Podcast 611: With Bill Beleck: Shou Sugi Ban, Surplus Building Products, and Air-Sealing Overhanging Joists
The crew hears from listeners about contracting in high-end zip codes and the economy of electric cars. Also: installing shou sugi ban forest products, saving leftover material, and how to air-seal a floor system that overhangs the foundation.
Follow the Fine Homebuilding Podcast on your favorite app. Subscribe now and don’t miss an episode:
![]() |
![]() |
![]() |
Alex shares thoughts on zip-code-adjusted contractor pricing and EVs. Bill Beleck, president of Nakamoto North America, talks about shou sugi ban forest products. John Paul asks about storing leftover building material and mechanical parts and fittings.
We’ve created a custom eLearning coupon for podcast listeners – code: PODCAST20
The Sustainable Home Building Accelerator
This intensive, interactive online series of courses is designed to rapidly advance your knowledge of sustainable home design and construction. Whether you’re an architect, builder, or a homeowner, we’ll give you the information and confidence to design and build well-crafted, practical homes that maximize performance and comfort.
Over 11 hours of video. AIA Approved 10 HSW/LU Credits. Resnet 10 PD Credits.
When you purchase all three courses, you’ll receive access to a year of GBA Prime as well as a copy of the Pretty Good House book!
Remember the code PODCAST20 for any Fine Homebuilding courses.
Editor Updates:
- Bill Beleck, president of Nakamoto North America, talks about shou sugi ban forest products.
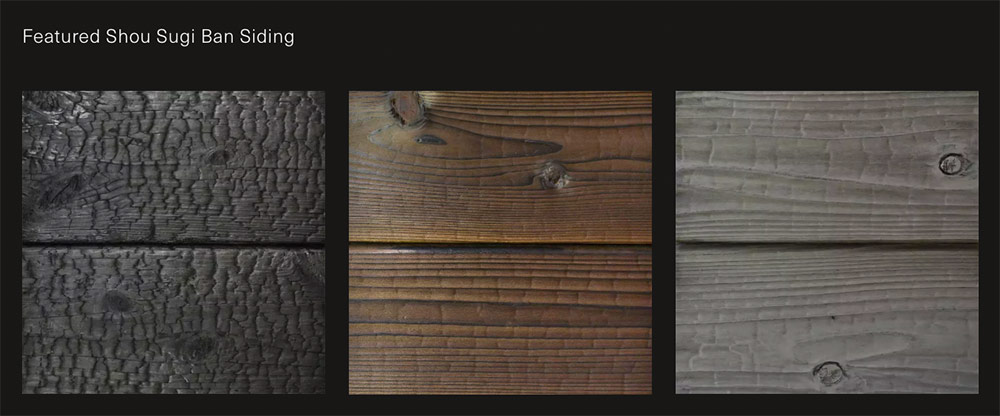
![]() |
![]() |
![]() |
![]() |
Listener Feedback 1:
Alex writes: FHB gang,
You inquired if anyone has been charged more for services living in more expensive areas, and I have experienced this firsthand.
I hired a contractor to do the masonry work for a garage I built and chatted him up about construction. He told me a story about a deck he built in Montgomery county, where he gave the client a quote that he thought was high because he didn’t really want to do the job. He ended up getting hired for it because the homeowner said he was the lowest bid. The contractor called this the Montgomery county tax.
Montgomery county is just north of Washington, DC, and there are some areas that are very expensive and other areas that are more middle income. To give you an idea of how much it costs to live in the area: My house is 750 ft² (1100 ft² including the basement) is valued at $650,000, and it’s the kind of home that gets torn down around me.
My 14-year-old gas-fired hot water heater started leaking from the pressure-relief valve, and I decided to replace it considering its age. I figured I would replace it with an instantaneous hot water heater and got a quote from a plumber to install the new hot water heater for $18,000, not including the cost of the heater. When I asked for a breakdown of where the $18,000 was going, the plumber blew off my question. That was the only and last time I’ll ever pay for any kind of bid—$100 wasted. I found someone else who installed it for $2,000 plus the cost of the water heater.
Love the podcast, keep up the great work – Alex
Related Links:
- Checking Your Construction Estimate
- Anatomy of a Building Project’s Price
- Estimates, Bids, and Proposals in Residential Building
Listener Feedback 2:
Alex writes:
If you do the math, you’ll find that owning an electric car is cheaper than an equivalent gas car. Here is a a spreadsheet using actual numbers for the state of Maryland.
Over a ten-year period—ignoring things like a panel upgrade, installing a Level 2 charger, or other expenses associated with either vehicle—it’s cheaper to own a Tesla Model 3 than a Honda Civic. If you keep your car longer, it becomes even more cost effective.
Related Links:
- NRDC: Electric vs. Gas Cars: Is it Cheaper to Drive an EV?
- energy.gov: Saving Money with Electric Vehicles
- A Truck That Powers the Job
Question 1: About charred wood siding
Next came the moment where one decision tripled the amount of work the fence would take: instead of taking the easy way and staining the 6-ft. deck boards black…we decided to do our fence in the Japanese style of yakisugi (sometimes referred to as shou sugi ban). The main benefits of this traditional technique is it gives the wood durability and incredible resistance to the elements. Claims of yakisugi producers say the wood should last 50-100 years with regular oiling every 10 years. At the time, we couldn’t find anyone who produced yakisugi in the board size we needed. This meant I now had an excuse to buy a flame thrower.
Here’s how we did the yakisugi: we bought 500+ 6-ft. untreated cedar deck boards and set them up vertically in batches of 60 on a homemade stand in our driveway. Our best results were stacking the boards three deep and twenty wide. This minimized the amount of setup time and helped limit the number of boards knocked off the stand by wind. For anyone attempting this at home, I’d recommend the IdealGas Single-Head Heating Torch, as the enclosed nozzle keeps the electrical starter from melting a hundred boards in. The wood goes through a process of 1) first-char on both sides, 2) brush both sides with water and an acrylic-bristle broom to remove the first layer of loose char, then 3) second-char on both sides, followed by 4) two coats of alkyd oil per side. What baffles me is that for the past five months the attendants at the gas station never questioned how we could be going through two 15-lb. propane tanks every two hours on the weekends.
For any yakisugi purest listening to this podcast, yes we are aware that we didn’t do the traditional flue method. Living in the suburbs of Minneapolis that seemed like too good a reason for someone to call the fire department on us. Even so, I was nervous and kept checking Nextdoor to see if anyone wrote about the crazy millennials down the street with a flame thrower. But what we found is this project actually had a very positive reaction from our neighbors. It gave them an excuse to stop by on their walks, ask questions, and cheer us on! Which was much needed as we transitioned into the digging phase of the project.
Related Links:
- Charred Wood Siding for Maintenance-Free Beauty
- Wood Siding: Burnt, Brushed, and Burnished
- Cladding Details That Last
Question 2: How do you store leftover materials?
John Paul writes:
As an ambitious DIYer I tackle nearly all the home repair and improvement on our house and studio/shop outbuilding. I often have material left over—a little lumber, paint supplies, plumbing and electrical fittings. I never know whether to save or return these items. It sure is handy to have stuff on hand for efficient repairs, but it can take up a lot of space. And it’s easy to spend a lot of time looking for stuff I’m sure I have, maybe as much time as a run to the hardware store. How do you decide what items to keep in stock and what to return? Have you found efficient ways to store and quickly find the many things used to build and maintain houses?
Related Links:
Question 3: What’s the best way to insulate cantilevered pockets?
Cory writes: Hello FHB,
Your group is awesome, inspiring me to tackle some basement insulation.
I’m in Roanoke (in southwest Virginia) and have a currently unfinished walkout basement (though 75% below grade). Our winters average 40˚ high/30˚ low. I’m currently insulating the rim joists with 2-in. XPS (phase 1 of ???). I plan to follow with 2-in. XPS on concrete walls, then studs/insulation/drywall. I’ve knocked out the first dozen or so and am starting to get the hang of the foam gun.
My scenario: I have about 10-12 cavities that cantilever over the concrete ~36 in. Part of the kitchen is above the cantilever and below the cantilever is the outside, below-grade patio base. Before the patio base was laid, I covered the underside with tar paper and 2-in. XPS. The cantilever pockets were previously filled with fiberglass batts.
My question: With all the nail protrusions into the cantilevered cavities from sheathing under the bumpout, cabinets/flooring above, and the dimensions, getting foam into these areas and in place will definitely be challenging. I could try to knock down nails and get a 3-ft. piece of tubing to seal XPS sections. Or should I plan to froth-pack these areas myself and keep moving on?
These cavities have some light mold (I’m guessing), likely from poor air-sealing previously (until a year ago these cantilevered cavities were below a deck, not a patio base).
Any insight you can share would be great! I’d love your input even before this is considered for podcast airing!
Thank you,
Corey
Related Links:
Podcast 611: Members-only Aftershow — Bill Beleck’s New House
The crew talks to Bill Beleck, president of Nakamoto North America, about building his new house. Discussion topics include putting forest products on display in a new build, how an asymmetrical roof is tough for a framing crew, and how wildfire affects building-material selections.
This episode of The Fine Homebuilding Podcast is brought to you by Loctite’s Tite Foam
Say no to inefficient and drafty. Say yes to Loctite Tite Foam.
When pros need to seal gaps too small for insulation but big enough to create a draft, they reach for Loctite’s TITE FOAM.
The high-density foam forms a tenacious bond to most common building materials, stays flexible to prevent cracking, and keeps air, moisture, and pests out of the house.
Whether you’re adding R value to the rec room, or finishing a boring basement, give that space a second chance with Loctite Tite Foam.
Visit LoctiteProducts.com for more information.
Check out one of our latest Project Guides: Energy Retrofit!
Check out our FHB Houses:
Visit the Taunton Store • Magazine Index • Online Archive • Our First Issues • All Access
If you have any questions you would like us to dig into for a future show, shoot an email our way: [email protected].
If we use your question we’ll send you a FHB Podcast sticker!
FHB Podcast T-shirts!
Represent your favorite podcast! Available in several styles and colors. Made from 100% cotton. Find the Podcast t-shirt and more cool products in the Fine Homebuilding Store.
Fine Homebuilding podcast listeners can now get 20% off anything in the Taunton store, including Pretty Good House.
Use the discount code FHBPODCAST to take advantage of this special offer. |
![]() |
“Finally, knowledgeable people talking about building reasonably-sized, high-performance houses for normal people with real budgets!” — DanD, VA, 8/19/22, Amazon.com review |
We hope you will take advantage of a great offer for our podcast listeners: A special 20% off the discounted rate to subscribe to the Fine Homebuilding print magazine. That link goes to finehomebuilding.com/podoffer.
The show is driven by our listeners, so please subscribe and rate us on iTunes or Google Play, and if you have any questions you would like us to dig into for a future show, shoot an email our way: [email protected]. Also, be sure to follow Fine Homebuilding on Instagram, and “like” us on Facebook. Note that you can watch the show above, or on YouTube at the Fine Homebuilding YouTube Channel.
The Fine Homebuilding Podcast embodies Fine Homebuilding magazine’s commitment to the preservation of craftsmanship and the advancement of home performance in residential construction. The show is an informal but vigorous conversation about the techniques and principles that allow listeners to master their design and building challenges.
Other related links
-
- All FHB podcast show notes: FineHomebuilding.com/podcast.
- #KeepCraftAlive T-shirts and hats support scholarships for building trades students. So order some gear at KeepCraftAlive.org.
- The direct link to the online store is here.