Podcast Episode 649: Sealing Crawlspaces, Problem Porches, and AC in Attics
The crew talks about trade work, deck longevity, sealing crawlspaces, overhanging floors, and AC ductwork.
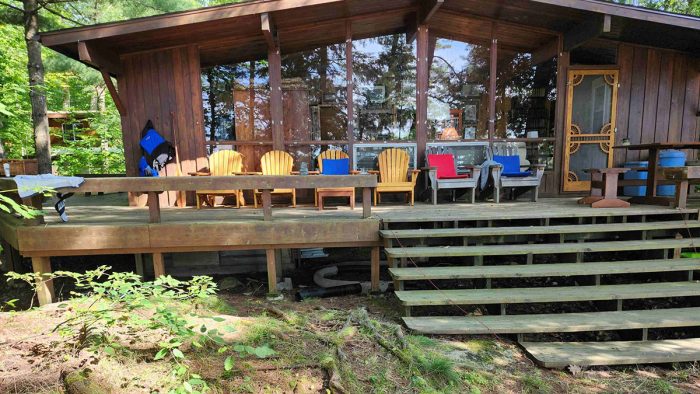
Follow the Fine Homebuilding Podcast on your favorite app. Subscribe now and don’t miss an episode.
![]() |
![]() |
![]() |
Remember, you can watch all your favorite clips from the show on our YouTube channel!
Doug says he lost 30 lbs. doing construction. Graham’s deck is in good shape. Tyler is sealing his crawlspace. Jeff’s porch is poorly detailed. Teewhite asks about sealing an attic with AC on GBA.
Check in:
Ian Schwandt is presenting at Remodeler’s Advantage.
Patrick: Repaired door jamb
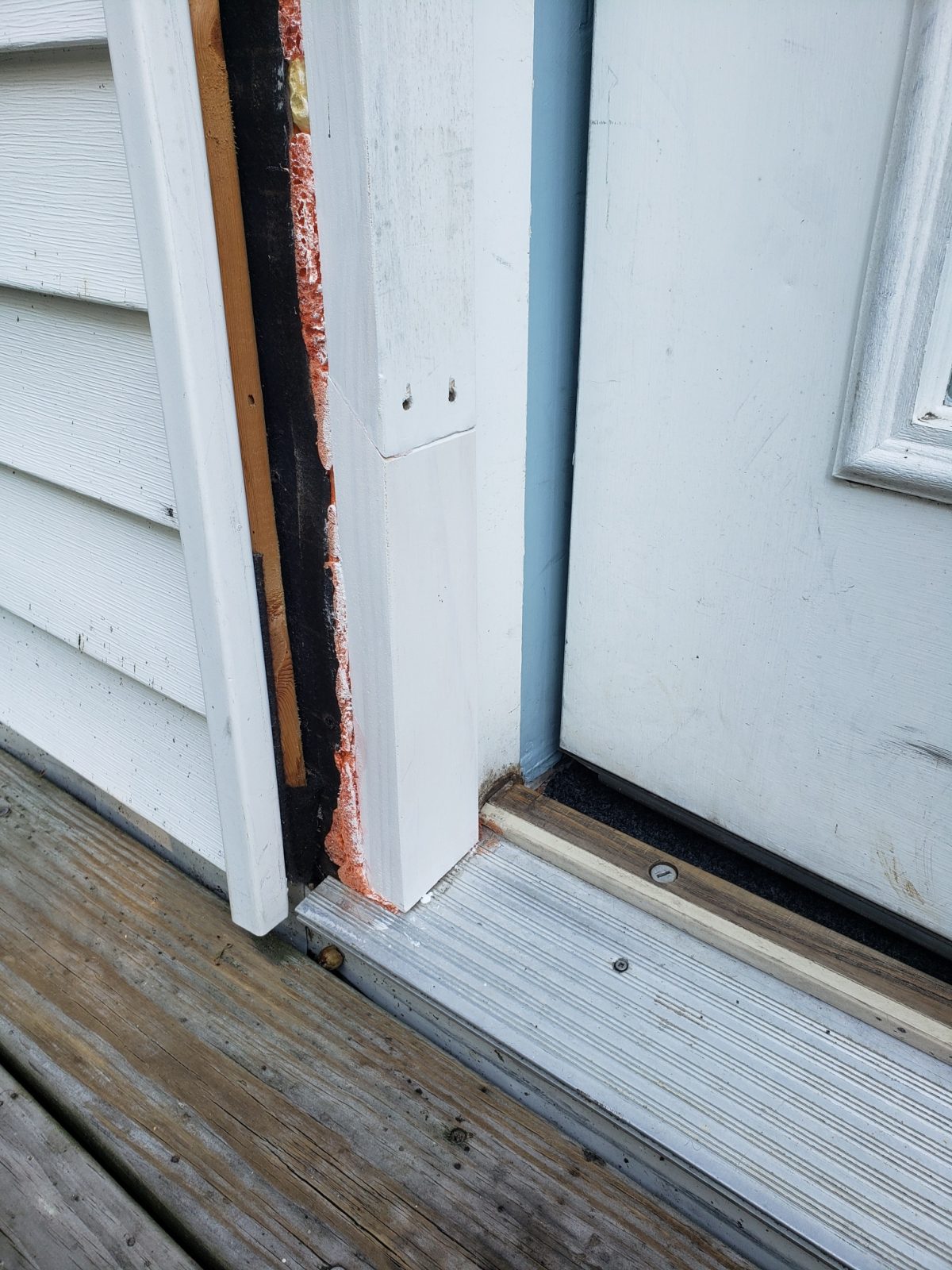
Listener Feedback 1:
Doug writes:
Hi All,
There have been several discussions about getting into the trades later in life. I once knew a guy who worked construction part-time. He told me that he watched the older workers. He wanted to learn how to work so he could still do this as he got older. I was 61 when I started to build our house. Every day I wished I was 10 years younger. The positive was that I lost 30 lbs. during the process. This was a combination of the work and the limited kitchen I was able to carve out of my shop—just a fridge, microwave, and toaster oven. Some nights I was so tired that dinner was just a few handfuls of trail mix and a couple of beers. Unfortunately, when the house was done and I had a real kitchen, the weight found me again.
Listener Feedback 2:
Graham writes:
Greetings FHB podcast crew,
I’m a longtime subscriber but fairly recent podcast listener. While on vacation at our cottage in northern Ontario, I listened to a recent episode where you asked about deck boards. Being on vacation gave me a few minutes to send in my first comment on a podcast while sitting on the deck looking out at the lake! Attached are a few photos of a deck I built in my early 20s in 1987, probably my first building project.
After close to 40 years of weather extremes, it is still going strong. (The cottage is just south of Parry Sound in Ontario.) The only maintenance needed is clearing pines needles out from between boards and doing a bleach-and-soap scrub every couple years. About 20 years ago I did something you probably shouldn’t—I used a rented floor sander to sand down the deck and then stained it with Sikkens ProLuxe Cetol 1.
A few boards on the bench to the side were replaced last year (it is in constant shade). When other boards are wet, can see some signs of a few starting to go, but it’s still very solid.
I thought you might get a laugh at the design. I think I read a book for the basics but then just did it.
The photo of the somewhat faded paper is the total plan for the deck—a sketch on a piece of paper now framed and on the wall. I can’t draw and I lack the patience for a detailed plan. But overconfidence and good problem-solving has always come through for me when building. The piers are probably some idea I came up with on the fly. Some of them might have one piece of rebar going through the concrete and into bedrock and then probably into a hole drilled up into the posts. There’s definitely no epoxy anchoring it, and certainly the 2x flat on top of the concrete to nail into the post is not listed in any codebook. The bench is not to code at the corner and on the side, but permits weren’t such a big deal up here back in the 80s. But we’ve had no accidents in 40 years.
Keep up the good work. I always get a tip or two each podcast.
Graham
PS The Muskoka chairs—a better Canadian version ? of Adirondack chairs—are new. I bought as a kit for probably less than I could have purchased the wood. I assembled and stained them this week, and they being put to good use. I did build the trestle table and a couple benches to fit the corner of the deck.
All the best,
Graham
RELATED STORIES
Question 1: What’s the best way to seal a vented basement crawlspace?
Tyler writes:
Hello,
I am working out how to encapsulate the crawlspace of a 1910 bungalow in Oregon (Climate Zone 4 marine). The project also includes sealing and insulating a few overhangs.
I can see daylight through the floorboards in a few spots, and the narrow lap siding is nailed directly to the 2×8 joist butt ends. I see recommendations to hang foam on the bottom of the joists, but I assume the lap siding would make a too-porous side of that cube, and I’m already pretty close to the ground.
I’m thinking of fitting foam to the bottom of the floorboards, sealing the edges with caulking or spray foam, then hanging Hardie on the bottom of the joists to protect everything. I might go with 1-in. to 2-in. foam board and fill the rest of the cavity with mineral wool.
Do you have any thoughts on insulation types and positions? There is an iron drainpipe from the bathroom sink that drops from the overhang, near the foundation wall. Do I need to insulate the drainpipe somehow? Should I leave an air gap (bridged with insect screen) in the Hardie panel? Is there a better way to approach this in general?
Thanks for the help. I really enjoy and appreciate the show!
Tyler
RELATED STORIES
Question 2: My brick porch is touching my wood-framed house. What’s the best way to fix this, and is a repair even necessary?
Jeff writes:
I’m trying to figure out how to make this repair. I ended up getting termites that enter the trim board below the exterior door sill because it was untreated regular pine touching the brick porch. The termites ultimately were tunneling back to the subterrain between the porch and the house, either behind or in front of the flashing. The brick porch has a foundation that is part of the main foundation. I feel like having a brick porch right up against the house is a bad design; there’s no way to see mud tubes, regardless if they are flashed or not. The exterminator took care of the termites a few years ago. I was waiting to retrim until I was sure the termite issue is under control. Is there a best practice construction detail drawing that I can view for a brick-porch detail? Should there be an air gap between the brick and the rim joist? Without getting too extreme and costly, I was planning to just retrim with PVC after air-sealing and re-flashing everything correctly, which I am trying to figure out howto do under the circumstances. Or does this door need to be ripped out and redone correctly? I’m in Climate Zone 5a (southeast Connecticut on the coast).
RELATED STORIES
Question 3: AC in a vented attic is a problem, but what do can I do about it?
teewhite7 from South Louisiana asked on GBA:
I live in southern Louisiana in a recently purchased 90s home that has several attic-access areas—some small for storage and two of them just to house the HVAC equipment. The previous owner stuffed R-19 batts in the rafter bays, in the soffits, and, generally, everywhere in some of these attic space/storage rooms. What little I know about attic venting made me think it was a bad move to not have any baffles.
So I opted to make my own baffles from 1-in. XPS and run them up to the upper attic areas where there are exhaust vents and replace all the wall and rafter batts with Rockwool.
My problem is that once I started removing the insulation on the walls that lead to the interior of the house, the drywall was damp and the fiberglass batt facings were damp/wet. My question is: without placing a dehumidifier in each of these rooms, what are my options? I feel like what little duct leakage there is isn’t enough to keep these rooms cooler/dry.
RELATED STORIES
- GBA.com: Insulating Cramped Attic Crawlspaces
- GBA.com: Ducts in an Unconditioned Attic
- Building Codes for Insulation and HVAC in Attics
Sign up for a Fine Homebuilding All-Access Membership
Unfortunately that is all the time we have for today. Thanks to Ian, Brian, and Andres for joining me, and thanks to all of you for listening. Remember to send us your questions and suggestions to fhbpodcast@finehomebuilding.com, and please like, comment, or review us no matter how you’re listening–it helps other folks find our podcast.
Happy Building!