Podcast Episode 638: Moldy Houses, Construction Careers, and Building on a Mesa
Listeners write in about changing careers, rainscreen raised beds, and introducing people to trade work. They ask questions about buying a moldy house, choosing construction as a career, and building on a sandstone mesa.
Follow the Fine Homebuilding Podcast on your favorite app. Subscribe now and don’t miss an episode.
Note: The Fine Homebuilding Podcast team is always looking for ways to improve, so we’re switching up our video strategy. But don’t worry—you’ll still be able to watch all your favorite clips from the show. Check out our YouTube channel or keep scrolling to see more!
![]() |
![]() |
![]() |
Paul says some construction careers are easier than others. Barbara D shows us her revamped raised beds. Thomas asks for an episode dedicated to career changes. Mason has big news. Matthew tried to buy a moldy house. Sydney is considering a construction career. John wants to build on solid sandstone.
Check in:
Mike: Castoff mowers
Brian: Lawn-to-pasture conversion
Andres: Considering gravel mulch
Patrick: New Panasonic bath fan
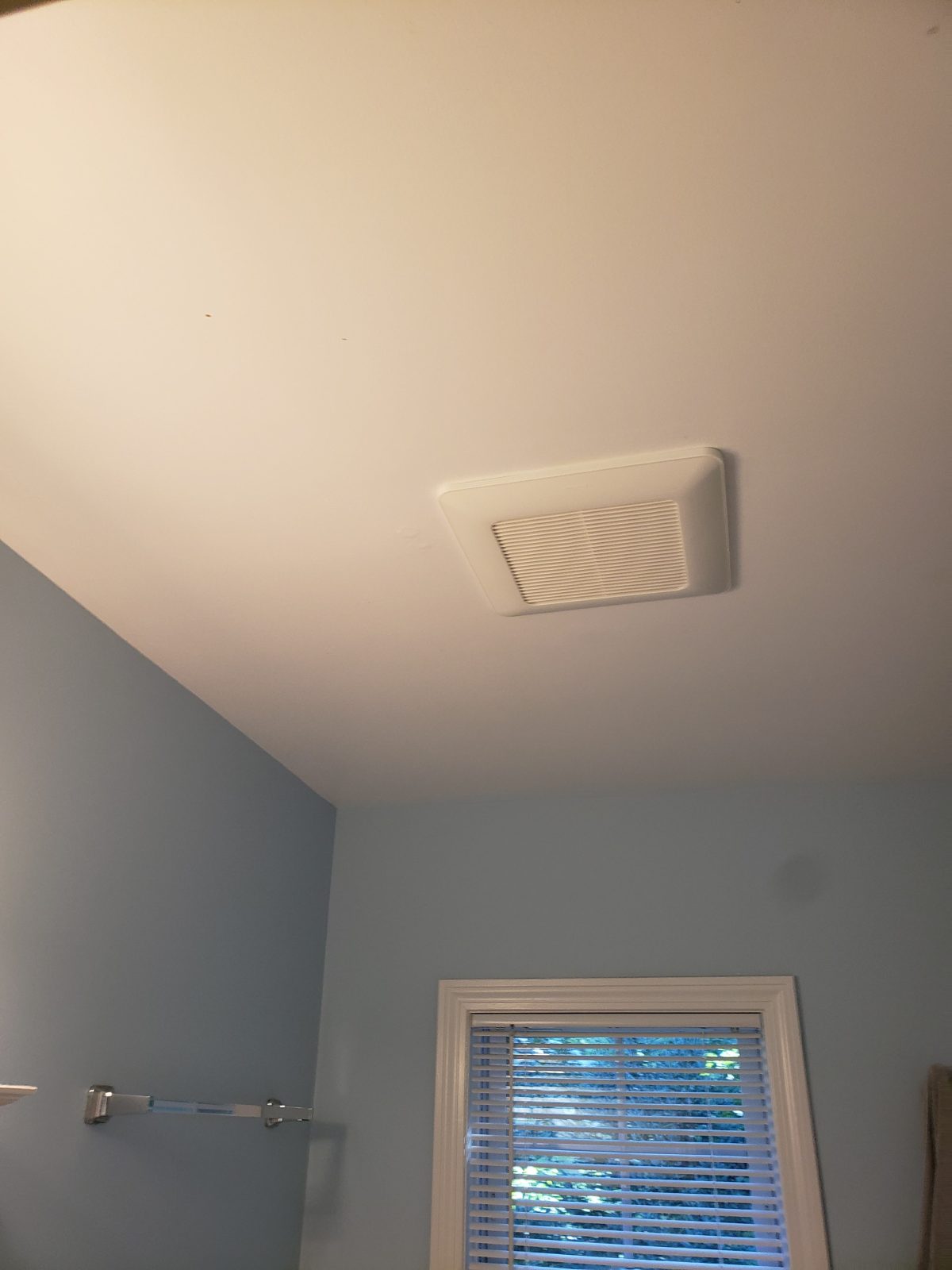
Listener Feedback 1:
Paul from Central California writes:
Hi Patrick and crew,
In a recent podcast, a listener wrote in seeking advice on entering a new career in construction in his 50s. I’ve known a couple middle-aged career-changers like that. After the first day, they couldn’t move, and then things really got bad. A career in the trades is demanding, even for 20-year-olds. The topic comes up regularly, so it deserves more discussion.
My father worked in construction until his death at age 69. He was a finish carpenter who showed up every day, despite his bad heart, bad back, and insulin-dependent diabetes. It was hard on him, obviously, but he loved what he did. He claimed, in fact, that the hard physical work was what kept him alive far longer than any of his doctors expected.
He had a college degree in engineering, yet never considered doing anything but construction. My grandfather also worked in construction well into his 80s. My uncle worked into his 70s. They didn’t work as hard in later years, but they still worked. So the idea that construction must only be for the young doesn’t have to be true.
While construction will never be easy work, there are some trades that are easier than others. Finish carpentry, for example, was a great fit for my dad. After all, trim is a lot lighter than, say, granite countertops. Electricians also have an easier time. Cabinet installers, window installers, and shower installers also bear a lighter load, and have lower barriers to entry as well.
Any career-changer in a professional setting expects hard questions in an interview. “What is it about this particular job that interests you?” “Do you understand what we do here?” The point is to keep someone from making a bad decision. Interviews aren’t rigorous in the construction world, so career-changers need to ask themselves such questions.
If you’re applying for an entry-level concrete job, for example, do you understand that you’re going to push an extremely heavy chute around the pad while slogging through very heavy wet concrete for 10 hours a day? That work is so hard that very few can handle it, even in the prime of life. At 50, you could end up in the ER after a week of it.
Do your research, but if you’re lazy, there’s an easier path. Just spend your next two weeks of vacation re-roofing your house. If you are still excited about construction after pulling the old roof off; cleaning up the yard; making 90 trips up the ladder carrying bundles of shingles, sheets of OSB, and rolls of tar paper; bending over all day to drive cap nails; and more, then it’s probably a good fit for you.
If you collapse in a heap after the second day and call someone else to finish, then you’ll have learned something very valuable, without ruining your life. You can substitute any heavy construction project you want, but make sure you put in 8-10 hours of hustle a day, under a time crunch, preferably while someone questions you incessantly whether you’ll be done before the next sub shows up. Because that’s construction.
Hope that helps someone. Thanks for all you do.
Paul
Listener Feedback 2:
Barbara D. from Sacramento writes:
Hi everyone,
As a dedicated podcast learner every Friday, I carried the concept of rainscreens into my garden this week. In an effort to give my new three-tiered raised garden beds the longest life possible, I first coated the bare pine boards with Thompson’s WaterSeal. But then I decided to go one step further. Voila! Internal rainscreens between the wood and the landscape fabric. The material is a very inexpensive plastic fencing material, double-layered because the holes were so large and also to increase the thickness of the air cavity. Air will enter at the edges of the bottom layer. Thought y’all would enjoy seeing this (photo above).
All the best,
Barbara D.
RELATED STORIES
Listener Feedback 3:
Thomas writes:
Hey FHB hosts!
I’m a mid-career construction manager in a market segment other than home building (the segment rhymes with “toad and fridge” or “drivel production”). I want to pivot my career over the next few years to incorporate more high-performance building systems and beautiful design, but I suffer from APS—analysis paralysis syndrome.
Could you consider an episode or a series of episodes diving into some of the jobs, careers, and vocations that are burgeoning with thanks to the advances in building science? Or more feature episodes of innovators (and normal people) making waves and wavelets in the industry?
I wouldn’t expect to get something for nothing, so here’s my attempt at throwing you guys a lead that might be a bit outside the FHB wheelhouse: Do you know of Elora Hardy of IBUKA (a sustainable design and architecture firm?
I really look forward to your show every week. Thanks for helping to keep craft alive!
RELATED STORIES
Listener Feedback 4:
Mason Lord writes:
Friends,
We have news to share!
“Touch a Trade” is now TradesUp, a nonprofit focused on sharing the joy of hands-on work, uplifting the future of the trades, and passing along skills that span generations.
Our fall event will now be called SPARK by TradesUp, and it is expanding to Martha’s Vineyard. During the past year, we’ve developed the new brand, secured the tradesup.org URL, attained nonprofit 501c3 status, forged an affiliate-type partnership with the Martha’s Vineyard Builders Association, and worked with nonprofit experts to begin to chart our approach to fundraising.
There’s been a lot happening, and I’m thrilled to have these organizational elements in place as we head into workshop and event season.
I want to thank you for your interest in our journey so far. In just two years, our volunteers, sponsors, and presenters have helped pass along the joy of the trades to more than 500 young people in our community. And we’re just getting started!
I especially want to acknowledge the trades and craftspeople that have contributed to making our events so successful. Please let us know if you might be interested in helping for our events in Kent or Martha’s Vineyard. Otherwise, please share our news with others.
Thank you again.
Mason Lord
Hudson Valley Preservation
TradesUp events this year:
- SPARK Kent: October 12, 2024, at the Sloane Museum and CAMA
- SPARK Martha’s Vineyard: October 26, 2024, at the Agricultural Hall.
Question 1: What can be done about a house built inches over dirt without a vapor barrier?
Matthew in Cleveland writes:
Hi Guys,
I have a question that might not be quite what you guys are used to, but it’s something I came across that has been really bothering me. I’m a project manager for a custom builder in the Cleveland, Ohio, area. My wife and I have been looking for a new house, and we just looked at one within three days of it being listed.
It’s a basic three-bedroom ranch listed at a price that a completely renovated house would be selling for. The pictures looked great online, as always. As soon as we walked in the house, a smell of mold hit me right in the face. It was so bad after being in the house for 10 minutes that I started to get sick and had to leave.
I noticed the hardwood had no subfloor and was cupped and swollen in every room. I found a small access panel behind a tub. I removed the panel and looked in using a flashlight. I found dirt 1 in. from the floor joists with no sign of a vapor barrier. After seeing this and taking into consideration the terrible mold smell, it seems to me that this house is a complete teardown, no matter how nice the house might have looked on the inside.
We decided on a low-ball offer (about what the land is worth because the house is worth nothing at this point). Our offer was denied and another offer came in and was accepted.
My question to you is do you see any fix to this house besides completely starting over? I can’t help but think that someone with no existing knowledge of how houses are built could come in into this house and overpay thinking they can remediate the mold, but the problem would just keep coming back due to the lack of a vapor barrier.
I feel terrible for this person that bought this house and wonder if there should be some kind of required pre-purchase mold inspection required with real estate transfers. It is so easy for someone with no knowledge to financially ruin themselves by purchasing something like this.
I love the podcast and appreciate your time reading this.
Evan Bache-Wiig from All Mold Pro in Rockwall, Texas, responds:
Good Morning!
Thanks for reaching out. This is an interesting house the reader is describing. I’m more familiar with building practices in my southern part of the county, but my first thought was that this had to be outside city limits, where it wasn’t permitted or inspected or perhaps it’s very old.
I have come across this type of damage with early 20th-century homes with crawlspaces in my area with a very low crawlspaces or crawlspaces that have had a hot water leak in them. Assuming the rest of the house is okay, I don’t think this house needs to be scrapped. My instructions for remediating this would be:
- Remove all flooring and lower cabinets.
- Flood-cut all walls 2 ft. up (assuming there is Sheetrock and insulation).
- Excavate the crawlspace as much as possible to install a vapor barrier across the soil.
- If visible mold is present in wall cavities with penetrations in the bottom plate (plumbing and electrical penetrations), take the Sheetrock off from floor to ceiling, then clean with an approved product followed by encapsulation with an anti-fungal paint.
- I would also check the attic to make sure that that soil moisture has not migrated up through the wall cavities and created a humidity/mold growth problem on attic lumber.
The listener commented that there should be a law requiring mold inspections, and while I think that would be too much to legislate, I strongly agree that buyers should invest in the general inspection as well as mold, plumbing, electrical, structural, and HVAC when purchasing older houses so they have a better idea of what they’re getting into. But that is not the reality, and frankly would be too expensive for most people.
I think I have posted on our All Mold Pro Instagram some videos of projects were the walls were flood-cut and the subfloor removed, but here are some below for you to enjoy! I’m always happy to comment on these things and would be happy to do another segment with you all if you wanted to talk about these kind of remediation projects.
![]() |
![]() |
![]() |
RELATED STORIES
Question 2: What should new grad Sydney be doing to pick a construction career?
Sydney in Colorado writes:
Hi FHB Podcast Team,
I recently graduated from college with a Bachelor of Arts degree in Integrative Design & Architecture. I plan to start an internship with a design-build company working on web and graphics work for web and print publication. It will also include mentorship on some drafting work, and hopefully evolve from there.
As I prepare, I am working on getting up to speed with CAD (SketchUp and AutoCAD) and reading some books. What advice do you have to someone who feels inexperienced in real-world, hands-on design-build work? I want to enter the job with a solid foundation to provide quality work for the company. I have experience working in the service industry, farming, non-profits, and groundskeeping.
My college program (Colorado College/CC) required courses involved studio work (i.e., small-group design work and independent work with design prompts and multiple critiques/feedback and iterations). I also took classes that piqued my interest: “Integrative Design & Architecture” (now titled “Design Studies”) and minor “Education”.
For the Education program, I did a semester off-campus to live and learn at the Catamount Institute Mountain Campus in Woodland Park, which focused primarily on individually crafting and conducting a five-week curriculum with a small group of fourth grade students. Here is the link to the program descriptions for my design major and the link to the TREE semester in Woodland Park:
https://www.coloradocollege.edu/academics/dept/art/requirements/concentrations/ida.html
http://www.catamountcenter.org/tree-semester/
I’m still up in the air as to what path I’d like to take in the construction industry. I’d like to be involved with the physical outdoor work and to develop enough knowledge about building science and zoning analysis to make informed design choices. I want to know how a structure can last for a while.
Biking in Colorado Springs and seeing the new and superficial-looking developments makes me curious as to what future towns and cities will look like if placed in the hands of people who don’t prioritize quality in building.
The internship in Princeton, N.J., starts July 1, so I plan to spend the month of June getting up to speed on zoning analysis and CAD/BIM.
Best,
Sydney
RELATED STORIES
Question 3: How does one build on solid sandstone?
John from San Juan County, Utah, writes:
Podcast crew,
My sincere thanks for all of the varied information. I happily listen to 30 minutes or more of air-sealing and heat-pump talk to learn construction tips. My question would be mostly for Mike Guertin.
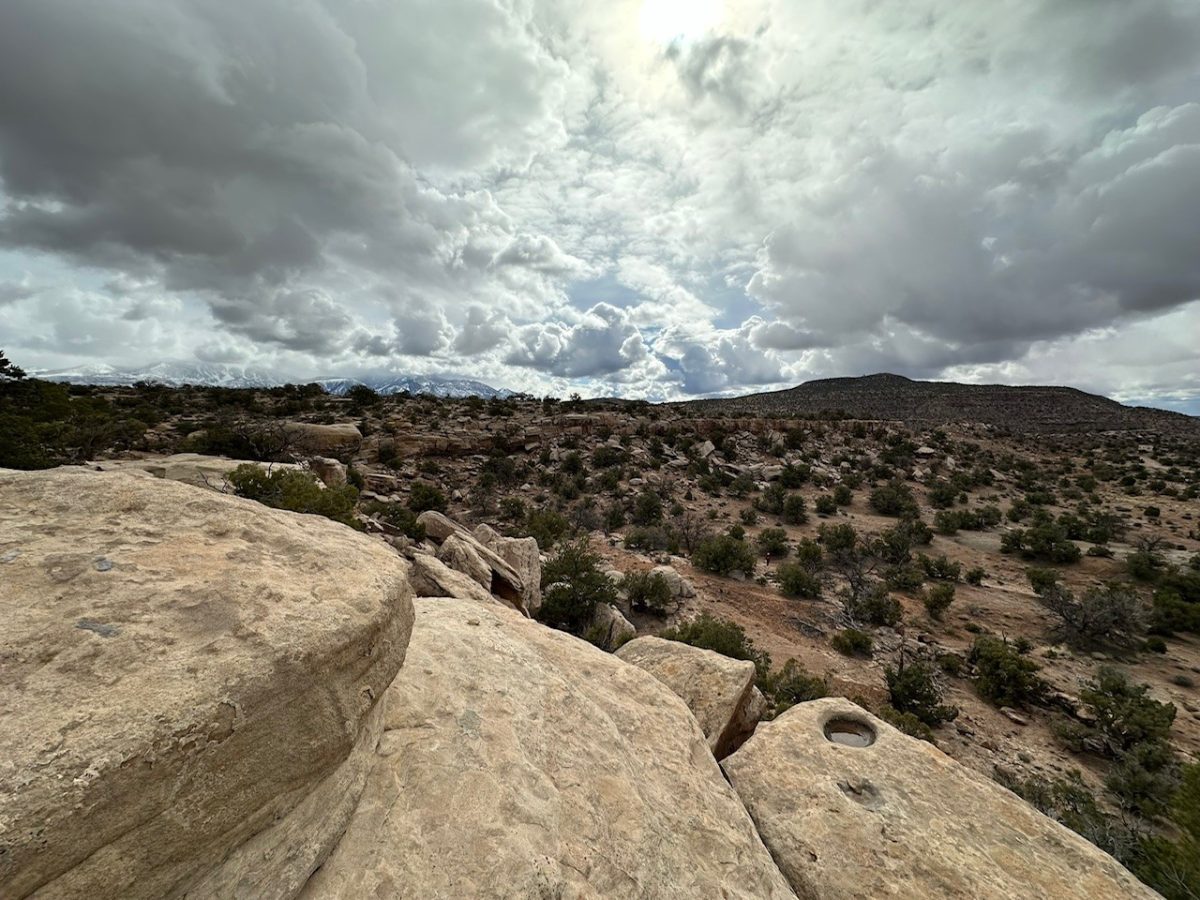
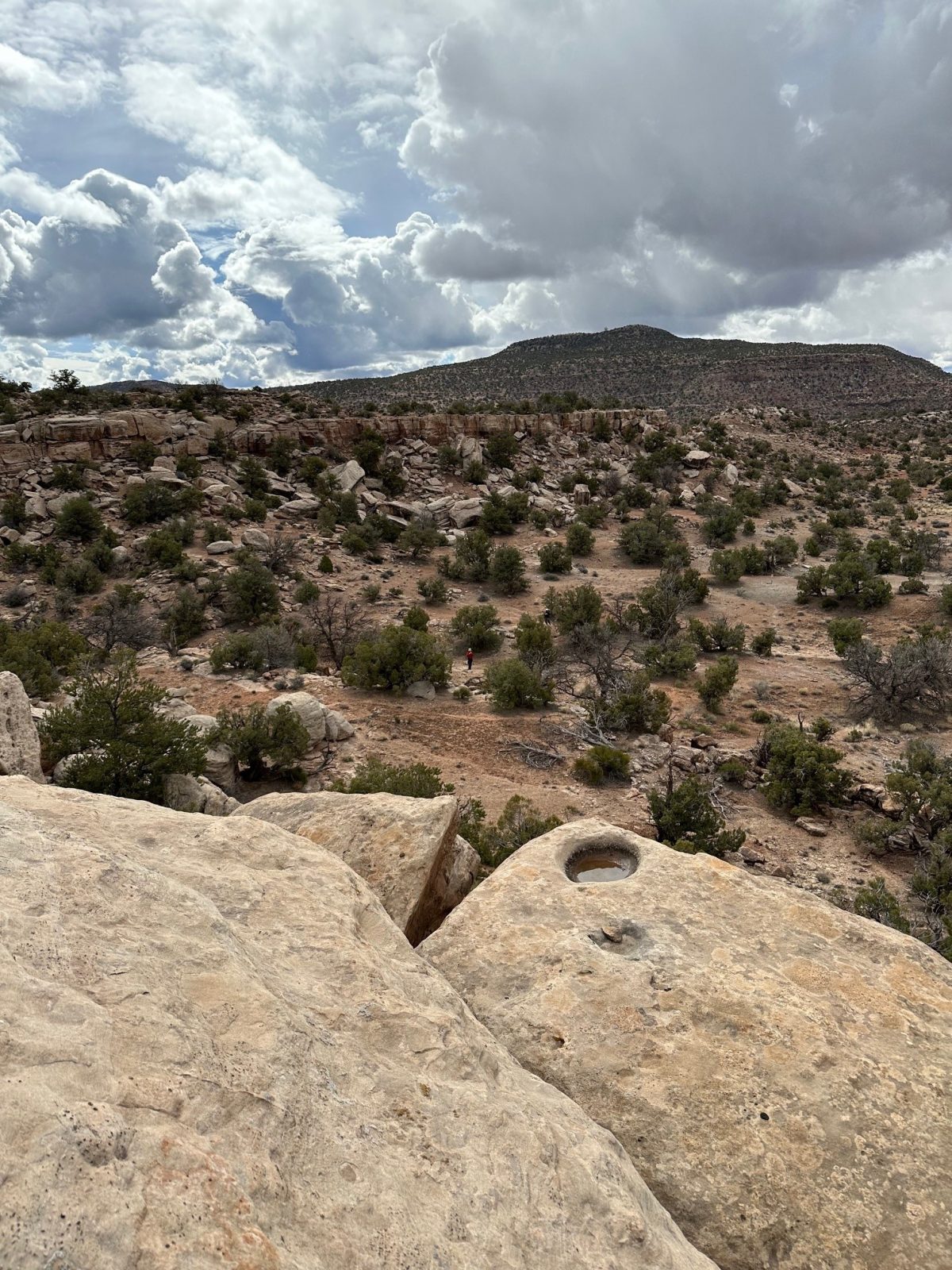
RELATED STORIES
Well, unfortunately, that is all the time we have for today. Thanks to Mike, Brian, and Andres for joining me, and thanks to all of you for listening. Remember to send us your questions and suggestions to [email protected], and please like, comment, or review us no matter how you’re listening—it helps other folks find our podcast.
Happy Building!
Fine Homebuilding Recommended Products
Fine Homebuilding receives a commission for items purchased through links on this site, including Amazon Associates and other affiliate advertising programs.
Reliable Crimp Connectors
8067 All-Weather Flashing Tape
Affordable IR Camera