Podcast 598: Stone Foundations, Failing Stucco, and Comfortable Garages
The crew hears from listeners about WRBs, Brian’s porch piers, and hidden costs of construction. Discussion questions include tightening a stone foundation, stucco on straw bales, and low-buck energy upgrades.
Follow the Fine Homebuilding Podcast on your favorite app. Subscribe now and don’t miss an episode:
![]() |
![]() |
![]() |
Mike Guertin explains western-style window installation. James suggests a cap for Brian’s sunken piers. Doug had some surprises on his new home build. Jameson thinks home inspectors help home buyers. Karl asks about his stone foundation. Seth has failing stucco on his straw-bale house. 74 Impala wants to make his garage suitable for occasional heating.
We’ve created a custom eLearning coupon for podcast listeners – code: PODCAST20
The Sustainable Home Building Accelerator
This intensive, interactive online series of courses is designed to rapidly advance your knowledge of sustainable home design and construction. Whether you’re an architect, builder, or a homeowner, we’ll give you the information and confidence to design and build well-crafted, practical homes that maximize performance and comfort.
Over 11 hours of video. AIA Approved 10 HSW/LU Credits. Resnet 10 PD Credits.
When you purchase all three courses, you’ll receive access to a year of GBA Prime as well as a copy of the Pretty Good House book!
Remember the code PODCAST20 for any Fine Homebuilding courses.
Editor Updates:
- Mike’s Quahog collecting
- Mark’s Exterior painting
- Jeff’s Fall cleanup
- Patrick’s Clear exterior finish photo shoot
Listener Feedback 1:
Mike Guertin:
One part of Steve’s question described the housewrap being installed after the windows were installed. You, Brian, and Ian discussed why it may have been done it that way—drying in the building and the possibility that the framers were charged with installing the windows and there was another sub who installs the housewrap. All plausible reasons.
Steve doesn’t mention where he’s located, but the housewrap practices may be due to location. Often in seismic areas and some high-wind zones the inspectors conduct a sheathing-nailing inspection as part of the framing inspection. Framing inspections are usually done after MEP rough-in trades have completed their inspections. In these areas the roofing is usually done and the walls are dried-in (as Ian noted) by installing the windows. If Steve had photos of the installed windows, they could be telling whether this was the case or not. Commonly called the “western” window flashing and WRB installation method, it is an approved method by all the major housewrap manufacturers. Though many wrap manufacturers will showcase the “eastern” install method (housewrap first/windows second), they will have a less prominent install detail on their websites or a technical bulletin that outlines the “western” method. And if they don’t have such instructions, they probably don’t sell to these markets where the “western” method is commonly used.
I’ve done dozens and dozens of trainings showing the “western” method, usually at JLC Live or IBS shows in CA, OR, WA, and Las Vegas. And I occasionally use the “western” method on my projects, depending on sequencing of the build.
Related Links:
- Save Energy with Storm Windows
- Installing and Flashing Windows Correctly
- Installing a Nail-Fin Window Over Housewrap
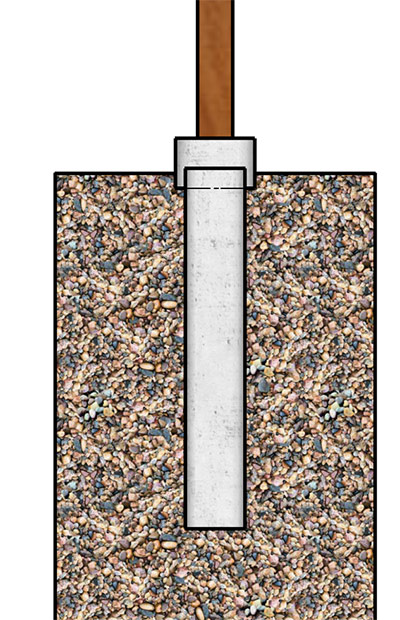
Listener Feedback 2:
James writes:
Hey podcast crew,
I have two major thoughts about Brian’s porch pier situation:
1. Don’t do anything permanent until you’ve had one full winter without any additional settlement. Since it’s only been through one winter, it might settle again this coming winter.
2. You could try pouring an extension on top of the pier with a larger diameter so that it stays seated despite the cold.
Related Links:
- 2 Ways to Detail Durable Porch Piers
- How to Form a Custom Concrete Pier for a Porch
- The Rotproof Porch
Listener Feedback 3:
Doug writes:
Hi Patrick and team,
On the after-show discussion of hidden building costs I’m glad you brought up site work. We had a completed plan for a house with a walkout basement we were going to build on a hill on our property. Before committing, I paid our excavator to do an hour of exploratory digging. Everywhere he tried on the hill he hit rock at about 2 ft. It would have required $25,000 in blasting. We decided to move down to the flattest area on our land and had our designer modify the plans to eliminate the basement and go slab on grade. Even with the change we had to blast for the footer and the septic line. That’s life in the mountains.
Well and septic can also have surprises. We do not have a water table as such. You have to hope to hit a pocket of water in the rock. We had a woman “witch” our well and drilled where she said. Even though every logical bone in my body says this is bunk, at 300 ft. we got 60 gal. a minute. But 1/4 of a mile from us a neighbor went down 575 ft. and got water that is undrinkable.
Landscaping was not really a cost because of Colorado water laws. With only 2 acres, our well permit does not allow any outside water use. Gravel is the primary landscape feature.
It was good the hear the experience of other owner-builders.
Related Links:
Listener Feedback 4:
Jameson writes:
Hello FHB,
I have suggested having a home inspector on your show in the past. The industry has changed a lot in the recent past, and it is a very interesting time to be a home inspector. In episode 591, you had a long conversation about an energy auditor for a newly purchased home. You were talking about making sure there are no bulk-water intrusion issues, no combustion problems and talking about an energy auditor finding leaks and electrical issues with his thermal camera. If there was only someone who would look at all these things and also look at the insulation, ventilation, and other building-science considerations….oh, wait there is. A qualified home inspector. It surprises me a bit nobody even considered this an option, and I think it speaks to misconceptions about our industry. We have changed from providing a basic opinion about buy or don’t buy, to now becoming a building consultant who teaches you about all parts of your home. Again, I would suggest you have a home inspector on the show (especially a high-quality inspector) to help people understand the value and importance of a home inspection. In Massachusetts, where I operate, we bring on building experts like your own Mike Guertin to ensure we are highly trained in as many of a home’s systems as possible. We do more inspections after the purchase than ever, with everyone waiving their inspections in the seller’s market. I get hired by builders and homeowners alike to help diagnose and prioritize problems, regardless of how long they have owned the property. Hopefully, knowing where to start for a homeowner will save them far more than the cost of an inspection in the long run.
My two cents!
Related Links:
- PRO TALK With Home Inspector Paul Barraza
- Ten Tips From a Home Inspector
- Tailgate: Carl Simmons, Inspector
Question 1: Should I fill the voids in my old stone foundation?
Karl on GBA Community and Q&A writes:
I have an old house on a fieldstone/rubble foundation. The exposed portions of the foundation are pointed with mortar. The non-exposed portion (i.e., exterior and below grade) of the foundation is a loose jumble of random-shaped fieldstones that flares outwards to a width of several feet as you approach its base. The stones throughout have substantial voids between them. It’s unclear whether this has always been the case, or whether 200 years of water has washed the fines into the cellar.
As I work to improve grading around the perimeter and install underground gutters beneath the eaves, I have easy access to the very top of this void network. Should I do anything to fill the voids?
The voids are substantial enough that either pea-gravel and a watery concrete or mortar would somewhat flow into them. The local vole and chipmunk populations would be very unhappy with me.
Related Links:
Question 2: How do I fix failing stucco on my straw-bale house?
Seth writes:
Hello,
I love the show. Thank you so much for all the knowledge you share. I am a remodeling contractor in northern Wisconsin, and I specialize in addressing building-performance conundrums. Now I have a bit of a puzzle with my own house that I’m hoping for some help with.
I built a straw-bale house about 17 years ago. I put up a post-and-beam frame, infilled with straw bales, and then plastered them with earthen plaster and then lime plaster on both the interior and exterior. The earthen plaster was a mix of clay and sand, both from my yard, with a little straw. I do not have any sort of vapor barrier.
As you might expect, warm moist air migrates into the walls during the winter and freezes on the interior side of the exterior plaster. Come February, as temperatures outside warm a little, the earthen and lime plasters essentially rehydrate, crack, and fail. I see this rehydration on the north wall but much more significantly on the gable walls. I tried putting some round aluminum soffit vents in the wall up high on the gables, but it didn’t help much. I recently put a large addition on the east side, which completely covered the east wall. When I pulled the plaster off to patch it, I found the straw to be completely mold free and intact.
Now, a large section of the plaster on the west side has failed and fallen off, and I need to address the problem. I am considering removing all of the straw down to the top beam, which creates the bottom of the gable triangle. Then I would seal that area off from the rest of the walls with plywood installed horizontally on top of the beam. Then frame it in, insulate it with cellulose, and side it with board-and-batten siding.
My hope is that with the gable area sealed off, the vapor will diffuse more evenly through the rest of the walls. My other thought is to allow significant venting through this area, but my concern is that moisture will still condense inside the walls.
I heat with a woodstove and a wood boiler, which heats my finished slab floor. I have an HRV and bath fans and will plan on a better range hood in conjunction with this solution.
Of course, all of us straw-bale builders laughed at the inspector who said we needed to paint the interior plaster with vapor-barrier paint, because he didn’t understand that straw-bale houses needed to “breathe.” If I knew then what I know now about building science, I never would have built my house this way. I could do that layer of paint now, but it would make any future lime-plaster repair nearly impossible, and I wouldn’t be able to get behind interior walls, etc.
My addition, by the way, is a double-stud wall with dense-pack cellulose and taped plywood sheathing. I have completely encapsulated the east gable wall in the addition, so I’m hoping there is no vapor drive in that direction. Since I have built the addition, that wall looks fine.
Thank you so much for any help you can offer,
Seth
Related Links:
Question 3: What’s a budget-friendly way to insulate my detached garage?
the74impala on GBA Community and Q&A writes:
We are getting ready to move into a new place for a while, and the garage is separate from the house. It is stick built with OSB sheathing and T111 siding. I would like to insulate it and get ready for the zone 7 winters we have in northern Wisconsin. I may need to work on a vehicle project.
![]() |
![]() |
This is a duplex, and we are only planning on living here a couple of years max, so I don’t want to invest too much. Would Tyvek after fiberglass batts cause any problems? I am wanting to have an air barrier more than a vapor barrier since the vapor goes through the Tyvek in and out. I just want to maintain the heat I temporarily need to keep in the enclosure while I am working.
Would poly be a better choice? I have some left over Tyvek, so the cash would be minimal for it. Same thoughts on the ceiling. I would put some baffles in at the eaves and put up the Tyvek. Then strap underneath with 2x before blowing in cellulose. I need to practice cellulose for another project.
Any thought/suggestions would be great. Thanks
Related Links:
- Podcast 147: What’s the Best Way to Build a Detached Garage Workshop?
- Adding a Multipurpose Outbuilding
END NOTE:
Podcast 598: Members-only Aftershow — Long-Lasting Paint Jobs
Discussion about how to get a good exterior paint job or clear finish and how different claddings respond to different coatings.
This episode of The Fine Homebuilding Podcast is brought to you by Loctite’s Pro Foam
The Gaps & Cracks and Window & Door items seal and insulate gaps and fit any standard foam gun applicator. Loctite’s Fire Block Pro Foam fills gaps while resisting the migration of fire and smoke. Perfect for electrical, plumbing, and wherever a fire-resistant foam is needed. Say yes to Loctite’s new Pro Foams. Say yes to Loctite.
Visit Loctiteproducts.com for more information.
Check out one of our latest Project Guides: Energy Retrofit!
Check out our FHB Houses:
Visit the Taunton Store • Magazine Index • Online Archive • Our First Issues • All Access
If you have any questions you would like us to dig into for a future show, shoot an email our way: [email protected].
If we use your question we’ll send you a FHB Podcast sticker!
FHB Podcast T-shirts!
Represent your favorite podcast! Available in several styles and colors. Made from 100% cotton. Find the Podcast t-shirt and more cool products in the Fine Homebuilding Store.
Fine Homebuilding podcast listeners can now get 20% off anything in the Taunton store, including Pretty Good House.
Use the discount code FHBPODCAST to take advantage of this special offer. |
![]() |
“Finally, knowledgeable people talking about building reasonably-sized, high-performance houses for normal people with real budgets!” — DanD, VA, 8/19/22, Amazon.com review |
We hope you will take advantage of a great offer for our podcast listeners: A special 20% off the discounted rate to subscribe to the Fine Homebuilding print magazine. That link goes to finehomebuilding.com/podoffer.
The show is driven by our listeners, so please subscribe and rate us on iTunes or Google Play, and if you have any questions you would like us to dig into for a future show, shoot an email our way: [email protected]. Also, be sure to follow Fine Homebuilding on Instagram, and “like” us on Facebook. Note that you can watch the show above, or on YouTube at the Fine Homebuilding YouTube Channel.
The Fine Homebuilding Podcast embodies Fine Homebuilding magazine’s commitment to the preservation of craftsmanship and the advancement of home performance in residential construction. The show is an informal but vigorous conversation about the techniques and principles that allow listeners to master their design and building challenges.
Other related links
-
- All FHB podcast show notes: FineHomebuilding.com/podcast.
- #KeepCraftAlive T-shirts and hats support scholarships for building trades students. So order some gear at KeepCraftAlive.org.
- The direct link to the online store is here.