Maximize HVAC Efficiency
This critical five-task commissioning process ensures forced-air heating and cooling is quiet, comfortable, and problem-free.
Synopsis: A critical element in the HVAC installation process is making sure the HVAC system was installed according to the plan and is working at maximum efficiency for energy savings and whole-house comfort. Called HVAC commissioning, this process involves five steps. In addition to explaining how each step works, author Chris Hughes shares key questions to ask when designing an HVAC system in the first place.
A comfortable and energy-efficient home requires a well-insulated building envelope that effectively controls air and moisture flowing through it. To regulate temperature and humidity, it also needs a properly designed and installed HVAC system with equipment and ductwork that matches the requirements of individual rooms for airflow and for heating and cooling.
But there is a critical step in the HVAC installation process that is frequently overlooked: making sure the HVAC system was installed according to the plan and is working at maximum efficiency for energy savings and whole-house comfort. This five-step series of tests is called HVAC commissioning and is usually part of the HVAC contractor’s job, but I’m going to go step by step through the process so you’ll know if your HVAC contractor is skipping one or more of the steps or fudging numbers.
Standard 310 is a new and widely accepted process for commissioning residential forced-air heating and cooling systems. This standard resulted from a collaboration among three organizations: the American National Standards Institute (ANSI), the Air Conditioning Contractors of America (ACCA), and the Residential Energy Services Network (RESNET). Commissioning pays huge dividends in comfort and energy savings for homeowners, and if the system is designed and installed according to the plan, commissioning is a relatively easy process that confirms everything is working properly. It can also reveal problems with the new system that if left unresolved could cause equipment damage or comfort complaints down the road.
Before commissioning: Start with a successful designWhat are the system’s design conditions? Commissioning confirms that a system is working to spec, but it won’t improve a system that’s performing poorly because of a flawed design. In addition to egregious errors like rule-of-thumb sizing or intentional What is the building’s airtightness target? Many HVAC designs use default estimated rates for air leakage, which can lead to oversized equipment that provides poor comfort and humidity control. The 2021 International Residential Code (IRC) recommends less than three air changes per hour (3 ACH50) as the airtightness goal for a comfortable home and efficient HVAC system. Airtightness should be specified in the Manual J load calculations and should be tested with a blower door before interior finishes are in place so that leaks can be corrected more easily. At a minimum, the airtightness specified in the Manual J should be confirmed with a blower-door test after system installation and before commissioning. What is the planned ventilation system? When a home is at or below 3 ACH50, most jurisdictions require mechanical ventilation. Whole-house supply-only and exhaust-only systems, as well as spot ventilation like bath fans and range hoods, can add to HVAC loads. In hot, humid climates a ventilating dehumidifier is better, and balanced ventilation systems—HRVs and ERVs—are the preferred solution for comfort and energy efficiency. The design should reflect the correct system. What is the house’s Solar orientation? South- and west-facing windows and doors can add greatly to cooling loads, but north-facing windows have little impact on the solar load of a house. North-facing windows also add significantly to the heating load. Solar orientation matters more than you would think, so check carefully that the design has it right. What is the window performance? Energy-performance ratings for windows include U-factor and solar heat-gain coefficient (SHGC) measurements. U-factor is an indication of heat transfer, and SHGC is a measure of how much solar radiation the windows allow into the home. Lower numbers are better for both measurements. HVAC system designers may assume a code-minimum U-factor or SHGC, so it is important to be specific if you are using glazing with better performance numbers. Where is the HVAC system located? This is a big one: Keep the equipment and ductwork in a conditioned space when possible—or expect higher energy bills and comfort complaints. Simply put, if you are putting ductwork in an unconditioned space (a vented crawlspace or attic or an unconditioned garage), you are essentially putting it outside of your building envelope and accepting a huge potential hit to comfort and efficiency. How many people will be in the house? Occupants add to cooling loads, and a residential load calculation includes one person per bedroom plus one. Some designers add extra people to justify a bigger system when it is not needed. |
You can think of commissioning as tuning the system. It starts with verifying that the system is designed properly, with an accurate heating and cooling load calculation and proper equipment selection based on the loads. For commissioning, the system must be fully complete, with ductwork installed and sealed according to the plan, with equipment fully operational, and with all grilles, registers, and specified filters in place.
In an ideal scenario, every new HVAC system would undergo commissioning by the HVAC contractor or a reputable third party, often an energy rater, to ensure that the system is working to spec. Unfortunately, commissioning is seldom part of residential HVAC installations, so you’ll need to be clear when hiring a contractor to install a new system that you want it to be properly commissioned per Standard 310.
Homeowners and home builders have an incentive to undergo commissioning because they can benefit through tax credits. If you hire a certified HERS rater to perform a commissioning process like the one shown here, then the property owner can apply for Zero Energy Ready Home tax credits for every home with a passing score.
Task 1: Evaluate the design
The design is the most important part of an HVAC installation, so the first task of commissioning is to evaluate the design specs for accuracy and then ensure that the components of the system match the specs. High-performance builders increasingly are using third-party design services because the designs by HVAC techs are almost always oversized, and some HVAC contractors don’t offer design services. I’ve seen badly designed or installed systems cost a great deal of money, time, and aggravation—maybe even one marriage. In order to right-size an HVAC system, a load calculation using Manual J should have been completed on the dwelling. A load calculation determines the home’s room-by-room heating and cooling loads, taking into account climate, airtightness and insulation values, size, window glazing and locations, and solar orientation. Load calculations are usually performed in a computer program or painstakingly done by hand.
After the load calculations come equipment selection (Manual S) and duct design (Manual D). Manual T is a subsection of Manual D and addresses the grille and diffuser selection; it’s sometimes overlooked in retrofits, but should be included in new-construction projects. These technical manuals are important components of a quiet, efficient, and comfortable heating and cooling system.
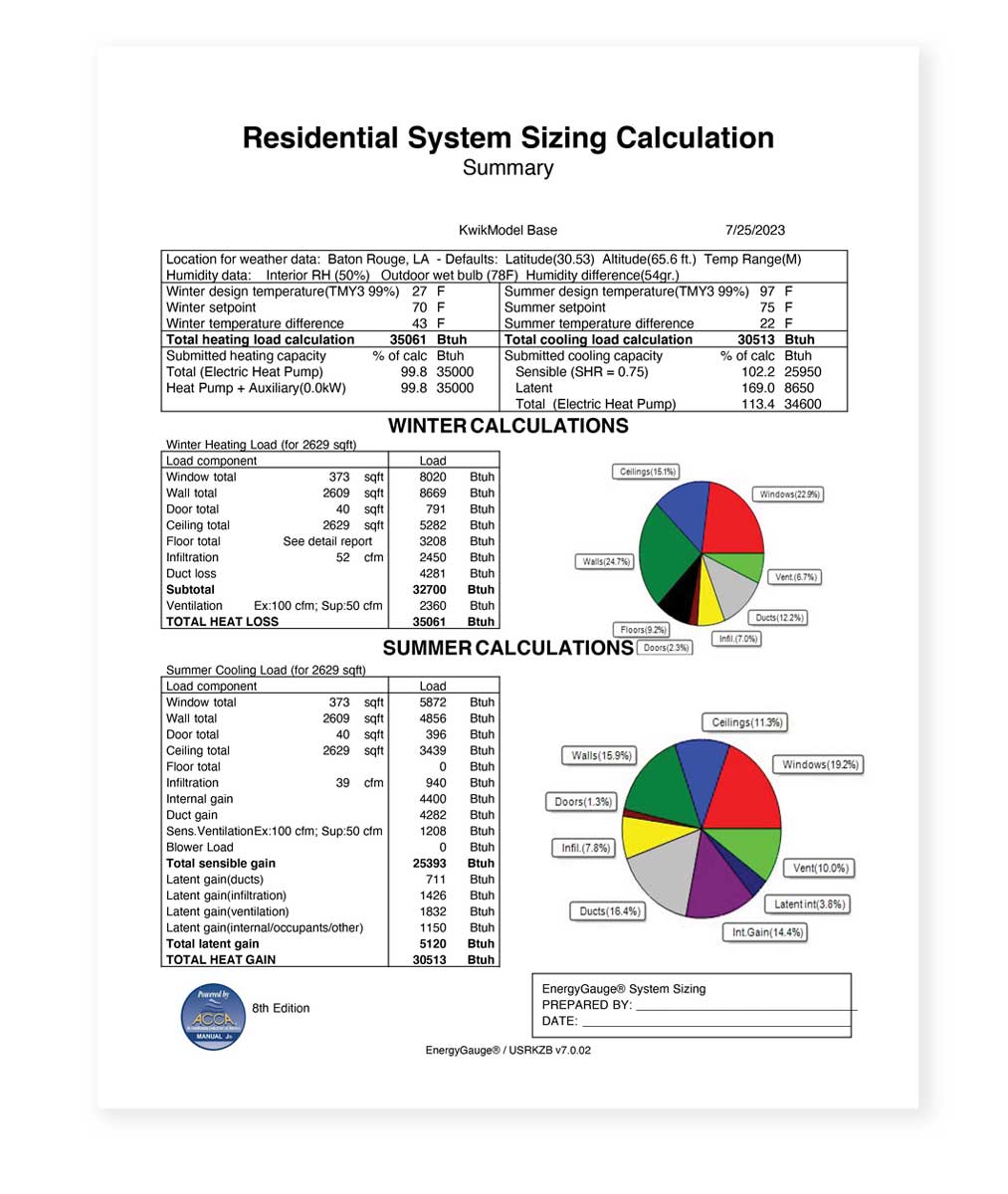
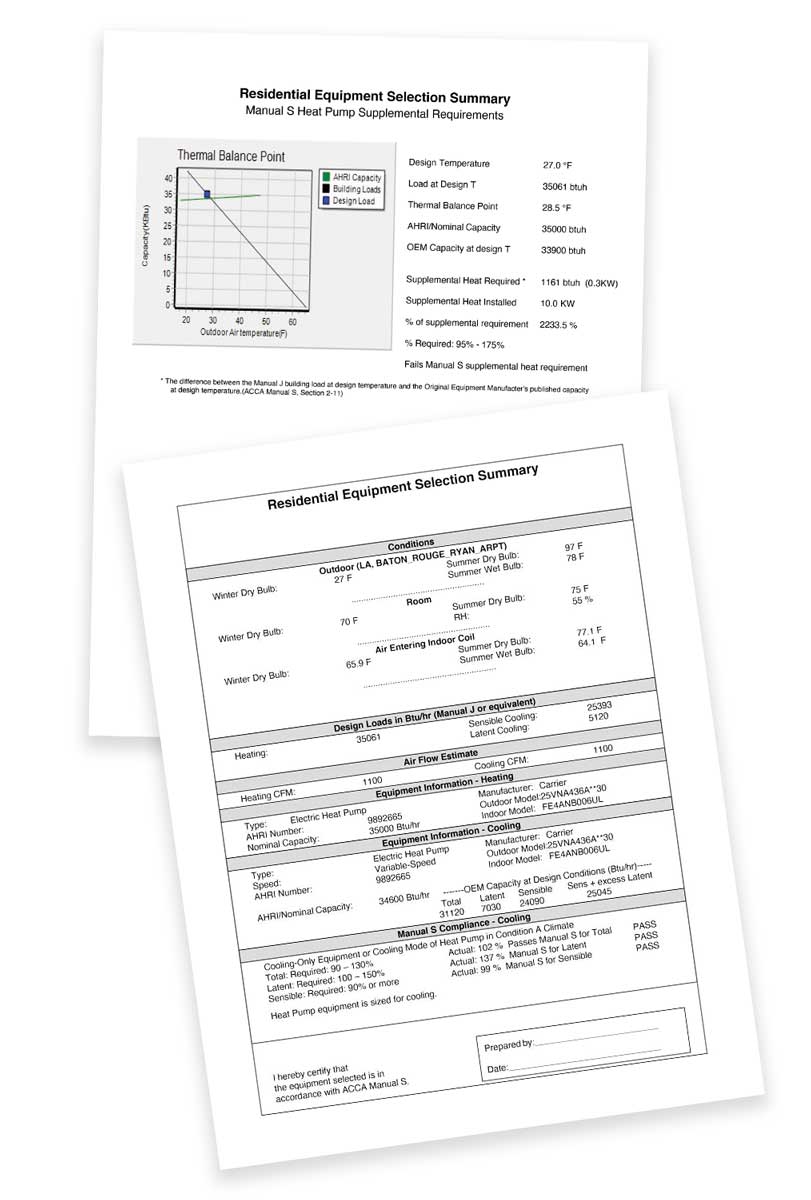
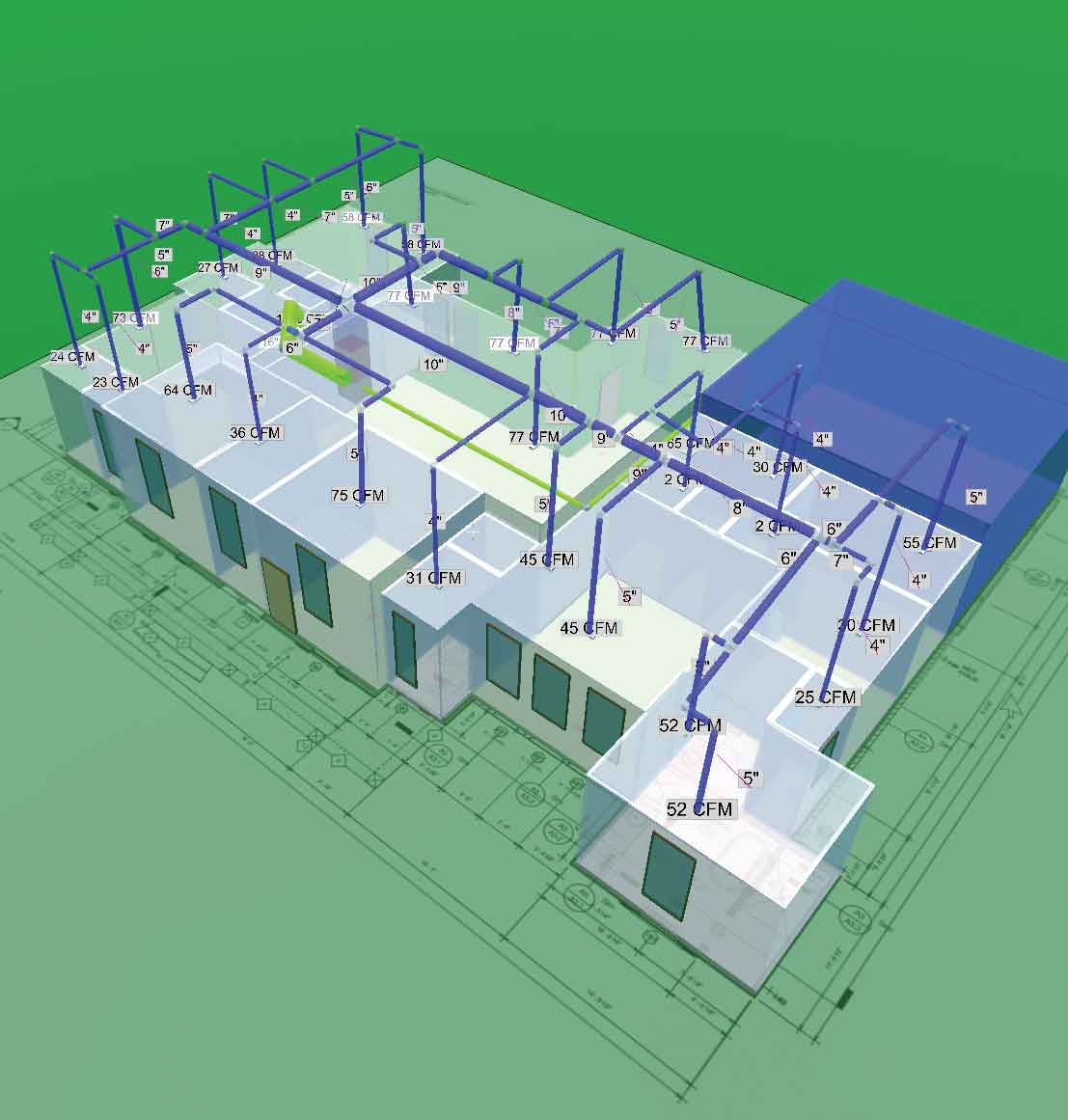
Task 2: Test duct leakage
Duct leakage is measured by connecting a duct-leakage fan and manometer to the installed ductwork. The tester pressurizes (or depressurizes) the HVAC system and measures the leakage flow rate in cubic feet per minute (cfm) per 100 sq. ft. of living space. Allowable leakage rates are listed in the International International Residential Code (IRC). Many jurisdictions don’t require duct-leakage testing, but if you have ductwork in unconditioned spaces, I advise it. Leaky ducts in unconditioned spaces have a significant impact on comfort, capacity, energy usage, and durability. Even if all the ductwork is inside the conditioned space, leaky ducts can cause isolated comfort problems by preventing conditioned air from reaching all of the registers, resulting in a bedroom that is too hot and humid in the summer, for example.
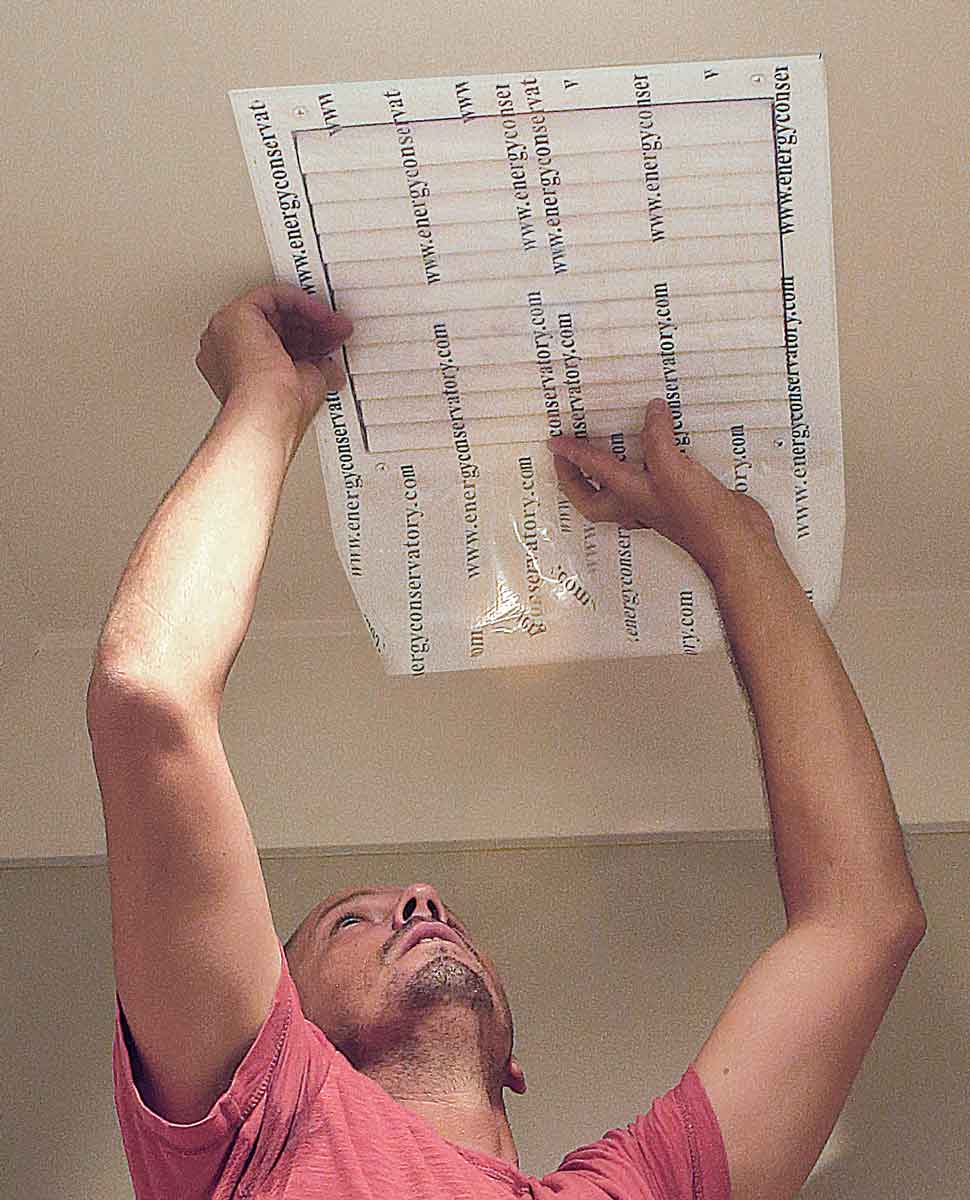
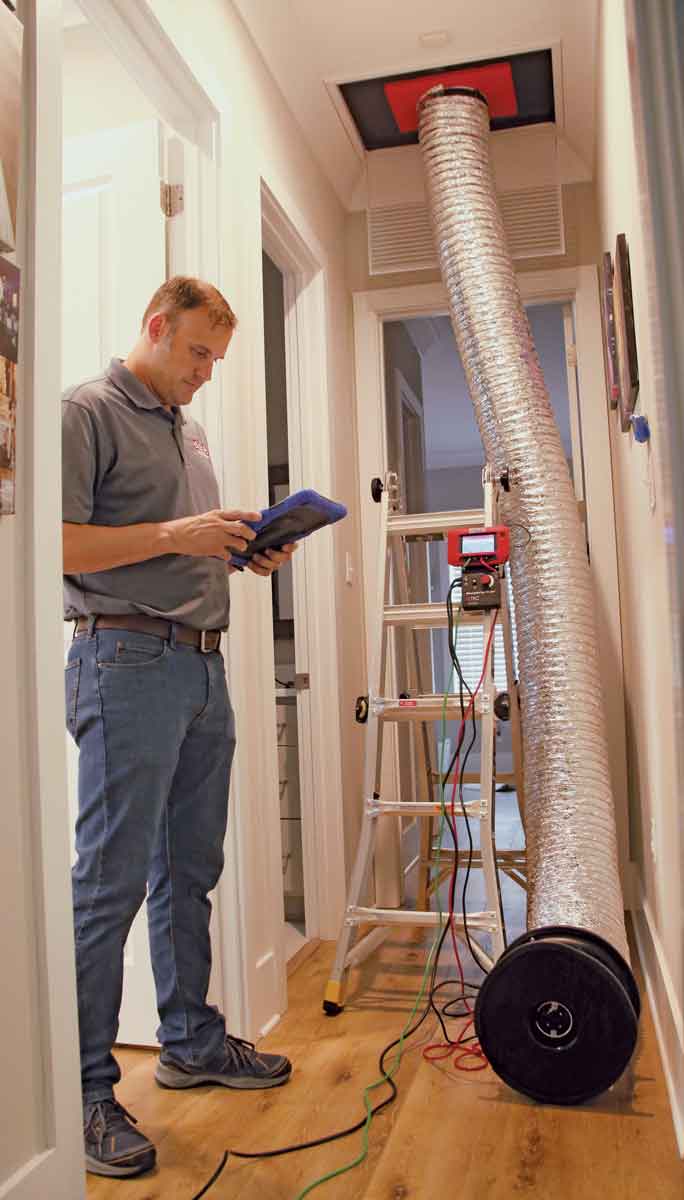

Task 3: Confirm system airflow
Ensuring that the system airflow across the cooling or heating coil within the air handler is set correctly is fundamental to ensuring that a system will properly condition and dehumidify a house. The Manual S system selection will have a total system airflow target for summer and winter. The commissioning process includes verifying this airflow target and confirming the correct fan speeds are selected for both heating and cooling. Proper fan speed is a balancing act with a vital role in protecting equipment and controlling humidity and temperature. System airflow tests should be completed after the system has run for at least 10 minutes to ensure that measurements are made at operational conditions.
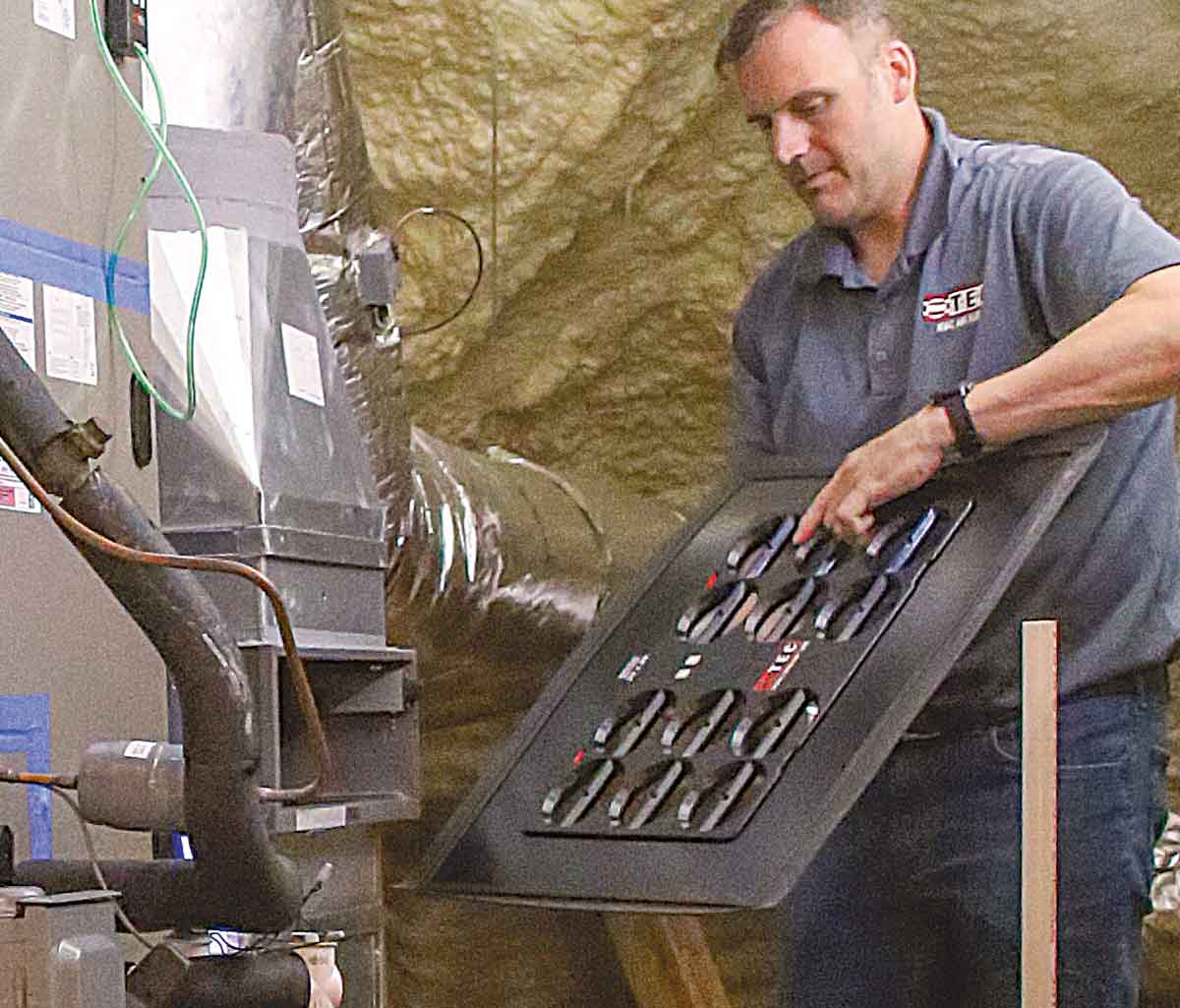
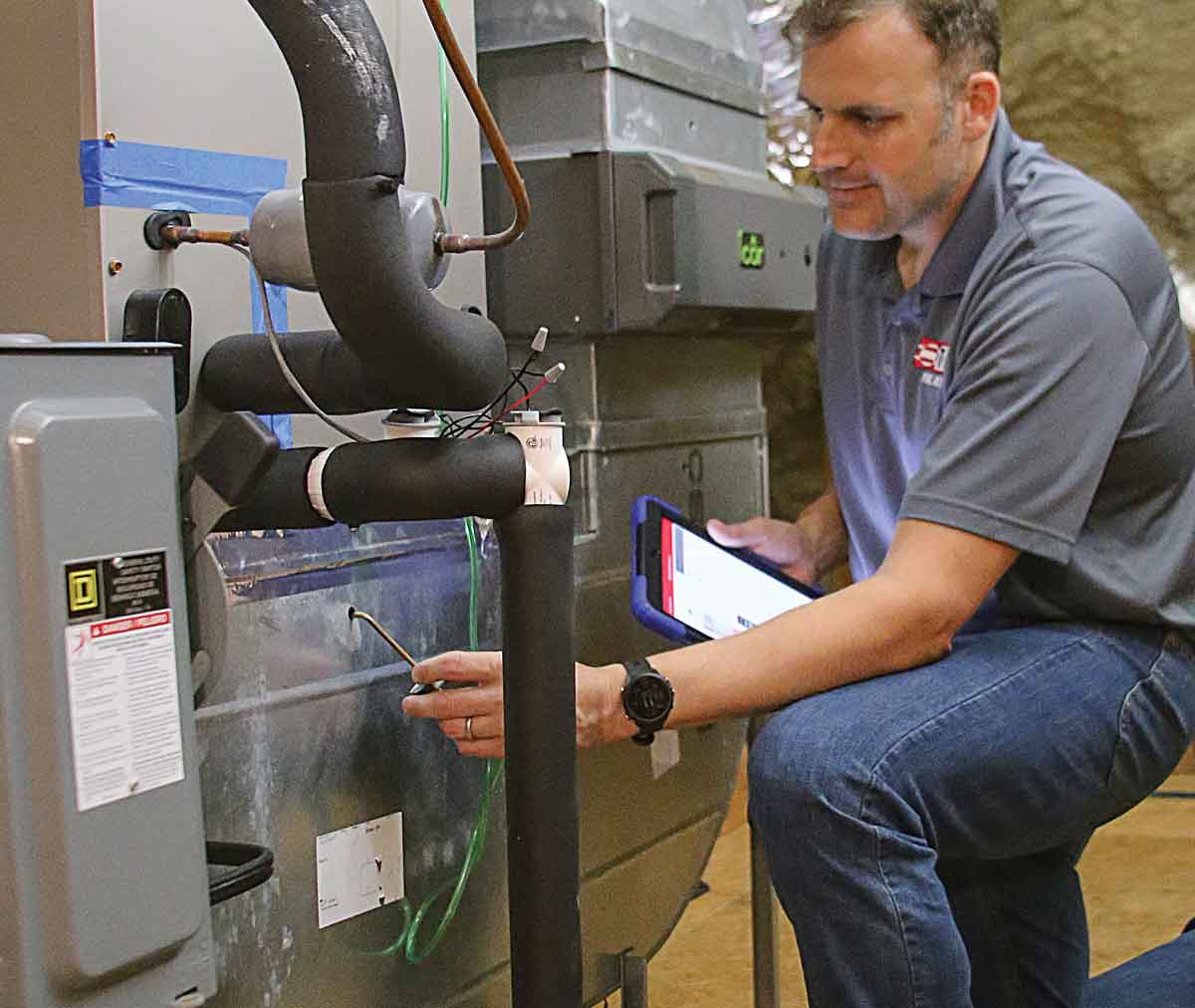
Task 4: Check power consumption
Checking the air handler’s blower for its wattage draw confirms that the ducts aren’t too restrictive and that the blower motor is working correctly. Some HVAC systems have on-board diagnostics that monitor wattage draw of the blower. More commonly, a clamp-on multimeter is used during commissioning to determine the watts consumed by the running blower motor.
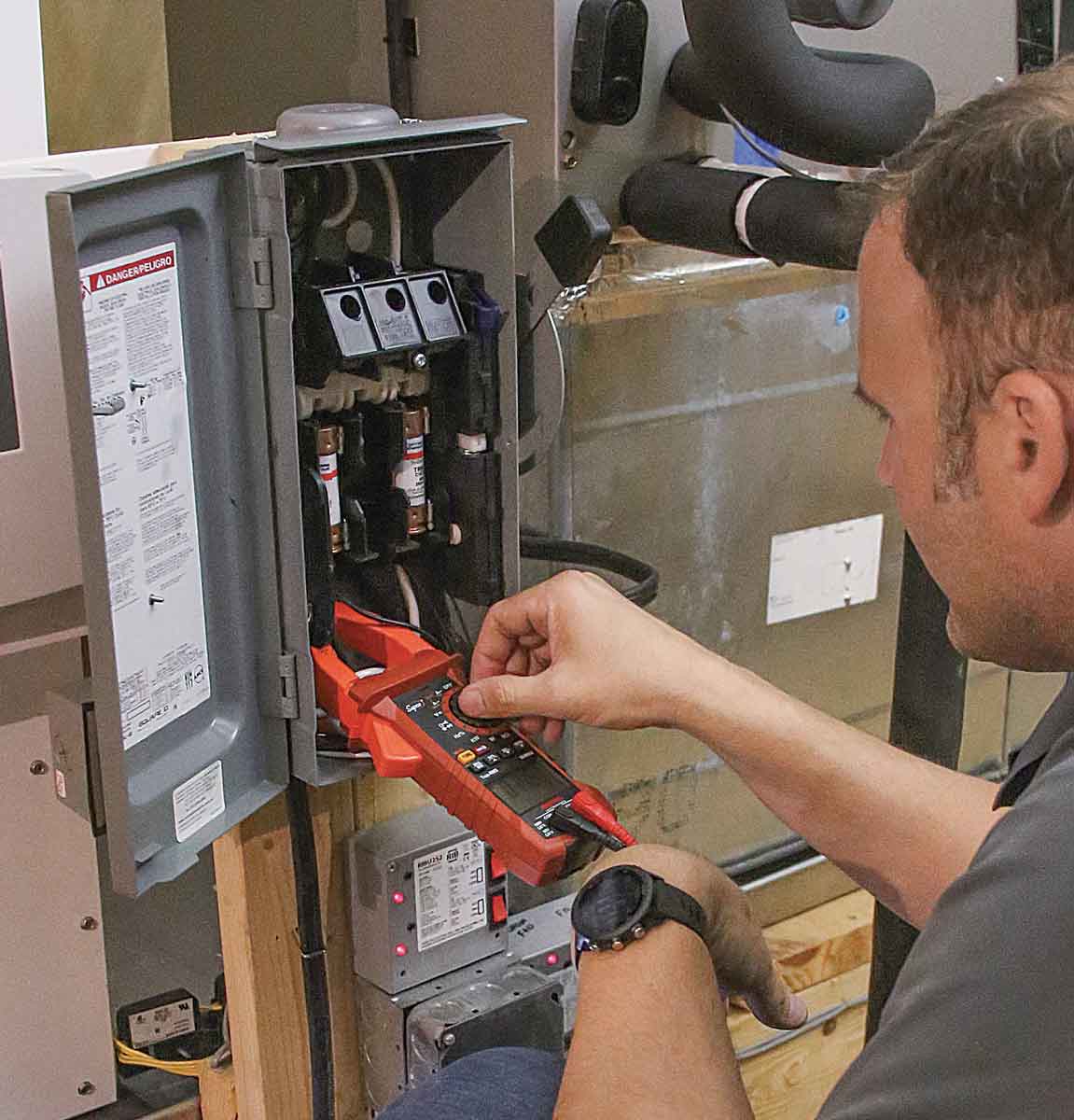
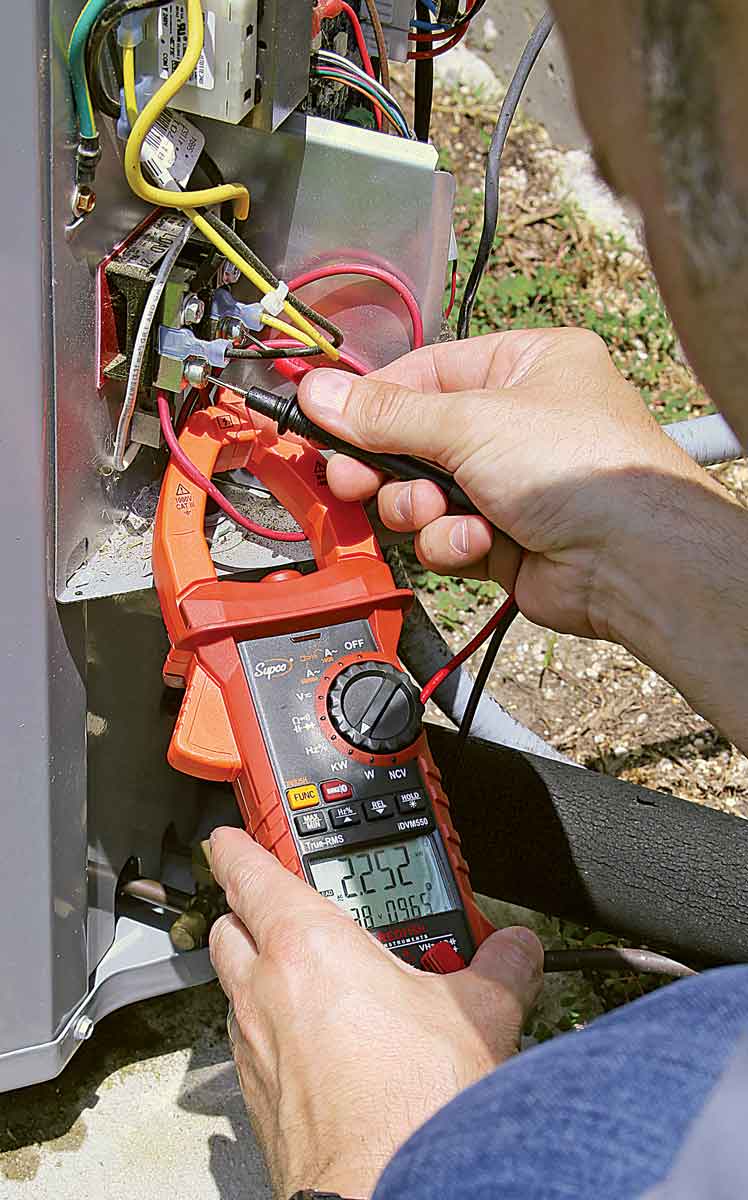
Task 5: Measure refrigerant charge
The amount of refrigerant in the system is described as its “charge,” and having the right charge plays an enormous role in the cooling capacity of the system. Traditional methods for establishing the refrigerant charge require HVAC training, because you have to connect pressure gauges to the refrigerant lines, but the measureQuick app allows you to measure the refrigerant charge without using a traditional refrigeration manifold set. If the refrigerant levels are low or high, the charge must be adjusted by a trained HVAC technician.
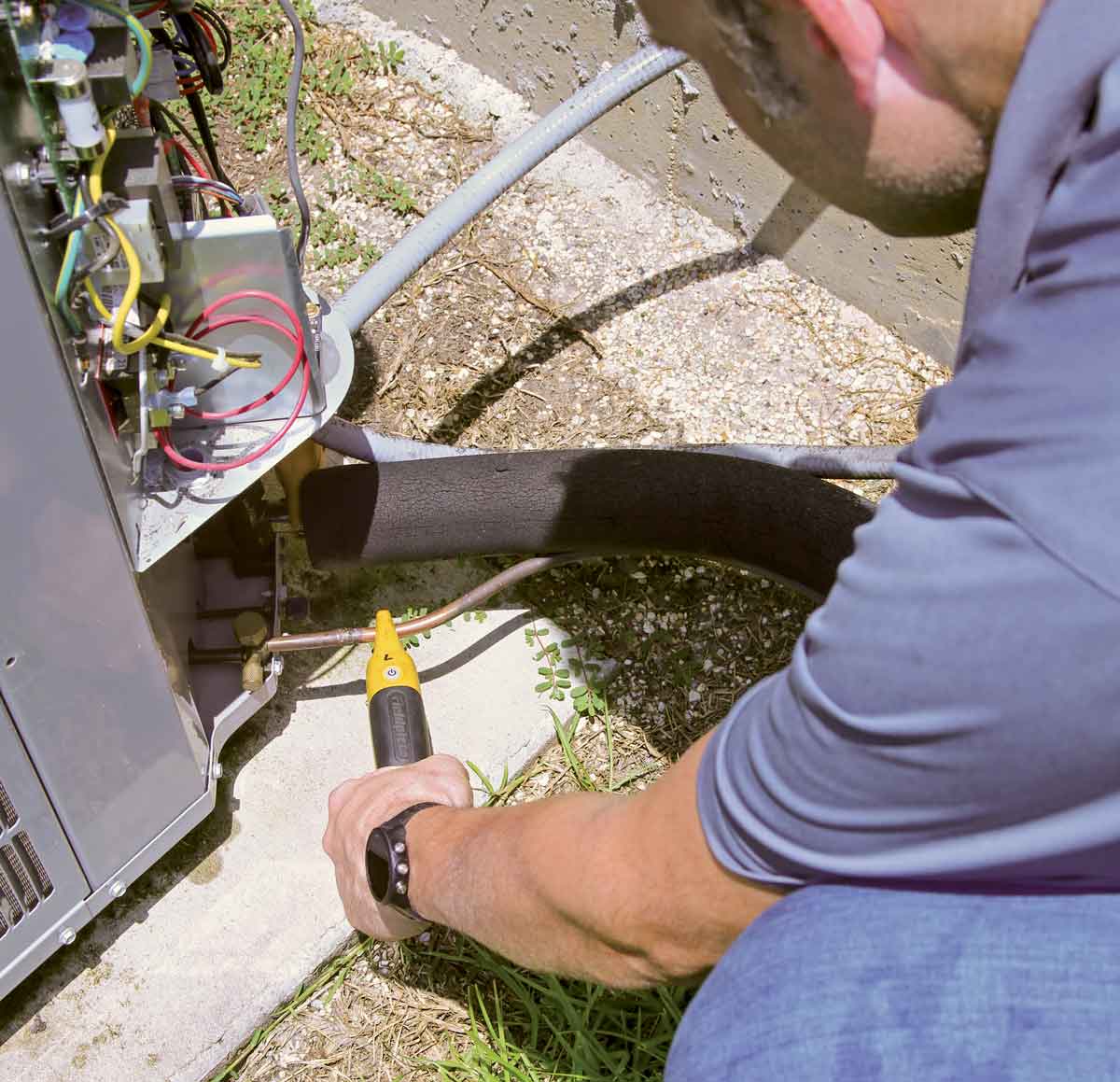
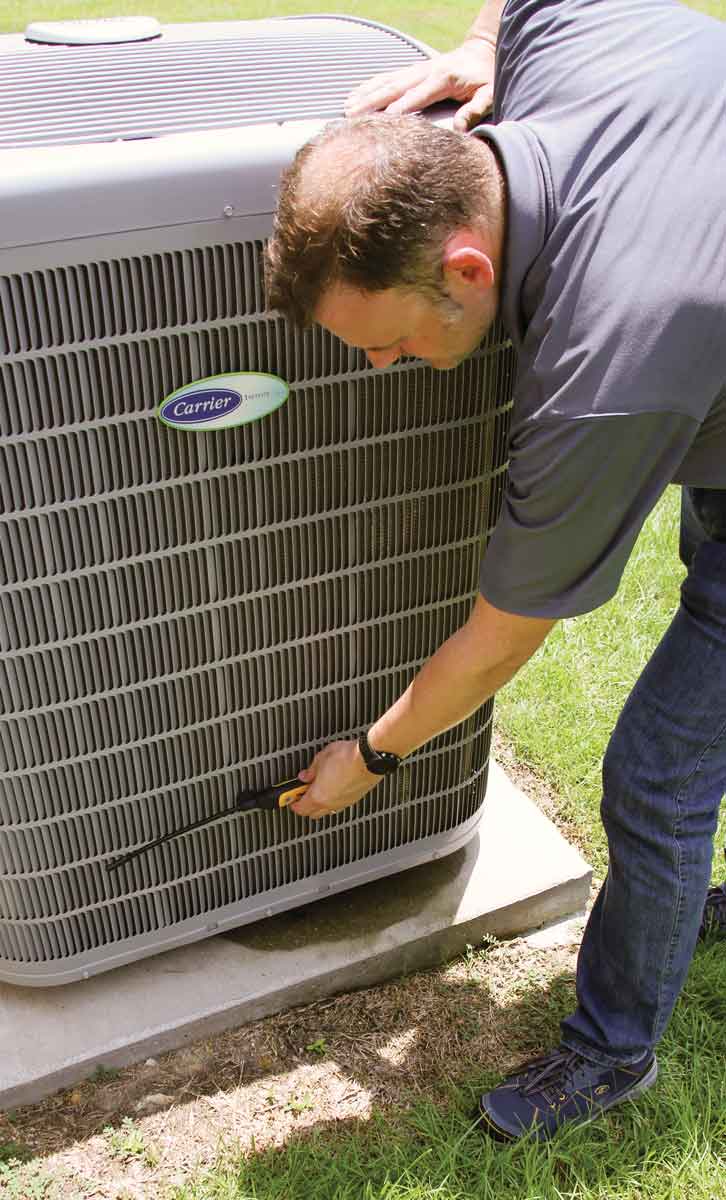
Chris Hughes is business development manager for TEC (The Energy Conservatory). Photos by Patrick McCombe.
From Fine Homebuilding #320
RELATED STORIES