Barn Transformation
In this small home remodel, a steel catwalk holds up the roof while opening up the space below.
Once used as a horse barn, farming equipment shed, and workshop, this 1950s structure was sitting on a old pier-and-beam foundation in poor condition, and was constructed of undersized roof trusses holding up a catwalk of “sketchy” plywood. The homeowner wanted to retain the striking catwalk and open up the main space, which required some difficult maneuvering. The barn turned into house was set on a new foundation, insulated, and air-sealed, with a new vented roof assembly over the original board roof sheathing. To save the catwalk and keep the space open, the build team strengthened the catwalk with a steel beam that also carries the roof load, which is now framed with just the top chords of the original trusses.
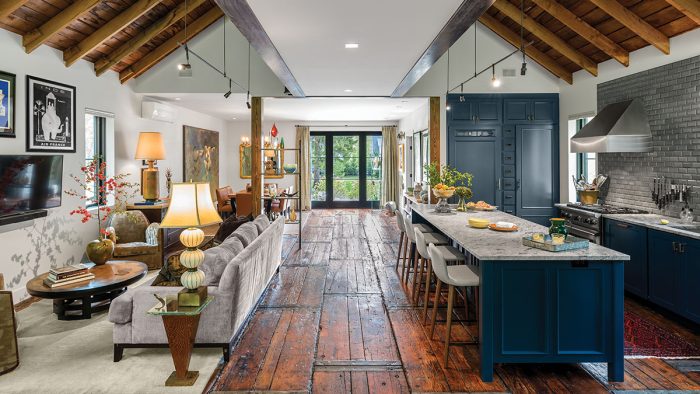
A New Life for an Old Home
Not too long ago, this 1420-sq.-ft. home was a “cobbled together, uninsulated felt paper shack with vinyl siding and trim,” according to builder Reggie Lebel. Today, it is a laudable example of preservation and adaptive reuse.
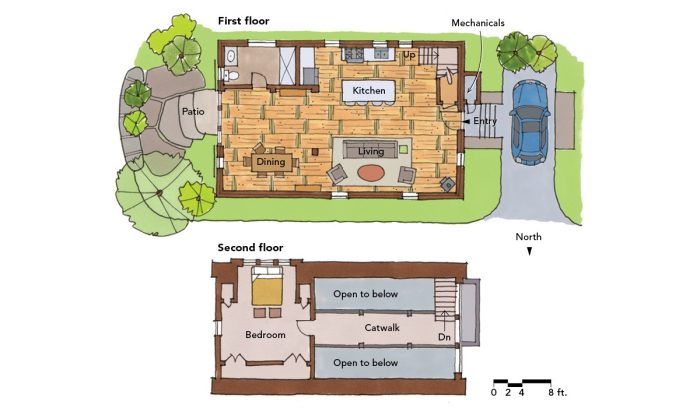
The homeowner, Stephen Peck, commissioned Briburn Architects to redesign an underutilized outbuilding, circa-1950s, that had been used over the decades for various purposes including as a horse barn, farming equipment shed, boat repair shop, and, most recently, general workshop. He wanted to turn the weatherbeaten, bare-bones structure into a high-performance home. When architect Chris Briley came on board, he faced what he’s since described as “a single room with a rickety old staircase connected to a loft by a ‘catwalk’ of sketchy plywood laid on the trusses.”
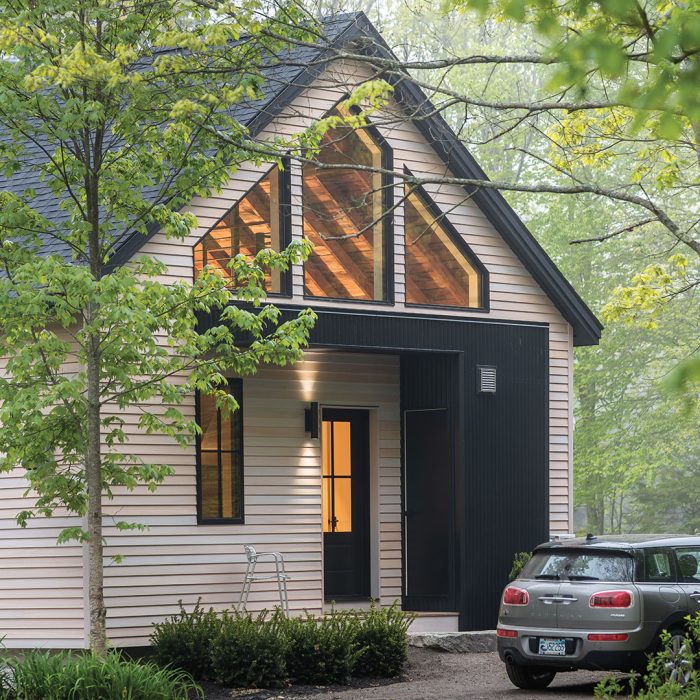
Maintaining the building shape and scale of details were among the design objectives; doing so would satisfy the homeowner’s larger goal to create a home befit for its generations-old, quintessential New England neighborhood in Falmouth, Maine. As an interior designer and art lover, Stephen also wanted to add some contemporary flair. He had a crystal-clear vision of what he wanted. It was up to Briburn and Emerald Builders to make it materialize.
“Most people would have torn down this old barn to make way for a new structure,” says Chris. “But Stephen was enchanted by its features, especially the catwalk and the floor made from World War II Liberty ship hatches. He wanted to honor the past by keeping such features, honor the present by making a comfortable, modern place for him and his husband to live, and honor the future by turning the drafty old barn into a highly energy-efficient, sustainable building.”
The scope of the work was colossal. The foundation was in poor condition and needed to be replaced. The roof structure consisted of undersized, sagging, site-built trusses surrounding the aforementioned “sketchy” catwalk. The solution was to use a new catwalk structure to support the roof framing, removing all but the top chord of the trusses to open up the space. The building was also set onto a new foundation, and a new roof assembly was built over the old board roof sheathing.
In the end, the homeowner’s vision for a capsule worthy of its contents has come to fruition. Chances are good it will be standing in another 100 years, and the folks who come upon it can add “home to art lovers” to its history.
Holding Up the Roof While Opening Up the Room
The original site-built roof trusses were undersized and had a significant sag; plus, they created a visually dizzying interior space that the homeowner wanted cleared. The catwalk was similarly underbuilt—but the catwalk was part of what sold the owner on the building. So the trusses had to go, and the catwalk had to stay.
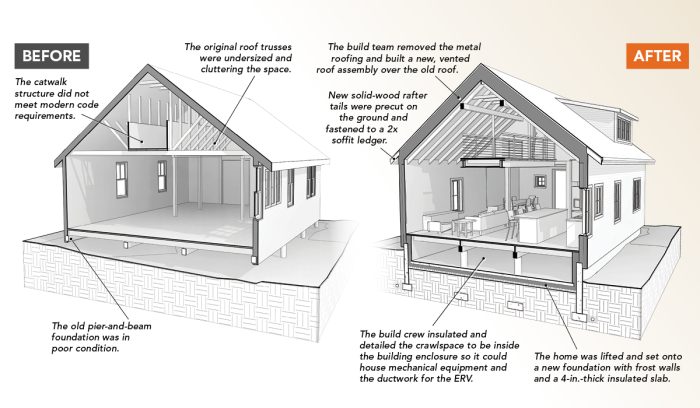
The solution was to use the new catwalk structure to support the roof framing. The first big move was to support and jack the top cord of the trusses, while also plumbing the exterior walls. The crew built a support and jacking system by installing temporary beams at the midspan of the top cord with posting locations that fit through the existing trusses of the roof structure.
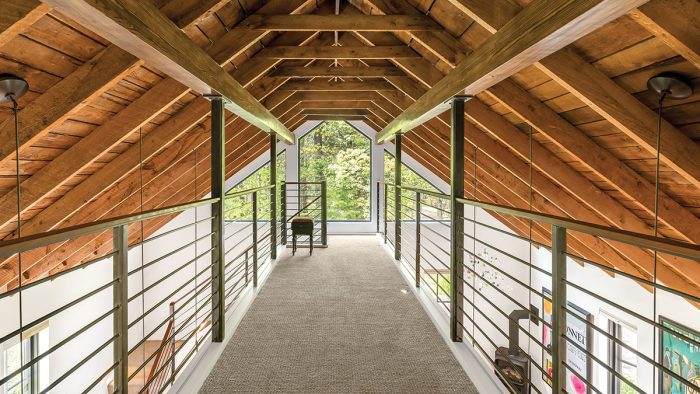
As they jacked the sag out of the roof, they used turnbuckle bracing on the walls to pull and push them straight and as plumb as they would go. Using the temporary beam as a top plate, they built a braced temporary wall from floor to ceiling so that they could then remove the truss webs and bottom cords, leaving the top cords as rafters. The crew had to do all of this work without damaging the structure’s “patina”—the aged look the homeowner was keen to retain.
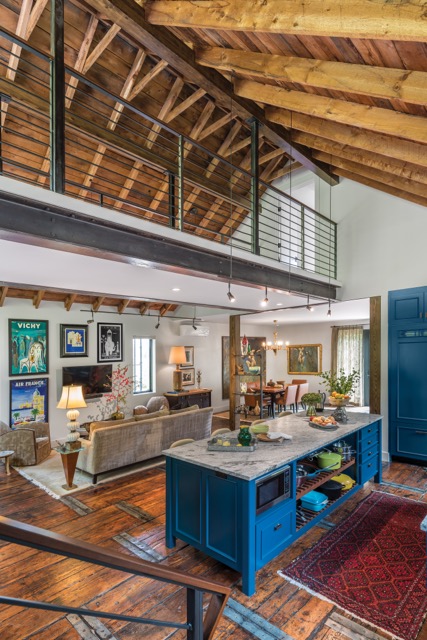
Two 24-ft.-long steel I-beams were installed for the catwalk structure, supported by timber posts that have a load path to footings under the slab. Two new laminated wood beams on either side of the ridge were let into the rafters with the use of birdsmouth cuts; the beams break the span of the rafters and are supported by steel posts that drop to the I-beams, making the catwalk the new structure for carrying the roof load. In one section of the roof, the bottom chords of the trusses were replaced with new floor joists for a new loft bedroom.
Getting 1000-lb. prefinished steel I-beams into the house and installed was a big challenge. To get the job done, the team fed the new beams in through the existing gable doors with a telehandler and carts on the first floor. Then they removed two panels of the existing metal roof and carefully cut out roof-sheathing boards to create access holes for the lifting straps used by the telehandler outside to lift the beams into place. (They cut the sheathing where it passed over the existing rafters so that the cuts wouldn’t be visible on the inside when the pieces were reassembled.)
Handling the beams’ massive weight while protecting all finishes from damage was a test of patience. The inside crew communicated with the operator outside via cell phones and headsets. “The process was exciting, tedious, and nerve-wracking all at the same time,” builder Reggie Lebel recalls. “It was like playing a really big, high-stakes game of Operation.”
This construction nail-biter is now one of the home’s most arresting features. The steel beams anchor the volume both physically and visually. Together with the new wood beams and preserved rafters and board sheathing, they contribute to a solid new building shell and the homeowner’s desired milieu.
— Kiley Jacques; senior editor at Green Building Advisor. Photos by Francois Gagne.
From Fine Homebuilding #324
RELATED STORIES
- Transforming an Old Barn Into a Modern One
- A Barn Reborn
- Renovation of an Old Barn Into a Modern High-Performance Home
Fine Homebuilding Recommended Products
Fine Homebuilding receives a commission for items purchased through links on this site, including Amazon Associates and other affiliate advertising programs.
Graphic Guide to Frame Construction
Not So Big House
A Field Guide to American Houses