Podcast Episode 652: Tool Batteries, Moldy Sheathing Behind Brick, and Rebuilding Decks
Listeners write in about power tool batteries, replacing sheathing behind brick, and rebuilding a pressure-treated deck.
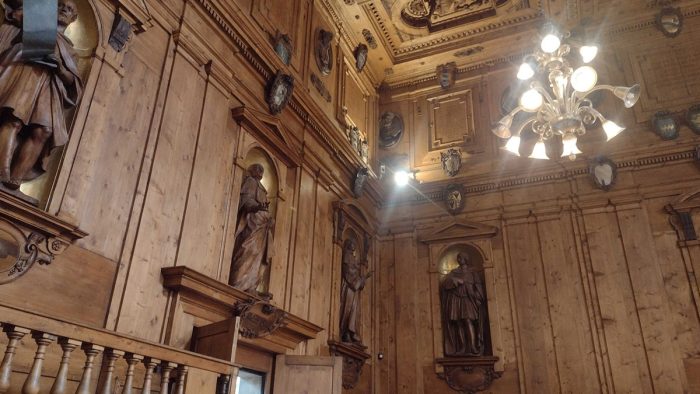
This week’s spotlight question comes from Jim, who asks on Fine Homebuilding’s Forum if he can replace rotted pressure-treated decking, or if he has to rebuild the whole deck.
The FHB Podcast crew talks about cross-compatibility of power-tool batteries. Contractor Evan in Dallas wonders how to replace moldy sheathing behind brick without removing the brick. The crew offers their best suggestions and discusses the importance of managing vapor drive behind brick and other reservoir claddings.
Follow the Fine Homebuilding Podcast on your favorite app. Subscribe now and don’t miss an episode.
![]() |
![]() |
![]() |
Note: The Fine Homebuilding Podcast team is always looking for ways to improve, so we’re switching up our video strategy. But don’t worry—you’ll still be able to watch all your favorite clips from the show. Check out our YouTube channel or keep scrolling to see more!
Check in:
Mike: Trip to Italy with Myron Ferguson: When? How long? Today we’re talking about wood timbers and decorative elements made of wood. It turns out that Mediterranean architecture is not all masonry. We’ll hear more about Mike’s trip to Italy in future episodes because I think there are valuable building lessons to be learned.
![]() |
![]() |
![]() |
![]() |
Listener Feedback 1:
Jordan writes:
Hi guys,
I’ve been listening to old episodes while working on an especially labor-intensive home project and came across a couple where you discussed the topic of battery compatibility across platforms. I’m on episode 551, where the idea of a universal battery comes up. I wanted to share my thoughts on this from the perspective of someone who has some knowledge in battery tech.
In the solar-energy storage world, it is not uncommon to see batteries that have protocols to communicate with a wide array of inverter manufacturers. The benefit here is the ability to share data (like capacity, cell voltage, and temperature) and to initiate various programmable actions through relays (like activating fans, sending alerts, stopping discharge, etc.), similar to how tool batteries communicate with tools.
If it’s possible for solar battery manufacturers to communicate with multiple inverter manufacturers, it seems like the only thing really holding tool companies back is loss of proprietary battery profits—which have to be huge, by the way. For comparison, a 48V 100Ah solar storage battery with full communication is around $1,300 (~$0.25/Wh) and a two-pack of Milwaukee M18 high-output 6Ah batteries is $250 or (~$1.16/Wh)., which is 4.6x the cost per watt-hour!
Per your discussion about whether it really relates to On-Board Diagnostic II (OBD-II): if not for a California Air Resources Board (CARB)—and then federal—mandate requiring a standardized connector and communication protocol by 1996, manufacturers would still be making proprietary ones and gouging techs for the privilege to work on them.
If tool manufacturers were required to maintain a standard protocol (or at least to release their communication protocol for use in approved battery adapters), they would be incentivized to make the batteries ones that people buy not because they have to, but because they’re the best. Best performance, most reliable, best value. Why should I, the end user, have to buy into a whole new system to get a tool I want just because I don’t have the batteries for it?
Batteries at their core are simple—cells, management system, temperature probes, connectors, maybe a fan, maybe vents. The third-party battery should be able to communicate everything in the pack to the tool, and the tool adjusts its output accordingly. For example, say you have an 18V-saw capable of putting 1800 to the motor, and the battery is 6Ah but only rated at 15C discharge, so the saw limits its power output to 1600W (6A * 15 * 18V = 1620VA max discharge). It’s really not that crazy, and it’s nothing they aren’t already doing in their own proprietary systems. Well, that was longer than intended. Whoops.
Cheers to keeping craft alive,
Jordan
RELATED STORIES
Question 1: How can you replace moldy sheathing behind brick without removing the brick?
Evan from Dallas writes:
Good evening FHB crew,
I have a challenging remodel question for y’all. The house is a 1970s slab house with a brick veneer that does not have weep holes. The exterior sheathing is a paper-faced gypsum board that was extremely moldy from sprinklers, drainage, etc.
Before mold remediation took place, I discussed removal options with the client including taking off the affected face of the gypsum board, cleaning, then painting the board with antifungal paint, and, as a final option removing the affected sections.
The clients are quite sensitive, so they opted to remove the affected gypsum-board sheathing 1 ft. to 2 ft. up in the affected areas. My question for y’all is how on earth do they rebuild this exterior wall?
They are not prepared to take the brick off to rebuild these areas, and I’m concerned that if we take rigid foam and stick it in the cavities, it will not lap in front of the black plastic at the base of the wall, which serves as a drainage plane to the weep holes.
My idea was to take rigid foam board and tape heavy, black plastic flaps to the bottom so that when it is inserted into the stud bay, the black plastic attached to the board can overlap the existing black plastic at the base of the wall. I’ve included pictures below. I’m sure Mike has something simpler than this to recommend from his past experiences.
Thank you for all you do!
Evan Bache-Wiig
All Mold Pro
![]() |
![]() |
RELATED STORIES
- VIDEO: How to Remove Old Window Sashes and Jambs from a Brick Wall
- Window Replacement With a Side of Rot Repair
- When Sunshine Dives Moisture Into Walls
Question 2: Can I replace only the rotted pressure-treated decking, or do I need to replace the whole deck?
Jim writes on the FHB Forum:
The deck attached to my house is 36 years old and was built when the house was.
Here are the specs for reference:
- Deck is 12 ft. x 12 ft. and attached to the house via a ledger
- 4-in. x 4-in. posts in poured-concrete piers
- Joists are 2 in. x 8 in., 16 in. on center
- Surface boards are 1 in. x 4 in.
- Deck surface is approximately 22 in. above the ground
- All wood is PT
The deck is not used very much, except for using the barbecue, and I’ve only stained it a few times over the years. I recently pressure-washed it and was going to stain it, but I noticed that one of the deck boards had split at a knot and a few others had problems at knots.
My plan was to remove some deck boards to check the condition of the joists and the ledger. The deck boards are attached with 2 1/2-in. screw-shank nails and are a bear to remove. The framing appears in good shape, so I was going to replace only the deck boards. I checked the posts at pier level and didn’t find any problems. I poked the joists via the floor-board gaps and everything was solid, but there was no waterproofing material on the tops of the joists.
Here are the options I’ve come up with:
- Replace just the bad deck boards
- Replace all the deck boards with the same type of decking and add waterproofing
- Replace all the deck boards with maintenance-free decking and add waterproofing
What’s your advice? What’s keeping me undecided is the longevity of the joists and ledger knowing that waterproofing was not done.
Thank you.
RELATED STORIES
Question 3: How do you put a guardrail post on a 45-degree corner? Are there prescriptive details?
JD from Maryland writes:
Hi Mike,
I’m building a deck with a 45-degree angle at one corner. I’ve looked through all the guardrail-post connection details I could find in the articles and videos that you’ve done, but I don’t see any that show how to approach 45-degree corners. Do you have any solutions for attaching posts on the outside of the rim joists at angled corners?
JD
Mike’s reply: There are no prescriptive details published by hardware or screw manufacturers, but I’ve tested my own field details and they’re pretty strong. Here’s a photo of how I approach it.
![]() |
![]() |
RELATED STORIES
Sign up for a Fine Homebuilding All-Access Membership
Well, unfortunately that is all the time we have for today. Thanks to Mike, Brian, and Andres for joining me, and thanks to all of you for listening. Remember to send us your questions and suggestions to [email protected], and please like, comment, or review us no matter how you’re listening–it helps other folks find our podcast.
Happy Building!
Learn about SketchUp for Builders by Jon Beer,
the new E-learning course from Fine Homebuilding
Fine Homebuilding Recommended Products
Fine Homebuilding receives a commission for items purchased through links on this site, including Amazon Associates and other affiliate advertising programs.
Reliable Crimp Connectors
8067 All-Weather Flashing Tape
Handy Heat Gun