A Tale of Two Energy Audits
How the work of a home-performance professional can result in a path toward improved energy efficiency, durability, and health.
Building scientist Monica Rokicki walks through the process of an energy audit using two case studies as examples. She discusses moving from pre-site-visit assumptions to on-site testing with infrared cameras and blower doors, tracking energy usage, and inspecting insulation and ductwork. Using energy modeling leads to a detailed audit that includes a report of recommended improvements along with potential return on investment. The article also includes a list of 10 common energy-retrofit mistakes to avoid.
What is an Energy Audit
Ask ten homeowners what the term “energy audit” means and you might get ten different answers. Many are surprised to learn that it is a legally defined term, with building science–based, national standards that emphasize building durability, comfort, and air quality as much as they focus on ways to reduce energy usage. A qualified energy auditor is an experienced, interdisciplinary building scientist. The most recognized certifications for home energy auditors include the Department of Energy’s Home Energy Rating System, for HERS rater certification, which focuses on new homes, and the Building Performance Association (BPI) certifications, which focus on performance diagnostics in existing homes.
Both perspectives are valuable, because no matter how new a home is, the day after the certificate of occupancy is issued, it’s an existing home, with particular conditions based on its climate zone, site, builder and subcontractors, owners, occupants, weather patterns, and more. For this reason, every energy audit will yield different recommendations. The result of a comprehensive energy audit is a road map for the homeowner, and recommendations are not limited to energy efficiency. They may also include corresponding indoor air quality improvements, suggestions for air monitors, projected dates for major equipment or appliance replacement, and coordination with other relevant home improvement projects.
Energy efficiency upgrades are typically also assigned a return on investment because the avoided cost of future energy use can pay for the improvements over time (they may be offset by available incentives or tax credits as well). At my Roanoke, Va., building science firm, Better Building Works, we also include a best-fit feasibility analysis for renewable energy, electrification, and electric vehicle charging, as well as a net-zero-energy plan, in our audits. In this article I plan to show what a comprehensive energy audit looks like for two different homes, and how the recommendations are similar or different depending upon the owners’ objectives and on-site conditions. Both homes are in our tricky mixed-humid climate zone, and both audits were completed in the fall of 2023.
Expectations and Assumptions
One of the first things we do is make sure to orient the audit process to address the homeowner’s objectives and needs. This means making sure we understand why the homeowner wants an energy audit, and asking them some basic questions, such as how long have they lived in the house, and how long do they plan to live there? We also like to know as much as possible about the history of the house. In the case of these two audits, here’s what we knew getting started.
The Mugford residence, built around 1900, is a Victorian home in a historic district. This home experienced a full gut rehabilitation in 2007 as part of a City of Roanoke initiative and was renovated to Energy Star standards at that time. The current owners purchased it in 2019. They are the second owners of the home since the renovation and recently remodeled the basement to add a TV room and shop. While the home is mostly occupied by the two of them and a small dog, they often host their children’s families for holidays. Their objective is to increase energy efficiency and indoor air quality.
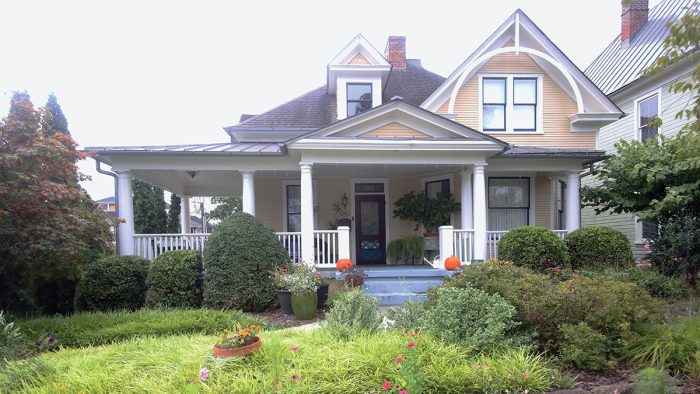
The Weitzenfeld house is a brick American Foursquare built in 1928. This home has had five prior owners. The current owner purchased the home in the summer of 2023. It will be occupied by two people and a large dog. The owner wants to sustainably improve the building’s energy efficiency, upgrade the kitchen, add a first-floor bathroom, and upgrade the heating and cooling system.
When starting an audit, we also want to know what the client’s energy bills can tell us. We complete an energy model after the on-site work is complete, but when actual energy use is available in advance, analysis gives us insight into how the building has been performing. This can help us identify anomalies and how energy use changes over the seasons. The lowest monthly usage (usually in spring or fall) helps us quantify energy use not driven by heating and cooling, called “base load.”
Finally, before we arrive, we try to state some of our assumptions. This helps us to not be stuck in our preconceptions as we gather more information. In this case, both homes have a basement and two occupied, conditioned levels above grade. Both have relatively large, vented attics with steep roofs. Both homes use gas and electric energy. And both homes will be similarly occupied.
We assumed that the Mugford residence would be well-insulated with a fairly tight building enclosure. There would still be significant air leakage where the upper level overhangs exterior space. Our recommendations for improvement would likely be minimal. Even though the basement is conditioned, annual seasonal energy use would be lower than the Weitzenfeld residence.
The Weitzenfeld Residence has no crawlspace, according to the owner, and the basement is unconditioned. We assumed the blower-door test would show that the home is very leaky. Annual energy use would be very high compared to the Mugford home.
Interestingly, we started to question these assumptions before even visiting the houses when we noticed that the summer energy use at the Weitzenfeld home had been surprisingly low (we had energy bills from the previous homeowner). We had to ask: Since energy usage data is from before the new owners purchased the home, is it still representative? Why is it so low in the summer? If there is no cooling system driving energy usage, are these months showing the true base load?
First, Some Observations
It’s now time for the on-site audit, which typically takes us between two and four hours. Upon arrival, our first step is to set up some basic air monitors for CO and CO2, along with temperature, humidity, and particulate matter. Then we ask the owners to give us a tour of the house. During this time, we often hear some new information about the home and their plans. And we are also creating a mental map of the home’s conditioned building enclosure, which will be documented with conventional photography, notes, and infrared thermography.
Our assumptions continued to be tested. For the Mugford home, it appeared that the kneewall attic spaces on the upper level and the main attic were not well-sealed. We could see that the basement workshop, which produces a large amount of particulate matter, was at least partially connected to the basement living area and first-floor level above. We also discovered a part of the basement that was formerly a crawlspace, and now has a concrete floor that we were unaware of.
At the Weitzenfeld home, we could easily observe that the unconditioned basement and attic both had many unsealed penetrations into the conditioned space, and that there was virtually no insulation between the basement and the first floor. We also learned that the previous homeowner used the existing fireplace for supplemental heat during the winter, and rarely used window-mounted air conditioning in the summer.
This explained the low summertime energy use, and alerted us that winter energy use, while high, would have been even higher without the use of the fireplace. The new owner planned to install central air conditioning and remove the window units. We learned more about the plan to remodel the kitchen and the challenge of routing plumbing and electrical into an area destined to be a small bathroom and pantry, which is adjacent to the back porch.
We also observed a dehumidifier in the basement, and the owner told us that the space is often over 70% relative humidity. There were signs of efflorescence and wetting at the lower side of basement walls. Because the floors showed little evidence of wetting, and the gutters and downspouts were clear and routed to direct liquid water away from the home, we suspected that high humidity levels were the result of air infiltration.
The next step is to record exterior and interior surfaces and materials, and identify potential areas of energy, water, or air leakage. At this time, we also record all equipment model numbers and fuel sources, especially for HVAC compressors and air handlers, furnaces or boilers, water heaters, and major appliances. Later, we’ll look these up to verify age, efficiency, and other details about the equipment. We also note all accessible areas where we can see insulation. We look at venting, grading, and neighboring conditions, and identify any areas of water infiltration.
Whenever there is open-combustion equipment inside of the building enclosure, we do combustion-area zone testing to alert the building owner of any unhealthy or dangerous conditions that can result in back-drafting. Even when that testing is not completed, we look for and identify all combustion equipment. At the Weitzenfeld home we identified an antique gas stove (with no ventilation hood) and a wood-burning fireplace. Both can be sources of indoor air pollutants.
Most concerning, however, was the old open-draft boiler, its rusty exhaust-vent piping, and its use of an existing chimney, which is rarely a good idea (note that the clothes dryer—an exhaust fan that exerts around 250 cfm of negative pressure—is nearby). The rusted areas on the vent and boiler were indications of back-drafting because water vapor is a component of combustion air.
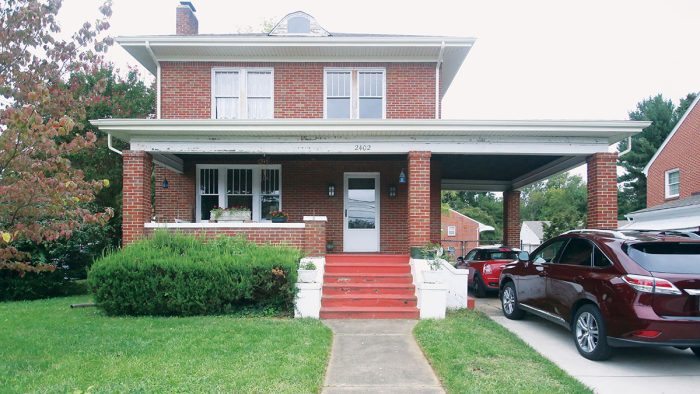
Staining indicated that this had been occurring for some time. Since the floor above had so many penetrations, combustion air was undoubtedly entering the living areas. During our energy audits we try to imagine—or ideally, test—the home under a condition we call “family reunion at the winter holiday.” What would happen if every bath exhaust, stove exhaust, and dryer were running at the same time as the fireplace is burning, the furnace is on, someone is taking a hot shower, and dinner is cooking on the stove? At the Weitzenfeld home, we’d be concerned.
What about the Mugford’s Energy Star home? While there is also combustion equipment at the Mugford home, there are fewer causes for concern. There is a gas furnace serving the basement and first floor, but it is a direct-vent unit, which is much safer than an atmospherically vented furnace. There is a gas stove too, but it has an exhaust fan that vents to the exterior. We were happy to see no unvented gas fireplace, which is quite common in the Victorian-era homes in this area.
Next, an Infrared Inspection
The first round of infrared thermography occurs at this stage, prior to the blower-door tests. We typically only complete infrareds at the interior, with particular focus on specific areas including the wall-to-floor and wall-to-ceiling intersections, ceilings, and doors or access hatches to unconditioned areas. At this stage, there is little pressure difference between inside and outside, so the infrared camera is usually picking up temperature difference driven by thermal barriers, but we sometimes also discover areas where water leaks have occurred, which will typically have a blob-like appearance.
Discoveries often have a silver lining. At the Weitzenfeld property, we noticed an odd metal plate in the basement wall. Infrared thermography revealed that this area was a heat bypass. Around the area, we also found efflorescence, an indication of long-term moisture infiltration. When we removed the plate, we found a small crawlspace with bare earth and no insulation. The good news is that once this space is remedied, it will offer a place for plumbing and electrical runs to the future guest bathroom.
Another silver lining at the Weitzenfeld property was in the walk-up attic, which is very leaky, especially at the attic door, chimney, and top plates of exterior walls. The owner had installed an attic fan after reading some online advice to do so. All of these things conspired together to exacerbate the stack effect, causing high winter energy bills. Fortunately, there was no mechanical equipment in the attic, so there was an opportunity to solve these energy issues and also gain an additional finished room in the attic.
There were also some interesting conditions in the Mugford basement and attic. The workshop was equipped with an air-filtration device to remove particulates created by woodworking, and it had its own stand-alone heating system. But there were multiple air bypasses into the adjoining TV room and mechanical closet that housed the air handler. Leaky ductwork throughout these areas could spread this particulate matter to the main levels of the house even more efficiently than air leakage.
Kneewall attics are a common feature of existing homes. Despite builder’s attempts to keep kneewall attics outside the air and thermal boundary, when they are poorly insulated and air-sealed, they are essentially being conditioned, which is a big waste of energy. In the Mugford residence, this air-sealing and insulation work was incomplete at the second-floor kneewalls. We observed similar discontinuities in air-sealing and insulation in the main, vented attic. A second heat-pump system and associated ductwork was in this attic, essentially operating outside, resulting in lower efficiency and the same air quality issues described in the workshop. In this case, it was potentially distributing unconditioned air, moisture, and dust from the attic into the house. There was minimal insulation, as well as wind-washing, making the actual insulation value around 25% less than the recorded R-value.
While we are investigating a home with infrared thermography, we also record interior thermostat settings and collect the data from our air monitors. We’ll later compare these ambient levels of CO and CO2, air temperature and relative humidity, and particulate matter after blower-door testing—if they are higher or lower, we can learn about indoor air pollutants and ventilation.
Blower-Door Time
We’ve learned that we can’t predict building tightness. And because knowing the accurate building tightness of a home is critical to proper heating and cooling equipment sizing, ventilation sizing, and determining air-sealing recommendations, we test airtightness with a blower door. With an accurate measurement for the house, we can estimate the total amount of air infiltration that regularly occurs in the home, known as “ACH natural.” It is also important to know where the air leakage is occurring. This is where the second round of infrared thermography comes in. With the blower door pressurizing the house, the infrared camera will detect the leaks.
The airtightness results are even more helpful when viewed in relation to the volume of the conditioned building enclosure. For a new home where the conditioned building enclosure is defined and continuous, we do one blower-door test. For existing homes, when we have areas that are thought of as outside of the conditioned building enclosure but are functionally inside of it, like the Weitzenfeld basement, or the Mugford kneewall attics, we run multiple scenarios.
At the Weitzenfeld home, we completed four tests: one with basement and attic doors closed, one with the basement door closed and the attic open, one with the basement door open and attic door closed, and one with both the basement and attic doors open. This accomplishes a few goals. First, it tells us how much air leakage a closed door prevents. Second, it guides decision-making regarding recommended improvements in these areas. Here, we found that the difference in leakage to the attic was about six times that of leakage to the basement. Does this mean that improvements to the attic are more important? Not necessarily. The floor between the basement and the main level is wood that will shrink and swell, and there are many gaps in the boards. The lower difference when the basement door is closed versus the attic indicates that the basement and main level are less separated. The ceilings between the upper level and the attic are plaster—an effective air barrier. We concluded that the attic door was the primary source of leakage, along with the unsealed gaps around the chimney, stair walls, plumbing and electrical penetrations, and eaves. We also look at air-quality monitors to see if CO2, particulate matter, temperature, or humidity has changed as a result of bringing air across exterior building penetrations. In the Weitzenfeld home, there was little to no difference, other than a slight dilution in particulate matter. The CO2 level was unchanged and low, consistent with the high amount of air changes we found in our tests.
At the Mugford home, we also completed four tests. The attic, accessed through a pull-down stair, remained closed except for maintenance, so was left in that state. Instead, we tested various open and closed configurations of the kneewall attics and basement door. The blower-door tests indicated very little difference with the basement door open or closed, which we expected as these two areas are both finished and conditioned. The kneewall attics were another story. These areas were very leaky, as was the pull-down stair access to the main attic.
Air-monitoring-equipment differences before and after blower-door testing indicated that particulate levels went up after the test. This verified our hunch that particulates from the workshop were entering the conditioned building enclosure. But CO2 levels went down. Again, this is consistent with most blower-door testing, which is moving air and exhausting or diluting CO2 levels.
Now We Model
After the site visit and once we have all the data, documentation, and numerical calculations together, we complete an asset-basis energy model. This model predicts energy usage for the home with its existing attributes (location, area, volume, fuel types, windows and doors, effective insulation values, equipment and appliance types and efficiencies, and airtightness). It is always completed as if the home is fully occupied for the full year. The results usually vary from the actual utility usage because of several factors including occupancy and homeowner behaviors. But the energy model is still useful, and it is required for underwriting, risk management, and big-data aggregating institutions like insurance companies, banks, and the Department of Energy. This means it can be leveraged at the point of refinancing or sale. And it is also quite valuable to predict proportional savings from potential upgrades, a requirement of any certified home energy audit.
The energy model can be used to discover the optimal combination of energy conservation measures. If any remodeling is planned, this type of energy model can be used to run scenarios, or to estimate the impacts of measures like incorporating a basement or attic into the conditioned building enclosure.
For most existing homes, we use Energy Design Systems’ software because it also completes a heating and cooling load calculation. We also use NREL’s PVWatts calculator and on-site observation to complete a feasibility analysis for solar photovoltaics. Occasionally, we complete energy audits for homes as the first step of a design process for significant remodels or renovations. In this case, a HERS rating, using more detailed Ekotrope modeling, can be completed and used to apply for Energy Star certification.
Recommendations Aren’t the End
After energy modeling, we roll all of our data up into a set of recommendations. Final recommendations always begin with durability, safety, and indoor air quality. Enclosure improvements are next, and only then do we recommend equipment and appliance upgrades. Improvements are typically given in phases, depending on the owner’s plans for the home. These projects had some recommendations in common (each house also had unique recommendations; see below).
For both homes, we recommended low-ppm CO detectors at each level and a continuous radon monitor. These CO monitors will alert the homeowners to turn off combustion equipment if levels begin to rise. And if continuous radon levels over 2 pC/l are found, they’ll know they need to install a radon mitigation system. We recommended the homeowners replace existing gas stoves with induction ranges. Until then at the Weitzenfeld home, since the existing stove will be difficult to vent to the exterior, and the short-term expense may not be in the budget, we recommend opening a window or door when cooking.
After all recommended air-sealing and insulation is completed, we recommended each home have a new blower-door test followed by proper ventilation calculations, and Manual J heating and cooling load calculations. This is the only way to accurately size HVAC equipment, including balanced ventilation. When it’s time to upgrade the water heater, we recommended a heat-pump unit.
When the report is presented to the homeowner, we explain our reasons for each prioritized recommendation, and how the right combination of energy efficiency, electrification, and renewables can yield the highest return on investment. While the energy audit is the best first step, the process does not stop here. For the best outcomes, we can now provide valuable retrofit project management and verify that work is completed to performance specifications. This will allow us to revisit HVAC equipment sizing and produce a revised energy model for appraisers, potentially increasing a property’s value.
The Mugford House Energy Improvements
This circa-1900 Victorian home received Energy Star certification nearly 20 years ago during a significant remodeling project. The current homeowners are hoping to improve energy efficiency and indoor air quality in the home. Even though this home had been remodeled in this century, it had some common issues that we verified with a thermal imaging camera, a blower-door test, and indoor air quality monitors.
First, we look around. Some issues are easy to spot with a visual inspection, like a lack of air-sealing and poor insulation at the rim joist. We will often verify this with a combination of blower-door testing and thermal imaging.
Energy Use Snapshot
From this chart, we can see that the winter heating season accounts for about 50% of total average annual energy use, particularly January. Summer cooling energy usage was nearly as high in August as in December. Spring and fall usage is a little higher that we typically see, as well. Base load is relatively easy to estimate from the lowest-energy-use month of November, and it is likely that the workshop is contributing to a higher base load than average in this home.
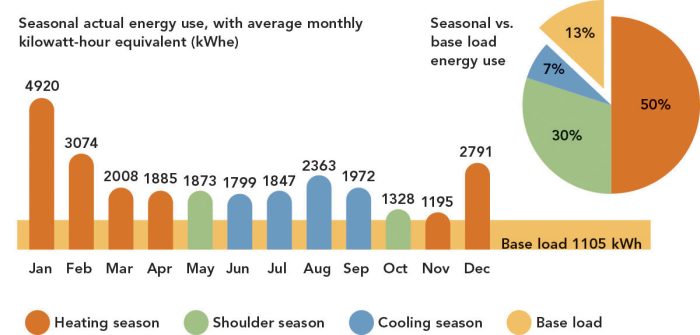
![]() |
![]() |
![]() |
Fan flow is measurable. Exhaust fans in kitchens and bathrooms play an important role in healthy indoor air quality. We try to visually verify that exhaust fans are ducted to the exterior before doing a fan-flow test to verify that the fans are moving an appropriate cfm for the space.
Recommendations
From a health perspective, the most significant issue in this house was that particulate matter from the workshop and attic was traveling into the conditioned living space. Our suggested energy improvements were common air-sealing and insulation improvements at the rim joist, in the kneewall attics, and in the main attic:
- Thoroughly air-seal all rim joists and the penetrations between the workshop and the adjacent basement mechanical and TV room.
- Clean and seal all ductwork, particularly the duct system serving the basement and first floor.
- Relocate the air and thermal barrier in the kneewall attics and in the main attic to the underside of the roof sheathing, bringing these areas and the existing heating and cooling equipment into the conditioned building enclosure.
![]() |
![]() |
Infrared insights. With the infrared camera, we scan the exterior walls, particularly where they meet the floors and ceiling, and we verify issues, like leaky and uninsulated kneewall attics and attic hatches. Photos courtesy of Rodney Diaz.
Potential Return on Investment: 8.3%
This assumes a $12,400 budget with a $1350 tax credit for the homeowners, and a 20% predicted efficiency improvement. The ROI will likely be closer to 10% if energy-cost escalations are included. Another way to look at it: The avoided energy costs over ten years will be $11,047.
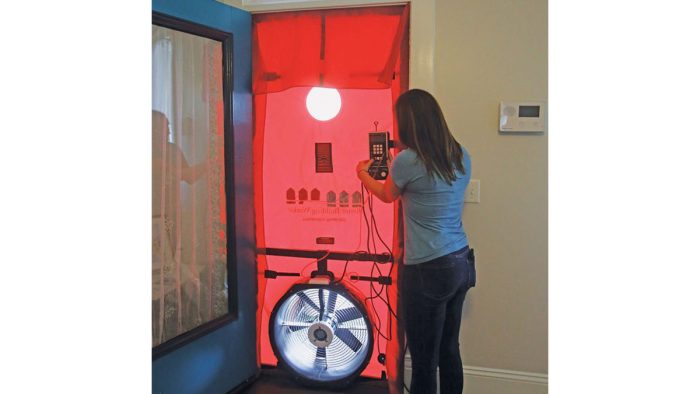
The Weitzenfeld House Upgrade Options
The new owner of this 1928 Foursquare is planning to remodel and take the opportunity to improve the building’s energy efficiency, while upgrading the kitchen, adding a bathroom, and installing new HVAC equipment. The new owner of this home hopes to improve the house by reducing energy use and improving indoor air quality, and by remodeling the kitchen, adding a first-floor bathroom, and potentially converting the walk-up attic to living space.
![]() |
![]() |
Energy Use Snapshot
From this chart, we can see that winter heating season usage dominates the energy use, and is 66% of total annual average energy use (this data was collected from the previous owner). The very low summer cooling energy usage is puzzling, however. We typically see cooling season usage higher than the spring or fall swing seasons. Base load for the former homeowner may be lower than it will be for the current homeowner, particularly if the new owner uses window-mounted air conditioners or installs new heat pumps and uses them for cooling.
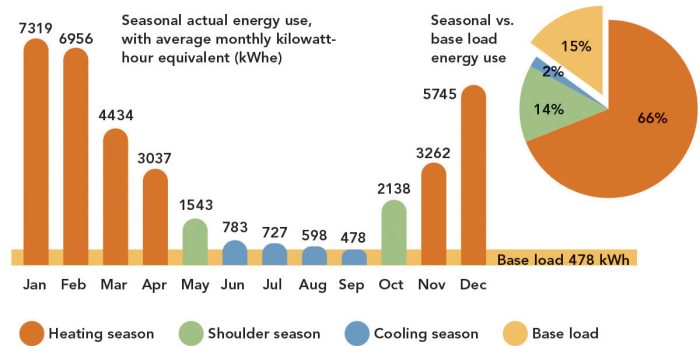
![]() |
![]() |
Recommendations
In this house, our recommendations were more thorough and included replacing combustion appliances and HVAC equipment, and completing air-sealing and insulation work in the basement and attic:
- Replace the bathroom exhaust fan and ducting to the exterior.
- Replace the wood-burning fireplace with a direct-vent gas stove, or better, decommission the chimney.
- Install a sealed vapor retarder in the crawlspace. Remove the access panel. Create a closed, conditioned crawlspace that’s connected to the basement.
- Decommission and remove the existing boiler and venting.
- Bring the crawlspace and basement into the conditioned building enclosure by air-sealing and insulating the band joist; consider insulating exterior walls.
- Bring the attic into the conditioned building enclosure and remove the attic fan.
- Install two Energy Star–rated heat pumps, appropriately sized. One will serve the basement and first floor, and the other will serve the upper floor and attic.
![]() |
![]() |
Potential Return on Investment: 10.9%
This assumes an $11,000 budget with a $1350 tax credit for the homeowner and a 30% predicted efficiency improvement. The ROI will likely be closer to 13% if energy-cost escalations are included. Another way to look at it: The avoided energy costs over ten years will be $12,590.
— Monica Rokicki; designer, building scientist, and founder and CEO of Better Building Works LLC in Roanoke, Va. Photos by Brian Pontolilo, except where noted.
From Fine Homebuilding #324
RELATED STORIES
- Energy Savings Begin with a Home-Energy Audit
- What Is a Home Energy Audit?
- An Energy Auditor’s Toolkit
- Every House Needs an Energy Audit
Fine Homebuilding Recommended Products
Fine Homebuilding receives a commission for items purchased through links on this site, including Amazon Associates and other affiliate advertising programs.
Handy Heat Gun
Affordable IR Camera
8067 All-Weather Flashing Tape