Furnace to Heat Pump Retrofit
With proper load calculations, equipment selection, installation, and commissioning, you may be able to save energy and money while cutting emissions from fossil fuels.
Synopsis: Done correctly, heat pump retrofits can drastically shrink household emissions and, in some cases, reduce energy costs. HVAC project manager Jon Harrod outlines the steps of a heat pump retrofit, which can take the form of a one-to-one furnace replacement, include the addition of a ductless zone, or incorporate a heat pump in addition to a furnace for a dual-fuel system. The first tasks involve determining the home’s air-leakage rates and heating and cooling loads, and then using that information to assess the existing ducts. Harrod discusses equipment capacity and how to determine the sweet spot for efficiency when deciding on a new system.
According to the Energy Information Administration, more than 50 million homes in the United States are heated with forced-air systems that burn natural gas, propane, or fuel oil. Replacing these furnaces with heat pumps presents a significant opportunity to reduce fossil-fuel use. Because ductwork is already in place, the retrofit can often be done without disrupting the finished space. The old furnace is removed, and the fuel lines and venting are capped. The heat pump’s indoor unit, the air handler, is installed in the place of the old furnace. Like a furnace, an air handler has a blower fan, but instead of a burner and heat exchanger, it has a refrigerant coil.
The heat pump also has an outdoor unit containing an additional coil, a fan or fans, a compressor, and controls. Refrigerant circulates between the indoor and outdoor units through insulated copper tubing. In summer, a heat pump provides air conditioning; in the winter, heating.
Done correctly, heat pump retrofits can drastically shrink household emissions and, in some cases, reduce energy costs. But there are several places where things can go wrong, leading to comfort complaints and excessive energy bills. I’ve been involved in dozens of these retrofits, including in my own home, and have experienced the learning curve firsthand. In this article, I’ll talk about the information I gather when planning a heat pump retrofit, then dig into equipment selection, installation, and startup, which are all critical to achieving a good result.
Set project goals and expectations
Any successful heat pump retrofit begins with clear goals. I start by asking what’s driving a customer’s interest. Are they looking to replace an aging system, cut their heating bills, or reduce their carbon footprint? Often, a heat pump retrofit provides an opportunity to address comfort and air-quality issues. Are there rooms that are inadequately heated or cooled? Are the customers interested in better air filters or central ventilation? I also ask whether they intend to keep another heat source such as a woodstove as backup. What is their plan in the case of an extended power outage?
It’s also important to talk about budget and financing. A high-efficiency heat pump will cost considerably more than a simple furnace and air conditioning replacement. But utility incentives, state grants, and federal tax credits can bring the net cost down, and financing can spread payments over time.
I also set appropriate expectations for energy savings. A heat pump’s efficiency can compensate for its added cost, particularly if it displaces a delivered fuel like oil or propane. But it’s important not to overpromise, and to acknowledge that savings are subject to changing energy prices, year-to-year weather fluctuations, and homeowner habits.
The building enclosure affects loads
Once I understand the customer’s goals, I gather information on the building. The building enclosure determines how much heating and cooling capacity is needed. The Air Conditioning Contractors of America (ACCA) Manual J provides the industry-standard method for calculating these design heating and cooling loads. Most Manual J calculations are done with software.
Careful sizing is critical to a good result. An undersized system won’t keep the house comfortable in extreme weather. But oversizing a system can also create problems: higher up-front cost, more frequent on-and-off cycling, more noise, and a shorter life span. In the summer, an oversized system will cool the home rapidly but shut off before it can dehumidify the air.
Accurate load calculations require accurate inputs. For surfaces like roofs and walls, this means taking careful measurements and assessing insulation levels. If in doubt, I’ll perform a thermal scan or probe the wall with a wire hook. For windows, I determine the number of panes, the frame material, and, if possible, the presence of a low-e coating. For cooling loads, window orientation and roof overhangs also come into play.
In most of the houses I’ve worked on, air leakage is the largest source of winter heat loss. Manual J allows a qualitative rating of building tightness. But measuring leakage with a blower door provides more accurate results.
The enclosure assessment may identify opportunities to upgrade insulation and reduce air leakage. In some cases, enclosure upgrades make it possible to heat the home with a smaller, less expensive heat pump.
Before proceeding with the retrofit, we also need to determine if the existing electrical service can accommodate the increased load. The National Electric Code describes a procedure for performing this assessment (NEC 220.83). Key inputs include the home’s square footage, the number of countertop small-appliance circuits, the wattage of larger appliances like electric ranges and water heaters, and the electrical requirements of the proposed equipment. If the calculation calls for more amps than the existing service can provide, an upgrade may be needed.
Will existing ducts work?
Heat pumps require one-and-a-half to three times more airflow through the duct system than furnaces with the same heating capacity. This is because heat pumps deliver cooler air, typically around 95°F, compared to the 105°F to 140°F typical of a fossil-fuel furnace. Each cubic foot of air contains less heat energy, so more flow is needed.
To determine if existing ducts can work, I make a quick tally of the size and number of supply and return trunks and branch ducts, then use an air-duct calculator to estimate their capacities. Duct calculators come in several forms—apps, online tools, and old-school cardboard slide rules. When we replace a furnace with a heat pump, enclosure improvements and careful sizing calculations often allow us to install a system with a smaller heat output than the one we are taking out. This downsizing often makes it possible to get satisfactory flows from existing ductwork. It’s not uncommon to replace an 80,000-Btu-per-hr. high-efficiency furnace (at approximately 1200 cu. ft. per minute, or cfm) with a 3-ton (36,000-Btu-per-hr.) heat pump (at approximately 1000 cfm); the reduction in system size more than cancels out the higher airflow per Btu required.
When the existing ductwork is undersized, I look for opportunities to add airflow. Is there a room that is currently underserved? Can I add a duct or enlarge an existing one? The easiest gains are usually on the return side. By upsizing the main return drop and installing a properly sized low-resistance filter, we can address the largest restrictions in most duct systems.
In addition to evaluating the size of the ductwork, I look at its overall condition. Are there visible leaks that can be sealed? Is ductwork that runs outside the thermal envelope insulated to at least code-minimum R-8? Fixing these issues can improve the delivery of heated and cooled air, reducing energy costs and comfort complaints. Duct improvements can also improve indoor-air quality and durability by preventing condensation (and associated mold growth) and keeping contaminated air from places like attics and garages out of the living space.
3 APPROACHES TO HEAT PUMP RETROFITS
One-to-one heat pump retrofit: A heat pump can replace a fossil fuel–burning furnace and air conditioning coil using the already-installed ductwork in many homes. If the home doesn’t have air conditioning, this furnace replacement is an opportunity to add it, while potentially reducing fuel use, saving energy, and increasing comfort. The new equipment includes an outdoor unit (the heat pump), copper line sets that carry the refrigerant, and the air handler, which is typically installed where the old furnace once sat. If the house has no backup heat source, the system may include an electric-resistance heating coil.
Heat pump retrofit with a new ductless zone: If the house has any space with comfort issues, or no heating and cooling at all, an additional zone served by a ductless minisplit can be part of the heat pump retrofit. Breaking off a zone from the main body of the house can also help overcome capacity limitations. In a single-zone system, the air handler must satisfy the house’s entire heating and cooling requirements. If the load exceeds the maximum that a single air handler can deliver, it may make sense to use a separate ductless head to meet a portion of that load. Similarly, if the existing ductwork is too small to meet the heat pump’s airflow requirements, you can serve a portion of the house with a ductless head so the existing ductwork can adequately serve the rest of the house. Branch ducts may need to be enlarged, but the more labor-intensive work of replacing the trunks can be avoided.
Adding a heat pump for a dual–fuel system: In dual-fuel systems, the furnace remains in place. The heat pump’s indoor coil sits downstream of the furnace, just like the coil on a conventional air conditioning unit. The furnace and heat pump cannot provide heat simultaneously. Instead, the heat pump operates at mild temperatures, where its heating capacities and efficiencies are highest. At colder temperatures, the thermostat calls on the furnace for heat. Dual-fuel systems typically switch between heat pump and furnace at outdoor temperatures between 20°F and 40°F. The switchover temperature can be set so the furnace comes on when the heat pump can no longer maintain the home’s temperature, or be programmed to switch based on when it’s most cost-effective. Because residential furnaces can have large heat outputs, dual-fuel systems can make sense for houses with loads too large for a single heat pump. They offer redundancy; if the heat pump fails, the furnace continues to deliver heat. And they can offer the lowest operating cost for customers with natural gas. On the downside, they typically only displace 50% to 70% of fossil-fuel use. Gas and propane infrastructure (tanks, meters, and piping) and monthly meter charges remain in place.
Integrating the new equipment
One more sizing issue that comes into play in heat pump retrofits is the size of the mechanical room itself. Air handlers can be taller than fossil-fuel furnaces (though typically not as tall as a furnace plus air conditioning coil). In older homes with short basements, available height becomes a consideration.
Some heat pump air handlers have the fan upstream of the refrigerant coil. When the air handler is installed vertically, the fan is at the bottom of the air handler blowing upward. The advantage of having the fan upstream of the coil is that the return duct can connect to the side of the air handler, and the air handler can sit on a pad on the floor.
Other designs have the fan downstream of the refrigerant coil. For the return air to pass across the coil, it must enter through the bottom of the unit. In this arrangement, the air handler, which can be 50 in. tall or more, sits at least 12 in. off the floor. In a short basement, this may not leave room for a transition to the supply ductwork. When the air handler won’t fit in a vertical configuration, one solution is to switch to a horizontal installation. This may involve reworking the supply and return ducts.
The placement of the outdoor unit also requires some thought. Outdoor units need unobstructed airflow. Larger, dual-fan units can be tall enough to block first-floor windows, especially when mounted on stands to keep them above snow depth. When possible, they should be located on the gable end of the house rather than under an eave or drip line. Outdoor units should be placed away from gas meters, propane regulators, dryer vents, and exhaust for combustion appliances. We also try to locate outdoor units away from bedrooms to avoid noise complaints.
Understanding equipment capacity
Before selecting equipment, I review my design heating and cooling loads, making sure that I’ve modeled the building envelope accurately. Manual J builds in robust safety factors, so there’s no need to pad your inputs. Doing so will unnecessarily inflate your results. The best practice is to perform an aggressive calculation—one that takes advantage of every legitimate opportunity to reduce estimates of heat loss and heat gain.
Next I’ll determine whether a single ducted heat pump can adequately meet the home’s needs. In most cases, the answer is yes; the new heat pump can act as a one-to-one replacement for the old furnace. Except for changes required to fix defects or improve airflow, distribution and zoning remain the same as with the old system. If the existing ductwork is in reasonable condition, a one-to-one replacement is usually the simplest—and most cost-effective—approach. But there are situations where adding one or more ductless zones can make sense.
Once I’ve decided whether additional zones are needed, I’m ready to specify the heat pump (or heat pumps) I’ll be using. Choosing which model to use is more complicated than selecting a furnace. Unlike a furnace, whose output remains fairly constant regardless of outdoor temperature, heat pump capacity can drop off in colder weather. Modern cold-climate heat pumps have several features, including variable-speed fans and compressors, that allow them to extract heat from very cold air. Still, we need to look at a unit’s extended performance data to know how much heat it can deliver under local design conditions.
For both heating load calculations and equipment selection, we use 1% design temperatures. In a typical year, only 1% of hours—about 88 hours per year—fall at or below these temperatures. Design temperatures provide a better basis for equipment selection than record extremes. The safety factors built into the Manual J calculations allow the house to remain comfortable during those rare times when the temperature falls lower.
Selecting Goldilocks equipment
At any given temperature, variable-speed heat pumps have both a maximum and a minimum capacity (“minimum modulation limit”). This allows them to ramp up or down in response to demand. The temperatures at which a heat pump can run continuously and meet the home’s full heating needs define its “Goldilocks range.” Efficiency is maximized by sizing equipment to spend most of its operating hours in this range; the heat pump is small enough to minimize mild-temperature cycling and large enough to minimize the use of expensive resistance heat. This usually means sizing the heat pump to meet around 90% of the design heating load. It also means looking closely at minimum modulation limits, which can vary significantly.
Plotting the extended performance data for the example heat pump above, we can see that at 5°F, it can produce as little as 4200 Btu per hr. and as much as 21,600 Btu per hr.; at 32°F it can modulate between 6750 Btu per hr. and 24,800 Btu per hr.
We can next add a line that shows how much heat a house will need to maintain a stable indoor temperature of 70°F. In this example, let’s say that we calculated that a house needs 25,700 Btu per hr. at its design temperature of 5°F (i.e., its design heat load is 25,700 Btu per hr.). In milder weather, we’ll need less, and once we reach an outdoor temperature of 60°F, we won’t need the heat pump at all; people, lights, and appliances produce enough waste heat to raise the indoor temperature the last few degrees.
In milder weather, the amount of heat needed is less than the minimum output. In these conditions, the heat pump will cycle on and off. As with a car in stop-and-go traffic, this cycling can reduce the heat pump’s efficiency, sometimes as much as 40%. At colder temperatures, the heating demand exceeds the heat pump’s minimum output, and the heat pump can run continuously. At very cold temperatures, the heat pump may no longer be able to make up for the home’s heat loss on its own. Below this balance point, we need supplemental heat, or the temperature in the house will drop. In most of the ducted heat pumps I’ve installed, the supplemental heat is provided by electric resistance heaters inside the air handler itself. If these were the primary heat source, they’d be prohibitively expensive. But, because the resistance heaters operate simultaneously with the heat pump, they only need to make up a small shortfall.
For systems with an air handler and one or more ductless zones, we’ll need to decide whether to use a single multizone outdoor unit or multiple single-zone outdoor units, each serving an air handler or ductless head. A multizone outdoor unit usually has less visual impact. It can also cost less, though the savings are often modest. On the other hand, multiple outdoor units provide redundancy. Because single-zone units have better turndown ratios (i.e., they can modulate down to a smaller fraction of their maximum output), designs that use multiple single-zone units can reduce mild-temperature modulation without sacrificing output at colder temperatures.
Customers sometimes ask what happens if a winter storm or grid failure knocks out power. I remind them that both heat pumps and fossil-fuel furnaces require electricity to run. Some customers opt for generators to keep the heat on in an extended power outage. Others, especially in rural areas, have woodstoves or vented propane heaters that do not require electricity.
Variable-speed heat pumps have minimum and maximum heat outputs; both decrease as temperature drops. Meanwhile, the heating load—the amount of heat required to keep the home at 70°F—increases as the temperature gets colder. The load at the local design temperature (5°F in this example) is the design heating load (1). At mild temperatures (2), the load is below the heat pump’s minimum output, and the heat pump cycles on and off. When the load falls between the minimum and maximum output (3), the heat pump is in the “Goldilocks range,” its sweet spot, where it runs continuously, ramping up or down as needed. When the temperature falls below the balance point (4), the heat pump continues to deliver heat but can no longer meet the full load, and supplemental heat is required (5). Minimizing supplemental heat and mild-temperature cycling are both important considerations when selecting heat pump equipment.
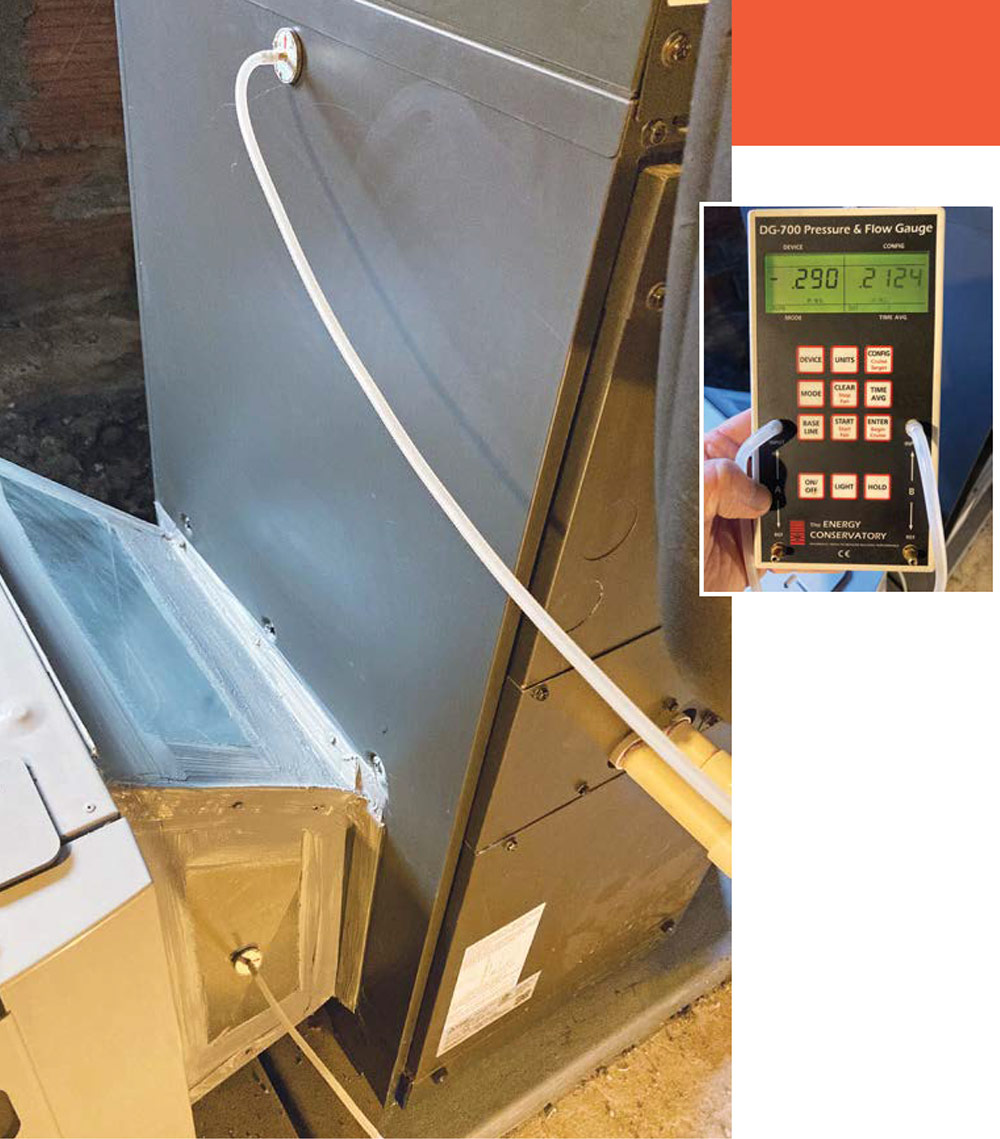
Commissioning is key
In a previous Fine Homebuilding article, I discussed best practices for installing ductless heat pumps (“Critical Details for Ductless Heat Pumps”). Many of the same considerations apply to ducted units: outdoor unit siting and mounting, electrical wiring, and, especially, the importance of properly connecting, leak-testing, and insulating the refrigerant piping.
One of the main differences is that the new air handler needs to be tied into the existing supply and return ductwork. The process, which involves a combination of prefabricated sheet-metal fittings and site-built transitions, provides an opportunity to make improvements. Undersized and poorly designed fittings near the air handler can be replaced with less restrictive ones. A low-resistance, high-efficiency air filter can be installed, and the ductwork can be sealed with mastic. In addition, any ductwork passing through unconditioned attics or vented crawlspaces must be carefully insulated.
Another difference with ducted heat pumps involves provisions for draining condensate, which forms on the indoor coil in cooling mode. The condensate pipes for most air handlers must be trapped to prevent the blower fan from sucking air through the drain. When the air handler is located in or above finished space, an auxiliary drain pan, secondary drain line, or flood detection device (a “wet switch”) is required.
Once the system is up and running, we need to measure its airflow. I use a manometer and static pressure probes to measure the difference in duct pressure between the inlet and outlet of the air handler. I then convert this to cfm using the manufacturer’s charts. I can adjust the fan speed if the airflow is slightly high or low. But if minor adjustments can’t bring the airflow within the recommended range, additional duct modifications may be needed.
Once the system has been tested, installed, and configured, I’ll walk the customers through its operation and maintenance. I’ll also reinforce a few points we covered earlier in the sales process. One is that supply-air temperatures may be cooler than they’re used to. Another is that their new, correctly sized heat pump will run more of the time than their old, oversized furnace. I’ll also remind them that while their electric bills will go up, those increases will be offset by reducing or eliminating their use of fossil fuels.
Drawings: Christopher Mills.
Photos: John Harrod, except where noted.
From Fine Homebuilding #322
RELATED STORIES
To view the entire article, please click the View PDF button below.