Podcast Episode 655: Engineer’s Approval, Subfloor Dehumidification, and Basement Window Headers
Listeners write in about engineering approvals, active subfloor dehumidification, and headers spanning basement windows.
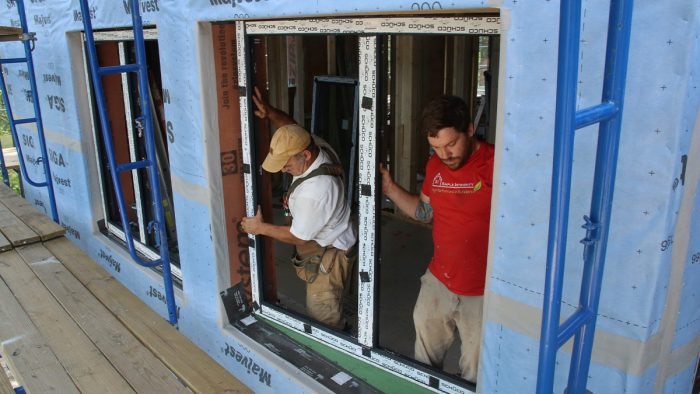
Brian, Ian, and Patrick hear from listeners and answer building questions. Does it make sense to dehumidify under a basement subfloor? Do basement windows need a header?
![]() |
![]() |
![]() |
Note: The Fine Homebuilding Podcast team is always looking for ways to improve, so we’re switching up our video strategy. But don’t worry—you’ll still be able to watch all your favorite clips from the show. Check out our YouTube channel or keep scrolling to see more!
Have a question or topic you want us to talk about on the show? Email us at [email protected].
Check In:
- Ian: Remodelers Advantage presentation and conference
- Brian: Haunted tub filler
- Patrick: Flangeless window install with Josh Edmonds
Listener Feedback 1:
Ron writes:
Hey guys,
I’m an electrical contractor in New Jersey. I do mostly service work. It’s always interesting to listen to professionals discuss the trades. Did we figure how the crickets were getting into that basement?
Keep up the good work. Thank you for what you do. I will always be interested in building science.
Thoughtfully,
Ron
Listener Feedback 2:
Bob writes:
Episode 650 included the discussion of the pig farmer’s walk and how beefy it needed to be to not collapse under the weight of a bale of straw. This reminded me an incident some 30 years ago in Old Lyme:
The fire department was dispatched to a “truck vs. bridge” accident. An empty drywall truck went under a local Amtrak bridge. The cab fit easily; the drywall boom lift at the back of the truck, not so much. Upon impact the truck stopped its forward motion and converted the energy into lifting the cab of the truck into the bottom of the bridge. The cab was mostly collapsed to the steering wheel. Amazingly and thankfully, the driver walked away shaken but seemingly otherwise fine.
We called Amtrak, who asked that we stay until their engineers were dispatched to inspect and verify the bridge was not damaged. We did, excited to see all the sophisticated equipment that must be involved with such a certification. They soon arrived. We were quite disappointed to learn how a bridge is determined safe (at least in this case): Key the radio and say “Okay, go ahead.” Shortly a train appeared and went over the bridge slowly. The engineers agreed it was all set and left.
So even the “pros” like to look and put it to use. If it does not collapse, it must be good enough.
I thoroughly enjoy your show as I drive around.
Bob
RELATED STORIES
Question 1: Does it make sense to use a dehumidifier to dry the spaces created by the dimple mat on the underside of the subfoor?
Andrew writes:
Hi Podcast crew,
I’m a longtime listener, first-time emailer. I grew up around DIYers and love the podcast. I wanted to share an idea for finished basement floors and get your take on it.
We purchased a 1986 home about four years ago in southern Vermont (Climate Zone 5b). It largely looked okay in the inspection, but as I have looked under the covers the last few years, just about everything was done as cheaply as possible.
Some quick examples: no interior insulation; 1/2-in. supply to shower far from the water heater; zero exterior outlets or sillcock (all these things are allowable but cheap). And then: sill plate not fastened to anchor bolts on foundation; bathroom fans vented to nowhere; and rotted doors and window sills with missing flashing (which are all actually wrong).
Now I am finishing the basement. I used Dricore (the basic panel with black plastic on the bottom). I followed the manufacturer’s recommendation to lay out the Dricore panels with a 1-in. margin at the foundation wall, and then frame all walls on top of it. The 1-in. margin also works nicely with the wall assembly because we are spray foaming the wall and rim-joist cavity above, and the insulation contractor told me to leave that size gap between the poured concrete and the studs (the wall will be concrete, closed-cell foam, studs, Sheetrock).
The only area of the basement that did not get Dricore is the utility room, so air/ humidity could possibly move anywhere under the continuous Dricore subfloor and end up in the utility room. My concern is that there is no gradient that would drive the air, so although the panels do allow moisture to leave the concrete, I wonder if that 1/4-in. gap will collect humidity and have a hard time drying out. My idea to address that is to run some cheap PEXb in the 1-in. gap around the perimeter of the room, cap one end, drill some small holes in it facing down, and connect the open end to a dehumidifier (which will be installed anyway). Think of a soaker hose in a garden, but for warm, dry air underneath the Dricore.
My question: Is this totally ridiculous? Have you ever seen an air-circulation system for an air gap underneath a subfloor? It’s only a couple hundred dollars in materials, so I am highly inclined to do it just in case. If I ever decide I don’t want it, I can just disconnect it from the dehumidifier. But if I don’t do it and I ever detect a moisture issue, I think I will be kicking myself for not installing this when it’s all easily accessible. Or am I just way off base altogether? What should someone be doing for a high comfort/performance floor assembly in a finished basement in northern climates?
Some other details you might be wondering about in your discussion:
- Finished floor will be LVP (I like the Cali wide planks)
- Finished walls will be Sheetrock
- No radon issues
- When I installed the sump pump, I did find a layer of poly between the concrete and gravel, but its condition under the whole basement is unknown. I suspect it could deteriorate or puncture after nearly 40 years of settling. The only thing that I was pleasantly surprised by was finding more than 12 in. of gravel under the slab, so I am assuming water under the slab can flow freely through to the pump.
Sincerely,
Belt and Suspenders for a dry basement,
Andrew
RELATED STORIES
Question 2: The structure above my replacement glass-block basement windows is sagging without the support of the old steel window frames. Should I be worried about it?
Cory writes:
Hi all,
I replaced my original 1950-ish (there’s some dispute) basement hopper windows with premade glass-block units. The original units were steel with the frame set into a channel in the block foundation on three sides (left, bottom, right) and were flush against the underside of the mudsill on the top edge. Where I live this is a very common window from that era: ~32 in. wide (2 blocks) and ~16 in. high. I watched about 17,000 YouTube videos about this replacement, and they were all pretty much identical. The installations went smoothly and we’re happy with the results.
Now, here’s where I start worrying: That steel was substantial (pictured below). My mudsill now runs ~32 in. over these windows unsupported. There are floor joists that land at various spots in that span, sometimes pretty close to the center of it. At least two of these basement windows have first floor windows framed above them where the studs that support the headers land within this unsupported span. One of those first floor windows is actually a ~7-ft.-wide bank of six windows, so it’s sizable. An experienced contractor friend who I trust suggested the rim joist is probably providing a lot of the support, but the rims here are not in line with the wall framing (it’s about 3/4 in. proud to allow for the original fiberboard sheathing to land flush with it).
Is this likely to cause problems? What should I watch for? I’m guessing I should get a laser level, make some marks, and watch for movement over time.
Any advice on how to shore this up if it is a problem? There’s about 2-1/2 in. on the interior of the top of the foundation wall that isn’t covered by the mudsill, so if something needed to be added to support the floor joists directly (to supplement the mudsill), there is some room to play with.
Yes, I’m the guy who asked what I’ll do about the nail holes in my new sheathing 25 years from now. Yes, Brian was right, my meditation practice helps! But this one seems like more than idle neurosis.
Anyway, thanks as always!
Cory
![]() |
![]() |
![]() |
![]() |
RELATED STORIES
Sign up for a Fine Homebuilding All-Access Membership
Sign up for our new eLearning course, Sketchup for Builders with Jon Beer
Well, unfortunately that is all the time we have for today. Thanks to all of you for listening. Remember to send us your questions and suggestions to [email protected], and please like, comment, or review us no matter how you’re listening–it helps other folks find our podcast.
Happy Building!
Fine Homebuilding Recommended Products
Fine Homebuilding receives a commission for items purchased through links on this site, including Amazon Associates and other affiliate advertising programs.
Affordable IR Camera
Reliable Crimp Connectors
Handy Heat Gun