&A, Retro footing) and sat in my brain for six years before I decided to take action. Last year while in yet another COVID lockdown, I decided that the pain of the dig would be worth it to capture the 350 sq. ft. of useable space that was only being used for storage and barely workable laundry, so I contacted a structural engineer to have a look at my plan. During the site visit it was determined that a version of that same L-shaped footing from issue 95 would actually be the best application for my specific case based on depth, age, and other factors. My existing 1942 home had no footings under the concrete walls, nor the center support columns or chimney. The floor was essentially scrap concrete and, in some instances, no more than an inch thick with no reinforcement. There was a great deal of moisture during spring and summer requiring a dehumidifier, but no visible running water intrusion. These issues combined with the height of the space convinced me that I should go for it. So, with stamped drawings in hand, I decided to grab the sledgehammer and get to work.
I’ve been steady at this in my spare time for just over 15 months now, with some fairly significant breaks along the way to enjoy summer, take family vacation, deal with a few sports-related injuries, and handle surges of busy work life. All of the excavation has been done by hand without any heavy equipment using a sledge, hammer drill, shovel, pick, and 5-gallon buckets to remove the soil, carry it up the stairs, across the yard, and down the front stairs to the dumpster below. I’ve been called crazy for doing so, but the challenges of yard access and related destruction of walkways and gardens to get a piece of machinery into the basement made it the only palatable choice.
Excavation has been done using the standard 5-ft. dig and 4-ft. form and pour approach. Because such little concrete is used at a time, bags of premixed concrete that are mixed and poured by hand also made the most financial sense. As you can see from the photos, I’ve very nearly finished all of the footings and excavation of the entire center area is complete. By the numbers, I have moved 55 cubic yards of soil and rock out and carried 386 bags of concrete in. With only about 2 cubic yards left to go, the end is near!
![]() |
![]() |
As I wrap up this stage of the job, I’m now turning my attention to the inevitable infill of gravel, floor pouring, and insulation. To prep for this, I’m extremely interested in your opinions on my planned insulation and water-control details. I’ve attached two sketches with some explanations and was wondering if you might be able to comment on what you see, best practices, and any considerations I may have missed, as well as some of these questions:
- I’m planning to run interior drainage board as a curtain down all of the exterior walls and under the floor to preemptively control any water penetration. Given the number of cold joints in the concrete, I think this might be a more reliable solution than a painted-on membrane. What are your thoughts?
- I’m planning to use XPS foam on the walls, including down between the walls and floor and under the floor. First, is XPS the right solution, or should I use EPS? Under the floor, if I use XPS (or EPS), do I also need a vapor barrier? I see a lot of conflicting information on this front, but my current understanding is that it would not be required.
- When it comes to finishing the insulation and sealing around the first-floor connection, I have the added challenge of embedded joists (full on one side of the house, partial on the other). How can I ensure I give my joists the best chance at longevity while still providing the best insulation and humidity control?
Bonus question: Before I pour the floor should I rough in for future radon control?
I know this is a long one. Even if you don’t get to it on the pod, thanks for reading and for continuing to supply your expertise and inspiration. Because of Fine Homebuilding, I still have at least one reason to look forward to checking the mailbox.
Related Links:
- Waterproofing a Basement From the Inside Can Be a Challenge
- Three Ways to Insulate Basement Walls
- Insulate Your Basement
END NOTE:
Podcast 569: Members-only Aftershow — Rob Yagid’s Addition
Jeff, Mike, and Patrick ask Rob about material choices, construction methods, and planned spaces in Rob’s new addition.
Check out one of our latest Project Guides: Energy Retrofit!
Check out our FHB Houses:
Visit the Taunton Store • Magazine Index • Online Archive • Our First Issues • All Access
Help us make better episodes and enter for a chance to win an FHB Podcast T-shirt: www.finehomebuilding.com/podcastsurvey
If you have any questions you would like us to dig into for a future show, shoot an email our way: [email protected].
If we use your question we’ll send you a FHB Podcast sticker!
FHB Podcast T-shirts!
Represent your favorite podcast! Available in several styles and colors. Made from 100% cotton. Find the Podcast t-shirt and more cool products in the Fine Homebuilding Store.
Fine Homebuilding podcast listeners can now get 20% off anything in the Taunton store, including Pretty Good House.
Use the discount code FHBPODCAST to take advantage of this special offer. |
![]() |
“Finally, knowledgeable people talking about building reasonably-sized, high-performance houses for normal people with real budgets!” — DanD, VA, 8/19/22, Amazon.com review |
We hope you will take advantage of a great offer for our podcast listeners: A special 20% off the discounted rate to subscribe to the Fine Homebuilding print magazine. That link goes to finehomebuilding.com/podoffer.
The show is driven by our listeners, so please subscribe and rate us on iTunes or Google Play, and if you have any questions you would like us to dig into for a future show, shoot an email our way: [email protected]. Also, be sure to follow Fine Homebuilding on Instagram, and “like” us on Facebook. Note that you can watch the show above, or on YouTube at the Fine Homebuilding YouTube Channel.
The Fine Homebuilding Podcast embodies Fine Homebuilding magazine’s commitment to the preservation of craftsmanship and the advancement of home performance in residential construction. The show is an informal but vigorous conversation about the techniques and principles that allow listeners to master their design and building challenges.
Other related links
-
- All FHB podcast show notes: FineHomebuilding.com/podcast.
- #KeepCraftAlive T-shirts and hats support scholarships for building trades students. So order some gear at KeepCraftAlive.org.
- The direct link to the online store is here.